Driveline vibraton found. Coming from rear of transmission.
#43
Teching In
Join Date: Jan 2009
Location: Anderson, SC
Posts: 33
Likes: 0
Received 0 Likes
on
0 Posts

I tried to get 2* on each end of the driveshaft. I dont think I can get it unless I raise the tranny more which I cant dop. I already have it raised 1/2" and any more it will hit the tunnel and I am not gonna try to lower the motor to get absolute perfect. At least this is the way I see it, maybe I am still confused.
If I raise the pinion a bit, then I get the 0* angles meaning everything is in a striaght line. The numbers in the diagram are NOT the angles, they are the readings of the angle finder. If I am right, the pinion is -1.
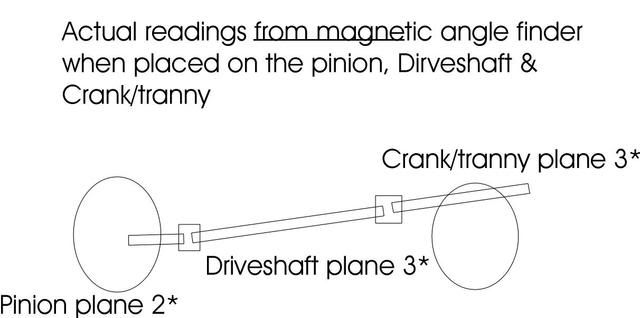
If I raise the pinion a bit, then I get the 0* angles meaning everything is in a striaght line. The numbers in the diagram are NOT the angles, they are the readings of the angle finder. If I am right, the pinion is -1.
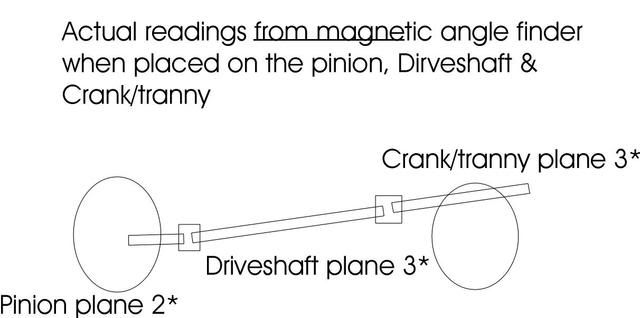
The plane of the two shafts should be the same. The vertical distance between the two planes should not result in more than a +15 degree angle of the drive shaft at the pinion shaft (looking from the right side of the car) and a -15 degree angle at the tranny tail shaft (again looking from the right side). U joints when flexed turn faster at the outside of the flex than they do on the inside. In your drawing the joint at the pinion is trying to bind up.The angle of the flex should be as close as possible at both ends of the shaft so that they offset each other and not bind up. The rear axle under load wants to twist the pinion angle up. The reason for setting the pinion angle to a -# from the horizontal plane of the two shafts is so that under load the pinion shaft returns to parallel or as close to that as you can get it.
I'm not trying to hijack your thread but do hope this helps.
#44

I spoke to some mechanical engineers today and we sketched it out. They recommended setting the pinion, DS and tranny/crank in a perfectly straight line to start off with and using the 3/4" spacer to raise the tranny a bit to account for the lower pinion offset on the 9". It would seem that doing this is a step in a better direction.
They said to lower the pinion exactly -2* like everyone has said. Once lowered, this will create about a 1* angle on the front of the DS connecting to the tranny.
The three laws of driveline angles should be satisfied:
Operating angles are within 1* of each other.
Neither angle is >3*
And each operating angle is at least .5*
I will try this next.
They said to lower the pinion exactly -2* like everyone has said. Once lowered, this will create about a 1* angle on the front of the DS connecting to the tranny.
The three laws of driveline angles should be satisfied:
Operating angles are within 1* of each other.
Neither angle is >3*
And each operating angle is at least .5*
I will try this next.
#46


Right now I am waiting a couple peiople to sit in the car to make the adjustment. According to some cocktail napkin sketches, this should do the trick. That minor vibe, if it remains will be in the DS. I talked to PST today. They think the problem might be that the rebalance was not done at high enough RPM to do the trick. Might send it to them for a final rebalance.
#50

