LSX is ready to be dropped in tomorrow (PICS!)
#1121
10 Second Club
Thread Starter
iTrader: (37)
Join Date: Jan 2004
Posts: 1,935
Likes: 0
Received 0 Likes
on
0 Posts

No graph yet but I'll have one soon, hopefully it will be a little easier to troubleshoot looking at the graph. Or maybe I'll get lucky and the spark plug wire was the issue and it will make the power it should this time.
#1122
FormerVendor

No sense in speculating until it is back on the dyno without a burned plug wire.
I don't know when the wire cooked but I can tell you I couldn't feel or hear a misfire though I know it must have been.
Can't hear or feel much as far as a misfire when the car has no mufflers, an F2 and 4k converter.
IMO the cam and springs are fine (though the cam may not be ideal). Boost pressure from a supercharged car should not effect valvetrain stability. Backpressure from a turbo is another story.
Anyway, lets go through the motions on the intake valve.
Intake stroke- closed valve has 26psi of boost behind it and begins to open. Air begins to fill the cylinder and pressure between intake and cylinder begins to equalize.
valve starts closing and cylinder pressure/intake pressure should be rather close. As soon as the intake valve closes the Compression cycle starts and cylinder pressure immediately eclipses intake manifold pressure.
Power stroke, until exhaust blowdown. Cycle starts over at end of exhaust stroke during overlap.
Not really seeing any reason a supercharged engine needs more valvespring due to boost pressure, only that it extends the usable rpm range of the engine.
Anyway, I think the low numbers are due to the torque converter, which certainly isn't up to task, and the cooked wire. Will re-evaluate once I get it back on the rollers.
I don't know when the wire cooked but I can tell you I couldn't feel or hear a misfire though I know it must have been.
Can't hear or feel much as far as a misfire when the car has no mufflers, an F2 and 4k converter.
IMO the cam and springs are fine (though the cam may not be ideal). Boost pressure from a supercharged car should not effect valvetrain stability. Backpressure from a turbo is another story.
Anyway, lets go through the motions on the intake valve.
Intake stroke- closed valve has 26psi of boost behind it and begins to open. Air begins to fill the cylinder and pressure between intake and cylinder begins to equalize.
valve starts closing and cylinder pressure/intake pressure should be rather close. As soon as the intake valve closes the Compression cycle starts and cylinder pressure immediately eclipses intake manifold pressure.
Power stroke, until exhaust blowdown. Cycle starts over at end of exhaust stroke during overlap.
Not really seeing any reason a supercharged engine needs more valvespring due to boost pressure, only that it extends the usable rpm range of the engine.
Anyway, I think the low numbers are due to the torque converter, which certainly isn't up to task, and the cooked wire. Will re-evaluate once I get it back on the rollers.
#1123
10 Second Club
Thread Starter
iTrader: (37)
Join Date: Jan 2004
Posts: 1,935
Likes: 0
Received 0 Likes
on
0 Posts

Thanks for clearing that up Jim. Can't wait to see how it does this time around. If it's still the same, I'll need to try a tighter converter. I might as well wait to do that until I have the fuel system to support it though.
#1125
10 Second Club
Thread Starter
iTrader: (37)
Join Date: Jan 2004
Posts: 1,935
Likes: 0
Received 0 Likes
on
0 Posts


#1126
TECH Addict
iTrader: (24)

No sense in speculating until it is back on the dyno without a burned plug wire.
I don't know when the wire cooked but I can tell you I couldn't feel or hear a misfire though I know it must have been.
Can't hear or feel much as far as a misfire when the car has no mufflers, an F2 and 4k converter.
IMO the cam and springs are fine (though the cam may not be ideal). Boost pressure from a supercharged car should not effect valvetrain stability. Backpressure from a turbo is another story.
Anyway, lets go through the motions on the intake valve.
Intake stroke- closed valve has 26psi of boost behind it and begins to open. Air begins to fill the cylinder and pressure between intake and cylinder begins to equalize.
valve starts closing and cylinder pressure/intake pressure should be rather close. As soon as the intake valve closes the Compression cycle starts and cylinder pressure immediately eclipses intake manifold pressure.
Power stroke, until exhaust blowdown. Cycle starts over at end of exhaust stroke during overlap.
Not really seeing any reason a supercharged engine needs more valvespring due to boost pressure, only that it extends the usable rpm range of the engine.
Anyway, I think the low numbers are due to the torque converter, which certainly isn't up to task, and the cooked wire. Will re-evaluate once I get it back on the rollers.
I don't know when the wire cooked but I can tell you I couldn't feel or hear a misfire though I know it must have been.
Can't hear or feel much as far as a misfire when the car has no mufflers, an F2 and 4k converter.
IMO the cam and springs are fine (though the cam may not be ideal). Boost pressure from a supercharged car should not effect valvetrain stability. Backpressure from a turbo is another story.
Anyway, lets go through the motions on the intake valve.
Intake stroke- closed valve has 26psi of boost behind it and begins to open. Air begins to fill the cylinder and pressure between intake and cylinder begins to equalize.
valve starts closing and cylinder pressure/intake pressure should be rather close. As soon as the intake valve closes the Compression cycle starts and cylinder pressure immediately eclipses intake manifold pressure.
Power stroke, until exhaust blowdown. Cycle starts over at end of exhaust stroke during overlap.
Not really seeing any reason a supercharged engine needs more valvespring due to boost pressure, only that it extends the usable rpm range of the engine.
Anyway, I think the low numbers are due to the torque converter, which certainly isn't up to task, and the cooked wire. Will re-evaluate once I get it back on the rollers.
But, 24 degrees of overlap, ~70 or so at 6thou lift is most likely a source of lost fuel. Probably would make a substantial more amount of power if there was a properly spec'ed cam for the setup!
Keep is posted!
#1127
10 Second Club
Thread Starter
iTrader: (37)
Join Date: Jan 2004
Posts: 1,935
Likes: 0
Received 0 Likes
on
0 Posts

