who is running pusher fans?
#23
TECH Addict

You must have used a CSR because even the standard Meziere is rated at 43 GPM. Your logic is flawed though.. the Meziere draws just 8 amps. That is not because it moves less water.. it is a more efficient way of doing the same job. Just 8 amps to turn the electric water pump... Lets do some conversions.
8 amps = 112 watts
112 watts = .15 horsepower
You could easily gain that power back by turning off the radio....
Anyway.. there are plenty of reasons to use a electric pump. Aesthetics, serviceability, simplicity. The key reason for me to switch the the electric pump was to be able to use a standard SBC roller timing set. The silly cam driven design of the LT1 pump was just another over engineered aspect of the motor.
Kris one thing you didn't mention is the hood you are using. While the stock fans may work if you have adequate hood clearance, they will not fit comfortably with a stock Camaro hood unless you use the smallest EWP available - the CSR. I was able to fit it all under a stock hood with the standard Meziere - the fan blades were to close for comfort to the pump though. This was when I was using the stock radiator.
Stock camaro hood, LS1 lid, EWP - http://joelrdevriendt.com/?p=46
8 amps = 112 watts
112 watts = .15 horsepower
You could easily gain that power back by turning off the radio....
Anyway.. there are plenty of reasons to use a electric pump. Aesthetics, serviceability, simplicity. The key reason for me to switch the the electric pump was to be able to use a standard SBC roller timing set. The silly cam driven design of the LT1 pump was just another over engineered aspect of the motor.
Kris one thing you didn't mention is the hood you are using. While the stock fans may work if you have adequate hood clearance, they will not fit comfortably with a stock Camaro hood unless you use the smallest EWP available - the CSR. I was able to fit it all under a stock hood with the standard Meziere - the fan blades were to close for comfort to the pump though. This was when I was using the stock radiator.
Stock camaro hood, LS1 lid, EWP - http://joelrdevriendt.com/?p=46
Power (Horsepower or Watts) is flow(distance) times pressure(force). W(Power)= Amps(Flow) * Volts(Pressure). Less power to the pump means less flow at the same pressure.
8amps @ 13V = 104W
745W = 1 HP
Therefore 104W = .1396HP
.1396HP will not move more water (read: Mass) the same amount of distance in the same amount of time than anything with more power than that. And that is ASSUMING 100% thermal/mechanical efficiency of the electric motor and pump (not the case... ever). Throw in the mix that the electricity comes from the alternator (belt driven) which has efficiency losses further reduces the efficiency of the system.
Check out this graph from Lingenfelter. It shows the flow rate of a 55gmp pump (not the Meziere pump) drop dramatically under pressure 6psi brought it to almost zero! So free flow versus pressure flow can vary dramatically depending on how much power is applied to the pump blades.
If the mechanical water pump pumps less water than the electric pump the mechanical water pump is using less power than the electric one. At 2000 rpms under pressure and restriction the stock LT1 Water pump moves 20GPM (half the free flow rate of the pump you list), but at 6000rpms (again under pressure and restriction) it flows 66GPM; a 53.48% increase over the FREE-FLOW rate of the electric pump you listed. What is the flow rate of the pump you listed under pressure and resistance? I called Meziere and I was informed that the 55GPM model will flow the same as the stock one at 3500rpms. But above that the stock pump will outflow the Meziere HD pump.
In drag racing this is great. 8-14 seconds at a time with minutes to hours between runs to cool down? You don't even need a water pump. It also is great in stop and go traffic. But for road racing and rally cross where the car will be over 4,000rpms for minutes with little cool down time? Mechanical is the way to go.
Mechanical water pumps have there disadvantages too. They don't work with the engine off (electric does) and the power they draw for pumping increases exponentially as the rpms rise (electric, not so much). But while a mechanical pump can't pump water through an engine that is off. They also take up less space under our space limited hoods.
Last edited by hrcslam; 06-03-2014 at 06:48 PM.
#25
11 Second Club
iTrader: (1)

