fuel pump options
#21
TECH Fanatic

Totally disagree. For every pound of boost you have in the cylinder, you effectively have one less pound of fuel pressure at the rail. With 15 lbs of boost on a car equipped with a 60 PSI "dumb" regulated fuel system, you will effectively be delivering 25% less fuel volume for a given PWM on a given injector size. Running that lean is a surefire way to trigger detonation and destruction of your engine.
If you run out of static head, you need more pump or less flow restriction. Trying to control injector PWM to compensate for rapidly changing boost pressure is a recipe for a very bad car day. I assume that you're going to try to solve that problem by bandaiding your tune by running super rich. When you do that, you can kiss your fuel economy and your catalytic converters goodbye. And you won't be making as much power as you could if you invested in a fuel system sized appropriately for your engine's demands.
If you run out of static head, you need more pump or less flow restriction. Trying to control injector PWM to compensate for rapidly changing boost pressure is a recipe for a very bad car day. I assume that you're going to try to solve that problem by bandaiding your tune by running super rich. When you do that, you can kiss your fuel economy and your catalytic converters goodbye. And you won't be making as much power as you could if you invested in a fuel system sized appropriately for your engine's demands.
To answer your question on how to determine fueling...well, that's why you tune with a wide band and adjust fueling through MAF and VE, with PE and BE as multipliers. If you have to rely on additional fuel pressure to maintain proper fueling, that's when you'll have a bad day. The controller can make fueling adjustments much faster (and more accurately) than fuel pressure can.
Below is my VE map the controller uses for fueling. As you can see, as airmass (relative to RPM and MAP) increases, the fueling increases as well. This is where my controller looks for all its base fueling, there are additional PE (Performance Enrichment) and BE (Boost Enrichment) multiplier tables that adjust the A/F ratio when the conditions are satisfied.
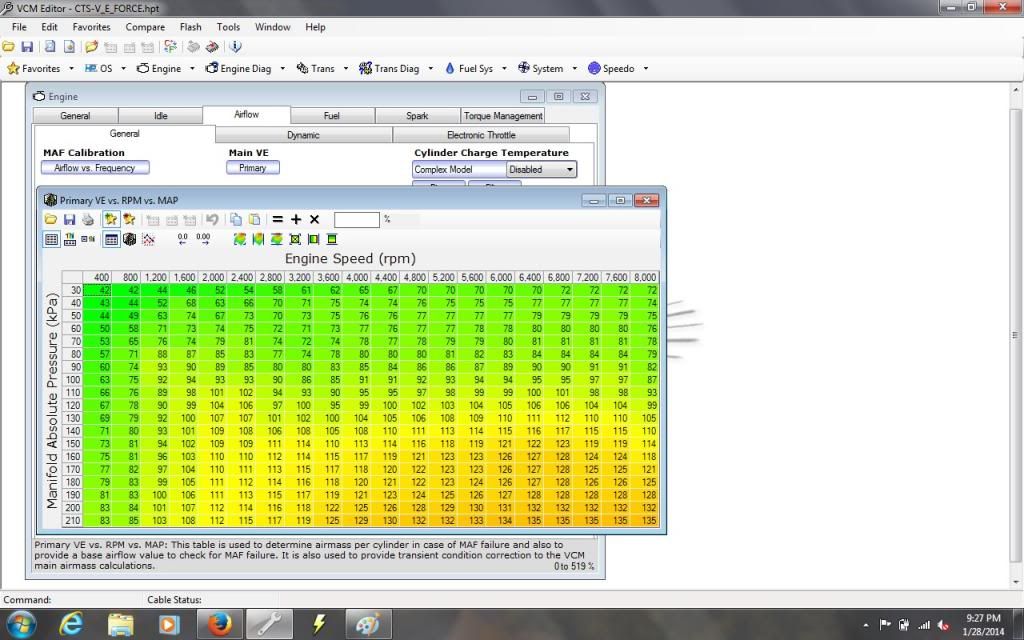
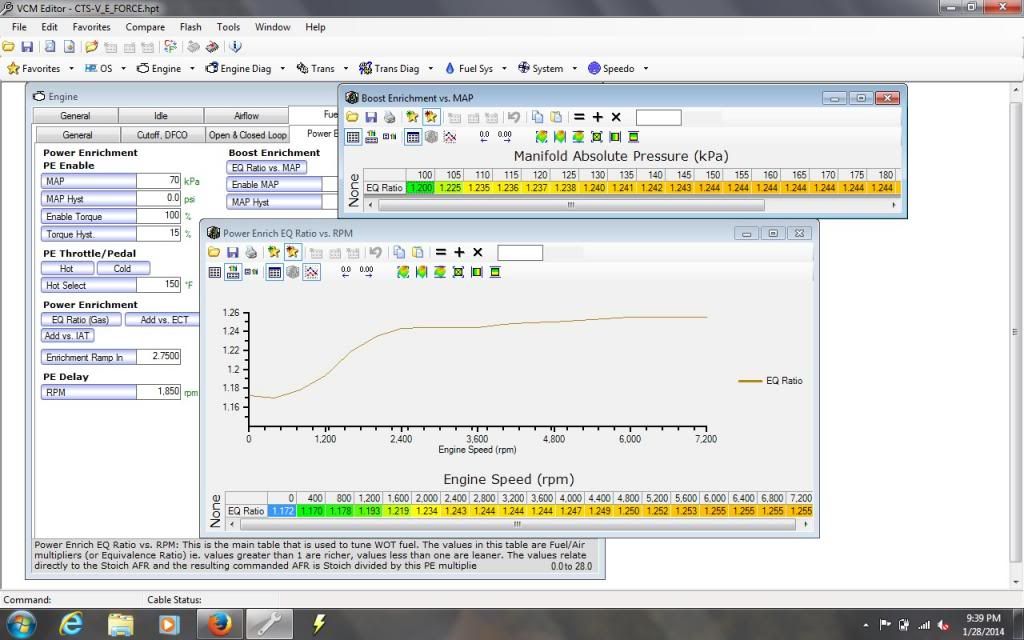
Last edited by DMM; 01-28-2014 at 08:58 PM.
#22