Well, if its not the springs, then definitely could be the burned hole haha. I must have missed the part of the burned wire. Sometimes you really can't even tell. I once accidentally left one of my wires completely off the plug and didn't even notice for a few mins while the motor was warming up at idle. No misfire, no stalling, nothing. I saw it, put it back on, and no change haha. Still ran fine.
But, 24 degrees of overlap, ~70 or so at 6thou lift is most likely a source of lost fuel. Probably would make a substantial more amount of power if there was a properly spec'ed cam for the setup!
Keep is posted!
But, 24 degrees of overlap, ~70 or so at 6thou lift is most likely a source of lost fuel. Probably would make a substantial more amount of power if there was a properly spec'ed cam for the setup!
Keep is posted!
#1128
10 Second Club
Thread Starter
iTrader: (37)
Join Date: Jan 2004
Posts: 1,935
Likes: 0
Received 0 Likes
on
0 Posts

It won't be able to get on the dyno until next Wednesday so for now I just have to wait. I'll post a vid later tonight of it running though so you guys can check it out but no street vids or dyno numbers until we put it back on the dyno and make sure the tune is good.
#1129
TECH Addict
iTrader: (24)

You may be right about the cam eating more fuel but I don't think it hurts power on a blower set-up. Turbo, yes but that's a whole different animal. With my set-up, I wouldn't be surprized if a cam with less over lap made a little more boost but I obviously don't need that and I think the power would be about the same anyway. My 346 & D1 did better than most and it had a cam everyone said was too big also, 232/234 .598/.598 on 112lsa. It made 680rwhp and was performing even better at the track. I figured this new cam I spec'd would work close to that with the bigger 402 engine. That's why I chose it, just trying to use what worked before just on a bigger playing field.
#1130
10 Second Club
Thread Starter
iTrader: (37)
Join Date: Jan 2004
Posts: 1,935
Likes: 0
Received 0 Likes
on
0 Posts

Your old cam would've been perfect. That cam has 9 degrees of overlap, MUCH less than the one you have now (at 23 degrees), and is the reason why it made good power on your blower setup, trapping most of the air and not bleeding it off out the exhaust. I wouldn't worry about making too much boost, thats what your boost controller is for. I would be more concerned with efficiency = power. Having FI allows you to run smaller/less overlap cams to make more power and have better driveability. The one you got now is a thumper, NA power making cam. Pull the charge pipe off and see what it makes NA, id bet it would make decent power (taking account the low compression). Anyway, take it with a grain of salt as I'm NOT an expert, its just from what I've observed. Good luck to ya!!!
Anyway, thanks for your input I just don't think it pertains to my set-up like it would a turbo.
#1131
9 Second Club
iTrader: (104)

IMO the cam and springs are fine (though the cam may not be ideal). Boost pressure from a supercharged car should not effect valvetrain stability. Backpressure from a turbo is another story.
Anyway, lets go through the motions on the intake valve.
Intake stroke- closed valve has 26psi of boost behind it and begins to open. Air begins to fill the cylinder and pressure between intake and cylinder begins to equalize.
valve starts closing and cylinder pressure/intake pressure should be rather close. As soon as the intake valve closes the Compression cycle starts and cylinder pressure immediately eclipses intake manifold pressure.
Power stroke, until exhaust blowdown. Cycle starts over at end of exhaust stroke during overlap.
Not really seeing any reason a supercharged engine needs more valvespring due to boost pressure, only that it extends the usable rpm range of the engine.
Anyway, lets go through the motions on the intake valve.
Intake stroke- closed valve has 26psi of boost behind it and begins to open. Air begins to fill the cylinder and pressure between intake and cylinder begins to equalize.
valve starts closing and cylinder pressure/intake pressure should be rather close. As soon as the intake valve closes the Compression cycle starts and cylinder pressure immediately eclipses intake manifold pressure.
Power stroke, until exhaust blowdown. Cycle starts over at end of exhaust stroke during overlap.
Not really seeing any reason a supercharged engine needs more valvespring due to boost pressure, only that it extends the usable rpm range of the engine.
Hmm.... What is going on during the blow down of the cylinder, before overlap? exhaust valve open, intake valve closed. 26 psi in the manifold is like 26 x Valve radius squared x 3.14 which equals effective psi working on the backside of valve, (basically trying to open the valve). If my math is correct that is another 85 pounds of pressure that is not there on a NA engine. Essentially, what this means is you need to subtract this value from your spring seat pressure, or compensate for it by setting it as the zero point when calculating closed valve spring pressures (seat pressure).
I thought this was pretty standard set-up for any blown motor??
#1132
FormerVendor