You are still comparing freeflow to actual system flow.
Far as the dimwit claiming the alternator only places bearing and brush load, maybe you can find an elementary school student to teach you some basic science.
Then go jumpstart a vehicle with a dead battery and notice the idle twitch on the running car when you hook the cable to the dead battery because of the extra load placed on the alternator. If the alternator was able to output power without placing additional load on the engine then you are describing a perpetual motion machine and have solved all the world's energy problems.
Thank you hrcslam for trying to educate these people too, most of the guys who understand elementary school level science aren't stubborn enough to try and correct the stubbornly ignorant. There are a lot of lurkers that get helped by those of us persistent enough to call out stupidity when we see it though.
Far as the dimwit claiming the alternator only places bearing and brush load, maybe you can find an elementary school student to teach you some basic science.
Then go jumpstart a vehicle with a dead battery and notice the idle twitch on the running car when you hook the cable to the dead battery because of the extra load placed on the alternator. If the alternator was able to output power without placing additional load on the engine then you are describing a perpetual motion machine and have solved all the world's energy problems.
Thank you hrcslam for trying to educate these people too, most of the guys who understand elementary school level science aren't stubborn enough to try and correct the stubbornly ignorant. There are a lot of lurkers that get helped by those of us persistent enough to call out stupidity when we see it though.
#26
TECH Addict

The flow from the electric pump is significantly reduced. The electric motor will never be more efficient than a direct pump from mechanical energy. The electric motor takes mechanical energy turns it into electrical energy (alternator efficiency loss) then converts it back into mechanical energy (electric motor efficiency loss) and tries to move as much water as possible with only 112W (my door speakers use more power than this).
By the laws of everything related to physics 112W will come no where close to being able to match the 275HP of a stock LT1 driving the water pump directly. The electric motor by it's self is already less efficient at moving anything than the direct mechanical drive (mechanical drive into a mechanical pump = only frictional losses, electric to mechanical drive to mechanical pump = frictional and thermal losses), add in where that electricity comes from and the entire system is less efficient at cooling at the same input power levels.
This will result in gains in power at higher rpms though because it's using less power to cool the motor down. But it will also result in higher coolant temps at sustained high rpms (road racing, rally cross, 4.10's on an A4 doing 75mph on I-10, etc.).
Will the electric pump add power? Yes. But it won't do it from efficiency gains, it'll do it by removing power from the cooling capability.
Last edited by hrcslam; 06-03-2014 at 09:51 PM.
#27
TECH Addict

You are still comparing freeflow to actual system flow.
Far as the dimwit claiming the alternator only places bearing and brush load, maybe you can find an elementary school student to teach you some basic science.
Then go jumpstart a vehicle with a dead battery and notice the idle twitch on the running car when you hook the cable to the dead battery because of the extra load placed on the alternator. If the alternator was able to output power without placing additional load on the engine then you are describing a perpetual motion machine and have solved all the world's energy problems.
Thank you hrcslam for trying to educate these people too, most of the guys who understand elementary school level science aren't stubborn enough to try and correct the stubbornly ignorant. There are a lot of lurkers that get helped by those of us persistent enough to call out stupidity when we see it though.
Far as the dimwit claiming the alternator only places bearing and brush load, maybe you can find an elementary school student to teach you some basic science.
Then go jumpstart a vehicle with a dead battery and notice the idle twitch on the running car when you hook the cable to the dead battery because of the extra load placed on the alternator. If the alternator was able to output power without placing additional load on the engine then you are describing a perpetual motion machine and have solved all the world's energy problems.
Thank you hrcslam for trying to educate these people too, most of the guys who understand elementary school level science aren't stubborn enough to try and correct the stubbornly ignorant. There are a lot of lurkers that get helped by those of us persistent enough to call out stupidity when we see it though.
#28
Launching!
iTrader: (1)
Join Date: Aug 2013
Location: Pittsburgh, PA
Posts: 241
Likes: 0
Received 0 Likes
on
0 Posts