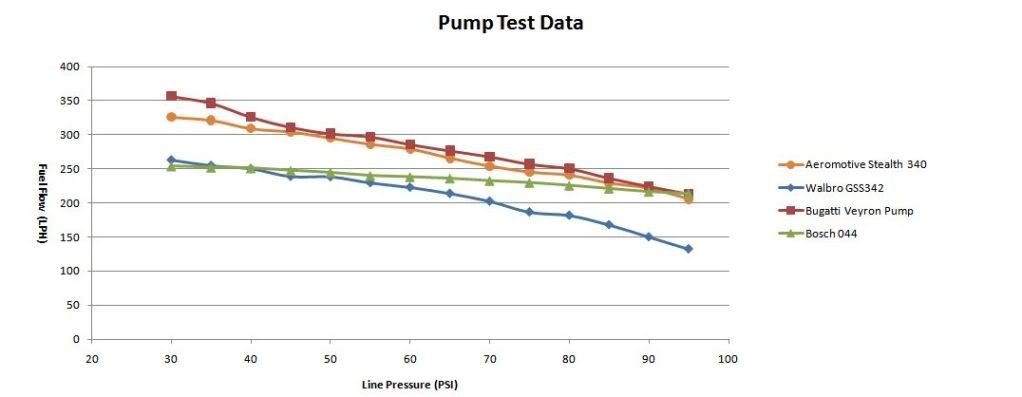
AFAIK, a regulator can respond faster to changing system conditions than the ECU can adapt with its sensor polling delays and limited control gain and bandwidth. Correct me if I'm wrong, but I think the most optimal fuel control system (and not just in a purely theoretical sense--this should have real, measurable horsepower implications) leverages the strengths of the mechanical and electrical control systems in the car to maintain a stable AFR. In other words, it's easier to tightly control a system that is already mostly stable.
Last edited by FuzzyLog1c; 01-28-2014 at 09:14 PM.
#23
TECH Fanatic

