2004 - 2007 CTS-V E-Force Build Thread
#21

From my experience, properly setup its not an issue. My current tune in my 408 is hacked to get around the g/sec limit.
Im not a fan of large MAF tubes and run MAF only. (for a few reasons)
1. Idle is very difficult unless you maintain the SD/MAF blend..
2. you dont 'see' boost
3. These ECM have a limit 511g/sec, which if you plan to run 700+rwhp, will give you problems.
Large MAF tubes have too low of even airflow for measurement. Its a pita to tune idle and low rpm.
I had to install a honeycomb to straighten the airflow to reduce the "jumping around" the MAF sensor was giving during idle, which helped considerably... add in a big cam... good luck.
In the end, I prefer SD over MAF always.
And I used a LS7 slot Sensor. (has IAT built in)
1. Idle is very difficult unless you maintain the SD/MAF blend..
2. you dont 'see' boost
3. These ECM have a limit 511g/sec, which if you plan to run 700+rwhp, will give you problems.
Large MAF tubes have too low of even airflow for measurement. Its a pita to tune idle and low rpm.
I had to install a honeycomb to straighten the airflow to reduce the "jumping around" the MAF sensor was giving during idle, which helped considerably... add in a big cam... good luck.
In the end, I prefer SD over MAF always.
And I used a LS7 slot Sensor. (has IAT built in)
#22
TECH Fanatic
Thread Starter

Continuing with the build...one thing I forgot to take pics of is the EVAP line. Since the EVAP connection is on the bottom of the inlet snout, I needed a 90* fitting. Turns out a '99+ Silverado EVAP line was the perfect fit...had a quick connect fitting and the nylon hose was perfectly molded to follow the exact angles of the E-Force manifold. I'll try to get a better pic of this line, maybe take the one off of my truck for documentation. The EVAP line is in Red, the PCV breather line is the Green arrow:
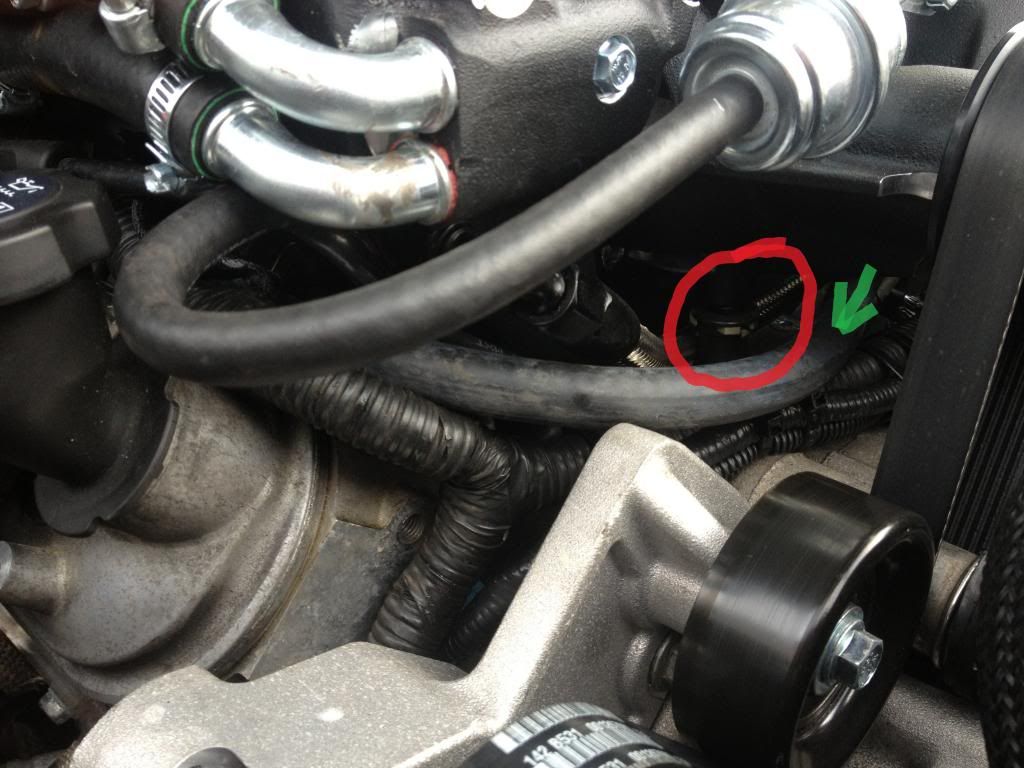
The tensioner bracket requires that you remove the passenger side harness retainer (as the bolt hole must be used for the bracket). I straightened the harness and ran it under the bracket. Once installed, there is a two wire connector that needs to be re-routed under the other harness' (Red circle) as it touched the tensioner.
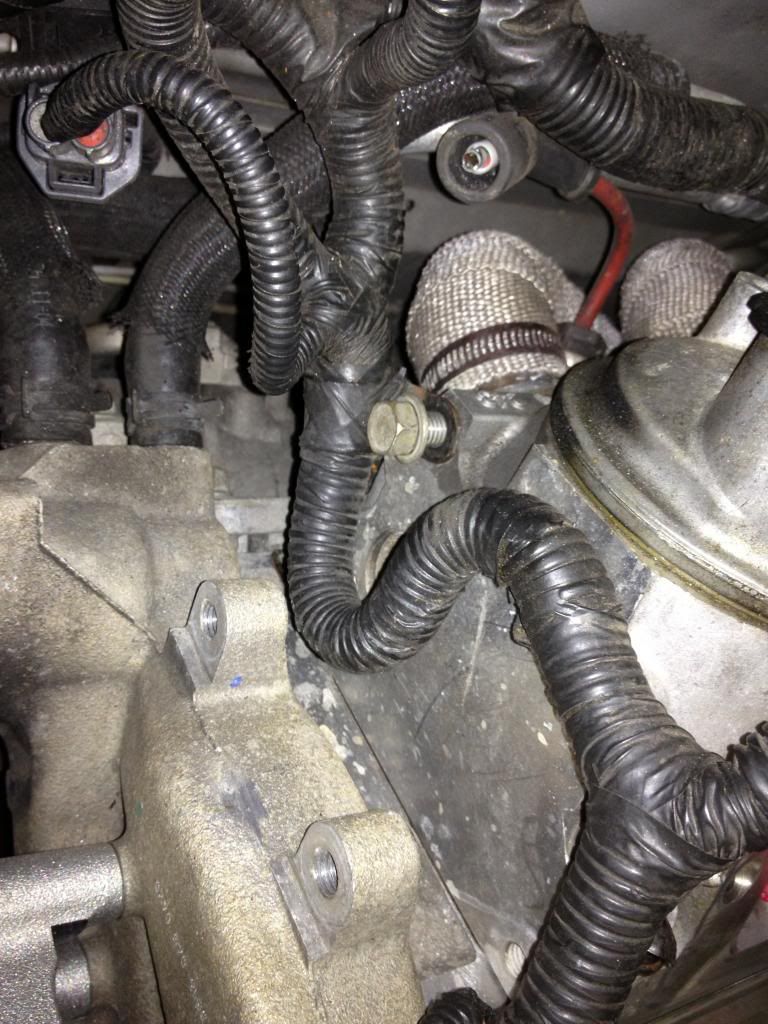
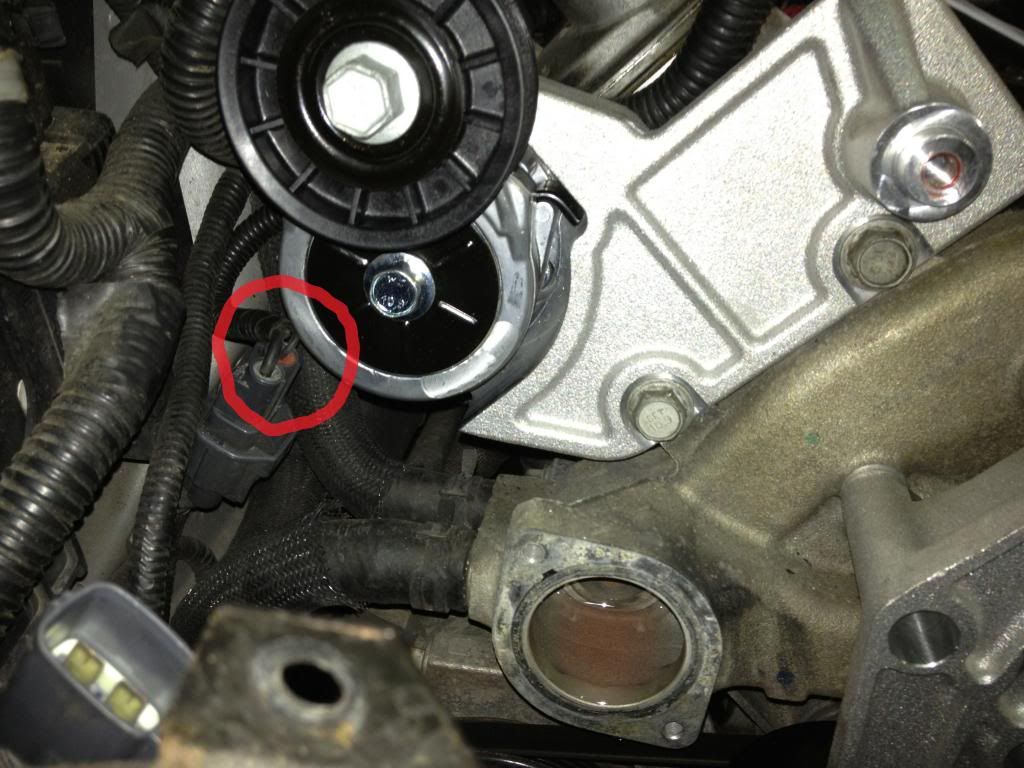
For the PCV system, I went cheap...shocker, huh? LOL! Anyhow, I used the best that Harbor Freight had to offer instead of the $120+ catch can. I epoxied the bottom vent closed so it wouldn't leak, and then temporarily mounted it to the drivers shock tower. I will make a bracket for it after I get the new expansion tank for the HEX system. Say what you will...the damn thing works! After about 200 miles I have a little oil puddled in the trap.
