Morel 5315 lifter preload
#61
TECH Senior Member
iTrader: (26)

I have done it all three ways and came up with similar numbers. I ended up shooting for a little more preload then Morel calls for. I am running between .055-.065 with a 7.350 pushrod. The cylinder #5 that I was getting a goofy reeding was bled down and the push rod was easily pushing down into the plunger. So that is something you have to really pay attention to.
Now my valve train is not getting nearly as noisy after hard runs as before.
In then end tho I think all this adjusting preload with push rod length is a bunch of bullshit. Why does somebody not come out with a light weight adjustable setup that is strong is beyond me? I am so tempted to pull the trigger on stud mount Comp 1.8 ultra pros. Everybody I have contacted says they prefer stock because its proven and I get it, but what a pain in the *** IMO. / rant
Now my valve train is not getting nearly as noisy after hard runs as before.
In then end tho I think all this adjusting preload with push rod length is a bunch of bullshit. Why does somebody not come out with a light weight adjustable setup that is strong is beyond me? I am so tempted to pull the trigger on stud mount Comp 1.8 ultra pros. Everybody I have contacted says they prefer stock because its proven and I get it, but what a pain in the *** IMO. / rant
#62
TECH Enthusiast
iTrader: (6)

If your zero lash measurement was 7.263, then...
(copied from instructions)
"Step 5 -- Add the preload to your measurement from step 4, make your adjustable PR this exact length, install it, and the rockers. OK, at this point, just double check you are definitely on the base circle. It’s easy to get ahead of yourself. Now, as you tighten it, your manly vice-grip hands are going to be able to partially preload the lifters. Don’t do that. You need to find exactly zero lash on that bolt. What I found works great is to use a 3” extension and the socket as a screwdriver. Gently and slowly turn it until it requires effort to keep turning. Slightly loosen and then come back to just touching. And one more time, very slightly loose and just barely touching.
Step 6 -- Put the ratchet on or (allen wrench) very carefully so as not to rotate the bolt until you are ready. Make sure you have plenty of freedom of movement. Tighten the bolt, keeping very close track of how much the wrench rotates. It will spin relatively easily and then start requiring some real torque to go any further. Right when you hit this point, you are no longer preloading the lifter, but are actually torqueing the bolt. How much did the wrench rotate? Figure on 0.075” per rotation. Did you get 180 degrees? You just got 0.038” of preload. Did you get 360 degrees? You just got 0.075” of preload. Did you get a full turn and a half (540 degrees)? You got 0.113” of preload."
How far did you turn before it required some muscle to continue? Sounds like about 3/4 of a turn? If that's correct, then you should have around 0.0585" preload. No further torque is used until you install the real pushrods, which should be around 7.322".
Yeah man, so much conflicting/wrong info. It makes this more difficult for us first-timers. Now, don't take my above measurement as 100% fact. You should double check multiple cylinders, if not ALL. Make your pushrod slightly longer/shorter and do the above check to make sure.
As Darth mentions, the pushrods you receive from a vendor will all vary slightly but will be close to what you're after. If you arrange them in order of the measurements you need from your testing, they'll all go in the right place.
(copied from instructions)
"Step 5 -- Add the preload to your measurement from step 4, make your adjustable PR this exact length, install it, and the rockers. OK, at this point, just double check you are definitely on the base circle. It’s easy to get ahead of yourself. Now, as you tighten it, your manly vice-grip hands are going to be able to partially preload the lifters. Don’t do that. You need to find exactly zero lash on that bolt. What I found works great is to use a 3” extension and the socket as a screwdriver. Gently and slowly turn it until it requires effort to keep turning. Slightly loosen and then come back to just touching. And one more time, very slightly loose and just barely touching.
Step 6 -- Put the ratchet on or (allen wrench) very carefully so as not to rotate the bolt until you are ready. Make sure you have plenty of freedom of movement. Tighten the bolt, keeping very close track of how much the wrench rotates. It will spin relatively easily and then start requiring some real torque to go any further. Right when you hit this point, you are no longer preloading the lifter, but are actually torqueing the bolt. How much did the wrench rotate? Figure on 0.075” per rotation. Did you get 180 degrees? You just got 0.038” of preload. Did you get 360 degrees? You just got 0.075” of preload. Did you get a full turn and a half (540 degrees)? You got 0.113” of preload."
How far did you turn before it required some muscle to continue? Sounds like about 3/4 of a turn? If that's correct, then you should have around 0.0585" preload. No further torque is used until you install the real pushrods, which should be around 7.322".
Yeah man, so much conflicting/wrong info. It makes this more difficult for us first-timers. Now, don't take my above measurement as 100% fact. You should double check multiple cylinders, if not ALL. Make your pushrod slightly longer/shorter and do the above check to make sure.
As Darth mentions, the pushrods you receive from a vendor will all vary slightly but will be close to what you're after. If you arrange them in order of the measurements you need from your testing, they'll all go in the right place.
#63
TECH Enthusiast
iTrader: (6)

