Out of curiousity why does everyone use 2.5" on the crossover pipe
#361
#364

The first time the concept was introduced to me was when it was explained that the energy contained in a gas (enthalpy) is a function of temperature only (NOT pressure). In other words, 1000 deg F gas has the same amount of energy at 14.7 psia as it does at 100 psia.
Edit: Sometimes when trying understand the science, it's best to start with an open mind. I had been rebuilding engines and racing before going to engineering school. I disagreed with the professors and books many times because of what I thought I knew and what I had been told by other racers. In the end, I was wrong on many accounts, including this one.
Edit: Sometimes when trying understand the science, it's best to start with an open mind. I had been rebuilding engines and racing before going to engineering school. I disagreed with the professors and books many times because of what I thought I knew and what I had been told by other racers. In the end, I was wrong on many accounts, including this one.
Enthalpy (H) - The sum of the internal energy of the system plus the product of the pressure of the gas in the system and its volume.
Pressure is inherent to the enthalpy change that drives a turbo. In the case of a car having lag and suddenly spooling a turbo with more RPM (and obviously exhaust gas volume), its a combination of temperature and pressure change, but I'd wager the volume*pressure component is significantly larger than the E component in the enthalpy equation on turbocharged internal combustion engine.
Edit - more directly. Air at 14.7 psia on either side of a turbine, with it 1000 F on the hot side, would not spool the turbine, but air at room temp on either side and 14.7 psia at outlet, 25 psia at inlet, would spool it no problem - hence why I say its because it allows for a faster pressure buildup. If you let pressure drop - of course temperature will drop, they are obviously interconnected, but temperature itself is only one factor - the cooling of the exhaust gas in this case is because of expansion through pressure change.
Last edited by Bimmerdude; 02-07-2014 at 05:18 AM.
The following users liked this post:
n2xlr8n66 (09-04-2021)
#365

Great topic. Back in November when my fabricator got my car to build my turbo set up I was all set on going 2.5" and right as he was ready to go he asked why not 2.25". I had to make a decision quick and did some research, made some calls but it was hard to find any kind of definitive answer due to the variations from combo to combo. Ultimately I choose to go with the 2.25" mainly because whether or not it increased velocity, pressure or spool time it wasn't small enough to cause a restriction in power up to the 1000RWHP or so.
#366

I remember my thermo class a bit differently from you on this one, enthalpy is a combined measure of all of the parts of energy. ...
Enthalpy (H) - The sum of the internal energy of the system plus the product of the pressure of the gas in the system and its volume.....
Enthalpy (H) - The sum of the internal energy of the system plus the product of the pressure of the gas in the system and its volume.....
"...for an ideal gas, the internal energy is a function of temperature alone!"
"...the internal energy of an ideal gas is a function of temperature only is known as Joules's law"
"We can also show that enthalpy of an ideal gas is a function of temperature only."
"For an ideal gas the definition of enthalpy, h=u+pv, gives us h=u+RT"
Relating this to the turbine, the first law of thermo is:
q=w+h2-h1+(V2^2-V1^2)/2+g(z2=z1)
Since you're not adding heat to the turbine, q=0. I did some quick and dirty math and found that V2 and V1 are close enough to cancel each other out, and potential energy change is negligible. Therefore, it simplifies to
w=h1-h2
And as stated above, h is a function of temperature alone. Therefore, the work done by a turbine is a function of the temperature change of the gas passing through it only, or
w=f(T1)-f(T2)
This is bringing back bad memories of homework sessions extending to 4 am.
Note that if all this weren't true, a gas turbine could not operate. Even though the pressure change and mass flow rate through the turbine and compressor are identical, the turbine produces about 1.5 times more power than the compressor absorbs. It is able to do this because the temperature change across the turbine is much greater than the temperature change across the compressor.
Think of this. . . you can extract work from a hot gas without undergoing a pressure drop (though possible, it's not typically practical). You can't extract work from a hot gas without undergoing a temperature drop.
Last edited by engineermike; 02-08-2014 at 11:08 AM.
#367