And that is where you are wrong sir. The 43 is free flow rating (like throwing a football down a hallway). The 66 is under pressure and restriction (like throwing a football underwater). The rep from Mezeire said so himself that the motors are not that strong vs the factory mechanical pump and he was talking about the 55GPM HD pump.
The flow from the electric pump is significantly reduced. The electric motor will never be more efficient than a direct pump from mechanical energy. The electric motor takes mechanical energy turns it into electrical energy (alternator efficiency loss) then converts it back into mechanical energy (electric motor efficiency loss) and tries to move as much water as possible with only 112W (my door speakers use more power than this).
By the laws of everything related to physics 112W will come no where close to being able to match the 275HP of a stock LT1 driving the water pump directly. The electric motor by it's self is already less efficient at moving anything than the direct mechanical drive (mechanical drive into a mechanical pump = only frictional losses, electric to mechanical drive to mechanical pump = frictional and thermal losses), add in where that electricity comes from and the entire system is less efficient at cooling at the same input power levels.
This will result in gains in power at higher rpms though because it's using less power to cool the motor down. But it will also result in higher coolant temps at sustained high rpms (road racing, rally cross, 4.10's on an A4 doing 75mph on I-10, etc.).
Will the electric pump add power? Yes. But it won't do it from efficiency gains, it'll do it by removing power from the cooling capability.
The flow from the electric pump is significantly reduced. The electric motor will never be more efficient than a direct pump from mechanical energy. The electric motor takes mechanical energy turns it into electrical energy (alternator efficiency loss) then converts it back into mechanical energy (electric motor efficiency loss) and tries to move as much water as possible with only 112W (my door speakers use more power than this).
By the laws of everything related to physics 112W will come no where close to being able to match the 275HP of a stock LT1 driving the water pump directly. The electric motor by it's self is already less efficient at moving anything than the direct mechanical drive (mechanical drive into a mechanical pump = only frictional losses, electric to mechanical drive to mechanical pump = frictional and thermal losses), add in where that electricity comes from and the entire system is less efficient at cooling at the same input power levels.
This will result in gains in power at higher rpms though because it's using less power to cool the motor down. But it will also result in higher coolant temps at sustained high rpms (road racing, rally cross, 4.10's on an A4 doing 75mph on I-10, etc.).
Will the electric pump add power? Yes. But it won't do it from efficiency gains, it'll do it by removing power from the cooling capability.
http://www.ws6.com/mod-14.htm
Being that a electric pump has a linear flow, it is actually flowing more water than the mechanical pump at lower RPMs (below 3500 I believe you said per Meziere), while using less power (as seen in the dyno graph)...
After looking over the test Lingenfelter does, the PSI is a differential from the inlet to the outlet.. not system pressure like you would see in a cooling system. They didn't even use a Meziere branded pump .. Not sure how this is a good comparison.
#29
TECH Addict

I am more of a results over numbers guy as I told you in the other thread with your pressure issue. It may look good on paper - but real world results are the true test. That being said... If the electric water pump is less efficient why does this dyno show more torque available from idle on up?
http://www.ws6.com/mod-14.htm
Being that a electric pump has a linear flow, it is actually flowing more water than the mechanical pump at lower RPMs (below 3500 I believe you said per Meziere), while using less power (as seen in the dyno graph)...
After looking over the test Lingenfelter does, the PSI is a differential from the inlet to the outlet.. not system pressure like you would see in a cooling system. They didn't even use a Meziere branded pump .. Not sure how this is a good comparison.
http://www.ws6.com/mod-14.htm
Being that a electric pump has a linear flow, it is actually flowing more water than the mechanical pump at lower RPMs (below 3500 I believe you said per Meziere), while using less power (as seen in the dyno graph)...
After looking over the test Lingenfelter does, the PSI is a differential from the inlet to the outlet.. not system pressure like you would see in a cooling system. They didn't even use a Meziere branded pump .. Not sure how this is a good comparison.
That dyno doesn't show increase in power over the entire rpm. It shows it over approx. 3250rpms. Anything less than .5% hardly qualifies as a quantifiable proof of increase or decrease (read: under 3250rpms on that graph). Hell, the 2% peak increase is within margin of error. Air Temp has a larger effect on power than that.
The actual difference in power between the two lines on that graph are immeasurable below 3250rpms. .15hp is immeasurable on the graph.....
#30
Village Troll 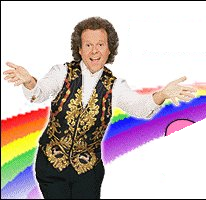
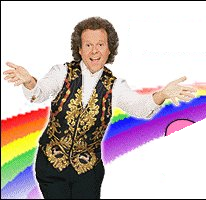
iTrader: (2)

