Flex Section or No Flex Section?
#1
On The Tree
Thread Starter
iTrader: (5)
Join Date: Jun 2007
Posts: 118
Likes: 0
Received 0 Likes
on
0 Posts

Guys
I'm building a single setup for my 240SX. I've never designed, nor fabricated anything like this, so I have just been going off of what I have seen others do.
The concept in question is whether or not I should keep the flex section in my current design. There is no way to implement a flex section into the piping on the passenger side.
The other question is whether or not I should add a mount for the turbo. I am thinking I might be able to get away with keeping my hot-side how it sits by bracing the turbo to the engine and not the chassis.
Another idea is just getting rid of the flex section and letting all the weight of the turbo hang on the exhaust. The turbo is an On3 70mm and I believe it weighs 15lbs
Here are the pics
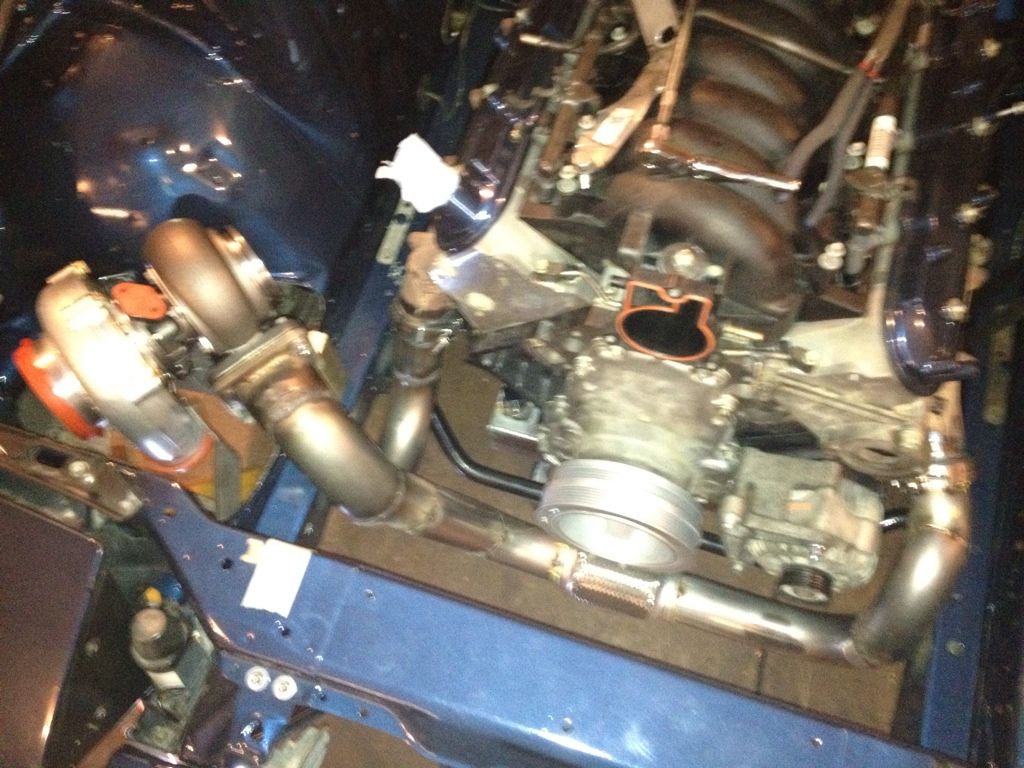
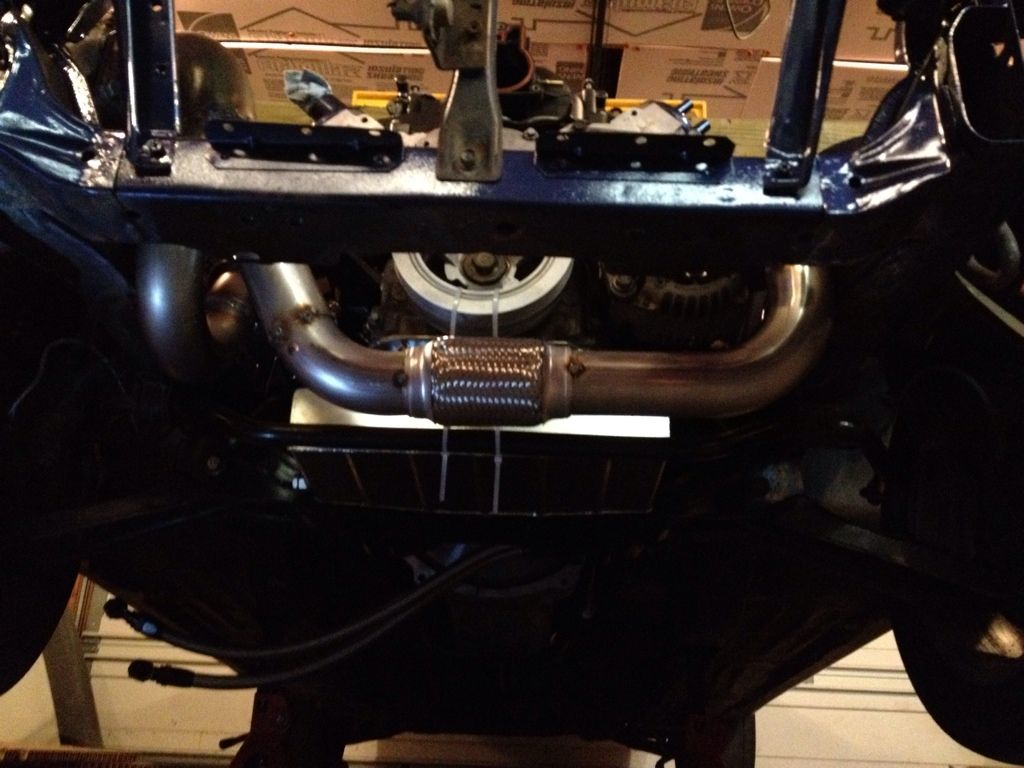
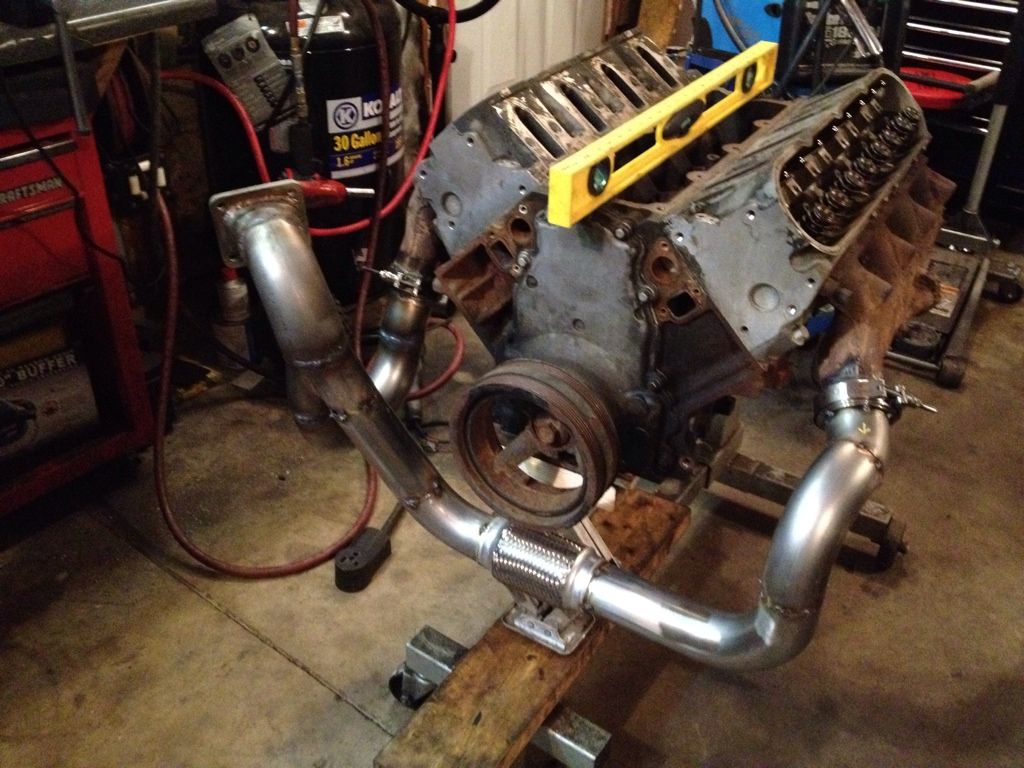
Thanks guys!