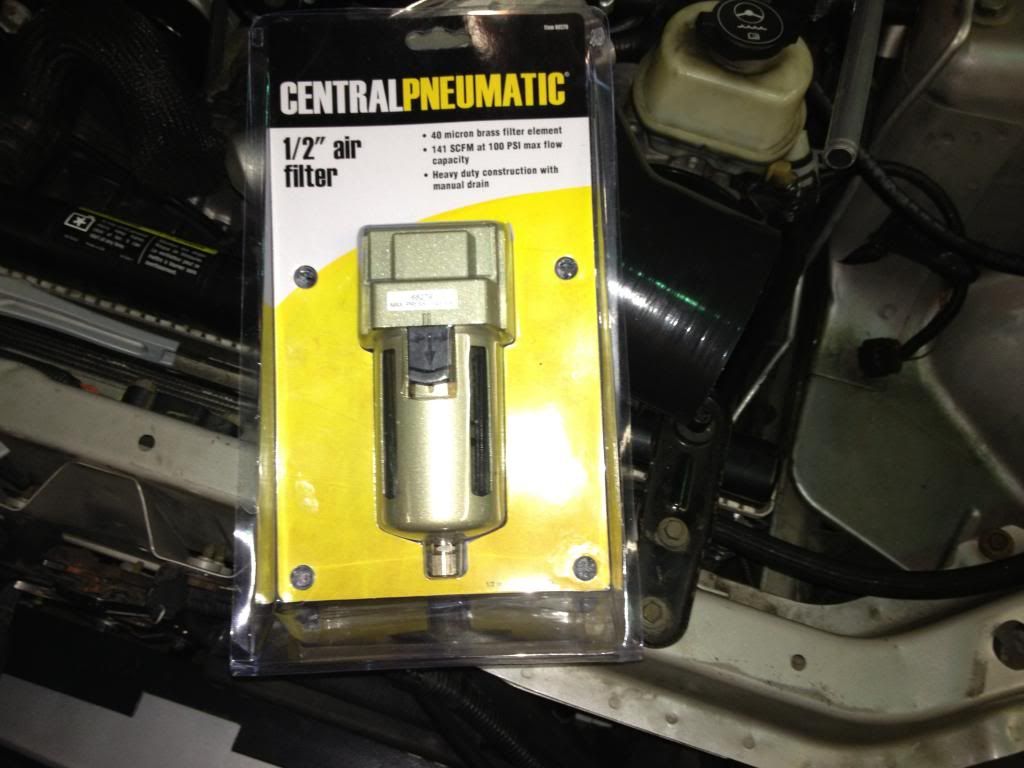
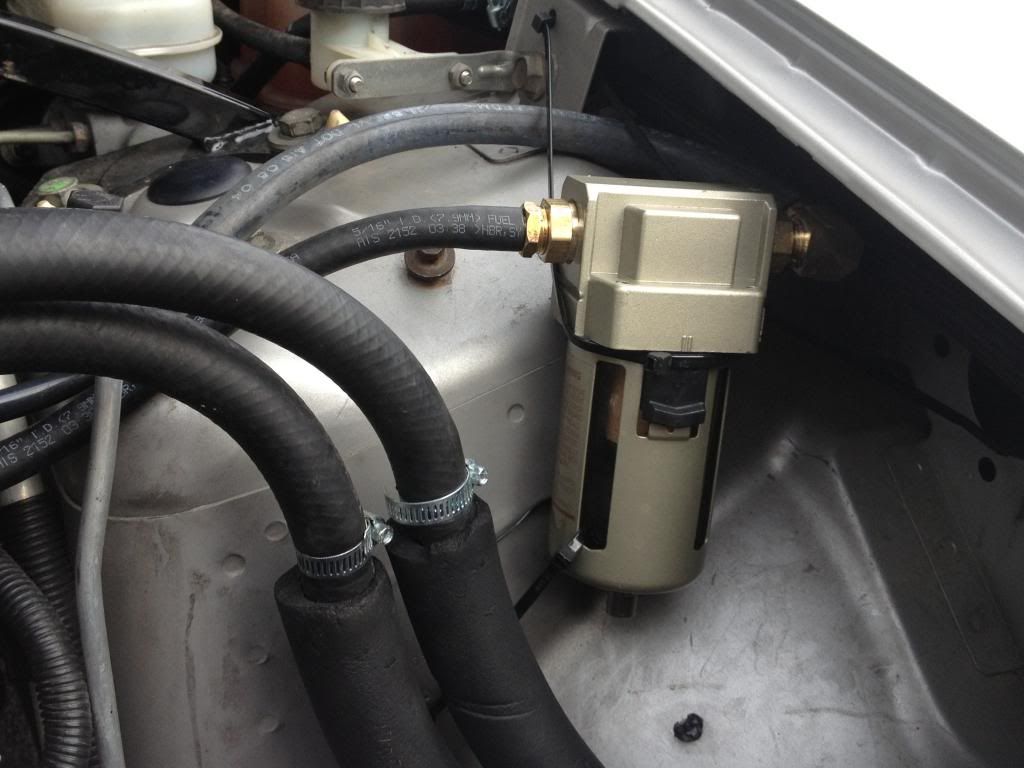
For the PCV breather, I drilled a hole in the 4" aluminum intake tubing and installed a power brake booster check valve and grommet. From the check valve, hose connects to the breather vent on the passenger head. I did not want crankcase vapors being sucked through the intake, so this was a low buck method for maintaining correct flow through the system.
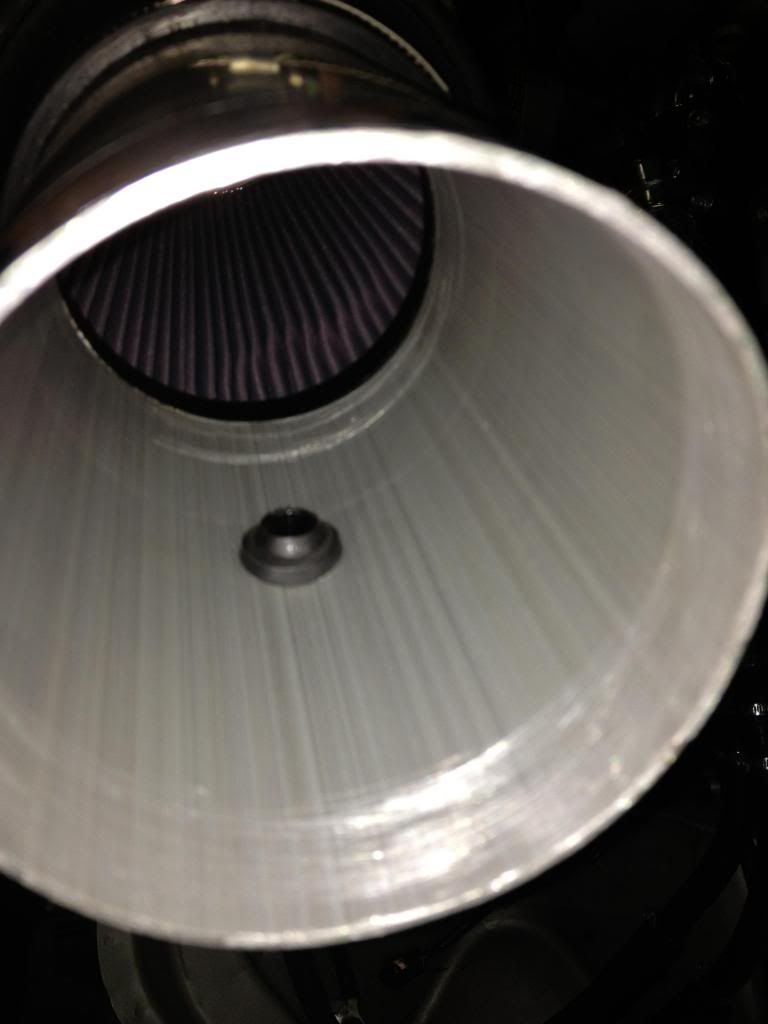
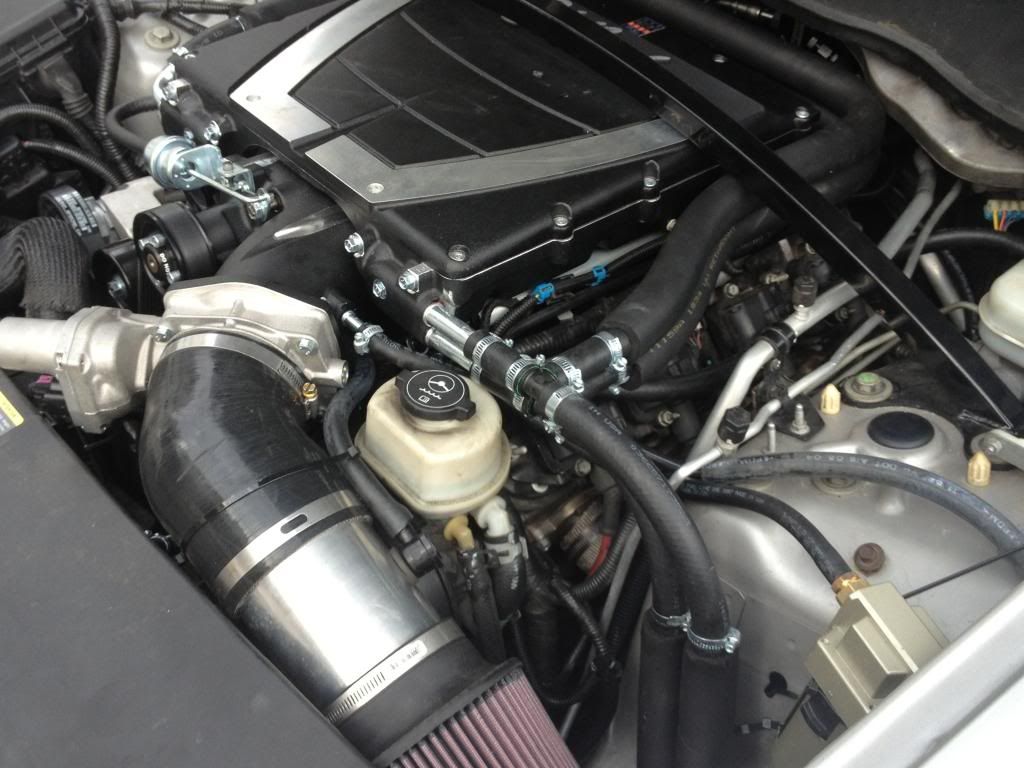
The underside of the hood had to be modified before it would close. I used putty to mark the area's that required clearance, and trimmed as necessary. Note the I have since installed the RevShift trans insert which raised the rear of the trans substantially (since the mount was collapsed)...so I may have trimmed more than required.
