Dowels close enough?
#21

never would i try to tighten the bolts to pull it home. i literally just got done replacing pilot, and installing a new gm bell to replace my quicktime. the new bellhousing wouldn't go on the dowel pins on the motor. i ended up buying a used bell and that one went on so an issue with new tremec piece. but i also thought about snugging the bolts to pull it on, but then i remember that this is soft aluminum here, and the trans bolts only get 37 pounds so don't do it. imagine that bolt pulling ur 100 pound trans only gripping on those small threads?
#22
Thread Starter
Joined: Mar 2004
Posts: 1,825
Likes: 217
From: Lansdale, PA

It's tick's LS7 clutch package with the standard steel flywheel. I followed their directions and removed the spring from the slave, bottomed it out and did my measurements using a flat piece of 1" thick steel i had.
Subtracting the width of the straight edge I got 2.18" from the top of the PP fingers to the face of the bell housing, and 1.97" from the slave surface to the trans mount surface, giving me .21"
Tick's spec is 0.125 to 0.200. Should I add a shim to shave that .21" in to spec?
Last edited by lees02WS6; 04-08-2018 at 04:29 PM.
#25

Make sure there isn't a bunch of grease inside the crank behind the pilot, I had a guy "help" me once and did that,, it stops the input shaft like a rock.. If you crank it in by the bolts it can split the crank.. Hydro-lock on a tiny scale
#26
Thread Starter
