Engine Break in Theory
#42
Teching In
iTrader: (3)
Join Date: Jul 2005
Location: Ashville, NY
Posts: 48
Likes: 0
Received 0 Likes
on
0 Posts


Adding a little to NC's very well written post, I'll give my two cents from an component engineer's perspective:
Engine components are machined to what we think are the correct geometry (size, form, and surface finish). FEA and other dynamic modeling tools give some insight as to how a component deforms under heat and load, and the component size and form can be adjusted so that near optimum geometry is achieved at worst case (heat and load) conditions. It might be a compromise because the components have to work together at less than worst case conditions too. Two good examples of this are the barrel and crown profiles on piston lands and skirts, and roller followers.
If component is sized incorrectly, or if the form and surface finish is way off, the performance, reliability, or durability of the component will be affected, and there isn't much that can be done from a break in perspective to correct a size, or gross form or surface finish issue (cylinder bores, ring gaps, or bearings clearances too tight or too loose or way out of round), they are what they are, and a good or bad break in won't have much of an impact.
The purpose of an engine break in is to allow the engine to correct slight form errors and surface finish anomalies. Designers and engineers take their best shot at determining the proper form and finish for a component, but limitations in machining process and measurement capabilities produce variations from what is thought to be the "ideal" form and finish. At the end of the day, the engine determines what the correct form and surface finish is, and that is the goal of break in - let the engine finish "machining" the components for the best fit under worst case operating conditions.
When an engine is first started, there will be asperity contact (microscopic material peaks extending above the oil film) between mating surfaces. The purpose of the break in is to gently remove the asperities and flush them from the mating surfaces.
Once the engine and fluids are brought up to operating temperature, the engine should be lightly loaded at moderate speeds This allows for initial contact of the largest asperities to occur. The engine is operated at this condition for a few minutes to allow these initial peaks to either wear or break away. The next step is to flush the material just removed from the joint and allow it to cool by going back to a light load and lower speed for a few minutes. Now go back and add a little more load and speed and do some more "machining" of the asperity peaks for a few minutes, and then drop the speed and load to flush the particles and cool again. This process is repeated until rated speed and power is achieved; and ideally all the asperity contact is eliminated, and the mating components are now operating on a film of oil with no metal to metal contact.
The key to a good break in is progressive loading and unloading of the engine to machine away asperities and then flush and cool the mating surfaces. Done correctly, this process will remove the bulk of the asperity contact and establish good running surfaces. Done incorrectly, and the asperities will not be removed, or worst case they will be smeared or transferred to mating surfaces, potentially resulting in a failure. The failure can be immediate and catastrophic, or it might just result in reduced durability. The goal of a break in is pretty clear, the debate centers more around how to achieve it or if it's needed.
So in general, this is why most engine manufacturers recommend varied engine speed and load on a new vehicle, and or sometimes limit full throttle or max rpm operation for some period of mileage. They are giving some guidelines to help promote the elimination of asperity contact and flushing the of the mating surfaces. If an engine is not highly loaded (push mower), or is not expected to have a long service life (top fuel dragster), then no break in is required.
As for the purpose of the initial oil change shortly after starting the engine, two factors should be considered:
1) The cleanliness of the engine components and the environment that the engine was assembled in.
2) The engine is generating some microscopic chips during the break in, and the filter may not be effective at removing these small particles.
Even if the engine manufacturer doesn't recommend it, that initial oil and filter change is cheap insurance...
As for the debate between using synthetic or conventional motor oil during break in, that's a topic unto itself, However, as someone mentioned, more and more engine manufacturers are using full synthetic oil as the factory fill, although it might be a good idea after a rebuild of traditional iron small block or big block. My recommendation would be to use conventional oil for a rebuilt "old engine". Newer engines that generally use harder materials, run closer clearances, and operate at higher temperatures might need the benefits of synthetic oil right from the start.