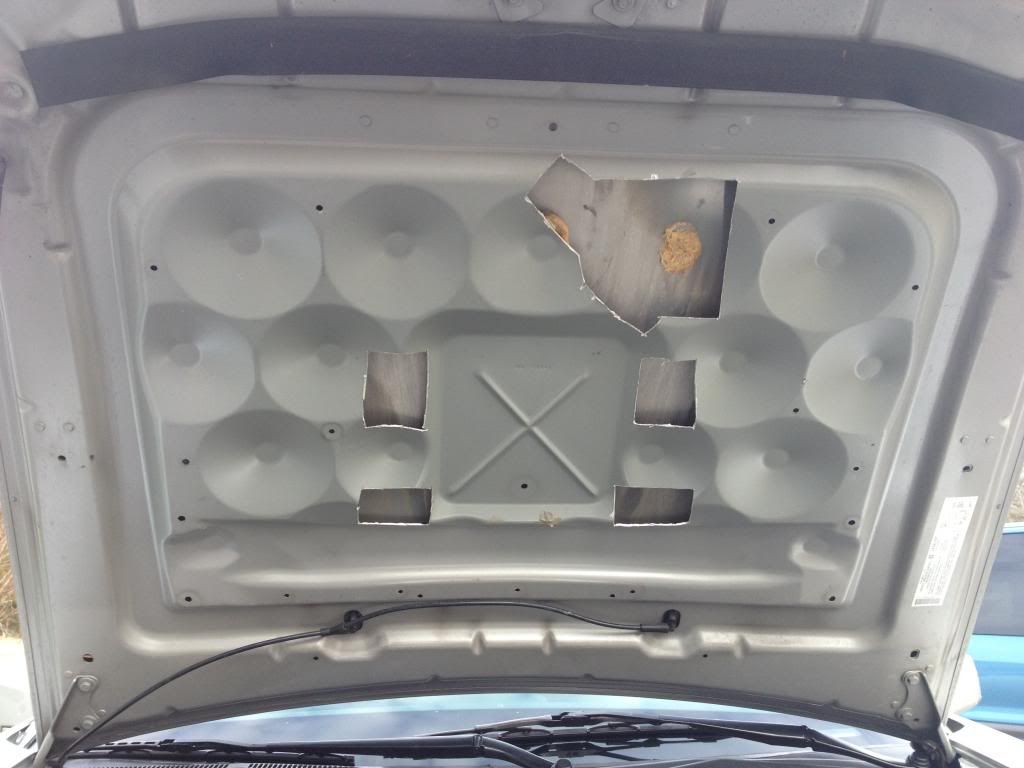
For power to the HEX pump, I wired the ground straight to the core support flange behind the driver headlamp since there was a threaded hole there. I ran the power line to the under hood fuse center and used the mini fuse tap (in a vacant switched fuse) with a 3 Amp fuse as control voltage to the relay. The 20 Amp fuse holder is secured to the stud for B+ to the pump side of the relay.
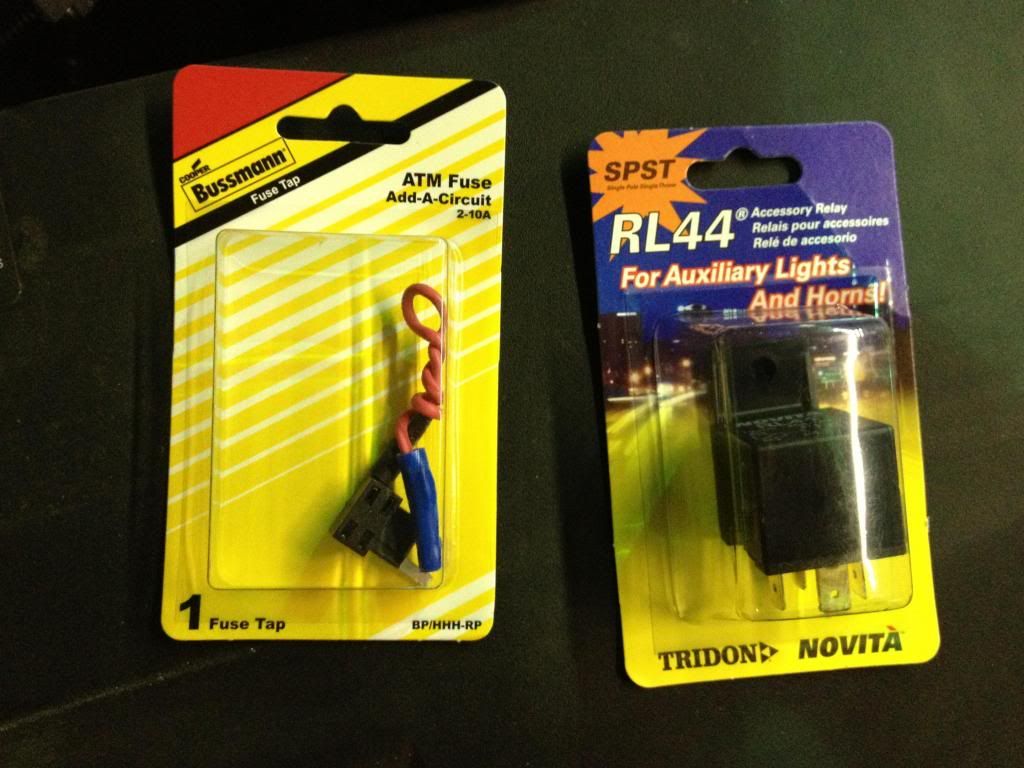
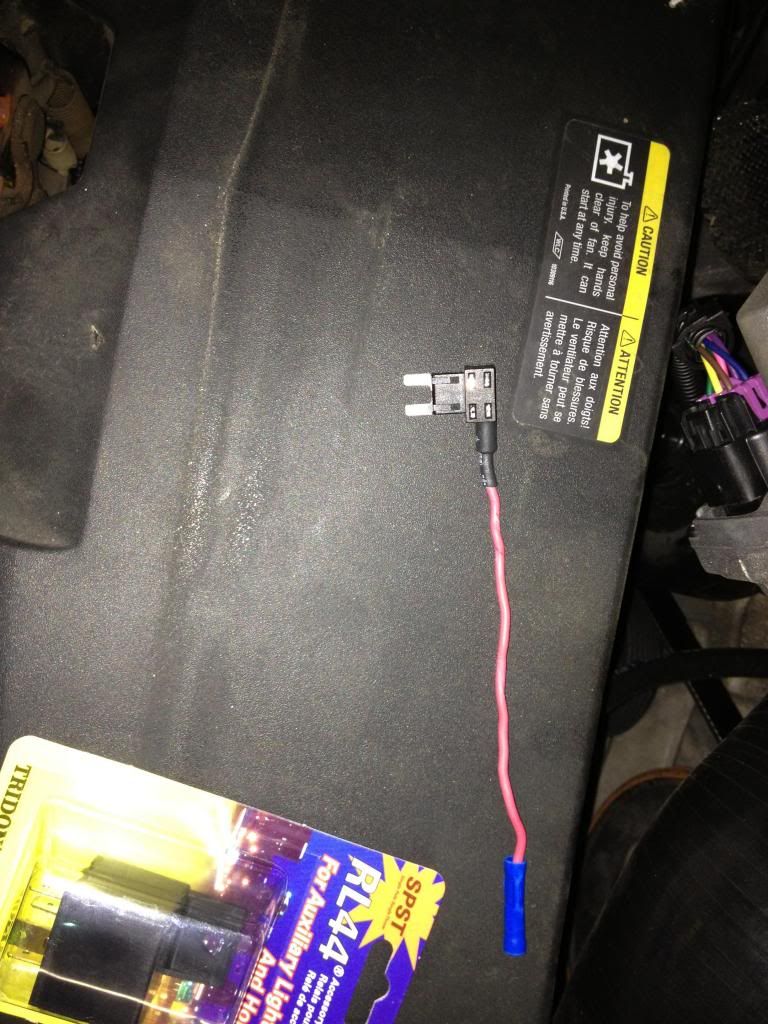
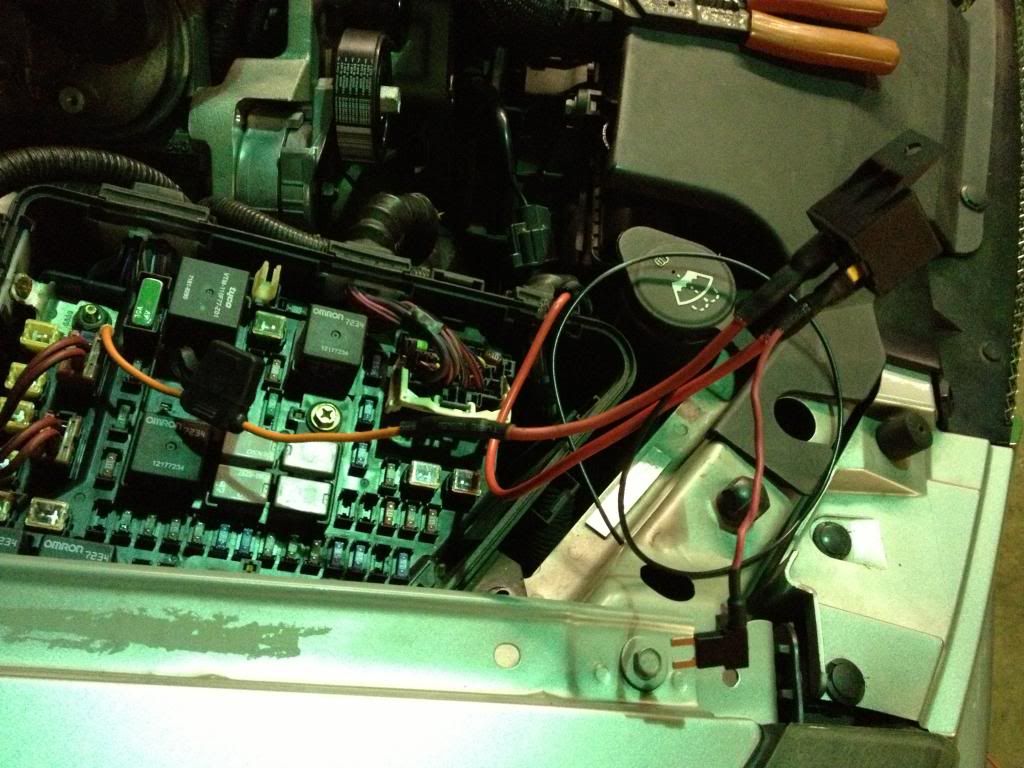
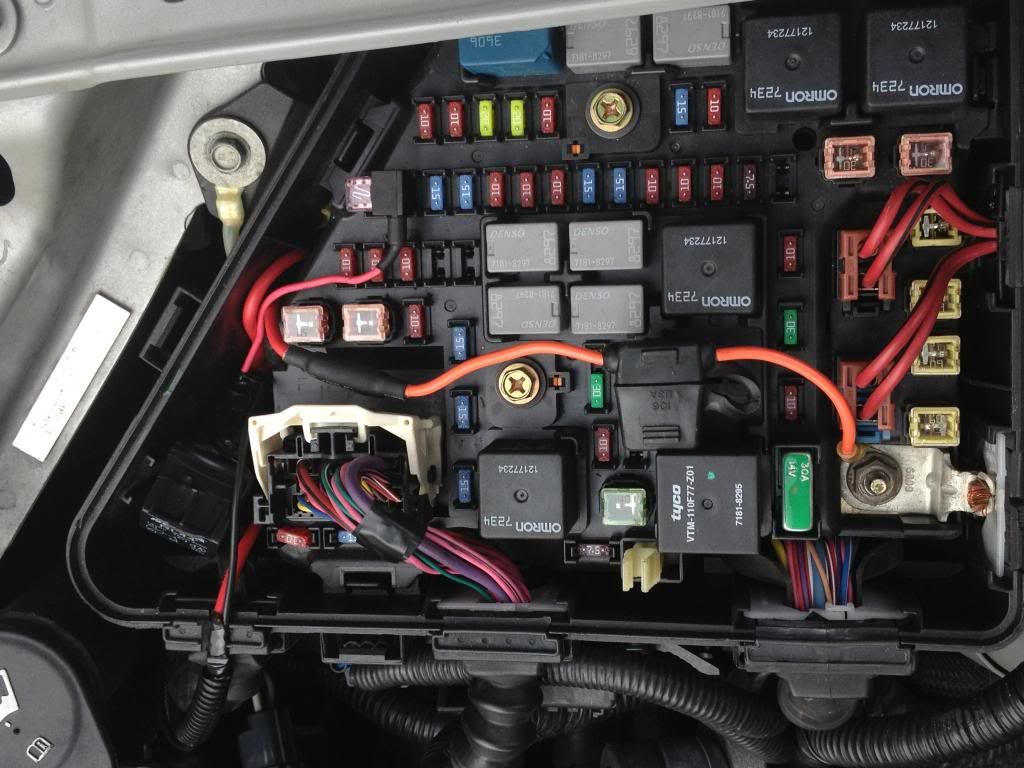
Forgot the belt...I have the 3.25" pulley but need to go bigger to get the boost down.