Update, good and bad news.
I have the transmission raised 1/2" with spacers and I achieved equal driveline angles of 2.6*. Thats with the car loaded with two people. The pinion and crank/tranny are parallel with the pinion having a -2.6* angle. Sounds good to me.
The thing that was screwing me up, was the crappy gravity gage and not having driver weight simulation in the car, and of course raising the tranny helped too. The Sears digital gage helped a lot and was well worth $25.00. Get one if you are messing with driveline angles.
The remaining vibe that I have is at its least intensity after the new adjustment.
The bad news. I went to remove my driveshaft and it would not come out. The Rockland bushing was partially seized and I had to force the DS out of the tranny. I then had to cut the bushing off of the DS so now its wasted. I have no clue why this happened.
I lubed the bushing with fluid like I was told and the DS inserted into the tranny snug but not tight. It was NOT total interference fit. Maybe it should have been lubed with grease.
The bushing shows signs where it has spun in the aluminum transmission housing so I have to assume that it is now wasted. No walk bushing my ***. FAWK. The DS should be fine as far as I can tell.
If any one has a busted T56 laying around and can sell me a housing, please PM me ASAP.
Cant believe this happened, I thought I was nearly there.
You guys that are going to use the Rockland bushing, better lube it with grease and NOT tranny fluid.
I have the transmission raised 1/2" with spacers and I achieved equal driveline angles of 2.6*. Thats with the car loaded with two people. The pinion and crank/tranny are parallel with the pinion having a -2.6* angle. Sounds good to me.
The thing that was screwing me up, was the crappy gravity gage and not having driver weight simulation in the car, and of course raising the tranny helped too. The Sears digital gage helped a lot and was well worth $25.00. Get one if you are messing with driveline angles.
The remaining vibe that I have is at its least intensity after the new adjustment.
The bad news. I went to remove my driveshaft and it would not come out. The Rockland bushing was partially seized and I had to force the DS out of the tranny. I then had to cut the bushing off of the DS so now its wasted. I have no clue why this happened.
I lubed the bushing with fluid like I was told and the DS inserted into the tranny snug but not tight. It was NOT total interference fit. Maybe it should have been lubed with grease.
The bushing shows signs where it has spun in the aluminum transmission housing so I have to assume that it is now wasted. No walk bushing my ***. FAWK. The DS should be fine as far as I can tell.
If any one has a busted T56 laying around and can sell me a housing, please PM me ASAP.
Cant believe this happened, I thought I was nearly there.
You guys that are going to use the Rockland bushing, better lube it with grease and NOT tranny fluid.
#51
Banned
iTrader: (58)
Join Date: Mar 2004
Location: Leola, PA
Posts: 756
Likes: 0
Received 0 Likes
on
0 Posts

Update, good and bad news.
I have the transmission raised 1/2" with spacers and I achieved equal driveline angles of 2.6*. Thats with the car loaded with two people. The pinion and crank/tranny are parallel with the pinion having a -2.6* angle. Sounds good to me.
The thing that was screwing me up, was the crappy gravity gage and not having driver weight simulation in the car, and of course raising the tranny helped too. The Sears digital gage helped a lot and was well worth $25.00. Get one if you are messing with driveline angles.
The remaining vibe that I have is at its least intensity after the new adjustment.
The bad news. I went to remove my driveshaft and it would not come out. The Rockland bushing was partially seized and I had to force the DS out of the tranny. I then had to cut the bushing off of the DS so now its wasted. I have no clue why this happened.
I lubed the bushing with fluid like I was told and the DS inserted into the tranny snug but not tight. It was NOT total interference fit. Maybe it should have been lubed with grease.
The bushing shows signs where it has spun in the aluminum transmission housing so I have to assume that it is now wasted. No walk bushing my ***. FAWK. The DS should be fine as far as I can tell.
If any one has a busted T56 laying around and can sell me a housing, please PM me ASAP.
Cant believe this happened, I thought I was nearly there.
You guys that are going to use the Rockland bushing, better lube it with grease and NOT tranny fluid.
I have the transmission raised 1/2" with spacers and I achieved equal driveline angles of 2.6*. Thats with the car loaded with two people. The pinion and crank/tranny are parallel with the pinion having a -2.6* angle. Sounds good to me.
The thing that was screwing me up, was the crappy gravity gage and not having driver weight simulation in the car, and of course raising the tranny helped too. The Sears digital gage helped a lot and was well worth $25.00. Get one if you are messing with driveline angles.
The remaining vibe that I have is at its least intensity after the new adjustment.
The bad news. I went to remove my driveshaft and it would not come out. The Rockland bushing was partially seized and I had to force the DS out of the tranny. I then had to cut the bushing off of the DS so now its wasted. I have no clue why this happened.
I lubed the bushing with fluid like I was told and the DS inserted into the tranny snug but not tight. It was NOT total interference fit. Maybe it should have been lubed with grease.
The bushing shows signs where it has spun in the aluminum transmission housing so I have to assume that it is now wasted. No walk bushing my ***. FAWK. The DS should be fine as far as I can tell.
If any one has a busted T56 laying around and can sell me a housing, please PM me ASAP.
Cant believe this happened, I thought I was nearly there.
You guys that are going to use the Rockland bushing, better lube it with grease and NOT tranny fluid.
#52

