what pinion angle with S60? vibration with 1.5 degree
#21
TECH Apprentice
iTrader: (5)

^^^ Absolutely!! This is exactly what I did with mine, and NO VIBRATIONS! This is how you must set it up, or you will have a vibration. I have mine set at only a -.5 angle, and it works great on the street. The car still hooks like a bizach so Im leaving it there, because there is no vibes.
#22
TECH Veteran
iTrader: (3)

Hmm also have bad vibration problems. was thinking broke trans mount or maybe shot output shaft whatever its called that can wobble around but now think its likely this pinion angle thing.
now this stuff is pretty confusing to me but buddy is pro racer. Not sure if he should have done this or not. My trans did seem to have a bad down angle with my 4l80 and dana 60. So he shimmed heck out of the thing to get zero trans down angle to the driveshaft. Then he set the torque arm think how bmr said to.
So should he take out those shims or leave the trans to driveshaft level and then what am I supposed to set the pinion angle to..I am supposed to make it point up a bit not down?
Can someone explain this a bit simpler for me. I have terrible vibrations that get really bad as speed goes up.
I run an adjustable torque arm on my 96 and have no vibrations noticeable at all.
now this stuff is pretty confusing to me but buddy is pro racer. Not sure if he should have done this or not. My trans did seem to have a bad down angle with my 4l80 and dana 60. So he shimmed heck out of the thing to get zero trans down angle to the driveshaft. Then he set the torque arm think how bmr said to.
So should he take out those shims or leave the trans to driveshaft level and then what am I supposed to set the pinion angle to..I am supposed to make it point up a bit not down?
Can someone explain this a bit simpler for me. I have terrible vibrations that get really bad as speed goes up.
I run an adjustable torque arm on my 96 and have no vibrations noticeable at all.
#23
11 Second Club
iTrader: (37)

Your friend has unfortunately made your problem much worse by putting the transmission at a higher downward angle. I bet your tranny is pointing down more than -3*, say it's -5*. If your rear end was pointing down -1.5 then your real pinion angle is something like (p = r + t), -5 + -1.5 = -6.5. That's could be 5 degrees out of whack!
This process works for me:
1) Pick a desired pinion angle (p).
Rules of thumb for pinion angles:
0 For a pure street car
-1 to -2 Mostly street, some drag duty
-2 to -4 Drag car
2) Measure the angle of the transmission output shaft (t) by measuring off the engine's harmonic balancer or the slip yoke. If your car is level this should be 1-3* pointing down. Use - if it's pointing down, + if pointing up.
3) Calculate what angle the rear end should be with this formula.
r = rear end pinion angle
p = desired pinion angle
t = tranny angle
r = p - t
4) Adjust the torque arm rod-end to set the rear end angle to (r). Remove the driveshaft if a good flat spot isn't available on the rear end.
Examples:
1) Desired pinion angle p = -1.0*
2) Tranny pointing down r = -2.0*
3) r = -1.0 - (-2.0), r = 1.0
4) Adjust rear to point up 1*
1) Desired pinion angle p = -2.0*
2) Tranny pointing down r = -1.5*
3) r = -2.0 - (-1.5), r = -0.5
4) Adjust rear to point down -0.5*
Good explanation of pinion angles:
http://www.jimobalek.com/?p=557
This process works for me:
1) Pick a desired pinion angle (p).
Rules of thumb for pinion angles:
0 For a pure street car
-1 to -2 Mostly street, some drag duty
-2 to -4 Drag car
2) Measure the angle of the transmission output shaft (t) by measuring off the engine's harmonic balancer or the slip yoke. If your car is level this should be 1-3* pointing down. Use - if it's pointing down, + if pointing up.
3) Calculate what angle the rear end should be with this formula.
r = rear end pinion angle
p = desired pinion angle
t = tranny angle
r = p - t
4) Adjust the torque arm rod-end to set the rear end angle to (r). Remove the driveshaft if a good flat spot isn't available on the rear end.
Examples:
1) Desired pinion angle p = -1.0*
2) Tranny pointing down r = -2.0*
3) r = -1.0 - (-2.0), r = 1.0
4) Adjust rear to point up 1*
1) Desired pinion angle p = -2.0*
2) Tranny pointing down r = -1.5*
3) r = -2.0 - (-1.5), r = -0.5
4) Adjust rear to point down -0.5*
Good explanation of pinion angles:
http://www.jimobalek.com/?p=557
#24
TECH Veteran
iTrader: (3)