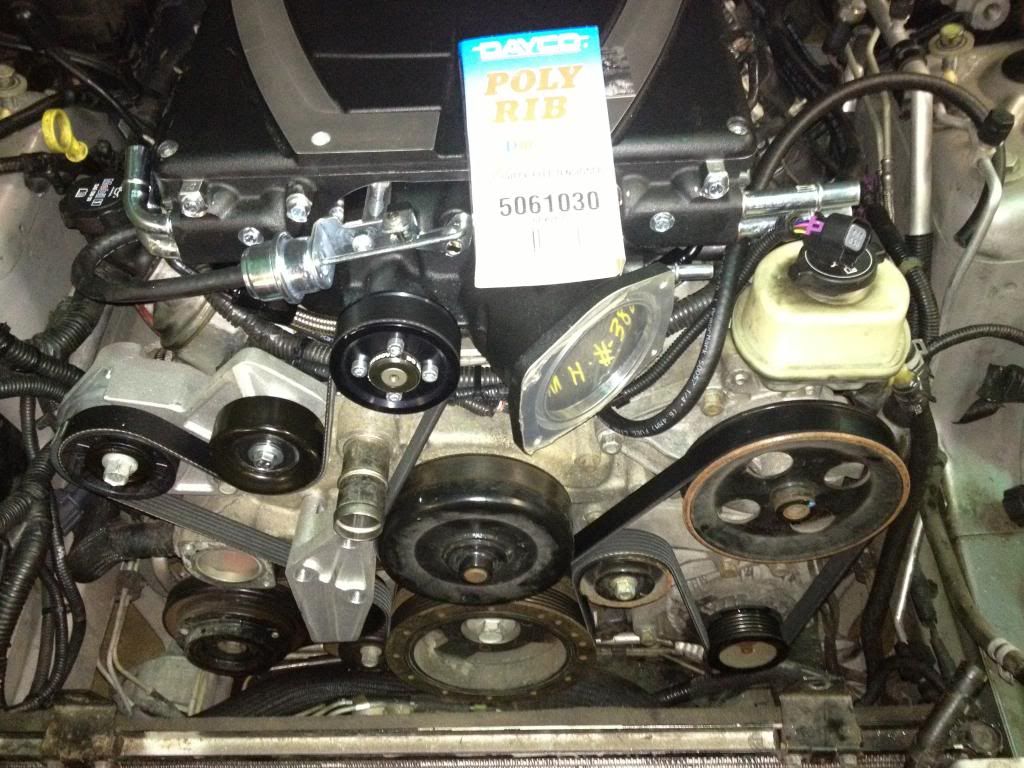
In addition to all of this, I installed a DW 300 fuel pump in the tank. I will be updating this thread as the new parts come in!
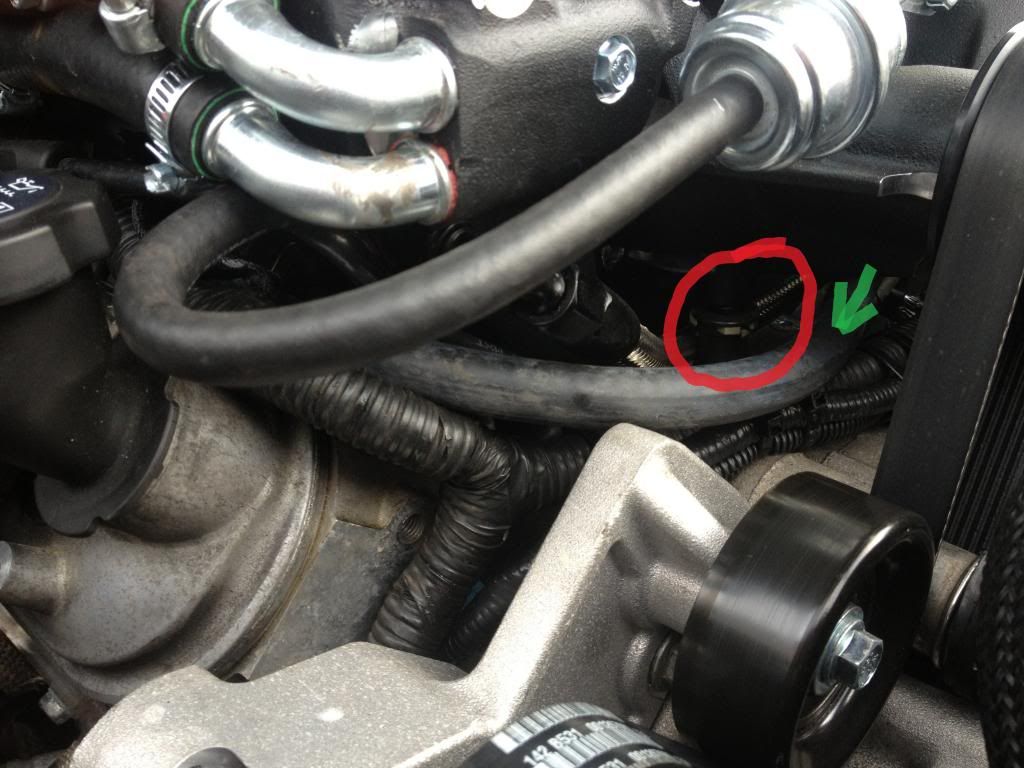
The tensioner bracket requires that you remove the passenger side harness retainer (as the bolt hole must be used for the bracket). I straightened the harness and ran it under the bracket. Once installed, there is a two wire connector that needs to be re-routed under the other harness' (Red circle) as it touched the tensioner.
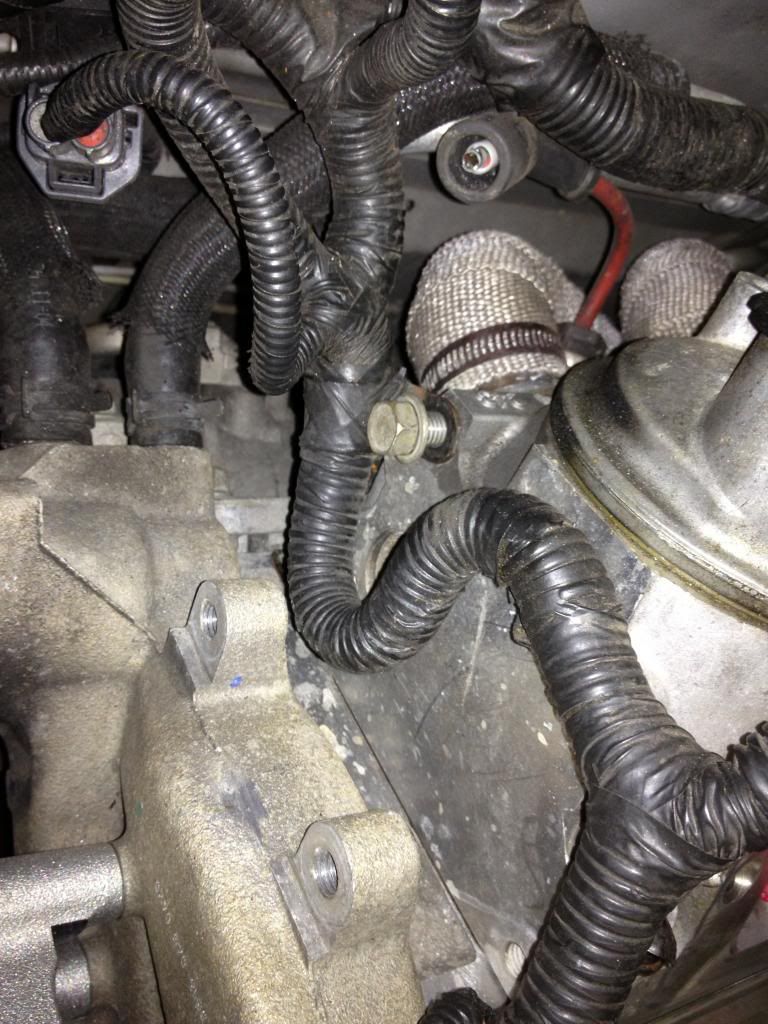
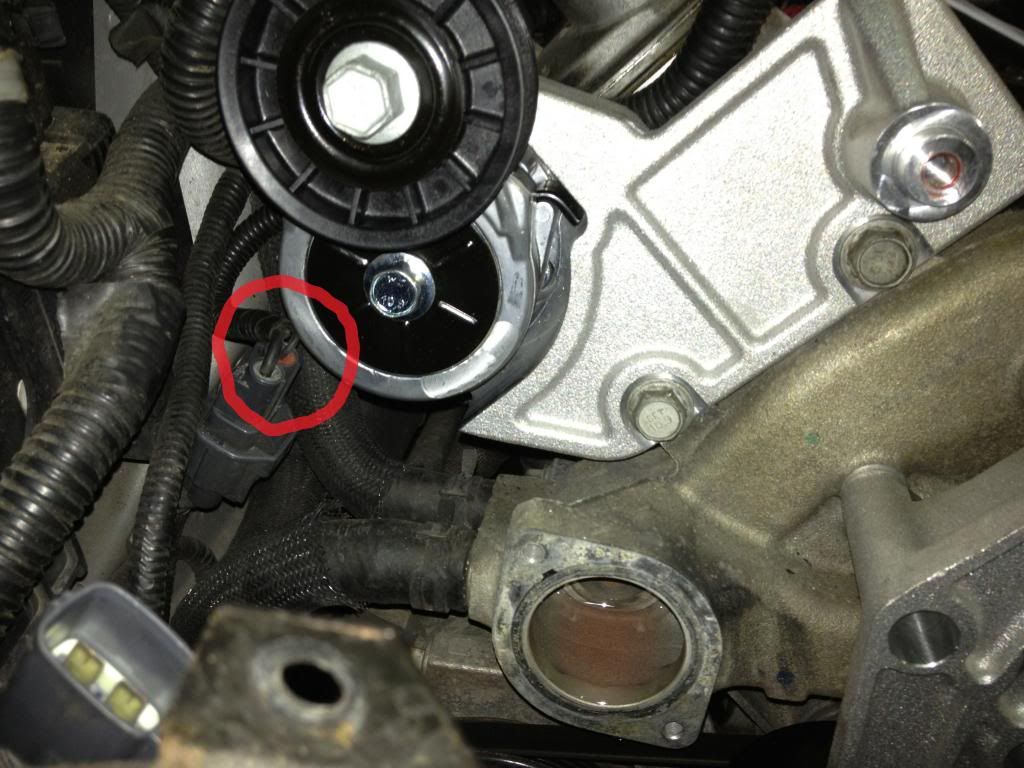
For the PCV system, I went cheap...shocker, huh? LOL! Anyhow, I used the best that Harbor Freight had to offer instead of the $120+ catch can. I epoxied the bottom vent closed so it wouldn't leak, and then temporarily mounted it to the drivers shock tower. I will make a bracket for it after I get the new expansion tank for the HEX system. Say what you will...the damn thing works! After about 200 miles I have a little oil puddled in the trap.