Yes, you are correct that having a stable fuel system is paramount. Otherwise, the controller is trying to hit a moving target for lack of a better term.
Flow rate does not always stay linear for very long as some pumps cannot handle the additional pressures. Granted, boost referencing does make things a little easier as the flow rate will not have a slope, but that does not really affect the tuning anyhow. I have not seen a situation where static fuel pressure created a lean condition unless under a LOT of boost. Even then, the referenced system is 3 BAR based.
And yes...the controller will always react faster than a mechanical regulator.
Here are a few posts by Lonnie:
Flow rate does not always stay linear for very long as some pumps cannot handle the additional pressures. Granted, boost referencing does make things a little easier as the flow rate will not have a slope, but that does not really affect the tuning anyhow. I have not seen a situation where static fuel pressure created a lean condition unless under a LOT of boost. Even then, the referenced system is 3 BAR based.
And yes...the controller will always react faster than a mechanical regulator.
Here are a few posts by Lonnie:
Here is my .02 as well.
First the 550rwhp is a safe number. Almost everyone can make it to 550rwhp & about half can see 600rwhp without a booster, but I cannot recommend this as it is my reputation if I sell an undersized pump.
As far as using RWHP, I do not like it, but in reality very few have their engines on an engine dyno... so there is not much other choice than to try & relate the pump size to RWHP. I take the dyno brand, geographical location, trans & rearend type into account when I discuss actual configurations with customers. Nitrous, supercharger & turbo cars are all different as well.
As far as boost referencing, it is less important with a large injector because there is ample reserve capacity. Using a smaller injector with high boost will surely limit the power capacity of an injector.
For example, a 60# injector (rated at 43.5psi) is a 70# flow equivalent at 58psi. Add 15# boost & you are back to the flow of a 60# injector without a boost reference. The boost reference will enable you to support roughly an additional 150hp with the same injector.
If you are running 96# injectors, you can run 43psi base pressure as well to make it easier on the fuel pump & still not worry about running out of injector until you are over 1000hp.
KP, since you are running one of those "red" regulators, I can understand your inconsistent results with it. (I'm trying to be gentle with my opinion, but trying to prevent others some unnecessary grief) I get about 1 call per month with boost reference problems when using that brand.... but don't blame me, I don't sell them. I've had very consistent results with Magnafuel & Weldon regulators in boost reference applications if anyone wants a recommendation.
Just a few items to think about.
First the 550rwhp is a safe number. Almost everyone can make it to 550rwhp & about half can see 600rwhp without a booster, but I cannot recommend this as it is my reputation if I sell an undersized pump.
As far as using RWHP, I do not like it, but in reality very few have their engines on an engine dyno... so there is not much other choice than to try & relate the pump size to RWHP. I take the dyno brand, geographical location, trans & rearend type into account when I discuss actual configurations with customers. Nitrous, supercharger & turbo cars are all different as well.
As far as boost referencing, it is less important with a large injector because there is ample reserve capacity. Using a smaller injector with high boost will surely limit the power capacity of an injector.
For example, a 60# injector (rated at 43.5psi) is a 70# flow equivalent at 58psi. Add 15# boost & you are back to the flow of a 60# injector without a boost reference. The boost reference will enable you to support roughly an additional 150hp with the same injector.
If you are running 96# injectors, you can run 43psi base pressure as well to make it easier on the fuel pump & still not worry about running out of injector until you are over 1000hp.
KP, since you are running one of those "red" regulators, I can understand your inconsistent results with it. (I'm trying to be gentle with my opinion, but trying to prevent others some unnecessary grief) I get about 1 call per month with boost reference problems when using that brand.... but don't blame me, I don't sell them. I've had very consistent results with Magnafuel & Weldon regulators in boost reference applications if anyone wants a recommendation.
Just a few items to think about.
Actually I told him to do it..... Madmax is running dual GSL392's. They do not like big pressure.
You not only have to boost reference for pressure compensation, but you also have to do so within the limits of the pump. If you try 58# base pressure & boost reference an additional 20#, you need 78psi. Most pumps will not be happy at this pressure or the flow will drop off significantly when you need it most (at high boost). The best way is to choose an injector that will support your power level while maintaining a max boost referenced pressure of under 65-70psi.
You not only have to boost reference for pressure compensation, but you also have to do so within the limits of the pump. If you try 58# base pressure & boost reference an additional 20#, you need 78psi. Most pumps will not be happy at this pressure or the flow will drop off significantly when you need it most (at high boost). The best way is to choose an injector that will support your power level while maintaining a max boost referenced pressure of under 65-70psi.
Last edited by DMM; 01-28-2014 at 09:44 PM.
#25