I'm building a single setup for my 240SX. I've never designed, nor fabricated anything like this, so I have just been going off of what I have seen others do.
The concept in question is whether or not I should keep the flex section in my current design. There is no way to implement a flex section into the piping on the passenger side.
The other question is whether or not I should add a mount for the turbo. I am thinking I might be able to get away with keeping my hot-side how it sits by bracing the turbo to the engine and not the chassis.
Another idea is just getting rid of the flex section and letting all the weight of the turbo hang on the exhaust. The turbo is an On3 70mm and I believe it weighs 15lbs
Here are the pics
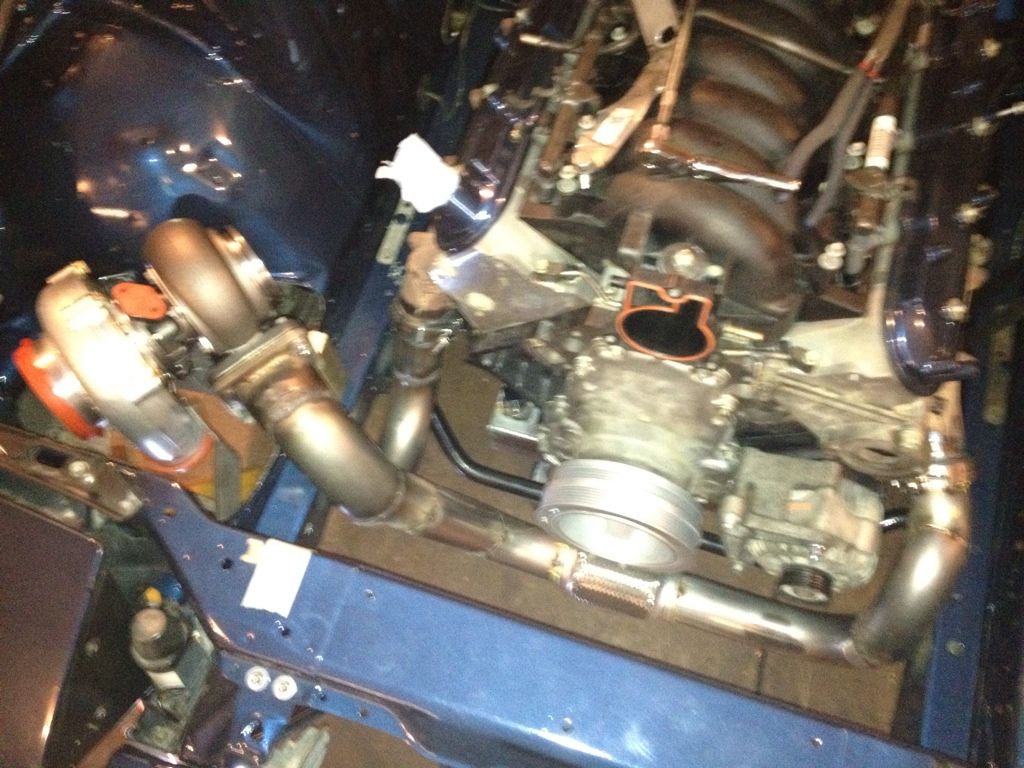
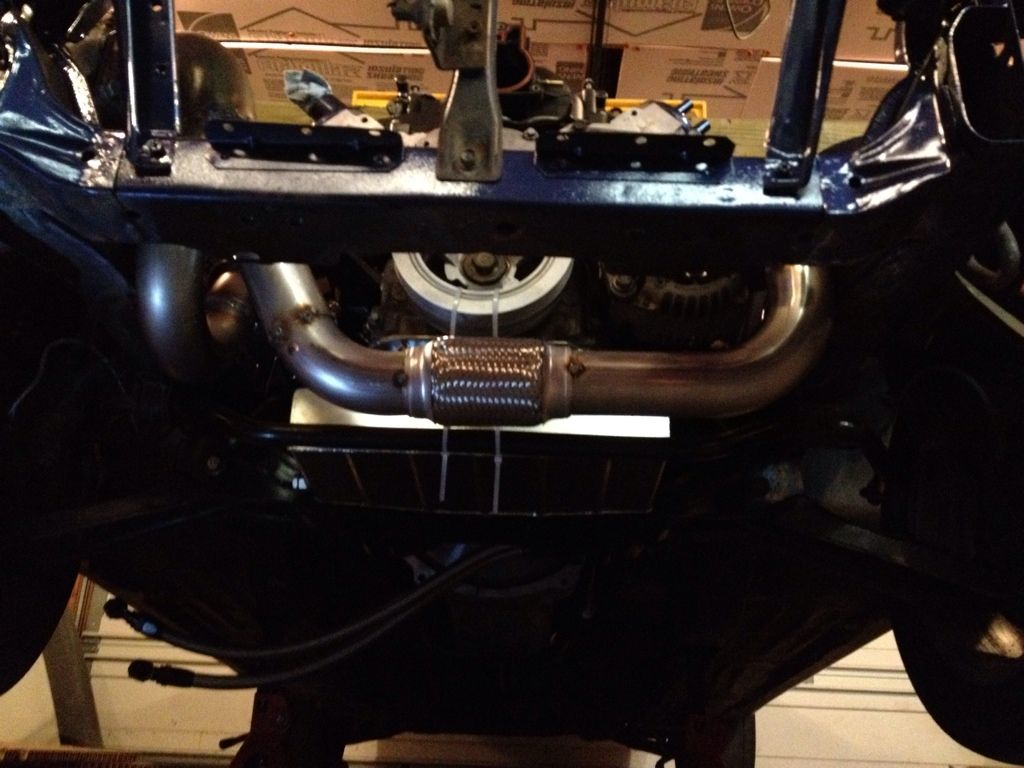
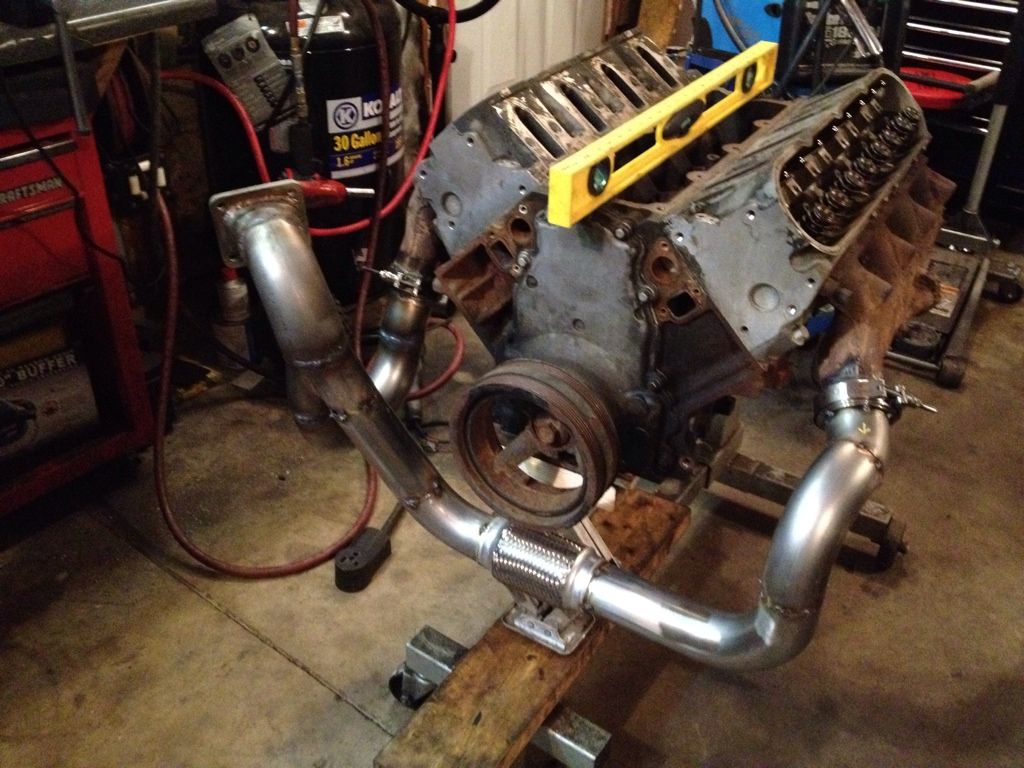
Thanks guys!