Okay, maybe that was a little more than two cents...
Engine components are machined to what we think are the correct geometry (size, form, and surface finish). FEA and other dynamic modeling tools give some insight as to how a component deforms under heat and load, and the component size and form can be adjusted so that near optimum geometry is achieved at worst case (heat and load) conditions. It might be a compromise because the components have to work together at less than worst case conditions too. Two good examples of this are the barrel and crown profiles on piston lands and skirts, and roller followers.
If component is sized incorrectly, or if the form and surface finish is way off, the performance, reliability, or durability of the component will be affected, and there isn't much that can be done from a break in perspective to correct a size, or gross form or surface finish issue (cylinder bores, ring gaps, or bearings clearances too tight or too loose or way out of round), they are what they are, and a good or bad break in won't have much of an impact.
The purpose of an engine break in is to allow the engine to correct slight form errors and surface finish anomalies. Designers and engineers take their best shot at determining the proper form and finish for a component, but limitations in machining process and measurement capabilities produce variations from what is thought to be the "ideal" form and finish. At the end of the day, the engine determines what the correct form and surface finish is, and that is the goal of break in - let the engine finish "machining" the components for the best fit under worst case operating conditions.
When an engine is first started, there will be asperity contact (microscopic material peaks extending above the oil film) between mating surfaces. The purpose of the break in is to gently remove the asperities and flush them from the mating surfaces.
Once the engine and fluids are brought up to operating temperature, the engine should be lightly loaded at moderate speeds This allows for initial contact of the largest asperities to occur. The engine is operated at this condition for a few minutes to allow these initial peaks to either wear or break away. The next step is to flush the material just removed from the joint and allow it to cool by going back to a light load and lower speed for a few minutes. Now go back and add a little more load and speed and do some more "machining" of the asperity peaks for a few minutes, and then drop the speed and load to flush the particles and cool again. This process is repeated until rated speed and power is achieved; and ideally all the asperity contact is eliminated, and the mating components are now operating on a film of oil with no metal to metal contact.
The key to a good break in is progressive loading and unloading of the engine to machine away asperities and then flush and cool the mating surfaces. Done correctly, this process will remove the bulk of the asperity contact and establish good running surfaces. Done incorrectly, and the asperities will not be removed, or worst case they will be smeared or transferred to mating surfaces, potentially resulting in a failure. The failure can be immediate and catastrophic, or it might just result in reduced durability. The goal of a break in is pretty clear, the debate centers more around how to achieve it or if it's needed.
So in general, this is why most engine manufacturers recommend varied engine speed and load on a new vehicle, and or sometimes limit full throttle or max rpm operation for some period of mileage. They are giving some guidelines to help promote the elimination of asperity contact and flushing the of the mating surfaces. If an engine is not highly loaded (push mower), or is not expected to have a long service life (top fuel dragster), then no break in is required.
As for the purpose of the initial oil change shortly after starting the engine, two factors should be considered:
1) The cleanliness of the engine components and the environment that the engine was assembled in.
2) The engine is generating some microscopic chips during the break in, and the filter may not be effective at removing these small particles.
Even if the engine manufacturer doesn't recommend it, that initial oil and filter change is cheap insurance...
As for the debate between using synthetic or conventional motor oil during break in, that's a topic unto itself, However, as someone mentioned, more and more engine manufacturers are using full synthetic oil as the factory fill, although it might be a good idea after a rebuild of traditional iron small block or big block. My recommendation would be to use conventional oil for a rebuilt "old engine". Newer engines that generally use harder materials, run closer clearances, and operate at higher temperatures might need the benefits of synthetic oil right from the start.
Okay, maybe that was a little more than two cents...
#43