I have done it all three ways and came up with similar numbers. I ended up shooting for a little more preload then Morel calls for. I am running between .055-.065 with a 7.350 pushrod. The cylinder #5 that I was getting a goofy reeding was bled down and the push rod was easily pushing down into the plunger. So that is something you have to really pay attention to.
#64

I recently installed these lifters in my engine with 799 heads milled .030 using the LS9 Gasket. I checked each lifter prior to installation on how stiff the plunger was. None of the plungers would even move with me using a pushrod and all the strength I have.
My method was simple. I installed all rocker arms and bolted them down with a t handle allen wrench tight as i could. Then each cylinder I checked took those 2 rockers off used an old push rod and the checker for the other valve. Put hand pressure on them to follow them through eo and ic recorded zero lash at each base circle making small adjustments to the checker and reinstalling the rocker till zero was perfect.
My results were very surprising to find not alot of common ground between the valves so I ordered 8 different sizes through Manton.
Also I was surprised that in order to get .045 preload on some valves i still needed 7.400 length pushrods on 3 valves and on one valve I needed 7.413 to get .045 a few were 7.380 and some 7.375. 7.375 was shortest the rest were in between 7.413.
After measuring 3 times and no changes found in the initial measurements I was thinking I might have payed for head milling that didn't get done. When I asked them if they did do it they said they did. Unfortunately I dont have a burette to cc the heads and check this and none of my buddies do either. However they also installed new valves but seems to me that would only shorten the pushrod more since they didnt use new seats they just cut new angles in the old seats.
My method was simple. I installed all rocker arms and bolted them down with a t handle allen wrench tight as i could. Then each cylinder I checked took those 2 rockers off used an old push rod and the checker for the other valve. Put hand pressure on them to follow them through eo and ic recorded zero lash at each base circle making small adjustments to the checker and reinstalling the rocker till zero was perfect.
My results were very surprising to find not alot of common ground between the valves so I ordered 8 different sizes through Manton.
Also I was surprised that in order to get .045 preload on some valves i still needed 7.400 length pushrods on 3 valves and on one valve I needed 7.413 to get .045 a few were 7.380 and some 7.375. 7.375 was shortest the rest were in between 7.413.
After measuring 3 times and no changes found in the initial measurements I was thinking I might have payed for head milling that didn't get done. When I asked them if they did do it they said they did. Unfortunately I dont have a burette to cc the heads and check this and none of my buddies do either. However they also installed new valves but seems to me that would only shorten the pushrod more since they didnt use new seats they just cut new angles in the old seats.
#67

Technically it shouldn't matter because the lifter is surrounded by the oil pressure. Notice the lifters body is machined down 360 degrees that portion of the lifter will see oil all the way around it. So its totally up to you.
#70
On The Tree
iTrader: (4)