Church right there. I used to question these "airfoil 'proves' 5hp gain/here's dyno..." threads when I have seen a good 7 to 10rwhp/1 to 2mph trap speed difference from air temperature alone from my own car. Glad there's someone else out there that agrees.
#31
TECH Addict

I do believe the electric pump does increase power to the rear wheels. It has to at only .15 hp, but it does it at a sacrifice.
I'd love to see someone with an electric water pump drive down I-10 at 75-80mph in 2nd (A4) or 3rd (M6) and tell me they won't overheat. Or in 4th on a 4L60e and 4.10's. Or in 3rd TH350 and 4.10's.
It's a give take.
#32
TECH Fanatic
iTrader: (2)
Join Date: Dec 2010
Location: Oklahoma
Posts: 1,084
Likes: 0
Received 0 Likes
on
0 Posts

I love how an intercooler pump graph is being used to prove pressure differential flow characteristics. They're not even the same thing; besides the two systems work differently. One is trying to drop the coolant temps back to ambient and the other trying to keep a steady temp. These pumps also have a different design as well. I do agree that they do flow less than a stocker at high rpms. But why is this still even debated. Most people never even flush the coolant system anyway. The radiator gets plugged and loses effective area. Each has there own best application. The electric does have a distinct disadvantage of not being able to pick one up at a parts store though.
On the fan front though I would say that one fan properly shrouded is better than two non-shrouded. It starts to be cfm over the area shrouded not just simply cfm overall. but hey im just an internet idiot talking though. so take it as you will.
On the fan front though I would say that one fan properly shrouded is better than two non-shrouded. It starts to be cfm over the area shrouded not just simply cfm overall. but hey im just an internet idiot talking though. so take it as you will.
#34
Launching!
iTrader: (1)
Join Date: Aug 2013
Location: Pittsburgh, PA
Posts: 241
Likes: 0
Received 0 Likes
on
0 Posts

Yeah, the test for Lingenfelter was shown as proof that the flow drops under pressure. It's basic physics really.
That dyno doesn't show increase in power over the entire rpm. It shows it over approx. 3250rpms. Anything less than .5% hardly qualifies as a quantifiable proof of increase or decrease (read: under 3250rpms on that graph). Hell, the 2% peak increase is within margin of error. Air Temp has a larger effect on power than that.
The actual difference in power between the two lines on that graph are immeasurable below 3250rpms. .15hp is immeasurable on the graph.....
That dyno doesn't show increase in power over the entire rpm. It shows it over approx. 3250rpms. Anything less than .5% hardly qualifies as a quantifiable proof of increase or decrease (read: under 3250rpms on that graph). Hell, the 2% peak increase is within margin of error. Air Temp has a larger effect on power than that.
The actual difference in power between the two lines on that graph are immeasurable below 3250rpms. .15hp is immeasurable on the graph.....
I agree here. But, to some extend when multiple unrelated sources dyno prove the same measurement it becomes acceptable. One chart showing gains of 2% is one thing, but many from different companies/people in different climates showing the same small gains is another.
I do believe the electric pump does increase power to the rear wheels. It has to at only .15 hp, but it does it at a sacrifice.
I'd love to see someone with an electric water pump drive down I-10 at 75-80mph in 2nd (A4) or 3rd (M6) and tell me they won't overheat. Or in 4th on a 4L60e and 4.10's. Or in 3rd TH350 and 4.10's.
It's a give take.
I do believe the electric pump does increase power to the rear wheels. It has to at only .15 hp, but it does it at a sacrifice.
I'd love to see someone with an electric water pump drive down I-10 at 75-80mph in 2nd (A4) or 3rd (M6) and tell me they won't overheat. Or in 4th on a 4L60e and 4.10's. Or in 3rd TH350 and 4.10's.
It's a give take.