well written.
Perhaps this is/was why I was always told to scotchbrite the skirts on pistons prior to final assy.
I had always assumed it was to put a little surface texture for oil retention purposes.
Perhaps this is/was why I was always told to scotchbrite the skirts on pistons prior to final assy.
I had always assumed it was to put a little surface texture for oil retention purposes.
#44
Teching In
iTrader: (3)
Join Date: Sep 2007
Location: Lansing, MI, USA
Posts: 21
Likes: 0
Received 0 Likes
on
0 Posts

All right, so all things considered; When a Brand new GM motor in installed in the factory, the last thing we do is chassis dyno the car, and not nicely...Basically a street race scenario... idle to 30MPH... then full bore up to the rev limiter in fourth in a manual... All 30 seconds after it gets started for the first time... Consider this post knowing who sells more engines, and who has more failures. I've witnessed it in first hand on the Grand Am's then the Malibus, then the CTS's, CTS-V's, SRX's, STS's, and STS-V's. The owner's manual clearly states to vary load, speed, and throttle input for the first 500 miles. My cousin made fun of me for varying my speed on the highway between 45 and 80 on the Reverend. The laughter stopped when a 600 mile '01 SS M6 took his '98Z A4 with a mild cam, the first, and second time.
[B]In short Do what the General tells you. 99 years in business should account for something.
[B]In short Do what the General tells you. 99 years in business should account for something.
#46
TECH Enthusiast
iTrader: (12)
Join Date: Aug 2007
Location: Rutland, MA
Posts: 590
Likes: 0
Received 0 Likes
on
0 Posts


Heat the oil in a pot of boiling water. Dump it in the motor, prime it (when possible). Fire it off, check for leaks, noises and get a good ballpark tune on it. Take it up through the rpms and check for oil pressure and a/f. Start making pulls. Change the oil after the first few pulls to check for foreign material in the filter. Put it in the car and run the ***** off it.
#48
TECH Resident
iTrader: (3)

Funny thing is, when I was a Development Engineer we never conducted break in on our test vehicles. When you had a test to conduct, whether the vehicle had 1 mile on it or 500 you would run them as is.
#49
TECH Apprentice
iTrader: (28)

I built the engine attached to this post and took it back over to Reher Morrison to put on the dyno for tuning. We started it, ran it between 2500-3500 RPM until the oil temperature was 130 degrees (10-15 minutes). Adjusted valve lash. Started it and ran it up to 5500 RPM, shut it down, and adjusted/checked valve lash. After that it was WOT pulls to 7500 RPM adjusting timing & jets in between pulls until peak power and optimum A/F ratio was obtained. Rings are broke in within 15 -20 minutes. If you have moving metal parts that are making contact rather than riding on a oil film and require some sort of break-in then you have other issues to worry about.
#51
On The Tree
Join Date: Jan 2008
Location: Where you least expect me
Posts: 100
Likes: 0
Received 0 Likes
on
0 Posts


I think what's been said needs to be clarified.
Bearings do not break in. Period. We should all already know this. The surface finish and roundness/taper requirements for bearing journals and bores are such that there are no asperities thicker than the oil film.
The breakin happens not only at the ring to bore interface, but also at the ring to piston interface. Rings rotate in the grooves as the engine runs. The cut angle on the bore hone causes this. As the rings rotate under load in either direction, they polish the piston ring grooves as well as the bores.
To a great extent, modern bore prep techniques, such as plateau brush honing eliminate a lot of bore break in and result in a ready-to-run bore, but nothing is perfect.
The myth of the soft breakin probably came from a few people who spun bearings thanks to breakin debris in their oil. It's not that the filter doesn't catch breakin debris... it's that an engine's redline RPM oil flow is WAY more than a filter can handle at a reasonable pressure drop. As the RPM climbs, oil flow volume rises and the bypass valve lifts and more of the engine's oil bypasses the filter. This can potentially pump breakin debris directly to the engine's bearings.
Moral of the story: If you can build a remote filter system of very great flow capacity, then you don't have to be very zealous about changing your oil for your breakin, and you can whip it hard right from the first crank without worry about detriment.
Bearings do not break in. Period. We should all already know this. The surface finish and roundness/taper requirements for bearing journals and bores are such that there are no asperities thicker than the oil film.
The breakin happens not only at the ring to bore interface, but also at the ring to piston interface. Rings rotate in the grooves as the engine runs. The cut angle on the bore hone causes this. As the rings rotate under load in either direction, they polish the piston ring grooves as well as the bores.
To a great extent, modern bore prep techniques, such as plateau brush honing eliminate a lot of bore break in and result in a ready-to-run bore, but nothing is perfect.
The myth of the soft breakin probably came from a few people who spun bearings thanks to breakin debris in their oil. It's not that the filter doesn't catch breakin debris... it's that an engine's redline RPM oil flow is WAY more than a filter can handle at a reasonable pressure drop. As the RPM climbs, oil flow volume rises and the bypass valve lifts and more of the engine's oil bypasses the filter. This can potentially pump breakin debris directly to the engine's bearings.
Moral of the story: If you can build a remote filter system of very great flow capacity, then you don't have to be very zealous about changing your oil for your breakin, and you can whip it hard right from the first crank without worry about detriment.
#52
On The Tree
Join Date: Jan 2008
Location: Where you least expect me
Posts: 100
Likes: 0
Received 0 Likes
on
0 Posts