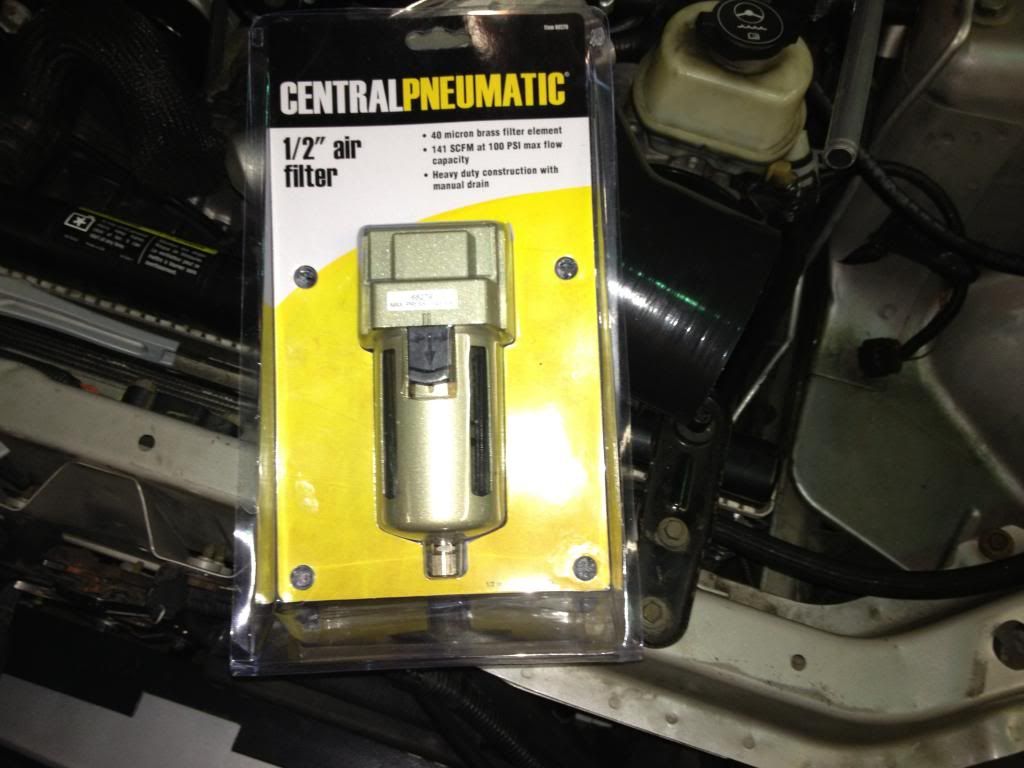
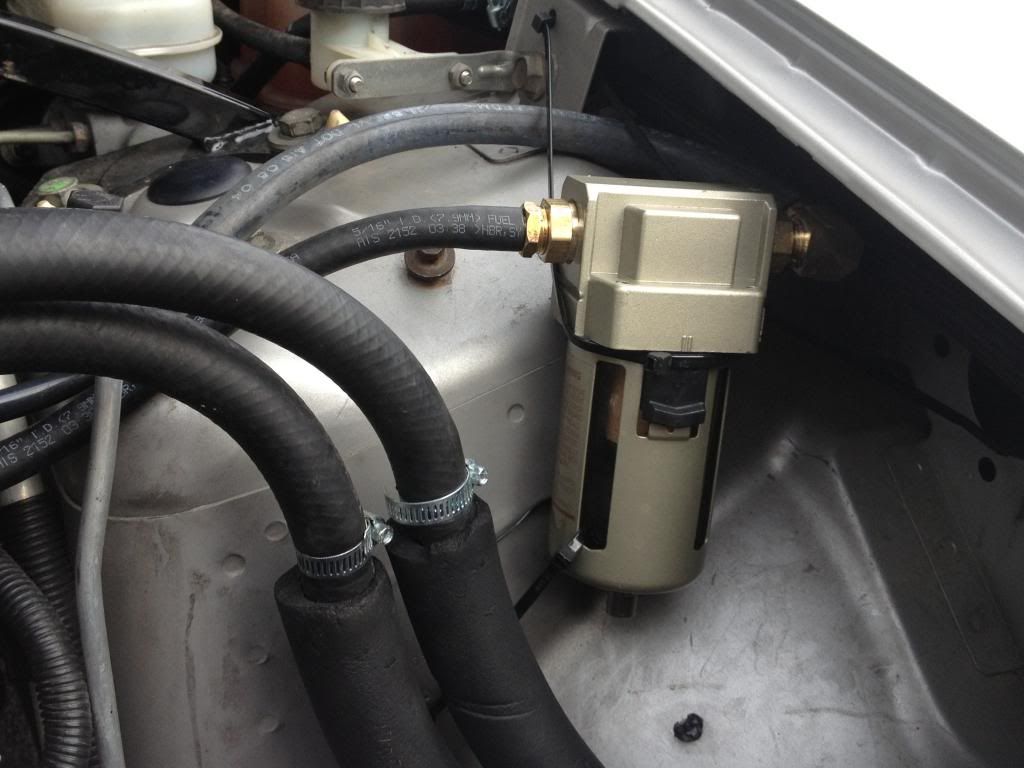
For the PCV breather, I drilled a hole in the 4" aluminum intake tubing and installed a power brake booster check valve and grommet. From the check valve, hose connects to the breather vent on the passenger head. I did not want crankcase vapors being sucked through the intake, so this was a low buck method for maintaining correct flow through the system.
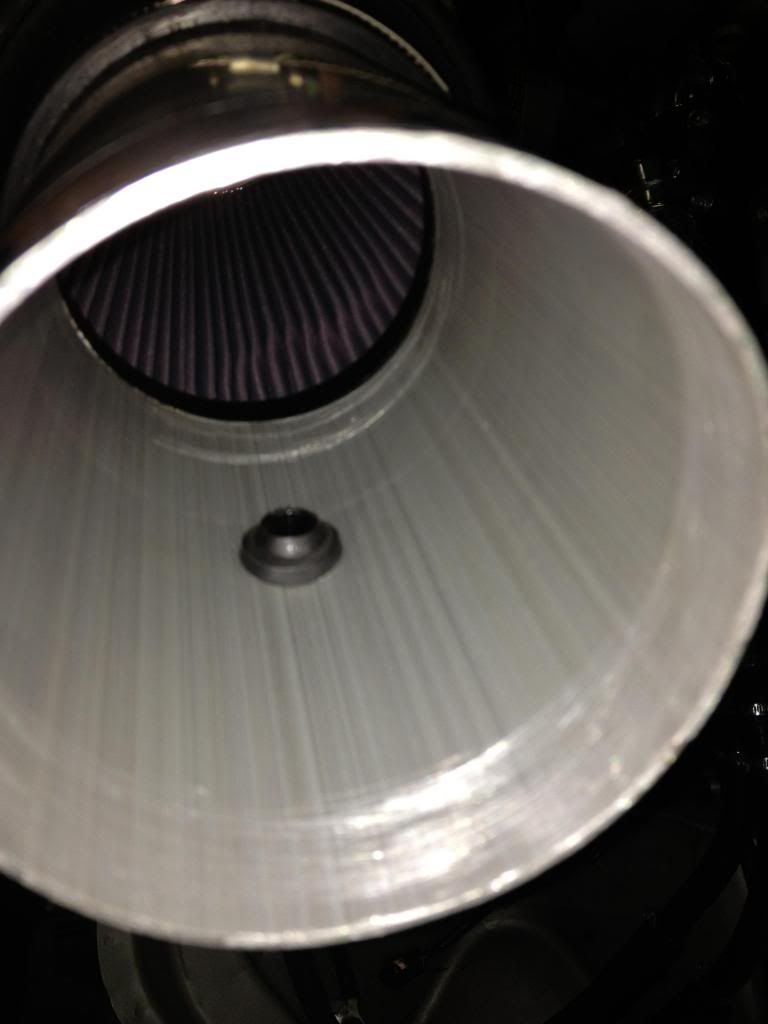
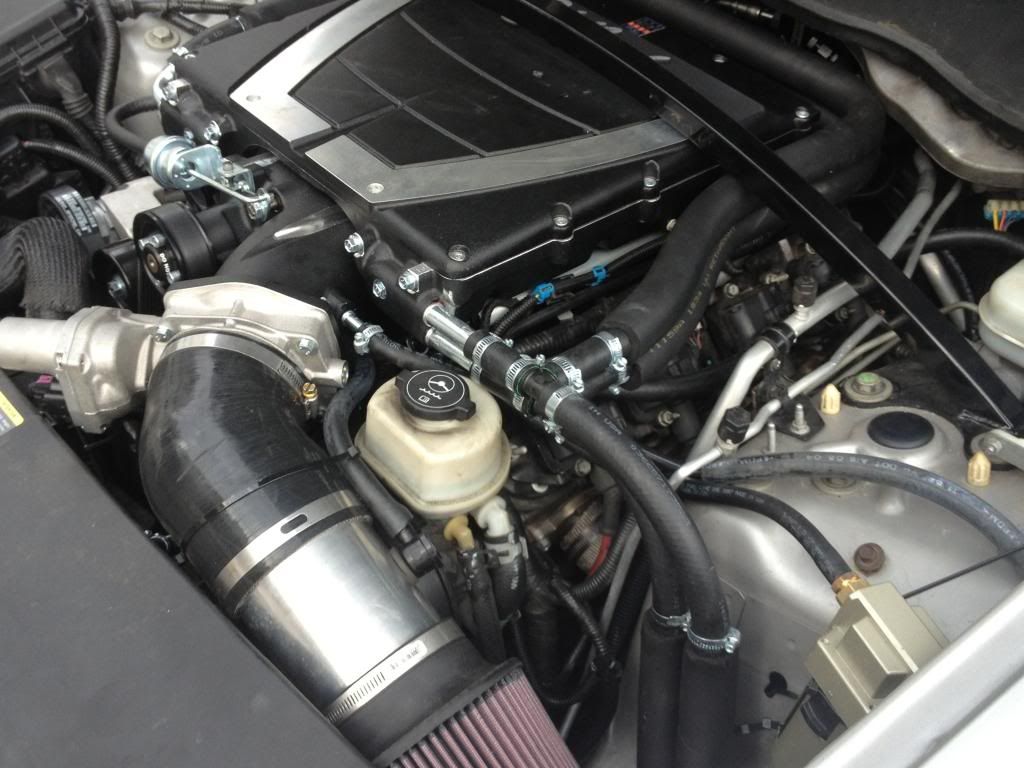
The underside of the hood had to be modified before it would close. I used putty to mark the area's that required clearance, and trimmed as necessary. Note the I have since installed the RevShift trans insert which raised the rear of the trans substantially (since the mount was collapsed)...so I may have trimmed more than required.