Your friend has unfortunately made your problem much worse by putting the transmission at a higher downward angle. I bet your tranny is pointing down more than -3*, say it's -5*. If your rear end was pointing down -1.5 then your real pinion angle is something like (p = r + t), -5 + -1.5 = -6.5. That's could be 5 degrees out of whack!
This process works for me:
1) Pick a desired pinion angle (p).
Rules of thumb for pinion angles:
0 For a pure street car
-1 to -2 Mostly street, some drag duty
-2 to -4 Drag car
2) Measure the angle of the transmission output shaft (t) by measuring off the engine's harmonic balancer or the slip yoke. If your car is level this should be 1-3* pointing down. Use - if it's pointing down, + if pointing up.
3) Calculate what angle the rear end should be with this formula.
r = rear end pinion angle
p = desired pinion angle
t = tranny angle
r = p - t
4) Adjust the torque arm rod-end to set the rear end angle to (r). Remove the driveshaft if a good flat spot isn't available on the rear end.
Examples:
1) Desired pinion angle p = -1.0*
2) Tranny pointing down r = -2.0*
3) r = -1.0 - (-2.0), r = 1.0
4) Adjust rear to point up 1*
1) Desired pinion angle p = -2.0*
2) Tranny pointing down r = -1.5*
3) r = -2.0 - (-1.5), r = -0.5
4) Adjust rear to point down -0.5*
Good explanation of pinion angles:
http://www.jimobalek.com/?p=557
This process works for me:
1) Pick a desired pinion angle (p).
Rules of thumb for pinion angles:
0 For a pure street car
-1 to -2 Mostly street, some drag duty
-2 to -4 Drag car
2) Measure the angle of the transmission output shaft (t) by measuring off the engine's harmonic balancer or the slip yoke. If your car is level this should be 1-3* pointing down. Use - if it's pointing down, + if pointing up.
3) Calculate what angle the rear end should be with this formula.
r = rear end pinion angle
p = desired pinion angle
t = tranny angle
r = p - t
4) Adjust the torque arm rod-end to set the rear end angle to (r). Remove the driveshaft if a good flat spot isn't available on the rear end.
Examples:
1) Desired pinion angle p = -1.0*
2) Tranny pointing down r = -2.0*
3) r = -1.0 - (-2.0), r = 1.0
4) Adjust rear to point up 1*
1) Desired pinion angle p = -2.0*
2) Tranny pointing down r = -1.5*
3) r = -2.0 - (-1.5), r = -0.5
4) Adjust rear to point down -0.5*
Good explanation of pinion angles:
http://www.jimobalek.com/?p=557
So all these f bodies have downward angle on the tranmissions? I didn't check pre 4l80 install. Thought had way more downangle with 4l80 due to bmr trans mount?
#25
11 Second Club
iTrader: (37)


#26
TECH Veteran
iTrader: (3)

Ok took out the shims .Bmr said shouldn't need them with 4l80 and their crossmember.
So now when measure driveshaft not trans or balancer get negative 3 and when measure read its negative 5. So is that negative 2 now.I hate math.
Bmr says to subtract the numbers so negative 5 subtract negative 3 is same as negative 5 plus positive 3 or negative 2.
Is this math right?
So to get zero now would I need to have negative 3 rear end and negative 3 driveshaft?
So what is 3 on rear and negative 3 on driveshaft postive 6? man i hate this crap.
So now when measure driveshaft not trans or balancer get negative 3 and when measure read its negative 5. So is that negative 2 now.I hate math.
Bmr says to subtract the numbers so negative 5 subtract negative 3 is same as negative 5 plus positive 3 or negative 2.
Is this math right?
So to get zero now would I need to have negative 3 rear end and negative 3 driveshaft?
So what is 3 on rear and negative 3 on driveshaft postive 6? man i hate this crap.
#27
TECH Enthusiast
iTrader: (4)
Join Date: Mar 2005
Location: Stanwood, WA
Posts: 546
Likes: 0
Received 0 Likes
on
0 Posts


You guys are making this way too complicated. Here's a picture of the proper way to set drive line angles. The front angle and the rear angle should be the same degree but opposite. Your tranny output and your pinion should be parallel. No complicated math required.
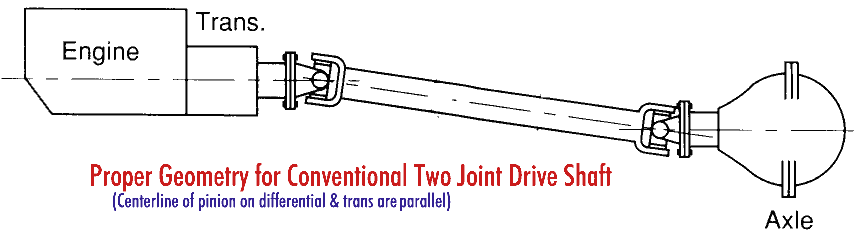
#28
TECH Veteran
iTrader: (3)

I think actually had postive driveshaft angle not negative like first thought as driveshaft is pointing up not down at back a bit.
So set torque arm to negative 2 down and if driveshaft is plus 2 this would give zero.
Traffic was heavy so coudn't try out the car at higher speeds. Maybe sunday.
If this don't work then will try to do the opposite trans angle thing. So that will likely necessitate a positive rear end angle as for sure my trans is negative angle.
If don't do that can just dial up the rear to like positive numbers and see what that does.
So anyone else with dana have to go postive to stop their vibes.?
So set torque arm to negative 2 down and if driveshaft is plus 2 this would give zero.
Traffic was heavy so coudn't try out the car at higher speeds. Maybe sunday.
If this don't work then will try to do the opposite trans angle thing. So that will likely necessitate a positive rear end angle as for sure my trans is negative angle.
If don't do that can just dial up the rear to like positive numbers and see what that does.
So anyone else with dana have to go postive to stop their vibes.?
#29
TECH Apprentice
iTrader: (4)
Join Date: Apr 2007
Location: KC
Posts: 320
Likes: 0
Received 0 Likes
on
0 Posts


I have a lot of vibration too, I had to replace the rear seal on the tailshaft and the bushing. When I put the S60 and adjusted the pinion angle I had no vibration at all. I stripped out my torque arm mount bolt off the stock tranny mount and put a new UMI relocation/crossmember mount for the Torque Arm. After all that the vibration was horrible. I think my pinion angle was set at zero. I played around with different angles and all and still sounds like crap. I broke down and took it to the shop finally and should hear back today or tomorrow.
#31
11 Second Club
iTrader: (37)

How are you measuring the tranny angle? Do not measure the driveshaft angle, measure off the crank balancer, it's the best flat surface to get the tranny angle. The driveshaft angle is not included in the equation, so it doesn't matter. That's the mistake that a lot of people make.