OBTW, what stones are used to hone GIII/IV bores?
I'm in the process of building a Caddy Northstar, which is technologically similar to an LS1, and had bad luck the first time around because the shop used silicon carbide stones to hone the bores. The Caddy bore liners are EXTREMELY hard and the combo of the hard stone on the hard iron only burnished the bores and didn't actually hone them. The Caddy has to be honed with aluminum oxide stones, which are softer than silicon carbide.
Are the GIII/IV engines the same way?
I'm in the process of building a Caddy Northstar, which is technologically similar to an LS1, and had bad luck the first time around because the shop used silicon carbide stones to hone the bores. The Caddy bore liners are EXTREMELY hard and the combo of the hard stone on the hard iron only burnished the bores and didn't actually hone them. The Caddy has to be honed with aluminum oxide stones, which are softer than silicon carbide.
Are the GIII/IV engines the same way?
#53

lingenfelter's is here in town. a good friend of mine had them assemble his 403 ls2 and when he asked about the "break in", the builder chuckled and said "there is no break in, it's ready to go." lol.
#54
Launching!
Join Date: Apr 2007
Location: College Station, TX
Posts: 264
Likes: 0
Received 0 Likes
on
0 Posts

There is EDM (Electro Discharge Machining), where electricity is used to make electrons bombard a surface and leave small craters. The most common form is the Wire EDM.
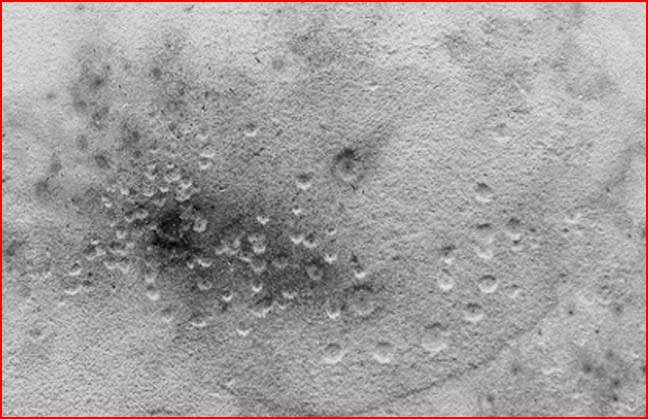

A Wire EDM would prove very fast in manufacturing. The wire would just skim the surface of the cylinder 360 degrees and move to the next one. All 8 could actually be done all at once. The downside is that the craters might not be the shape we are looking for.
There is also Electrochemical Machining, another non-traditional process. It works by anodizing (corroding) the surface and washing away the loose particles.

ECM is very slow, but precise. It is even used to cut the tips of needles (like the doctor uses) so that there are no burrs. The ECM could cut perfect circles or a spiral down the cylinder wall with no burrs. Unfortunately, it would probably take an hour (unprofessional estimation) for each cylinder. Although, there would be no seal break-in with this process. It would probably yield a cylinder that has a much more efficient seal than engines today.

