11/1 compression 8 psi vs 8.4/1 with 15 psi, same dynamic is one more or less safe?
#21
8 Second Club
iTrader: (4)

Mitsubishi Lancer Evo IX MR 870+Ps@11.000rpm (Boost 14psi) - YouTube
High compression + boost = awesomeness
High compression + boost = awesomeness
Though comparing a small bore 2.0, with a 4V head reving to 11k isn't exactly a good comparison.
Still.. I bet I could spank him with a $200 8.5:1 JY motor and never rev over 6k.

#22
9 Second Club

Mitsubishi Lancer Evo IX MR 870+Ps@11.000rpm (Boost 14psi) - YouTube
High compression + boost = awesomeness
High compression + boost = awesomeness
I dont know anyone who's been able to buy any of their products, and for their huge power claims...actual real world performance of any cars they have posted videos of...well, doesnt seem to back the claims
#23

IMO starting out at 11:1 static is too high for a forced induction pump gas setup. A big cam effectively reduces the DCR because it delays the intake valve closing point. The longer you delay this past the optimal point, the more problems you’ll run into. Timing, reversion, poor cylinder filling etc.
Because a cam calculator spit out 7.8:1 DCR does not mean your DCR will be 7.8:1 your entire RPM range. The majority of the DCR drop effect caused by a large cam will happen at low engine speeds. As RPM increases, the DCR will increase as well. I think this will get you into trouble when mixed with boost.
Sounds like your trying to use the cam as a crutch when what you really need to do is drop your static compression. The cam should be matched to your engine and desired power band. What you plan on doing is VERY counterproductive and I don’t think you’ll be happy with the results.
Because a cam calculator spit out 7.8:1 DCR does not mean your DCR will be 7.8:1 your entire RPM range. The majority of the DCR drop effect caused by a large cam will happen at low engine speeds. As RPM increases, the DCR will increase as well. I think this will get you into trouble when mixed with boost.
Sounds like your trying to use the cam as a crutch when what you really need to do is drop your static compression. The cam should be matched to your engine and desired power band. What you plan on doing is VERY counterproductive and I don’t think you’ll be happy with the results.
#24
8 Second Club
iTrader: (4)

i can drop my static down to 10.54 with a .060 gasket but then would i mess up the quench and be counterproductive? the motor is together and i'm not changing pistons or heads... i do have -10cc dished pistons and have heard that the quench acts differently with dished vs flat tops
I know they make thicker than .060 head gaskets. Cometic makes a .070 gasket you can purchase off the shelf. They also will make a custom HG any thickness you want. I ran a 3mm (.11”) head gasket on my inline 6. Worked great.
#25

You would have to know what your quench area was. From what I’ve read there is an ideal “window” of .035-.065. Going to tighter will usually end up in piston to valve contact. Going slightly less than ideal will increase you chance of knock. .070-.110 is generally considered a BAD area. Once out of this range you basically have a “non quench” engine and your good to go!
I know they make thicker than .060 head gaskets. Cometic makes a .070 gasket you can purchase off the shelf. They also will make a custom HG any thickness you want. I ran a 3mm (.11”) head gasket on my inline 6. Worked great.
I know they make thicker than .060 head gaskets. Cometic makes a .070 gasket you can purchase off the shelf. They also will make a custom HG any thickness you want. I ran a 3mm (.11”) head gasket on my inline 6. Worked great.
#26
8 Second Club
iTrader: (4)

http://www.crankshaftcoalition.com/wiki/Quench
Pretty much, but the piston dish throws a bit of a loop in there. Do your dished pistons have a quench pad? I'd ask TSP personally what they suggest.
Pretty much, but the piston dish throws a bit of a loop in there. Do your dished pistons have a quench pad? I'd ask TSP personally what they suggest.
#28

Since your making 520whp now I see no problem making 700whp on 8 psi. If you keep the compression up run meth. Maybe I missed it but which head unit are you going to run?
#29

Flow Data:
No Exhaust Pipe
LIFT INTAKE FLOW EXHAUST FLOW
.100" 66 CFM 57 CFM
.200" 147 CFM 117 CFM
.300" 228 CFM 170 CFM
.400" 282 CFM 206 CFM
.500" 321 CFM 227 CFM
.600" 343 CFM 235 CFM
.650" 355 CFM 241 CFM
.700" 360 CFM 245 CFM
#31

IMO starting out at 11:1 static is too high for a forced induction pump gas setup. A big cam effectively reduces the DCR because it delays the intake valve closing point. The longer you delay this past the optimal point, the more problems you’ll run into. Timing, reversion, poor cylinder filling etc.
Because a cam calculator spit out 7.8:1 DCR does not mean your DCR will be 7.8:1 your entire RPM range. The majority of the DCR drop effect caused by a large cam will happen at low engine speeds. As RPM increases, the DCR will increase as well. I think this will get you into trouble when mixed with boost.
Sounds like your trying to use the cam as a crutch when what you really need to do is drop your static compression. The cam should be matched to your engine and desired power band. What you plan on doing is VERY counterproductive and I don’t think you’ll be happy with the results.
Because a cam calculator spit out 7.8:1 DCR does not mean your DCR will be 7.8:1 your entire RPM range. The majority of the DCR drop effect caused by a large cam will happen at low engine speeds. As RPM increases, the DCR will increase as well. I think this will get you into trouble when mixed with boost.
Sounds like your trying to use the cam as a crutch when what you really need to do is drop your static compression. The cam should be matched to your engine and desired power band. What you plan on doing is VERY counterproductive and I don’t think you’ll be happy with the results.
#32

also i would not be considering this if it were not on a centrifugal blower... my buddy with the novi 5.0 has 9-10psi on 11/1 compresiion running 19 degrees timing with no knock at all even in hot ambient... his iat never goes above ambient as well and he is not running meth or race gas either, its on pump and he makes 650rwhp and traps consistet 135-136 at 10.2-10.4 in the quarter
#33
8 Second Club
iTrader: (4)