#2
TECH Addict
iTrader: (8)

Only reason I would think people use it is because the way they weld it the pipes warp all over. Proper way to fab up a system is tack it all together except the last joint between each side, fully weld it all, and then put it back in and line it up and weld the last joint in place. If you tack it all together like you have it, if it were not a flex, then take it out and weld it.... it would probably be over a 1/2" off from lining up with anything. When you weld something, the heat expands it, and then when it cools it actually shrinks to be smaller than before you heat it. And since you cant weld an entire joint all at once, starting on one side can warp it slightly......do that to a bunch of joints and you could have it all over the place.. Can be done... you just really need to know how to weld it... not "how"... but the actuakl procedure itself, where and how much.
If you are not confident with your pipe welding skills.....leave the flex otherise you'll have a pain in the *** on your hand. I was a pipe fitter/welder for 9 years prior to my current job... There is a lot of thermodynamics involved. Heat can be your friend ...or your enemy.
If you are not confident with your pipe welding skills.....leave the flex otherise you'll have a pain in the *** on your hand. I was a pipe fitter/welder for 9 years prior to my current job... There is a lot of thermodynamics involved. Heat can be your friend ...or your enemy.

#3
TECH Senior Member
iTrader: (17)

Have a flex joint in mine and blew it up last weekend. Running 22psi on a 4.8L and the massive borg warner 1.32AR 96mm exhaust wheel, so it didn't have much back pressure. Few too many heat cycles and they get weak. Needless to say I am removing it this weekend...
#5
TECH Regular
iTrader: (7)

There some bad information in this thread already.
Bellows (flex) is used to accommodate thermal expansion of the system and isolate vibration. It should not be used to correct misalignment caused by the weld process.
There are a variety of different materials and manufacturing methods used to produce bellows. Using the wrong bellows (type of construction, length, grade of material....) can lead to premature failure.
Should you use a bellows in your application? Absolutely.
I would without a doubt add a support for the turbo. Bracing off the engine makes perfect sense, it'll result in less movement in your crossover tube since the entire assembly will move together.
Bellows (flex) is used to accommodate thermal expansion of the system and isolate vibration. It should not be used to correct misalignment caused by the weld process.
There are a variety of different materials and manufacturing methods used to produce bellows. Using the wrong bellows (type of construction, length, grade of material....) can lead to premature failure.
Should you use a bellows in your application? Absolutely.
I would without a doubt add a support for the turbo. Bracing off the engine makes perfect sense, it'll result in less movement in your crossover tube since the entire assembly will move together.
#6
TECH Fanatic
iTrader: (4)

if your turbo is solid mounted to the frame, then you will need a flex piece to seperate the vibration/movement from your motor to the turbo that is solid mounted (unless motorplated, but that isn't the case)
It is always a good idea to run some kind of support for your turbo to reduce the weight/stress on your hot side that everything is hanging on.
a flex joint has nothing to do with "welding a kit together"....
here is a picture of my turbo support I made. It's made out of some chromoly round bar and a few chassis tabs. one part bolts to a water pump bolt, and the lower part bolts to one of the alternator bolts. it's rather simple, but reduces a lot of weight/stress from the hot side
It is always a good idea to run some kind of support for your turbo to reduce the weight/stress on your hot side that everything is hanging on.
a flex joint has nothing to do with "welding a kit together"....
