MAF or not to MAF with 10psi or SD?!
#21

I don't see the scaling as a big issue, but looking at your picture, a MAF is not even an option. You have room for one but that BOV would totally wreak havoc on it.
Go SD.... it works fine.
Beautiful looking engine bay by the way.
To add.. looking at the pic again you actually have a great straight piece of pipe for a car style MAF... and welding a bung on is easy..... but again... wont work with BOV there.
Go SD.... it works fine.
Beautiful looking engine bay by the way.
To add.. looking at the pic again you actually have a great straight piece of pipe for a car style MAF... and welding a bung on is easy..... but again... wont work with BOV there.
Yea the MAF has to be after the BOV right? Otherwise the BOV bleeds metered air. Ugh lol. Could flip the charge pipe but the BOV would prob be put into the hood as the 4" cowl is really only in the center for like 1ft on each side of the engine bay centerline.
Thank u for the compliment. It's still a frigin mess but wait till u see when it's done lol. Not bad for a stock 150k motor

Torqstorm welds all that stuff on like the BOV, 1/8"npt and 1/4"npt bungs so I have no say on the setup or placement. If I were to change the tubing I would prob run a really small A2A IC and keep the meth but then I would purchase couplers that had provisions for the card style MAF a universal BOV etc since I would be routing the tubing all over. But for now I'm sticking with how it is and working wiTh what I got. Plus once I get the SD tune down I doubt I'll need to ever go back to MAF.
#22

I got 2 bad one's 1 st got random back fires. til it went out .2nd the 0 to 5 volt table spike so bad til through 1635 code .which shut truck off til computer was reset stick with gm or some other name brand
#23

I'm probably going with SD at this point. But I do still have the original MAF to the truck and motor which is a Delphi. But at this point it's not going in I don't think.
#25

When I went to EFI university tuning school, the way the MAF and MAP functions were described this way: The MAP is the sensor used for transitions, on and off the throttle, changes in RPM, where the sensor has a faster response. The MAF is more accurate in measuring the true airflow, but slower to stabilize, also somewhat due to the elasticity of the air it measures. Simply put, the MAF works better steady state, think cruising at 75 with the cruise control on, but the MAP does a better job running around town and beating the car up. As others have said, the MAF is fussy about placement in the tube, being in a straight section, and proximity to the BOV, as it will seriously mess with it's function. I vote SD all the way in your application.
#27

Thanks for the responses.
So SD gives better throttle response but MAF would handle larger changes in ambient temps. Only reason I say that is because in the spring/fall I might drive the car in 70* weather, then drive in the summer at 90-100*F when car shows are going on... thats quite of range in temp for a SD tune to work in no? I just know that MAF's are more forgiving and SD can be a picky bitch.
So SD gives better throttle response but MAF would handle larger changes in ambient temps. Only reason I say that is because in the spring/fall I might drive the car in 70* weather, then drive in the summer at 90-100*F when car shows are going on... thats quite of range in temp for a SD tune to work in no? I just know that MAF's are more forgiving and SD can be a picky bitch.
Having a wideband log while you drive each individual air/fuel ratio per cell makes it a LOT faster. Here is an example,

I can set it to only show me values which have a certain threshold of log points, and I can show max, min, or average values for those cells over any distance drive. That way I weed out cells which may have collected only transient data. I can also watch a replay of the drive to determine if an individual cell has good data or not, based on what the engine was doing at the time. Then, finally, I can use an excel formula (or calculate by hand) a fairly accurate percentage adjustment value (it compares desired a/f with actual a/f), and copy/paste the adjustment back into the ECU and go for a new drive to confirm. It also means I can log the drive with a closed laptop next to me, and not have to tune while driving. If you would like the excel file I have that is capable of doing this math PM me.
The best pro to the maf is the ease of tuning and reliability in daily driver applications, and especially for beginners to tuning. The downside is presence of the sensor, additional plumbing, the sensitivity of the maf to turbulence (you need a well designed tube, and no compressor surge/ a well designed recirculated bypass valve for boost applications where applicable) and you must have NO intake/boost leaks if you want to drive the car on the maf (no limping home without a proper leak-free plumbing).
Last edited by kingtal0n; 02-29-2016 at 01:37 PM.
#28

PM sent!
I just got the PCM and harness mounted into the car. So hope to finish some more stuff up and then start working on the ECM tuning. Which I need the battery in the car to do.
I just got the PCM and harness mounted into the car. So hope to finish some more stuff up and then start working on the ECM tuning. Which I need the battery in the car to do.
#29