Joined: Mar 2004
Posts: 1,825
Likes: 217
From: Lansdale, PA

That won't be an issue. I installed the engine, the pilot bearing and the clutch.
#27
Thread Starter
Joined: Mar 2004
Posts: 1,825
Likes: 217
From: Lansdale, PA

That crappy little plastic tool was dead on the nuts. The new tool slides all the way in to the pilot bearing, and there is no play in the quarter master tools. I checked the depth with a digital caliper. I even inked up the edges of the tool to see if it marked the pilot bearing, it did.
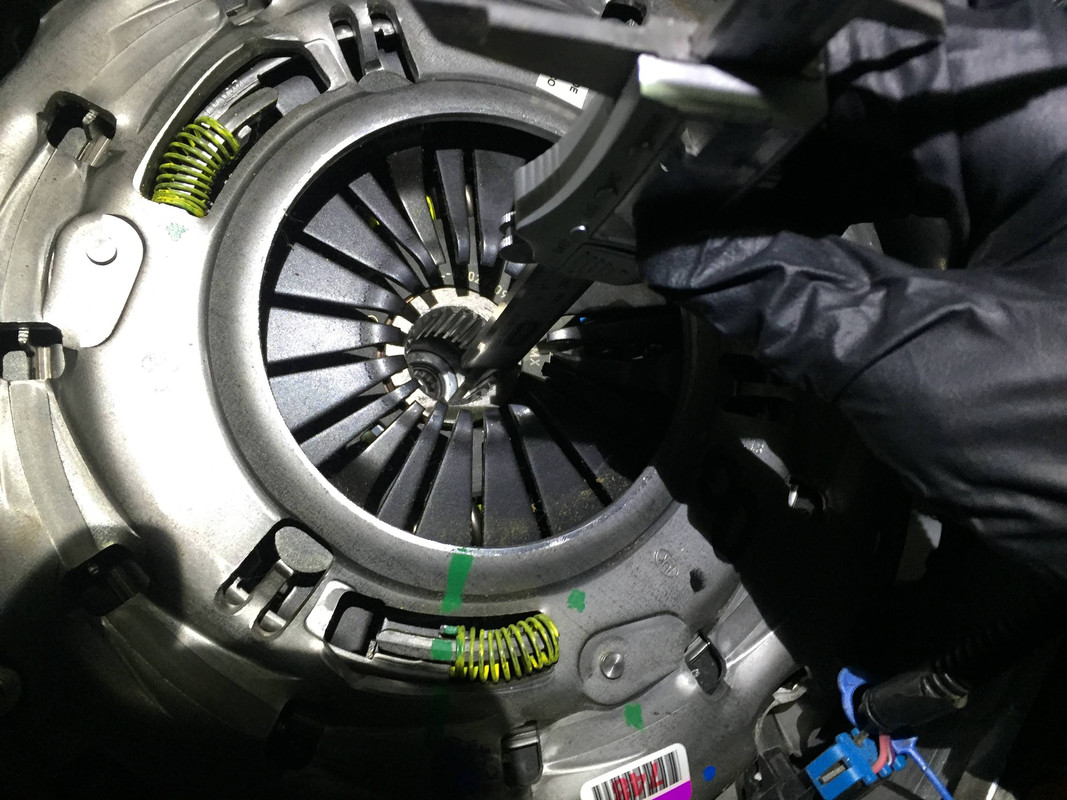
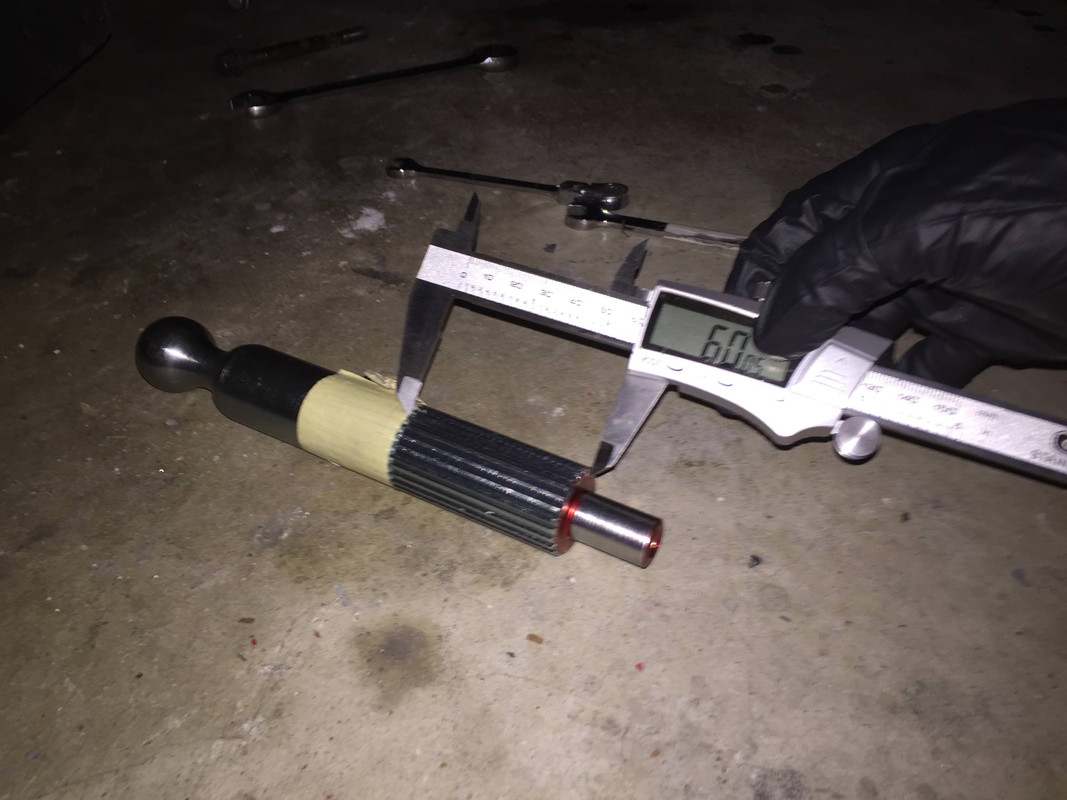
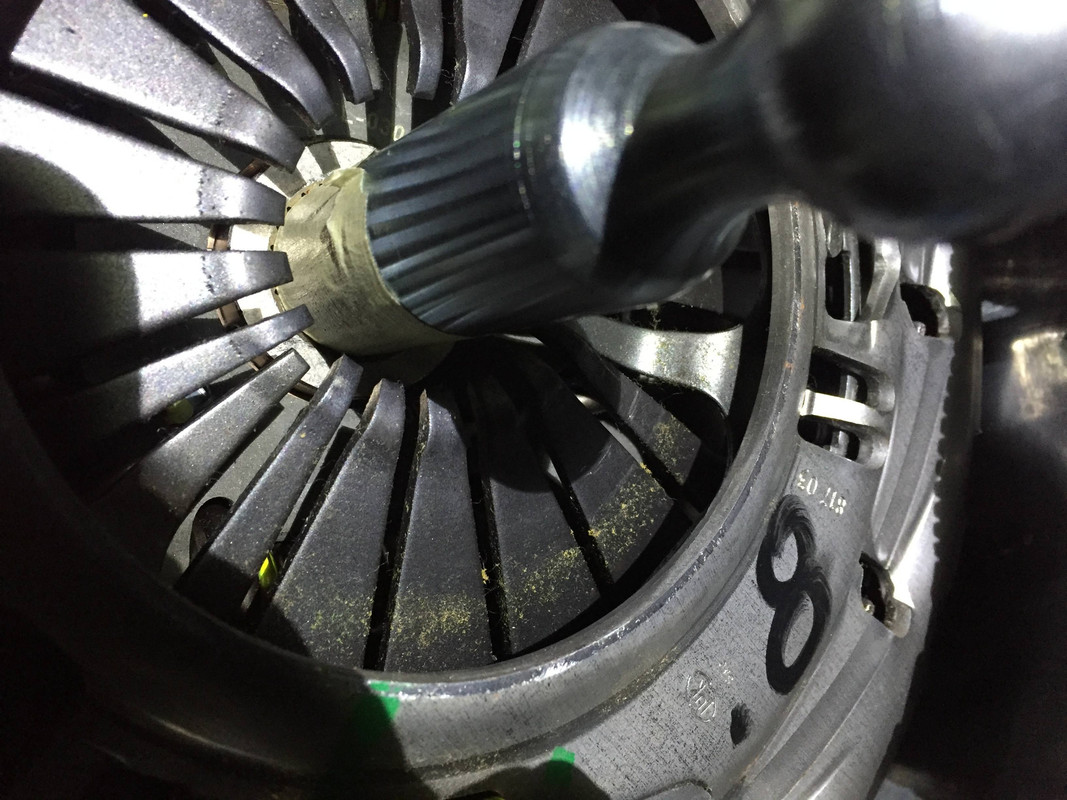
Bottom line, I'm getting frictional resistance and I'm not strong enough to push it home.