You're looking at the bolt and not the travel at the cup of the rocker. Ont he bolt, the thread pitch is 1.25mm, so one turn of the bolt lowers the center of the rocker .0.49".
BUT, the preload on the lifter is actually 2.7/1.7 or 1.588 times further than the bolt moves, because it's a lever, and the valve side is fixed when you're preloading the lifter. .049 x 1.588 = .078 is how much preload you get on one turn of the bolt.
BUT, the preload on the lifter is actually 2.7/1.7 or 1.588 times further than the bolt moves, because it's a lever, and the valve side is fixed when you're preloading the lifter. .049 x 1.588 = .078 is how much preload you get on one turn of the bolt.
See section 4, in particular 4e. "how many turns to tighten the adjuster nut
after zero-lash"
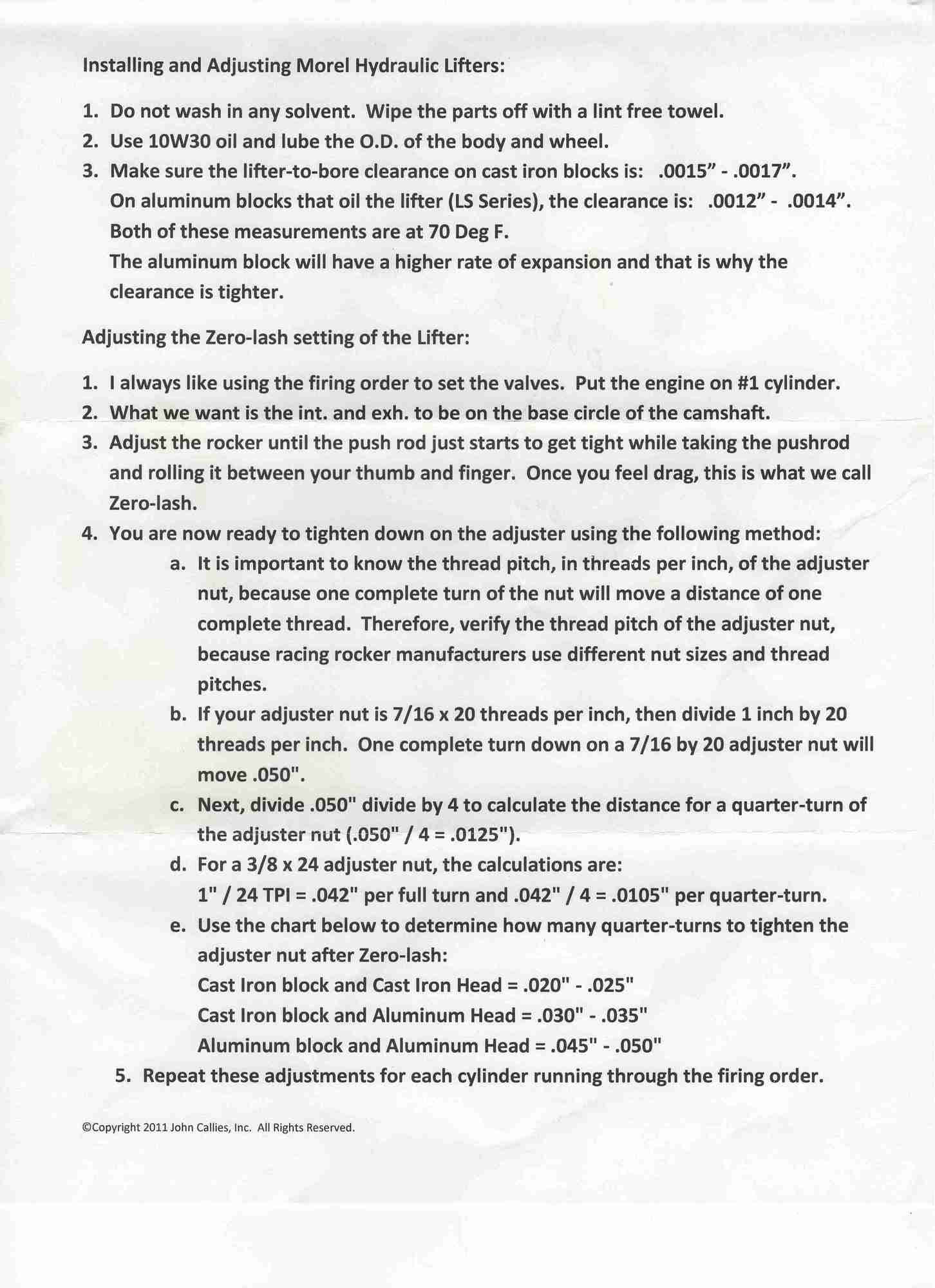
#71
10 Second Club
iTrader: (22)
Join Date: Mar 2006
Location: Northwest side of Chicago
Posts: 3,677
Likes: 0
Received 2 Likes
on
2 Posts