I think we are arguing semantics - PV=nRT and nR is a pair of constants.
My point is that because the dynamic response of the turbo is related to pressure induced spooling (I understand that in an all out environment you wouldn't follow this logic - street car rules I think we can), maintaining a minimal volume will allow the pressure to raise more quickly, allowing for earlier and faster spool.
Everything you've said I would agree with for a jet turbine, but on an automobile we aren't going to design a 90% efficient system in our garages.
I also have been thinking that it makes sense to step the crossover (back on topic of the thread), I'd be curious if anyone has taken EGT readings at different points along a crossover.
This whole conversation makes me think it might make some sense to follow the header primaries rule and account for cooling but maintain velocity/temperature by reducing volume (cross section) as you approach the turbo?
My point is that because the dynamic response of the turbo is related to pressure induced spooling (I understand that in an all out environment you wouldn't follow this logic - street car rules I think we can), maintaining a minimal volume will allow the pressure to raise more quickly, allowing for earlier and faster spool.
Everything you've said I would agree with for a jet turbine, but on an automobile we aren't going to design a 90% efficient system in our garages.
I also have been thinking that it makes sense to step the crossover (back on topic of the thread), I'd be curious if anyone has taken EGT readings at different points along a crossover.
This whole conversation makes me think it might make some sense to follow the header primaries rule and account for cooling but maintain velocity/temperature by reducing volume (cross section) as you approach the turbo?
#368

Though I'd share. I'm putting together a mild combo and will hopefully be ready in the coming months. I went ahead and ordered/received 2" material for my up pipes and will merge it into a 10" piece of 2.5". I'll set the 2.5" about 1" passed the inlet flange into the exhaust housing.
I'll have an apples to oranges comparison at best, but I figured once it's done and I get a good datalog from the new set up I'd post what I find.
I'll have an apples to oranges comparison at best, but I figured once it's done and I get a good datalog from the new set up I'd post what I find.
#369

I also have been thinking that it makes sense to step the crossover (back on topic of the thread), I'd be curious if anyone has taken EGT readings at different points along a crossover.
This whole conversation makes me think it might make some sense to follow the header primaries rule and account for cooling but maintain velocity/temperature by reducing volume (cross section) as you approach the turbo?
This whole conversation makes me think it might make some sense to follow the header primaries rule and account for cooling but maintain velocity/temperature by reducing volume (cross section) as you approach the turbo?
#370

For you guys using a 2.25 crossover, how are you dealing with the merge, or more importantly the flange for a T4.
My original plan was to build the passenger side to bend upwards (manifolds down and forward) into the T4 flange by itself, and then build the drivers side and have it merge into the passenger side pipe wherever fitment allowed. 2.25 from the manifolds to the T4. The problem is the major size difference between a T4 flange and a round 2.25 pipe. So I was going to use a 2.25 to 3 inch cone and weld the T4 flange to the reshaped 3 inch pipe. Someone even recommended using a T4 flange that's made with a 2.25 round opening and bolting that straight to the rectangular T4 turbine.
Just curious how you guys are dealing with this. I would really like to find a decent 2-1 merge that goes from 2.25 to 3 and use that.
My original plan was to build the passenger side to bend upwards (manifolds down and forward) into the T4 flange by itself, and then build the drivers side and have it merge into the passenger side pipe wherever fitment allowed. 2.25 from the manifolds to the T4. The problem is the major size difference between a T4 flange and a round 2.25 pipe. So I was going to use a 2.25 to 3 inch cone and weld the T4 flange to the reshaped 3 inch pipe. Someone even recommended using a T4 flange that's made with a 2.25 round opening and bolting that straight to the rectangular T4 turbine.
Just curious how you guys are dealing with this. I would really like to find a decent 2-1 merge that goes from 2.25 to 3 and use that.
#371