When the exhaust cycle starts the intake valve has allready been closed through compression and power cycle and is stable. You would need enough boost to push the valve off the seat on it's own at that point, which isn't happening.
On a turbo engine exhaust backpressure is a problem as it can be double intake manifold pressure. Exhaust valve can bounce when closing as intake cycle is just beginning and there is not enough pressure in the cylinder to offset exhaust backpressure.
On a turbo engine exhaust backpressure is a problem as it can be double intake manifold pressure. Exhaust valve can bounce when closing as intake cycle is just beginning and there is not enough pressure in the cylinder to offset exhaust backpressure.
#1133
8 sec potential, 12 sec slip
iTrader: (50)

As long as the spring load is greater than the load of the boost on the valve, you should be ok. Seems to me that the force of the spring > force of the boost on the valve. Therefore, valve would remain closed by my math..
I hope ya get it figured out man
I hope ya get it figured out man

#1136
10 Second Club
Thread Starter
iTrader: (37)
Join Date: Jan 2004
Posts: 1,935
Likes: 0
Received 0 Likes
on
0 Posts

Great info on the valve train guys, I love learning new stuff
Had to take the car home for a week since it's not going back on the dyno until Wednesday. It was an interesting drive home to say the least. First time driving with the new engine, first time driving it with the new blower, first time driving it with no power steering, first time driving strapped into a bucket and first time driving with a th400 ever. It was a little scary, hearing all kinds of weird noises I don't remember not to mention my head was ratteling from no cats or mufflers and I had to avoid cops any way possible. Luckly I had a short 10mile back roads drive and saw no cops and had no incidence and made it to the garage safely. It sure isn't much of a street car at this point lol. It will be a ton better when I have some mufflers on it. Plus it's not much fun to drive when your scared if you give it too much gas it might blow up lol. I krept home like a grandma
Anyway, I thought I'd finally share a vid of it running so this is how it sounds:

Had to take the car home for a week since it's not going back on the dyno until Wednesday. It was an interesting drive home to say the least. First time driving with the new engine, first time driving it with the new blower, first time driving it with no power steering, first time driving strapped into a bucket and first time driving with a th400 ever. It was a little scary, hearing all kinds of weird noises I don't remember not to mention my head was ratteling from no cats or mufflers and I had to avoid cops any way possible. Luckly I had a short 10mile back roads drive and saw no cops and had no incidence and made it to the garage safely. It sure isn't much of a street car at this point lol. It will be a ton better when I have some mufflers on it. Plus it's not much fun to drive when your scared if you give it too much gas it might blow up lol. I krept home like a grandma

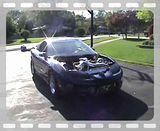
#1138
10 Second Club
Thread Starter
iTrader: (37)
Join Date: Jan 2004
Posts: 1,935
Likes: 0
Received 0 Likes
on
0 Posts

Oh yeah, about it being loud, you should of heard it on the dyno. I thought I could take it.....nope fingers went in the ears real quick. That sucker screams at wot!
#1139
10 Second Club
Thread Starter
iTrader: (37)
Join Date: Jan 2004
Posts: 1,935
Likes: 0
Received 0 Likes
on
0 Posts

I don't think I will sell it, at least I'm not trying very hard. If someone was to make me a good offer I might have to take it but I'm not planning on selling it now. It's just too exciting finally having it running again, I think I was just discouraged with the issues and I'm in need of money so it seemed like a smart thing to do lol. Worst case senario, I might just have to part out a few high dollar parts and then replace them when things get better.
#1140
9 Second Club
iTrader: (104)

When the exhaust cycle starts the intake valve has allready been closed through compression and power cycle and is stable. You would need enough boost to push the valve off the seat on it's own at that point, which isn't happening.
On a turbo engine exhaust backpressure is a problem as it can be double intake manifold pressure. Exhaust valve can bounce when closing as intake cycle is just beginning and there is not enough pressure in the cylinder to offset exhaust backpressure.
On a turbo engine exhaust backpressure is a problem as it can be double intake manifold pressure. Exhaust valve can bounce when closing as intake cycle is just beginning and there is not enough pressure in the cylinder to offset exhaust backpressure.

I would assume many on this forum don't experience these issues on their procharged LS engines because not many are using serious superchargers like rufertic (sp?) creating 26 psi. It seems most pushing it are in the 18-20 psi range. I would suggest 200+psi of seat pressure springs minimum, maybe higher, can't have too much in my opinion. Of course, I don't think I would be using a HR cam either with that kind of seat pressure, most likely a SR. The final spring selection would be based upon how aggressive the closing ramp of the intake lobe is.
Good luck with the combo, I have been following along on and off for awhile, quite a bumpy road. I think it will haul the mail when it is lined out. Glad to hear you are making headway. Seems to have the interest of many 68,XXX views!!