I would also recommend a laser, but I don't know if it could reach into the depths of the cylinder; however, it would be a reletively fast process.
#55

I have a brand new forged short block, pp stage 2 performance heads and 220/230 .581/.592 115lsa+1 comp cam. My question is that I am also running a vortec supercharger on this set up and should I break the motor in with the supercharger ingaged or not ingaged? Max boost is 10 lbs, also running diamond pistons and diamond racing rings.
#56
TECH Regular

The day when everyone has a blowby meter won't come soon enough. We dyno at partial load until blowby falls to a plateau then start our testing regimin. The rounder the bores and rings, the quicker it breaks in. Iron rings make life easy, but steel rings better be manufactured perfectly.
Going with dino oil is a good idea. I've had customers try synthetic right off the bat then have oiling issues. To fix, fresh hone-new rings-with dino oil-problem fixed. Can I say that it's the oils fault? well...the machinists that did the work both times is very good.
One thing that IS a good idea to do is put synthetic oil IN THE RING GROOVES ONLY before putting the rings in..then dino oil in the pan and Dextron on the walls. This reduces the chances of microwelding.
A well machined block, crank, and piston can be beat upon almost immediately.
Going with dino oil is a good idea. I've had customers try synthetic right off the bat then have oiling issues. To fix, fresh hone-new rings-with dino oil-problem fixed. Can I say that it's the oils fault? well...the machinists that did the work both times is very good.
One thing that IS a good idea to do is put synthetic oil IN THE RING GROOVES ONLY before putting the rings in..then dino oil in the pan and Dextron on the walls. This reduces the chances of microwelding.
A well machined block, crank, and piston can be beat upon almost immediately.
#57
On The Tree
iTrader: (1)
Join Date: Jun 2008
Location: Archie, MO
Posts: 196
Likes: 0
Received 0 Likes
on
0 Posts


ok so i know this is kindof an old post but i need an idea. all the replies have been about street car. now what about track car that will only see the 1/4 mile as mine will. i pulled the motor of the wkend to do a refresh (my first time in an ls1, mainly build yamaha banshee motors for my background knowlegde with motors). my motor had just under 155,000 so i figured it was a good time to put new rings in and check out the bearings and all the other fun stuff. its also gettting a 400 turbo with no electric hook ups so i wont have the speed or the odo (i assume). i plan on using my 90% of the stock parts (maybe new cam, def polishing on the heads) sorry for the rambling, just letting everyone know what my plans are. back on track, what would be the best way to break mine in (and anyone else in my shoes) also no paved roads close to me that i can take a run on (one down side of living in the country on gravel)
#59

The day when everyone has a blowby meter won't come soon enough. We dyno at partial load until blowby falls to a plateau then start our testing regimin. The rounder the bores and rings, the quicker it breaks in. Iron rings make life easy, but steel rings better be manufactured perfectly.
Going with dino oil is a good idea. I've had customers try synthetic right off the bat then have oiling issues. To fix, fresh hone-new rings-with dino oil-problem fixed. Can I say that it's the oils fault? well...the machinists that did the work both times is very good.
One thing that IS a good idea to do is put synthetic oil IN THE RING GROOVES ONLY before putting the rings in..then dino oil in the pan and Dextron on the walls. This reduces the chances of microwelding.
A well machined block, crank, and piston can be beat upon almost immediately.
Going with dino oil is a good idea. I've had customers try synthetic right off the bat then have oiling issues. To fix, fresh hone-new rings-with dino oil-problem fixed. Can I say that it's the oils fault? well...the machinists that did the work both times is very good.
One thing that IS a good idea to do is put synthetic oil IN THE RING GROOVES ONLY before putting the rings in..then dino oil in the pan and Dextron on the walls. This reduces the chances of microwelding.
A well machined block, crank, and piston can be beat upon almost immediately.
I have always used the easy 500 mile break in proceedure with the 20 minute warm up to get parts accustomed to each other on initial start up with good results. I guess it could all be old school techniques considering I built my first engine back in 92'. The one thing that does bother me about LSX motors though is that there is no way to prime them. So you are relying on assembly lube to get the job done.