It isn't temperature that makes SD a picky bitch, its the way the fuel map reflects engine VE. A MAF car I can tune in an hour, its done quick, because you just program the upper airflow values to the air fuel ratio you desire and tweak it slightly after a few street passes. SD tuning is completely different; you drive around, sometimes for hours, making minor adjustments to a fully warm engine seeking perfect air/fuel values for every cell, and there are a whole bunch of cells, some you can't ever expect to reach, and some right near those that you know would be difficult to hit but still have a chance to get there in some situations.
Having a wideband log while you drive each individual air/fuel ratio per cell makes it a LOT faster. Here is an example,
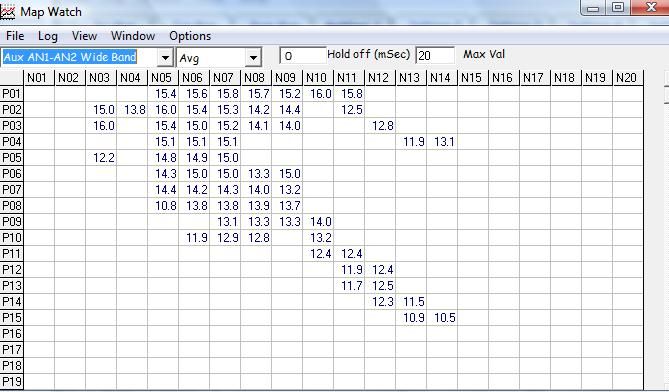
I can set it to only show me values which have a certain threshold of log points, and I can show max, min, or average values for those cells over any distance drive. That way I weed out cells which may have collected only transient data. I can also watch a replay of the drive to determine if an individual cell has good data or not, based on what the engine was doing at the time. Then, finally, I can use an excel formula (or calculate by hand) a fairly accurate percentage adjustment value (it compares desired a/f with actual a/f), and copy/paste the adjustment back into the ECU and go for a new drive to confirm. It also means I can log the drive with a closed laptop next to me, and not have to tune while driving. If you would like the excel file I have that is capable of doing this math PM me.
The best pro to the maf is the ease of tuning and reliability in daily driver applications, and especially for beginners to tuning. The downside is presence of the sensor, additional plumbing, the sensitivity of the maf to turbulence (you need a well designed tube, and no compressor surge/ a well designed recirculated bypass valve for boost applications where applicable) and you must have NO intake/boost leaks if you want to drive the car on the maf (no limping home without a proper leak-free plumbing).
Having a wideband log while you drive each individual air/fuel ratio per cell makes it a LOT faster. Here is an example,
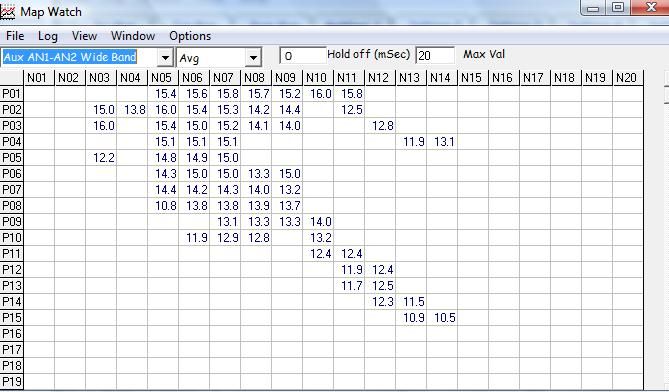
I can set it to only show me values which have a certain threshold of log points, and I can show max, min, or average values for those cells over any distance drive. That way I weed out cells which may have collected only transient data. I can also watch a replay of the drive to determine if an individual cell has good data or not, based on what the engine was doing at the time. Then, finally, I can use an excel formula (or calculate by hand) a fairly accurate percentage adjustment value (it compares desired a/f with actual a/f), and copy/paste the adjustment back into the ECU and go for a new drive to confirm. It also means I can log the drive with a closed laptop next to me, and not have to tune while driving. If you would like the excel file I have that is capable of doing this math PM me.
The best pro to the maf is the ease of tuning and reliability in daily driver applications, and especially for beginners to tuning. The downside is presence of the sensor, additional plumbing, the sensitivity of the maf to turbulence (you need a well designed tube, and no compressor surge/ a well designed recirculated bypass valve for boost applications where applicable) and you must have NO intake/boost leaks if you want to drive the car on the maf (no limping home without a proper leak-free plumbing).

#30

The problem with a load dyno is, that it must be used properly, which they rarely are. You can't just load the engine to hold specific sites on the map because there is no bearing on vehicle weight, its just enough load to hit the cell (like some kinds of engine dyno). The engine's rate of change of RPM depends on vehicle weight (heavier vehicle = slower rate of change acceleration) and that is the critical key feature of ignition timing advance that a load dyno will often be used incorrectly for, since they can be used to hold any load/rpm you desire, the cell is "artificial" for those conditions, i.e. you will never actually have that kind of engine load with the same acceleration (Rate of change), only that one time, that one day, on the dyno does it exist.
For example. Take any car/engine, (imagine your own car if you want) and put your foot all the way down, WOT. You know what that feels like right? So tell me, now, where was the MAP sensor during the run? If the car was N/A it sat on 0psi the entire time at WOT.
Now, start adding cement blocks to the trunk. The car (engine) will now accelerate more slowly, the more weight you add. This calls for reduced ignition timing. The factory computer handles this well because as soon as the knock sensor starts to raise it's hand, the timing is reduced on the fly, and possibly an alternative low octane map becomes more and more used. Now let me ask you: did the MAP sensor reading change during WOT? Nope, still 0psi, even though the entire tune needed to be changed to compensate for the additional weight, the MAP sensor never gave a hint of any difference (it still sat in the exact same cells the entire time as before). The same thing happens in reverse, if you start removing weight, the car gets lighter, the map still reads 0psi across the board, but now the tune has once again changed for those cells because vehicle weight changed.
So when you are on a load dyno, there is no "vehicle weight" (rolling resistance), there is only user defined load. So whatever cell you are tuning inside, is only for that one specific load, i.e. it does not reflect the actual condition the engine will run in once the vehicle weight is applied in each gear (this usually leads to over-timing the engine, since getting a peak number on the dyno is a thing those inexperienced tend to shoot for, i.e. use less load and more timing and it looks like you have more safe power, until the vehicle is back on the road and starts knocking) Since gearing and time spent at WOT will also influence the final outcome (such as a rising EGT or cylinder head temp)... I tend to tune my cars on the street to simulate actual engine load, actual rate of change, and use a little common sense based on the application (ask the owner, "you ever intend to carry 4 passengers and luggage?" etc)
#31