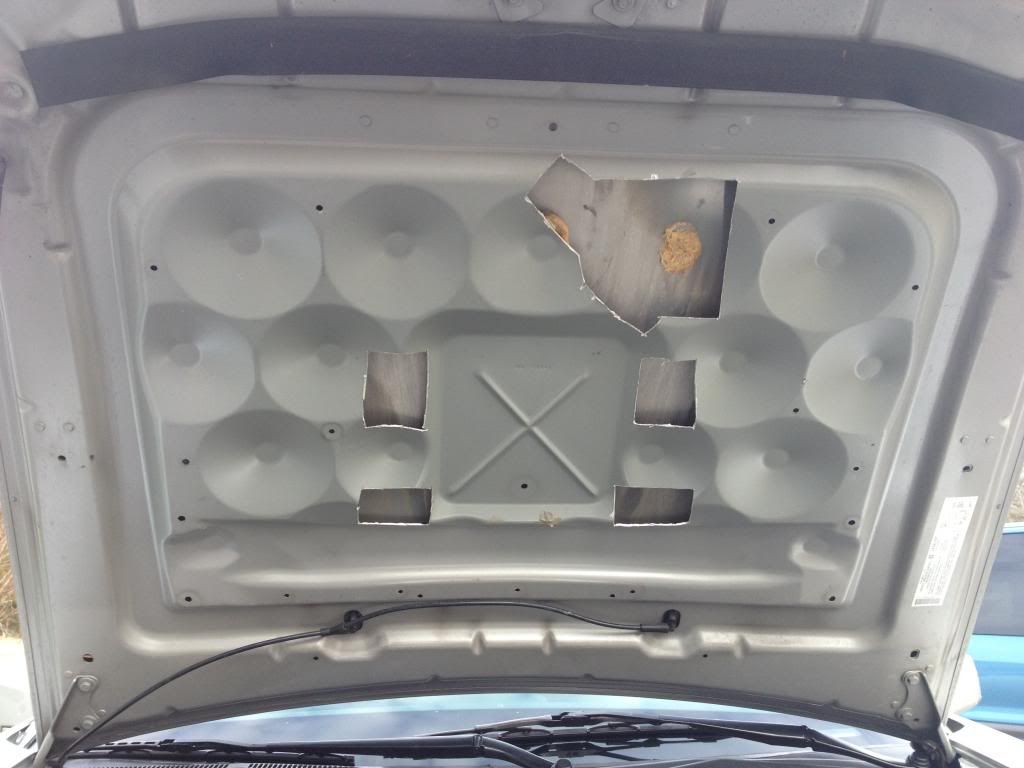
For power to the HEX pump, I wired the ground straight to the core support flange behind the driver headlamp since there was a threaded hole there. I ran the power line to the under hood fuse center and used the mini fuse tap (in a vacant switched fuse) with a 3 Amp fuse as control voltage to the relay. The 20 Amp fuse holder is secured to the stud for B+ to the pump side of the relay.
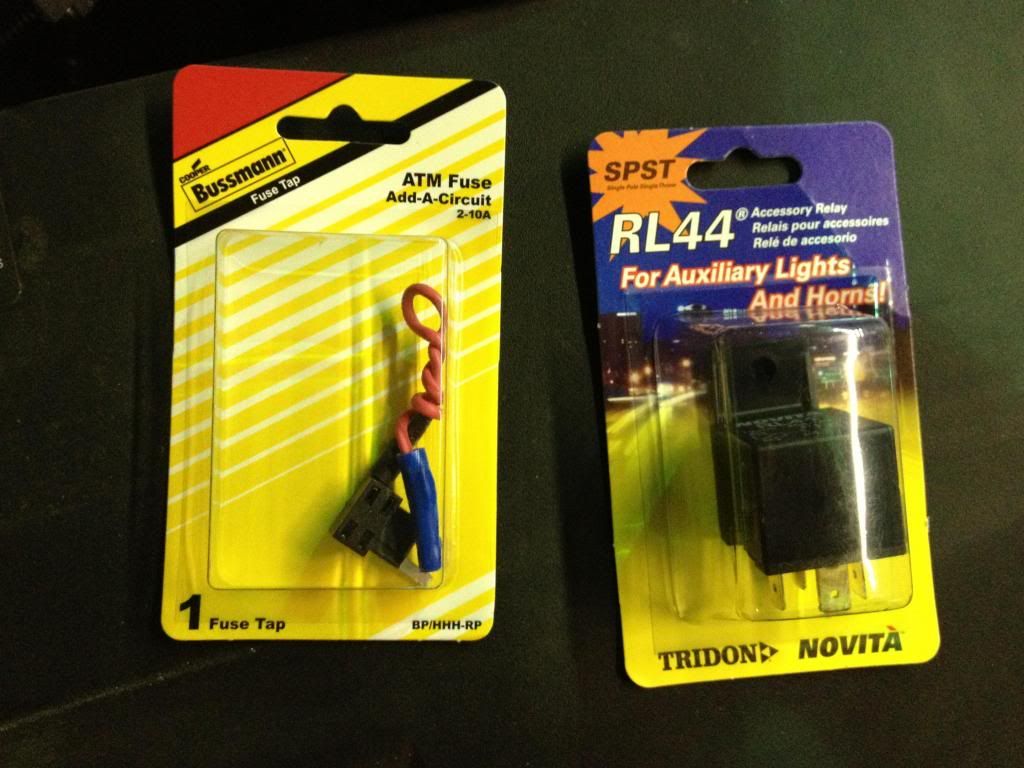
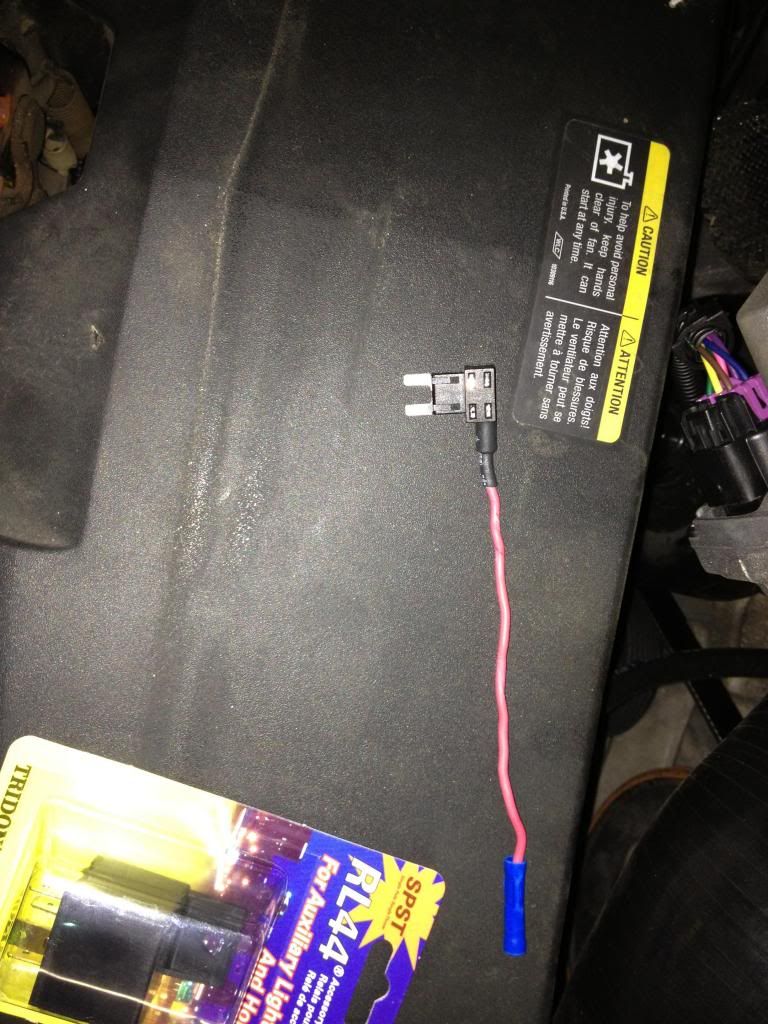
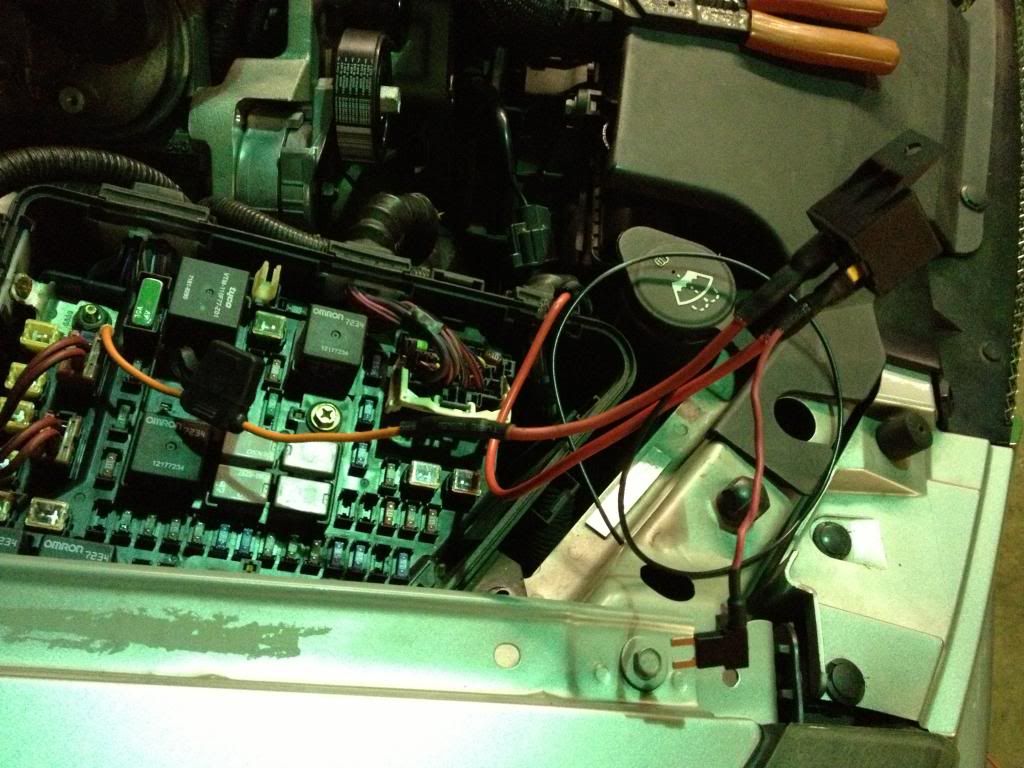
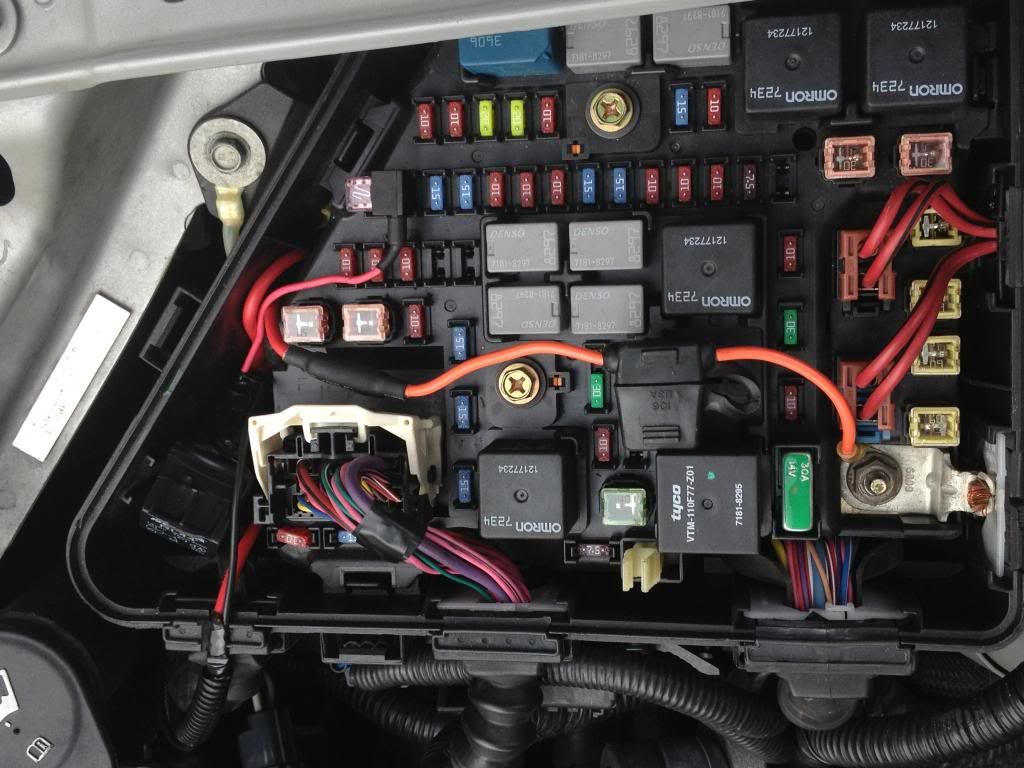
Forgot the belt...I have the 3.25" pulley but need to go bigger to get the boost down.
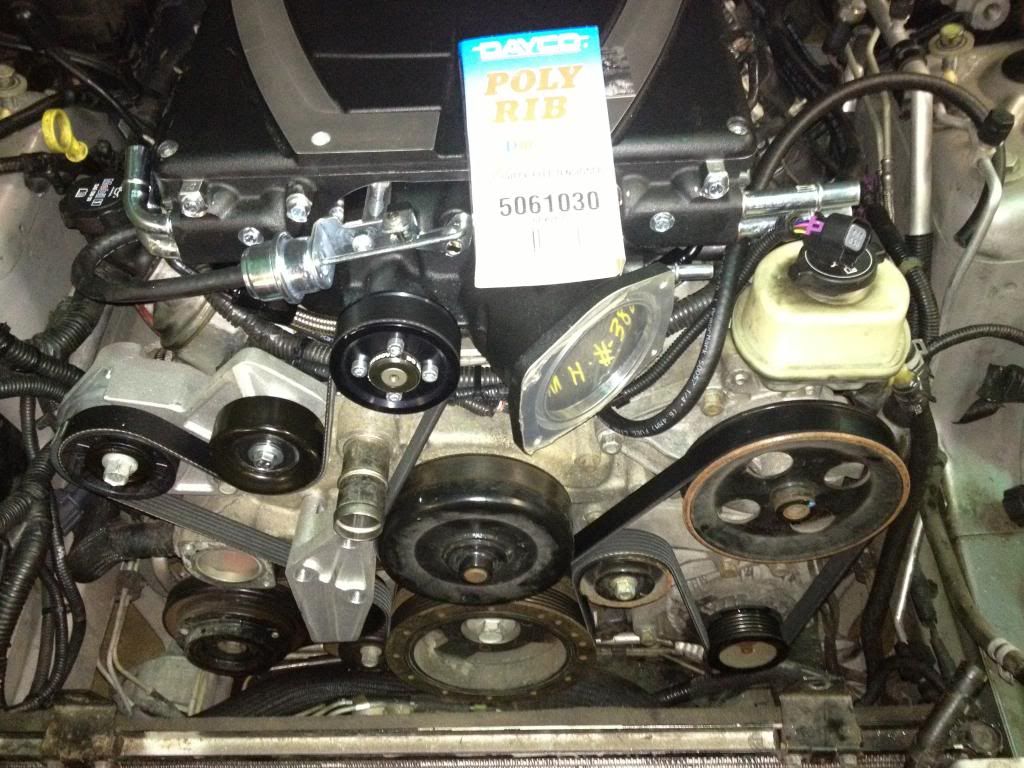
In addition to all of this, I installed a DW 300 fuel pump in the tank. I will be updating this thread as the new parts come in!
Last edited by DMM; 12-28-2012 at 10:08 PM.
#23
#24
TECH Fanatic
Thread Starter
#26
TECH Fanatic
Thread Starter

Well...I know how well the HEX/Intercooler system is working now. I have been running about 20* above ambient temps, however, while driving/logging at constant highway speeds I noticed the IAT's were over 140*! Turns out that one of the fittings on the HEX was leaking and drained the entire system! I had to remove everything to reseal it.
Nice to know the system is operating as designed and not just a product of lower ambient temps. Still waiting on the expansion tank, plug wires, and bigger pulley from Summit. Should be here by end of the week (hopefully).
Side note...there is huge power potential here. Looking at the VE tables now that they have been dialed in (+/- 2 LTFT), there is a HUGE amount of air going through the motor. I have to start my timing tables at -3* in the highest airmass columns (1200 - 1600 RPM) to prevent KR. I have also noticed that changing the stoich from 14.68100 to 14.42254 made a WORLD of difference in drivability...night and day in fact (and helped with the KR). Thinking of running 14.68100 stoich and opening the PE tables to command 14.42254 AFR with moderate throttle input before the BE tables kick in.