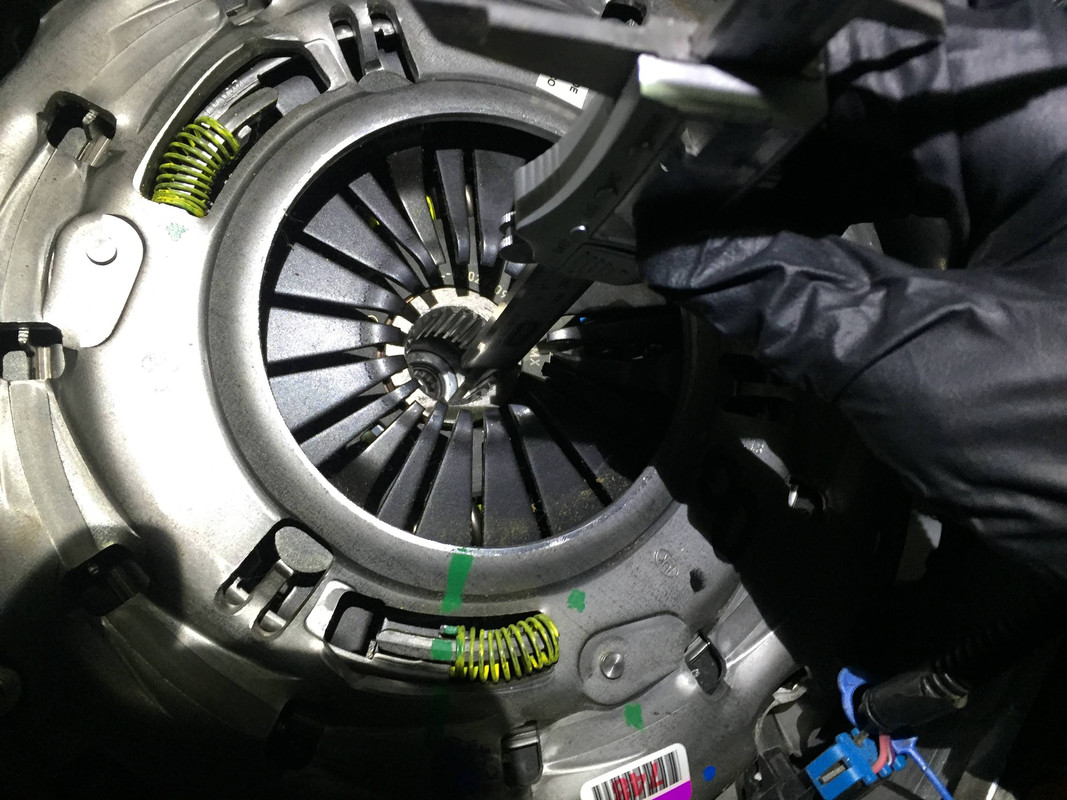
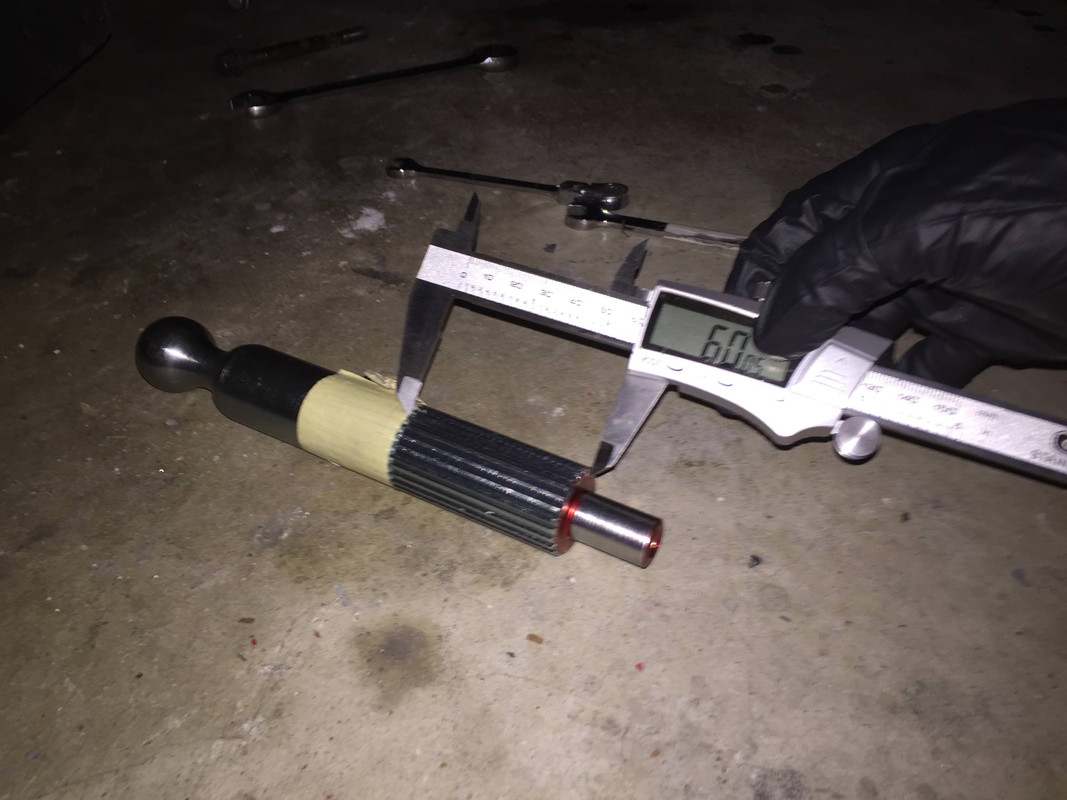
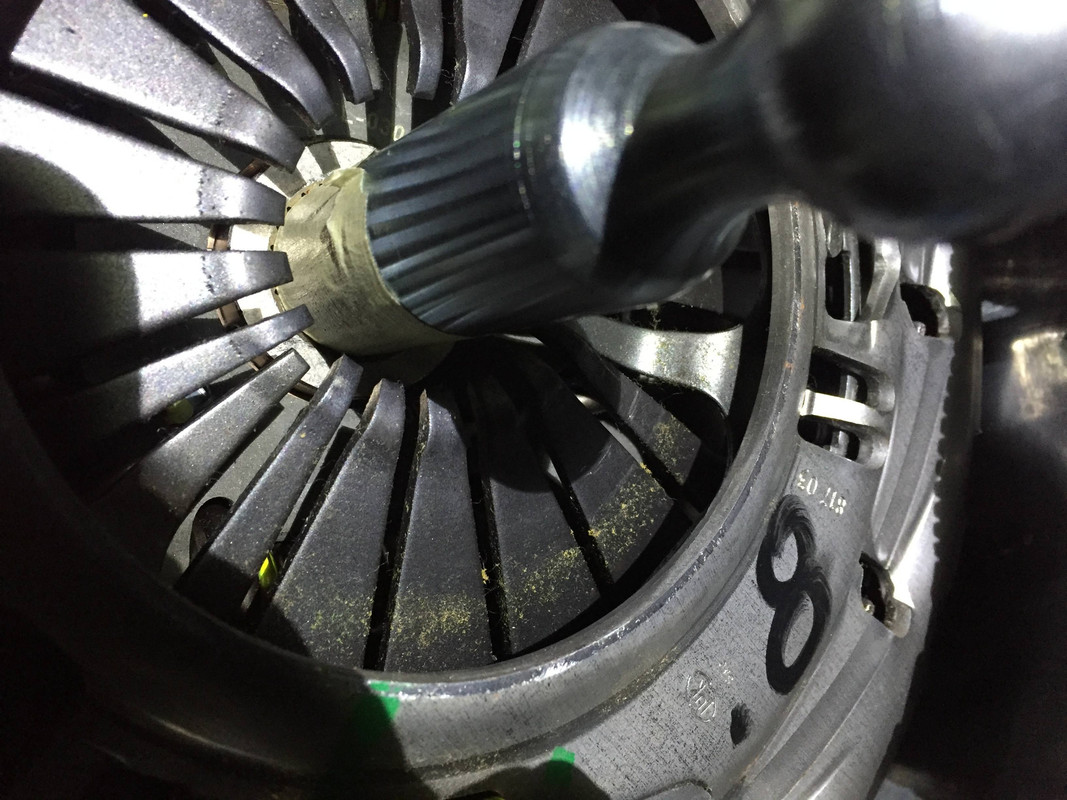
Bottom line, I'm getting frictional resistance and I'm not strong enough to push it home.
Last edited by lees02WS6; 01-04-2021 at 11:42 AM.
#28

How about this. Remove you throw out bearing and if it slides all the way up you will know it's the spring holding it out. Then you can pull it back out. Reinstall the throw out and install it again.