I think you should run the most compression you can to achieve your power goal on the fuel you plan to run. Since your starting with pump gas, 11:1 is too high IMO. The amount of cylinder pressure you’d need to bleed off to run decent boost would be counterproductive. Your just wasting power and you’ll have a cam that’s not matched properly the motor. A cams main purpose is to time the valve events to produce the broadest power range in your engines rpm window. It’s not meant to drop 2-3 points of compression! Hanging the valves open that long is a waste.
Assuming you could keep the cylinder pressure exactly the same then the knock threshold would be the same for both engines. In the real world there’s no way you could do that. What your talking about doing won’t accomplish equal cylinder pressures.
I'm not saying it won't work either. I'm just saying I'd go the other route. Try it, let us know.
#34

A cams main purpose is to time the valve events to produce the broadest power range in your engines rpm window. It’s not meant to drop 2-3 points of compression! Hanging the valves open that long is a waste.
I'm not saying it won't work either. I'm just saying I'd go the other route. Try it, let us know.
I'm not saying it won't work either. I'm just saying I'd go the other route. Try it, let us know.
the cam i'm using now is the one i would be using with the blower. it is an n/a cam, but it will also work with 8 psi well, the same as how stock ls3 picks up 190 to 200 rwhp on 7psi with a procharger with the stock cam and 10.7 compression, those cams are 8.3 dynamic and have absolutely no problems with boost, i get what your saying about maximizing a setup, but my setup runs strong n/a and with just 7-8 psi i will be able to hit around 700rwhp no prob, i'm not trying to have any more than that and 8psi should be no issue at all, i talked to my tuner about it and he agrees, he only thinks its a bad idea to run 10psi or up on 11/1 and most of the stuff they tune on is boost
this is my n/a graph
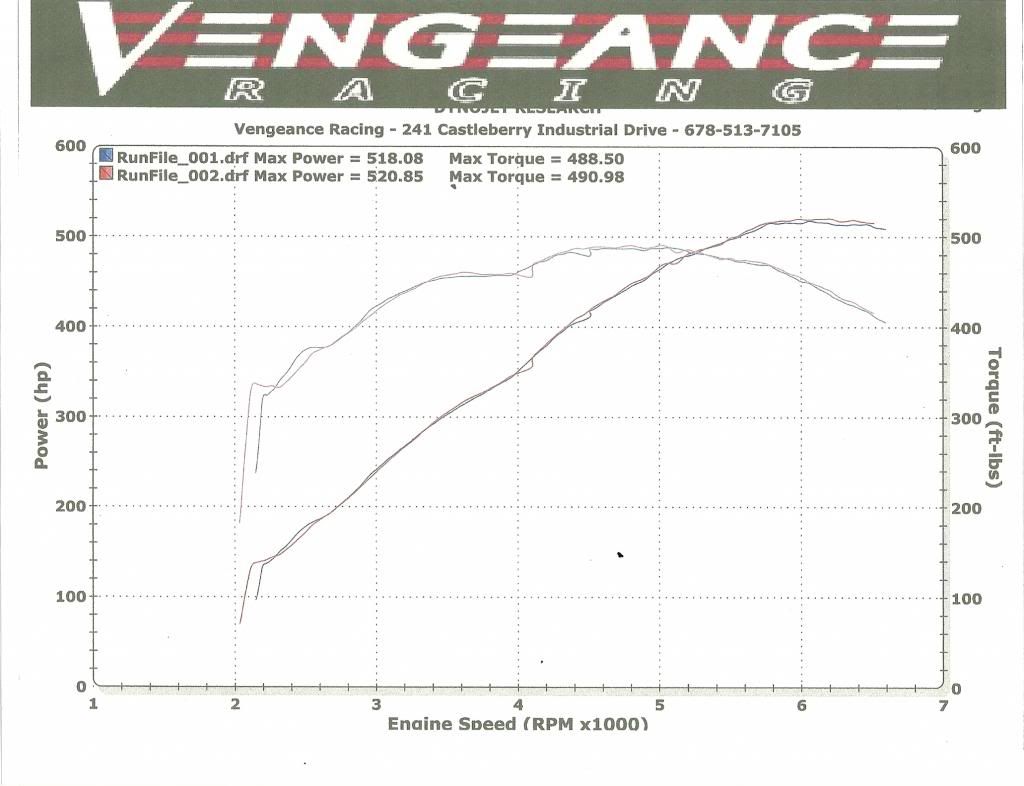