More to come....
Nice to know the system is operating as designed and not just a product of lower ambient temps. Still waiting on the expansion tank, plug wires, and bigger pulley from Summit. Should be here by end of the week (hopefully).
Side note...there is huge power potential here. Looking at the VE tables now that they have been dialed in (+/- 2 LTFT), there is a HUGE amount of air going through the motor. I have to start my timing tables at -3* in the highest airmass columns (1200 - 1600 RPM) to prevent KR. I have also noticed that changing the stoich from 14.68100 to 14.42254 made a WORLD of difference in drivability...night and day in fact (and helped with the KR). Thinking of running 14.68100 stoich and opening the PE tables to command 14.42254 AFR with moderate throttle input before the BE tables kick in.
More to come....
#27

Looks great man good job. Mine is waiting on a retune with a smaller pulley, and meth then D2 coilovers. After that its off to paint..
My 3.25 pulley only gives me 8 PSI. Im guessing my LS9 cam may be letting some boost get through.
My 3.25 pulley only gives me 8 PSI. Im guessing my LS9 cam may be letting some boost get through.
#28
TECH Fanatic
Thread Starter

So, I found out why I had so much boost...I ordered a larger pulley and changed it out when it arrived and found that I had 3.00" pulley already installed. My reasoning for going with that large of a pulley is that I have changed so much with the installation of the E Force, I would rather get the whole package right and then increase the boost incrementally.
Edit: HTTR!!!