The problem with a load dyno is, that it must be used properly, which they rarely are. You can't just load the engine to hold specific sites on the map because there is no bearing on vehicle weight, its just enough load to hit the cell (like some kinds of engine dyno). The engine's rate of change of RPM depends on vehicle weight (heavier vehicle = slower rate of change acceleration) and that is the critical key feature of ignition timing advance that a load dyno will often be used incorrectly for, since they can be used to hold any load/rpm you desire, the cell is "artificial" for those conditions, i.e. you will never actually have that kind of engine load with the same acceleration (Rate of change), only that one time, that one day, on the dyno does it exist.
For example. Take any car/engine, (imagine your own car if you want) and put your foot all the way down, WOT. You know what that feels like right? So tell me, now, where was the MAP sensor during the run? If the car was N/A it sat on 0psi the entire time at WOT.
Now, start adding cement blocks to the trunk. The car (engine) will now accelerate more slowly, the more weight you add. This calls for reduced ignition timing. The factory computer handles this well because as soon as the knock sensor starts to raise it's hand, the timing is reduced on the fly, and possibly an alternative low octane map becomes more and more used. Now let me ask you: did the MAP sensor reading change during WOT? Nope, still 0psi, even though the entire tune needed to be changed to compensate for the additional weight, the MAP sensor never gave a hint of any difference (it still sat in the exact same cells the entire time as before). The same thing happens in reverse, if you start removing weight, the car gets lighter, the map still reads 0psi across the board, but now the tune has once again changed for those cells because vehicle weight changed.
So when you are on a load dyno, there is no "vehicle weight" (rolling resistance), there is only user defined load. So whatever cell you are tuning inside, is only for that one specific load, i.e. it does not reflect the actual condition the engine will run in once the vehicle weight is applied in each gear (this usually leads to over-timing the engine, since getting a peak number on the dyno is a thing those inexperienced tend to shoot for, i.e. use less load and more timing and it looks like you have more safe power, until the vehicle is back on the road and starts knocking) Since gearing and time spent at WOT will also influence the final outcome (such as a rising EGT or cylinder head temp)... I tend to tune my cars on the street to simulate actual engine load, actual rate of change, and use a little common sense based on the application (ask the owner, "you ever intend to carry 4 passengers and luggage?" etc)
For example. Take any car/engine, (imagine your own car if you want) and put your foot all the way down, WOT. You know what that feels like right? So tell me, now, where was the MAP sensor during the run? If the car was N/A it sat on 0psi the entire time at WOT.
Now, start adding cement blocks to the trunk. The car (engine) will now accelerate more slowly, the more weight you add. This calls for reduced ignition timing. The factory computer handles this well because as soon as the knock sensor starts to raise it's hand, the timing is reduced on the fly, and possibly an alternative low octane map becomes more and more used. Now let me ask you: did the MAP sensor reading change during WOT? Nope, still 0psi, even though the entire tune needed to be changed to compensate for the additional weight, the MAP sensor never gave a hint of any difference (it still sat in the exact same cells the entire time as before). The same thing happens in reverse, if you start removing weight, the car gets lighter, the map still reads 0psi across the board, but now the tune has once again changed for those cells because vehicle weight changed.
So when you are on a load dyno, there is no "vehicle weight" (rolling resistance), there is only user defined load. So whatever cell you are tuning inside, is only for that one specific load, i.e. it does not reflect the actual condition the engine will run in once the vehicle weight is applied in each gear (this usually leads to over-timing the engine, since getting a peak number on the dyno is a thing those inexperienced tend to shoot for, i.e. use less load and more timing and it looks like you have more safe power, until the vehicle is back on the road and starts knocking) Since gearing and time spent at WOT will also influence the final outcome (such as a rising EGT or cylinder head temp)... I tend to tune my cars on the street to simulate actual engine load, actual rate of change, and use a little common sense based on the application (ask the owner, "you ever intend to carry 4 passengers and luggage?" etc)
Good post.