#26
TECH Addict
iTrader: (10)

Either way when ever I come to it (years

#28
TECH Fanatic

That would be my goal as well but I'm thinking procharger for right now. Plans change though. Are you staying with the stock tank? I'm going to look into a fuel cell.
#30
TECH Senior Member
iTrader: (18)

From what Ive been told by Lonnies who builds some nasty fuel systems is the stock tank just isnt designed well for high hp setups. If I ever wanted to make more then a single drop in could handle I would put a fuel cell in the spare tire well and run a magnafuel external pump. A lot more accessible, cheaper, and way easier to get a pump to handle whatever you need.
#31
TECH Fanatic
#32
TECH Fanatic

Lonnie installs a second Walbro pump outside of the module on a fixture he fabricates and installs in the tank. I was contemplating this with a foam surround to keep the fuel from sloshing away from the second pump although I found the PWM kit I was looking at before losing my old HDD.
I now believe that I am going to use two DW200 or DW65c pumps (the 300 series is too big) and have them paralleled into one outlet just as the V2 pumps are. I will remove the regulator from the module, seal the return, and install a single inlet/outlet fuel filter in the OE location using a Cavalier filter.
To make it all work I plan to rely on the "Fuel on Demand" kit which is a hell of a deal for $350.00 (Amazon has it for $313.00) and it is complete even including the pressure sensor. It is also the only PWM fuel controller that has a vac/boost port that can be configured through the software to increase fuel pressure 1:1 if you choose to do so. The software is complete and is like nothing I have seen with any other stand alone unit.
Here's the manual if anyone would like to check it out: http://www.professional-products.com...structions.pdf
I now believe that I am going to use two DW200 or DW65c pumps (the 300 series is too big) and have them paralleled into one outlet just as the V2 pumps are. I will remove the regulator from the module, seal the return, and install a single inlet/outlet fuel filter in the OE location using a Cavalier filter.
To make it all work I plan to rely on the "Fuel on Demand" kit which is a hell of a deal for $350.00 (Amazon has it for $313.00) and it is complete even including the pressure sensor. It is also the only PWM fuel controller that has a vac/boost port that can be configured through the software to increase fuel pressure 1:1 if you choose to do so. The software is complete and is like nothing I have seen with any other stand alone unit.
Here's the manual if anyone would like to check it out: http://www.professional-products.com...structions.pdf
Last edited by DMM; 01-29-2014 at 10:32 PM.
#34

Just a crazy thought, I know on the Dmaxes you can drill a 2-3 inch hole in the bottom of the tank and stick a sump on it. High HP diesels all run external lift pumps so that would be something I would think of doing if there is room instead of dealing with all the fuel pump nightmares that everyone seems to be having. Then again I sold my V1 and I can't remember what it looks like under there... and sloshing would be an issue to be addressed as well. Just thunked a thought.
#35

[QUOTE=FuzzyLog1c;17981710]I don't buy those fuel flow numbers. 98 LPH will only support 212.5 RWHP on a 0.5 BSFC, 58 PSI system. I thought the OEM pump was good for around 190 LPH rated pump @ 60 PSI. In order to support 400 RWHP on a LS6 motor with 0.5 BSFC and 58 PSI fuel system, theoretically, you need a pump that can deliver 185 LPH. We already know through dyno testing that people start to run out of headroom on the stock pump at around 400 RWHP (depending on actual BSFC). Which is why the Walbro GSS342 (255 LPH) pump is a very popular choice for bolt-on cars making less than 500 RWHP. And why the MP112 kits came with a Kenne Bell Boost-A-Pump. Running a pump rated at 13.5 VDC at 18 VDC will give you something like 45% more flow, albeit at the cost of massively increased heat generation and current consumption and reduced system lifetime.
Those numbers weren't produced through our fuel system. Just the stock bucket on a bench to show the difference in performance. They didn't have our rails, regulator, or lines. They used whatever they had on the bench. They did say though that the stock fuel bucket puts severe limitations on the flow due to the jet. You cant use that sheet to determine what your results will be without a test through a complete CTS-V fuel system
Those numbers weren't produced through our fuel system. Just the stock bucket on a bench to show the difference in performance. They didn't have our rails, regulator, or lines. They used whatever they had on the bench. They did say though that the stock fuel bucket puts severe limitations on the flow due to the jet. You cant use that sheet to determine what your results will be without a test through a complete CTS-V fuel system
#36