For you guys using a 2.25 crossover, how are you dealing with the merge, or more importantly the flange for a T4.
My original plan was to build the passenger side to bend upwards (manifolds down and forward) into the T4 flange by itself, and then build the drivers side and have it merge into the passenger side pipe wherever fitment allowed. 2.25 from the manifolds to the T4. The problem is the major size difference between a T4 flange and a round 2.25 pipe. So I was going to use a 2.25 to 3 inch cone and weld the T4 flange to the reshaped 3 inch pipe. Someone even recommended using a T4 flange that's made with a 2.25 round opening and bolting that straight to the rectangular T4 turbine.
Just curious how you guys are dealing with this. I would really like to find a decent 2-1 merge that goes from 2.25 to 3 and use that.
My original plan was to build the passenger side to bend upwards (manifolds down and forward) into the T4 flange by itself, and then build the drivers side and have it merge into the passenger side pipe wherever fitment allowed. 2.25 from the manifolds to the T4. The problem is the major size difference between a T4 flange and a round 2.25 pipe. So I was going to use a 2.25 to 3 inch cone and weld the T4 flange to the reshaped 3 inch pipe. Someone even recommended using a T4 flange that's made with a 2.25 round opening and bolting that straight to the rectangular T4 turbine.
Just curious how you guys are dealing with this. I would really like to find a decent 2-1 merge that goes from 2.25 to 3 and use that.
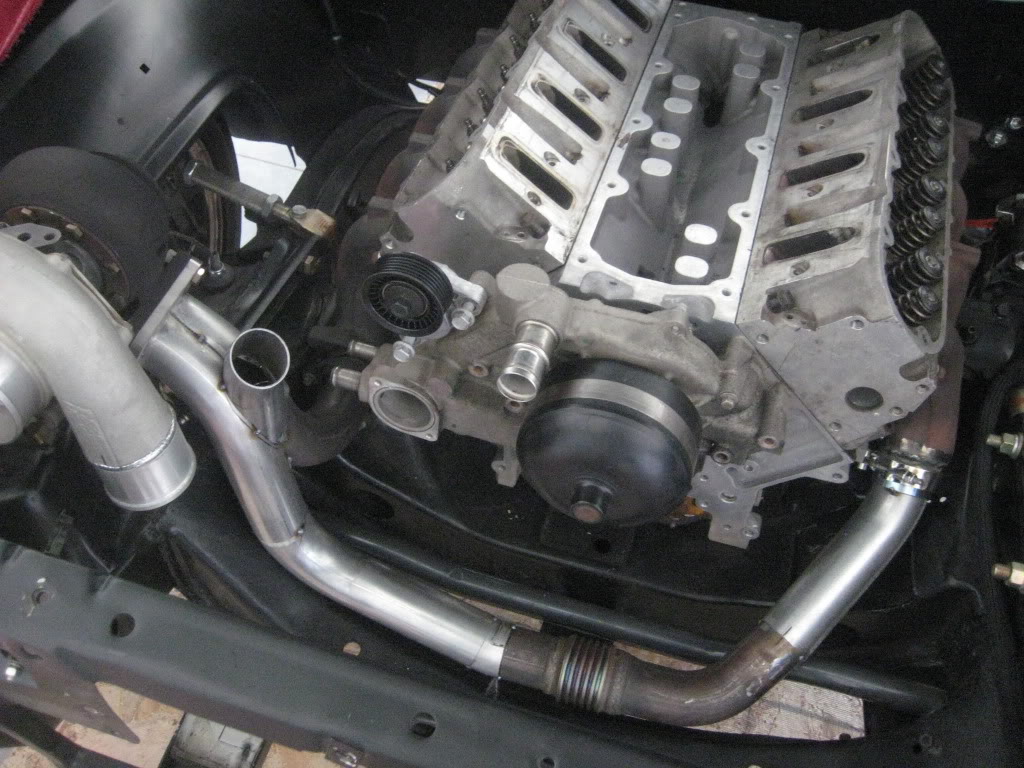

But also have done it similiar to what you are thinking of doing using a 2.25 to 2.5 Y and a 2.5 to T4 transition from Columbia River.
#372

For you guys using a 2.25 crossover, how are you dealing with the merge, or more importantly the flange for a T4.
My original plan was to build the passenger side to bend upwards (manifolds down and forward) into the T4 flange by itself, and then build the drivers side and have it merge into the passenger side pipe wherever fitment allowed. 2.25 from the manifolds to the T4. The problem is the major size difference between a T4 flange and a round 2.25 pipe. So I was going to use a 2.25 to 3 inch cone and weld the T4 flange to the reshaped 3 inch pipe. Someone even recommended using a T4 flange that's made with a 2.25 round opening and bolting that straight to the rectangular T4 turbine.
Just curious how you guys are dealing with this. I would really like to find a decent 2-1 merge that goes from 2.25 to 3 and use that.
My original plan was to build the passenger side to bend upwards (manifolds down and forward) into the T4 flange by itself, and then build the drivers side and have it merge into the passenger side pipe wherever fitment allowed. 2.25 from the manifolds to the T4. The problem is the major size difference between a T4 flange and a round 2.25 pipe. So I was going to use a 2.25 to 3 inch cone and weld the T4 flange to the reshaped 3 inch pipe. Someone even recommended using a T4 flange that's made with a 2.25 round opening and bolting that straight to the rectangular T4 turbine.
Just curious how you guys are dealing with this. I would really like to find a decent 2-1 merge that goes from 2.25 to 3 and use that.
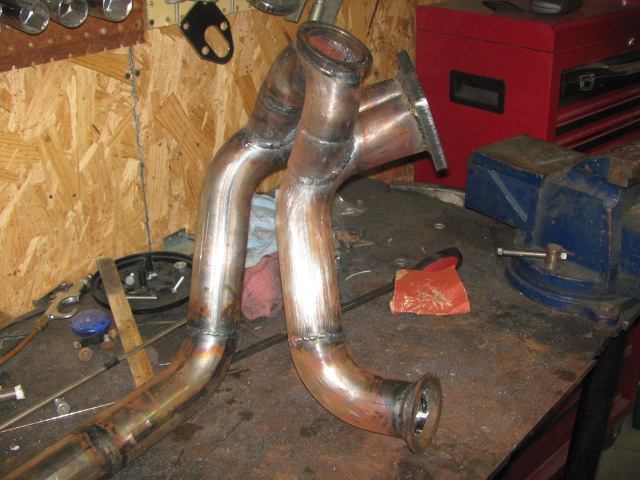