#35
TECH Addict

It certainly is quantifiable. This is one graph, there are many people who have duplicated this same result. The threads are to old to go digging up, and I just don't feel the need to prove it.
Umm.. I run a 4l60e and 4.3 gears. I drive 45 miles each way to the track - in 95* air in the summer- with half a air dam - and a 43 GPM Meziere pump - with no issue
I usually don't drive below 70 MPH and regularly do 80 on some stretches.
Umm.. I run a 4l60e and 4.3 gears. I drive 45 miles each way to the track - in 95* air in the summer- with half a air dam - and a 43 GPM Meziere pump - with no issue

What I am disagreeing with is that the system is not more efficient than stock, therefore the power gains happen from reduced cooling capability NOT efficiency. It is an epistemic impossibility.
Last edited by hrcslam; 06-04-2014 at 05:14 PM.
#36
TECH Addict
#38
Launching!
iTrader: (1)
Join Date: Aug 2013
Location: Pittsburgh, PA
Posts: 241
Likes: 0
Received 0 Likes
on
0 Posts

Fluid dynamics doesn't agree with your statement. This is exactly like saying "pumping losses under pressure is not the same as pumping losses under pressure". They are both used as heat exchangers, they use liquid to cool air, they literally work the same way. They use the same physics of thermal dynamics and fluid dynamics. The variables are a little different, but the drop in GPM due to pressure is factually proven through fluid dynamics and shows right there on that graph.
So the pump can cavitate if pressure is to high.. so what. In the test they used restrictor plates to create restriction. How much restriction will the cooling system create for the pump to flow water? You don't know. Neither does Lingenfelter.. but they weren't even testing Meziere pumps, or even water pumps.
I'm sorry you can't comprehend what I am saying. I'm not disagreeing with the results, yours seem exaggerated but still plausible given the conditions. 3000+ rpms in 95°F heat for 45 minutes? What do your temps read if you don't mind me asking?
I comprehend perfectly. You are the one who doesn't get it. WE ALL KNOW IT MOVES LESS WATER THAN THE STOCKER. It says so right on the pumps ratings. Here it is.. spelled out with more clarity. The EWP uses just .1396 horsepower to adequately cool the engine. Conservatively the mechanical water pump uses 6 HP at the upper RPMs. This makes the EWP more efficient at its job.
Efficient:
utilizing a particular commodity or product with the least waste of resources or effort.
preventing the wasteful use of a particular resource.
I said 45 miles, not minutes. Temps read 185.
What I am disagreeing with is that the system is not more efficient than stock, therefore the power gains happen from reduced cooling capability NOT efficiency. It is an epistemic impossibility.
So the pump can cavitate if pressure is to high.. so what. In the test they used restrictor plates to create restriction. How much restriction will the cooling system create for the pump to flow water? You don't know. Neither does Lingenfelter.. but they weren't even testing Meziere pumps, or even water pumps.
I'm sorry you can't comprehend what I am saying. I'm not disagreeing with the results, yours seem exaggerated but still plausible given the conditions. 3000+ rpms in 95°F heat for 45 minutes? What do your temps read if you don't mind me asking?
I comprehend perfectly. You are the one who doesn't get it. WE ALL KNOW IT MOVES LESS WATER THAN THE STOCKER. It says so right on the pumps ratings. Here it is.. spelled out with more clarity. The EWP uses just .1396 horsepower to adequately cool the engine. Conservatively the mechanical water pump uses 6 HP at the upper RPMs. This makes the EWP more efficient at its job.
Efficient:
utilizing a particular commodity or product with the least waste of resources or effort.
preventing the wasteful use of a particular resource.
I said 45 miles, not minutes. Temps read 185.
What I am disagreeing with is that the system is not more efficient than stock, therefore the power gains happen from reduced cooling capability NOT efficiency. It is an epistemic impossibility.
It's funny you say that, because I don't know how many times you have given your car as an example of being a top performer with the AI topend. How many times have you ran 11.5's - or even .6 .7 .8? What was the DA when you ran it? It looks pretty cold out in the vid. A car that can run 11.5 once in the winter doesn't make it a 11.5 second car.
#39
TECH Addict