here is a picture of my turbo support I made. It's made out of some chromoly round bar and a few chassis tabs. one part bolts to a water pump bolt, and the lower part bolts to one of the alternator bolts. it's rather simple, but reduces a lot of weight/stress from the hot side
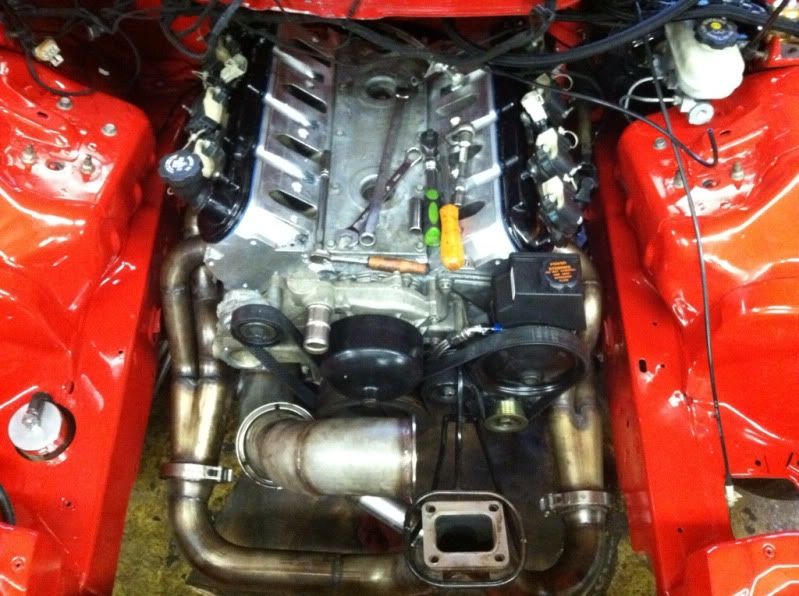
#7
TECH Addict
iTrader: (8)

There some bad information in this thread already.
Bellows (flex) is used to accommodate thermal expansion of the system and isolate vibration. It should not be used to correct misalignment caused by the weld process.
There are a variety of different materials and manufacturing methods used to produce bellows. Using the wrong bellows (type of construction, length, grade of material....) can lead to premature failure.
Should you use a bellows in your application? Absolutely.
I would without a doubt add a support for the turbo. Bracing off the engine makes perfect sense, it'll result in less movement in your crossover tube since the entire assembly will move together.
Bellows (flex) is used to accommodate thermal expansion of the system and isolate vibration. It should not be used to correct misalignment caused by the weld process.
There are a variety of different materials and manufacturing methods used to produce bellows. Using the wrong bellows (type of construction, length, grade of material....) can lead to premature failure.
Should you use a bellows in your application? Absolutely.
I would without a doubt add a support for the turbo. Bracing off the engine makes perfect sense, it'll result in less movement in your crossover tube since the entire assembly will move together.
Ive never used a flex.....built a few setups... never had a crack or failure or anything related.
I agree if you brace the turbo to the frame... isolate it from the engine if not solid mounted.. So many variables.... I dont agree, and I dont disagree...


Trending Topics
#8

https://ls1tech.com/forums/showthrea...+88mm+lq9+blow
That's my build thread. I have first hand experience with this. 42lb turbo, no flexpipe and a brace to help hold the turbo. After initial startup and a few heat cycles, leaks developed at the vbands. Taking off the vband revealed that everything had moved around after the heat cycles about a quart inch. We cut/realigned/rewelded and it hasn't moved or produced any leaks since. Then I swapped turbos and could no longer use the support bracket. Its been about 5k miles of street driving and no issues with warping, cracking or exhaust leaks, fingers crossed! There's pics of all the piping, flanges and support brackets in the build thread above.
That's my build thread. I have first hand experience with this. 42lb turbo, no flexpipe and a brace to help hold the turbo. After initial startup and a few heat cycles, leaks developed at the vbands. Taking off the vband revealed that everything had moved around after the heat cycles about a quart inch. We cut/realigned/rewelded and it hasn't moved or produced any leaks since. Then I swapped turbos and could no longer use the support bracket. Its been about 5k miles of street driving and no issues with warping, cracking or exhaust leaks, fingers crossed! There's pics of all the piping, flanges and support brackets in the build thread above.
#10
9 Second Club

the bends may take up some flex, but ideally you need a double or triple sleeved slip joint there. That will allow for expansion/contraction between the two sides.
And regardless of anything else, the turbo should not be left to hang on the pipework. It should always have some support so there is minimal weight hanging on the pipes.
And regardless of anything else, the turbo should not be left to hang on the pipework. It should always have some support so there is minimal weight hanging on the pipes.