#373

Could use a t4 to 2.5" flange and bump it up at the end. I think I paid $25 for mine, couldn't find a cheaper one this time....
http://www.ebay.com/itm/T4-Undivided-to-2-5-inch-Inlet-Turbo-Flange-Transition-1-2-thick-CNC-machined-/130912462220?pt=Motors_Car_Truck_Parts_Accessories&hash=item1e7afda58c&vxp=mtr
http://www.ebay.com/itm/T4-Undivided-to-2-5-inch-Inlet-Turbo-Flange-Transition-1-2-thick-CNC-machined-/130912462220?pt=Motors_Car_Truck_Parts_Accessories&hash=item1e7afda58c&vxp=mtr
#375

Probably would've taken the time to form the ends into cones to match the ID form of the turbine housing. no gap, no turbulence when it enters, has to be worth something, maybe damn near unmeasurable, but gotta be worth something.
Im talking, slitting the pipe, knocking it in there, to form its own shape, weld it up, and grind it smooth... inside and out.
#377

I've always wanted to try this, had i not re-used an old flange i wouldve.
Probably would've taken the time to form the ends into cones to match the ID form of the turbine housing. no gap, no turbulence when it enters, has to be worth something, maybe damn near unmeasurable, but gotta be worth something.
Im talking, slitting the pipe, knocking it in there, to form its own shape, weld it up, and grind it smooth... inside and out.
Probably would've taken the time to form the ends into cones to match the ID form of the turbine housing. no gap, no turbulence when it enters, has to be worth something, maybe damn near unmeasurable, but gotta be worth something.
Im talking, slitting the pipe, knocking it in there, to form its own shape, weld it up, and grind it smooth... inside and out.
Probably helps with the sealing at the flange as well for those running higher drive pressures.
#378

Quote:
Originally Posted by HexenLord View Post
For you guys using a 2.25 crossover, how are you dealing with the merge, or more importantly the flange for a T4.
My original plan was to build the passenger side to bend upwards (manifolds down and forward) into the T4 flange by itself, and then build the drivers side and have it merge into the passenger side pipe wherever fitment allowed. 2.25 from the manifolds to the T4. The problem is the major size difference between a T4 flange and a round 2.25 pipe. So I was going to use a 2.25 to 3 inch cone and weld the T4 flange to the reshaped 3 inch pipe. Someone even recommended using a T4 flange that's made with a 2.25 round opening and bolting that straight to the rectangular T4 turbine.
Just curious how you guys are dealing with this. I would really like to find a decent 2-1 merge that goes from 2.25 to 3 and use that.
these were bends, 2-1/4" to 3" merge and 3" to t4 adapter I bought and used to make the merge I have. I know the wastegate placement isnt ideal or the greatest but it works for now and next time I build one I know better. since the 3" round to t4 was slightly bigger I had about 1/8" of cutting to do and it was a smooth transition into the flange
Originally Posted by HexenLord View Post
For you guys using a 2.25 crossover, how are you dealing with the merge, or more importantly the flange for a T4.
My original plan was to build the passenger side to bend upwards (manifolds down and forward) into the T4 flange by itself, and then build the drivers side and have it merge into the passenger side pipe wherever fitment allowed. 2.25 from the manifolds to the T4. The problem is the major size difference between a T4 flange and a round 2.25 pipe. So I was going to use a 2.25 to 3 inch cone and weld the T4 flange to the reshaped 3 inch pipe. Someone even recommended using a T4 flange that's made with a 2.25 round opening and bolting that straight to the rectangular T4 turbine.
Just curious how you guys are dealing with this. I would really like to find a decent 2-1 merge that goes from 2.25 to 3 and use that.
these were bends, 2-1/4" to 3" merge and 3" to t4 adapter I bought and used to make the merge I have. I know the wastegate placement isnt ideal or the greatest but it works for now and next time I build one I know better. since the 3" round to t4 was slightly bigger I had about 1/8" of cutting to do and it was a smooth transition into the flange
#380

Slip fitting the pipe gives pipe extra structure support. Over but joints. I do this to the pipes. Have access to a pipe expander. Any professional muffler shop will have one. And not charge much to expand one end of the pipe for a slip fit. Not only that. It will be easier to rotate the pipes if got bends and easier to mock up the pipes.