Seriously? You post the definition of efficient and its the system you defend that is less efficient by the definition you posted. Lol.
Also I never said it didn't flow what they claimed. I said it flowed less than advertised under pressure. That is a factual statement verified by Mezeire.
Now for a quick lesson in physics.
HP = (GPM*PSI)/1714
So at 1 psi (which is higher than free flow pressure) it takes .02hp to move 43GPM. But the pump is free flow rated at 43GPM and using .13hp? So it's less than 15% efficient at moving coolant. Hmmmm.
Later will come the thermal dynamics lesson of BTUs of cooling capability based on GPMs.
Again the system uses less power but at a sacrifice to cooling capability. Which is fine for drag racing and many other scenarios.
UPDATE:
As promised, here's the math on GPM and cooling.
This equation goes like this BTU/Hr= GPM*500*Temperature Difference °F
So if the coolant enters the radiator at 220°F and leaves at 195°F it would have a Temperature difference of 25°F.
So at 43GPM (again not the case under operating pressure but we'll roll with it) the equation above provides a total of 537,500 BTU's/hr of cooling.
With the factory rated max of 66GPM operating the equation above provides 825,000 BTU's/hr of cooling. A 50+% INCREASE in cooling capability. That is HUGE. And that is giving the electric pump an inaccurate rating of 43GPM under operating pressure. The real difference is much bigger.
But hey what do engineers and scientists know.
Originally Posted by PA94Z
A car that can run 11.5 once in the winter doesn't make it a 11.5 second car.
Last edited by hrcslam; 06-05-2014 at 10:15 AM.
#40
TECH Fanatic
iTrader: (7)

Far as the dimwit claiming the alternator only places bearing and brush load, maybe you can find an elementary school student to teach you some basic science.
Then go jumpstart a vehicle with a dead battery and notice the idle twitch on the running car when you hook the cable to the dead battery because of the extra load placed on the alternator. If the alternator was able to output power without placing additional load on the engine then you are describing a perpetual motion machine and have solved all the world's energy problems.
Then go jumpstart a vehicle with a dead battery and notice the idle twitch on the running car when you hook the cable to the dead battery because of the extra load placed on the alternator. If the alternator was able to output power without placing additional load on the engine then you are describing a perpetual motion machine and have solved all the world's energy problems.
Either the alt. can supply enough voltage, or it can't. When it needs to supply more voltage, you think the alternator has to "try" harder? It has to overcome some internal resistance? The only things I mentioned above create friction, voltage is generated by an alternating magnetic field.
The voltage regulator compensates for this. Does the alternator generate more charge at higher RPM's? Sure it does, the lines of flux are being cut faster. But do your headlights get super bright, do wires start to melt from overheating when you go WOT? No, because the voltage regulator REGULATES the voltage to keep it around 14v. Crazy, huh?
When you jump a vehicle, you're taking potential energy away from the other one. You're draining the battery a bit, and the alternator on the running car must supply that now to compensate. This can affect the ignition system and PCM voltage, which can cause stumbling. Your example proves no part of your previous point and just illustrates you don't know how an alternator works.