Just a crazy thought, I know on the Dmaxes you can drill a 2-3 inch hole in the bottom of the tank and stick a sump on it. High HP diesels all run external lift pumps so that would be something I would think of doing if there is room instead of dealing with all the fuel pump nightmares that everyone seems to be having. Then again I sold my V1 and I can't remember what it looks like under there... and sloshing would be an issue to be addressed as well. Just thunked a thought.
#37
TECH Regular
iTrader: (2)

Twin DW300 fuel pumps are used in the fuel module bucket. One pump is primary while the other is triggered using a pressure switch at 1-2 psi (Hobbs). Each fuel pump has it's own independent relay running in parallel and fed from the battery using 10awg.
The fuel lines use 8AN supply and 6AN return (1/2" and 3/8"). The fuel lines alone do not greatly expand the capabilities of the fuel system - it's the components! In order to use a 'proper' fuel regulator, you have to add a return fuel line to the system. The return line is coupled to the fuel module and dumped directly on the twin fuel pumps keeping them covered.
Having said all that, I do not expect fueling to be an issue when the boost comes. If the $1200 price tag seems high, that's because it is and that's also a typical price. By typical I mean similar cost on numerous other platforms where a very similar fuel mod was done.
#38

Philistine, I think we talked briefly about this last year, but it might be worth talking about again: do you think that it might be worth trying to run the second pump off a 4 or 6 psi Hobbs switch to avoid heating up the fuel unnecessarily?
Obviously, we'd want to show through testing that the primary pump can supply the engine up to the 4/6 psi power level and that the secondary pump can spool to rated speed fast enough to keep up with a WOT application right below the trigger point. This may be one of those ideas that works great on a turbocharged setup (or certain types of superchargers) that can't create a "brick wall" style torque curve.
Obviously, we'd want to show through testing that the primary pump can supply the engine up to the 4/6 psi power level and that the secondary pump can spool to rated speed fast enough to keep up with a WOT application right below the trigger point. This may be one of those ideas that works great on a turbocharged setup (or certain types of superchargers) that can't create a "brick wall" style torque curve.
Last edited by FuzzyLog1c; 01-31-2014 at 06:32 AM.
#39
TECH Regular
iTrader: (2)

Philistine, I think we talked briefly about this last year, but it might be worth talking about again: do you think that it might be worth trying to run the second pump off a 4 or 6 psi Hobbs switch to avoid heating up the fuel unnecessarily?
Obviously, we'd want to show through testing that the primary pump can supply the engine up to the 4/6 psi power level and that the secondary pump can spool to rated speed fast enough to keep up with a WOT application right below the trigger point. This may be one of those ideas that works great on a turbocharged setup (or certain types of superchargers) that can't create a "brick wall" style torque curve.
Obviously, we'd want to show through testing that the primary pump can supply the engine up to the 4/6 psi power level and that the secondary pump can spool to rated speed fast enough to keep up with a WOT application right below the trigger point. This may be one of those ideas that works great on a turbocharged setup (or certain types of superchargers) that can't create a "brick wall" style torque curve.
#40

Something that I don't yet understand is how much boost (if any) a heavily-overdriven supercharger might make below 2000 RPM. It would be a waste of time and money building/installing the relays, Hobbs switch, and indication lights if both pumps are going to wind up run continuously. It's just something else I have to check on.
Last edited by FuzzyLog1c; 01-31-2014 at 07:51 AM.