Bumping this up with a question.
Some have said in this thread that you want to stop measuring preload once the rocker bolt snugs and that when you torque you are not adding more preload.
Now I totally understand that once its snug and you go ahead and torque it that you are not adding anymore preload. But if using a dial indicator why not just set to 0 lash, 0 out your indicator and go ahead and torque. Then what ever the dial reads is your real world preload.
Alex
Some have said in this thread that you want to stop measuring preload once the rocker bolt snugs and that when you torque you are not adding more preload.
Now I totally understand that once its snug and you go ahead and torque it that you are not adding anymore preload. But if using a dial indicator why not just set to 0 lash, 0 out your indicator and go ahead and torque. Then what ever the dial reads is your real world preload.
Alex
#72
Moderator
iTrader: (4)
Join Date: Jul 2014
Location: My own internal universe
Posts: 10,452
Received 1,852 Likes
on
1,152 Posts


Originally Posted by SPRAYED 01
Bumping this up with a question.
Some have said in this thread that you want to stop measuring preload once the rocker bolt snugs and that when you torque you are not adding more preload.
Now I totally understand that once its snug and you go ahead and torque it that you are not adding anymore preload. But if using a dial indicator why not just set to 0 lash, 0 out your indicator and go ahead and torque. Then what ever the dial reads is your real world preload.
Alex
Some have said in this thread that you want to stop measuring preload once the rocker bolt snugs and that when you torque you are not adding more preload.
Now I totally understand that once its snug and you go ahead and torque it that you are not adding anymore preload. But if using a dial indicator why not just set to 0 lash, 0 out your indicator and go ahead and torque. Then what ever the dial reads is your real world preload.
Alex
The rocker bolt rotation method is what was being discussed. However, I only use it as a backup method.
In other words, I use the length checker and calipers to get the zero lash number. Then, i take my adjustable pushrod, add the desired preload, find dead soft touch on the rocker bolt, and count rotations to VERIFY the measurements I already obtained. As long as its close I use the caliper measurements.
#73
10 Second Club
iTrader: (22)
Join Date: Mar 2006
Location: Northwest side of Chicago
Posts: 3,677
Likes: 0
Received 2 Likes
on
2 Posts


I keep seeing people post up the sheet saying basically .020-.050 preload on the morel lifters. Then other come on and say .050-.060.
What is correct?
If you say .050-.060 where did you find that info?
What is correct?
If you say .050-.060 where did you find that info?
#74
TECH Senior Member
iTrader: (26)

.020 would be for Iron head Iron block, .030-.040 would be for Aluminum head Iron block, .040-.050 would be for all aluminum. The .050-.060 came from Martin when he was at tic performance. The 5315 plunger travel is right around .120, so .060 is right in the middle of it's range. It has been mentioned in the past that ideally you want be in the middle.
My engine seems to like 1.125-1.25 bolt turns to 22ft lbs the best with these lifters. Anything under 1 turn and I get noise after it's been ran hard. Basically .050-.060 yields the quietest operation for my setup. Ymmv
My engine seems to like 1.125-1.25 bolt turns to 22ft lbs the best with these lifters. Anything under 1 turn and I get noise after it's been ran hard. Basically .050-.060 yields the quietest operation for my setup. Ymmv