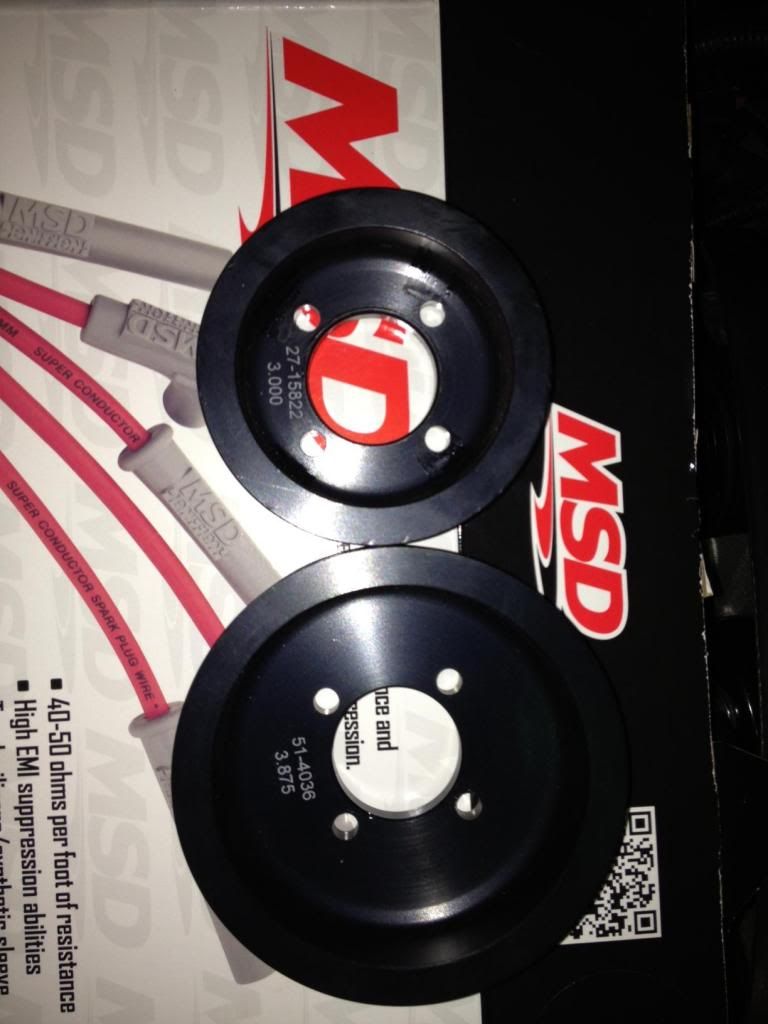
Last edited by DMM; 01-06-2013 at 04:09 PM.
#31
TECH Fanatic
Thread Starter

It's been pretty frustrating, honestly. Everything with the e Force is perfectly fine, it's only the "Jabsco" marine duty pumps I am using for the HEX that I am having issues with. When they work, the IAT's are 10* - 15* of ambient temps, so the system is working REALLY well.
My first pump leaked coolant past the shaft seal and filled the entire motor with coolant. It started making a horrible noise (go figure) and I finally took the motor apart to drain the half a quart of coolant. Keep in mind, it still worked but the coolant trashed the bearings. If anyone knows where I can get the little internal bearings for an electric motor, please let me know.
So, I order another one to replace it...to the tune of $180. It is what it is...anyhow, driving around and it starts running like pure crap. I hook up my laptop and find the IAT's are 140*+. Get home, pull the bumper cover to find the brand new Jabsco pump not running. I removed the impeller cover and find the motor seized. I break it loose, and get it going again and it's working fine. Drove it a while after installing the 8.8" and everything is fine. I leave this morning on the 100+ mile trip for training and the pump stops working again about 45 minutes into the trip...UGHHH!
So...I have two brand new Jabsco pumps...almost $400 worth of 12v electric pumps with less than 10 hours on each of them with hard failures.
Trying to find Jabsco's company info but cannot find a damn thing on them. The internet companies that I bought them from say they no longer sell the product and cannot assist...WTF? Strongly considering the ultimate dick move of calling AMEX and disputing the charges...at least I'd get my money back.
Other than that, runs like a top! I've been playing with the DFCO and have enabled the lean cruise option in the PCM and have been playing with the tables, hoping to have better than stock MPG.
You still looking to take my Gen IV Diff off my hands?
My first pump leaked coolant past the shaft seal and filled the entire motor with coolant. It started making a horrible noise (go figure) and I finally took the motor apart to drain the half a quart of coolant. Keep in mind, it still worked but the coolant trashed the bearings. If anyone knows where I can get the little internal bearings for an electric motor, please let me know.
So, I order another one to replace it...to the tune of $180. It is what it is...anyhow, driving around and it starts running like pure crap. I hook up my laptop and find the IAT's are 140*+. Get home, pull the bumper cover to find the brand new Jabsco pump not running. I removed the impeller cover and find the motor seized. I break it loose, and get it going again and it's working fine. Drove it a while after installing the 8.8" and everything is fine. I leave this morning on the 100+ mile trip for training and the pump stops working again about 45 minutes into the trip...UGHHH!
So...I have two brand new Jabsco pumps...almost $400 worth of 12v electric pumps with less than 10 hours on each of them with hard failures.
Trying to find Jabsco's company info but cannot find a damn thing on them. The internet companies that I bought them from say they no longer sell the product and cannot assist...WTF? Strongly considering the ultimate dick move of calling AMEX and disputing the charges...at least I'd get my money back.
Other than that, runs like a top! I've been playing with the DFCO and have enabled the lean cruise option in the PCM and have been playing with the tables, hoping to have better than stock MPG.
You still looking to take my Gen IV Diff off my hands?
#32

Having spent a good portion of my life on boats I would venture that the reason you are having this sort of failure rate with these pumps is the duty cycle you running them through. They seem like a bilge style pump (if not discount this altogether and I will go sit in my corner and stfu hehe) which is not designed to run continuously, but rather intermittently in an on demand function. This coupled with the fluid temperature you are pushing will lead to overheating of bilge style pumps. These pumps are not designed to move 100*+ degree water constantly. Bilge duty cycle's on boats are most commonly (with the size of motor you are running) going to be less than one minute sustained, unless you are sinking (your boned anyways then, break out the bail), water temps will be much lower as well. These factors in combination will lead to pumps that are running much hotter than they were originally designed to. Just my two cents, but it would be my bet in regard to those pumps.
#33

So, I order another one to replace it...to the tune of $180. It is what it is...anyhow, driving around and it starts running like pure crap. I hook up my laptop and find the IAT's are 140*+. Get home, pull the bumper cover to find the brand new Jabsco pump not running. I removed the impeller cover and find the motor seized. I break it loose, and get it going again and it's working fine. Drove it a while after installing the 8.8" and everything is fine. I leave this morning on the 100+ mile trip for training and the pump stops working again about 45 minutes into the trip...UGHHH!
So...I have two brand new Jabsco pumps...almost $400 worth of 12v electric pumps with less than 10 hours on each of them with hard failures.
Trying to find Jabsco's company info but cannot find a damn thing on them. The internet companies that I bought them from say they no longer sell the product and cannot assist...WTF? Strongly considering the ultimate dick move of calling AMEX and disputing the charges...at least I'd get my money back.
So...I have two brand new Jabsco pumps...almost $400 worth of 12v electric pumps with less than 10 hours on each of them with hard failures.
Trying to find Jabsco's company info but cannot find a damn thing on them. The internet companies that I bought them from say they no longer sell the product and cannot assist...WTF? Strongly considering the ultimate dick move of calling AMEX and disputing the charges...at least I'd get my money back.
http://www.ctgclean.com/tech-blog/20...rmance-curves/
On the 50840, the datasheet says that the motor must be located above the pump head if mounted vertically.
Last edited by FuzzyLog1c; 02-11-2013 at 06:48 PM.
#35
TECH Fanatic
Thread Starter

What model are you running? Some Jabsco pumps are rated for intermittent operation. Have you considered the possibility that the pump is overheating, either due to poor cooling, hot coolant, or too much flow resistance in your system?
http://www.ctgclean.com/tech-blog/20...rmance-curves/
On the 50840, the datasheet says that the motor must be located above the pump head if mounted vertically.
http://www.ctgclean.com/tech-blog/20...rmance-curves/
On the 50840, the datasheet says that the motor must be located above the pump head if mounted vertically.
I bought the second one as there was a possibility that I could have not set the seal properly on the first one causing the failure. I never disassembled the new pump though, and the motor shaft/impeller was seized tight. It took a hefty blow with a screw driver to free it, but it worked fine from that point on. There are plenty of posts about the Jabsco pumps (all models) seizing up in a short period of time. Wish I had done homework before taking the V2 guy's word about this thing.
Plenty of these pumps are installed in this manner, and the HEX operates at near zero PSI, and gravity won't do much of anything to a seal rated at 9 PSI+.
Looks as if I'll have to change my setup.
BTW Fuzzy...nice to see you're dug out...or did you get an internet connection to the snow castle?
#37
TECH Fanatic
Thread Starter

So I completely disassembled the Jabsco pump and found that one of the motor brushes was sticking...which explained the intermittent operation that was when cold. I will likely figure something else out with the HEX pump after I install the air filter in the inner fender well.
I'll most likely use a remote electric pump like this one...http://www.jegs.com/i/JEGS-Performan...ductId=1275715
Should have gone with this from the start.
I'll most likely use a remote electric pump like this one...http://www.jegs.com/i/JEGS-Performan...ductId=1275715
Should have gone with this from the start.
#38
Launching!

So I completely disassembled the Jabsco pump and found that one of the motor brushes was sticking...which explained the intermittent operation that was when cold. I will likely figure something else out with the HEX pump after I install the air filter in the inner fender well.
I'll most likely use a remote electric pump like this one...http://www.jegs.com/i/JEGS-Performan...ductId=1275715
Should have gone with this from the start.
I'll most likely use a remote electric pump like this one...http://www.jegs.com/i/JEGS-Performan...ductId=1275715
Should have gone with this from the start.
#39
TECH Fanatic
Thread Starter

I don't have any data on the twin, dual pass heat exchangers built into the E Force, so it's really a guessing game as to what will work the best. Since I am averaging about 10* - 15* above ambient temps when the system is functional, and nearly 140* when it's inoperative, I'd say I got pretty close.
I also spoke with Brian Tooley today (by far one of the nicest guys you could ever deal with BTW) about slightly modifying one of his cam profiles for use with my combo since it was really close to what I was looking for. I should be picking up a set of 317 heads next weekend so the cam will probably be ordered immediately afterwards since I may need new valve springs, seals, etc.
#40

Generally speaking, more = better with regards to a liquid/air heat exchanger system. If you take a standard system (take a V2 for example) and increase the available HEX surface area, hold more coolant, and increase the flow rate, you will see the benefit in lower IAT's.
I don't have any data on the twin, dual pass heat exchangers built into the E Force, so it's really a guessing game as to what will work the best. Since I am averaging about 10* - 15* above ambient temps when the system is functional, and nearly 140* when it's inoperative, I'd say I got pretty close.
I also spoke with Brian Tooley today (by far one of the nicest guys you could ever deal with BTW) about slightly modifying one of his cam profiles for use with my combo since it was really close to what I was looking for. I should be picking up a set of 317 heads next weekend so the cam will probably be ordered immediately afterwards since I may need new valve springs, seals, etc.
I don't have any data on the twin, dual pass heat exchangers built into the E Force, so it's really a guessing game as to what will work the best. Since I am averaging about 10* - 15* above ambient temps when the system is functional, and nearly 140* when it's inoperative, I'd say I got pretty close.
I also spoke with Brian Tooley today (by far one of the nicest guys you could ever deal with BTW) about slightly modifying one of his cam profiles for use with my combo since it was really close to what I was looking for. I should be picking up a set of 317 heads next weekend so the cam will probably be ordered immediately afterwards since I may need new valve springs, seals, etc.