Had it staked and loctited too. Not sure I can afford another $55.00 bushing if this is going to happen. I am going to get the housing back off ASAP and check it out. Hopefully I can get a $5.00 OE bushing to work. There are no words to describe how much this SUCKS.
I got the housing off again and the bushing barely spun. The inner bore does not appear to be damaged to require replacement of the housing, as of yet. I will drop it of at a shop today for analysis plus I am shipping the driveshaft back to Strange for a precise re-balancing.
I got the housing off again and the bushing barely spun. The inner bore does not appear to be damaged to require replacement of the housing, as of yet. I will drop it of at a shop today for analysis plus I am shipping the driveshaft back to Strange for a precise re-balancing.
Last edited by wrd1972; 01-15-2009 at 07:17 AM.
#53
TECH Addict
iTrader: (61)
Join Date: Mar 2002
Location: USA
Posts: 2,304
Likes: 0
Received 0 Likes
on
0 Posts


Couple questions:
1. When you measured the .0015" clearance, did you mic the ID of the bushing and the OD of the shaft, and then subtract the values prior to bushing install? If so, the .0015" value is actually the diametrical clearance, and the radial clearance (which is what you want & is half that value or .00075") MUCH too tight for they type/class of fit required in this application.
Plus, after the bushing is pressed into the housing the ID will be even smaller yet, reducing the clearance due to slight distortion of bushing regardless of what type mandrel is used.
2. If you measured the gap between the bushing and shaft after bushing install and got the .0015" value - that is still on the borderline of being too tight for type/class of fit required. Any amount of wobble induced by improper driveline angle, worn U-joints, or improperly balanced DS will cause the bushing to gall onto the yoke shaft regardless of type lubricant used. Once bushing galls to shaft, it will impart damage such as you saw to the yoke shaft and the bushing WILL spin in the TS housing regardless of the 'no spin' claims.
IMHO, as a Mechanical Design Engineer for 20 some odd years now, if those clearances you measured are correct, that bushing is too tight for the type/class of fit required and should not be used.
-Jay-
1. When you measured the .0015" clearance, did you mic the ID of the bushing and the OD of the shaft, and then subtract the values prior to bushing install? If so, the .0015" value is actually the diametrical clearance, and the radial clearance (which is what you want & is half that value or .00075") MUCH too tight for they type/class of fit required in this application.
Plus, after the bushing is pressed into the housing the ID will be even smaller yet, reducing the clearance due to slight distortion of bushing regardless of what type mandrel is used.
2. If you measured the gap between the bushing and shaft after bushing install and got the .0015" value - that is still on the borderline of being too tight for type/class of fit required. Any amount of wobble induced by improper driveline angle, worn U-joints, or improperly balanced DS will cause the bushing to gall onto the yoke shaft regardless of type lubricant used. Once bushing galls to shaft, it will impart damage such as you saw to the yoke shaft and the bushing WILL spin in the TS housing regardless of the 'no spin' claims.
IMHO, as a Mechanical Design Engineer for 20 some odd years now, if those clearances you measured are correct, that bushing is too tight for the type/class of fit required and should not be used.
-Jay-
#54
TECH Apprentice
iTrader: (6)
Join Date: Oct 2007
Location: Pittsburgh
Posts: 373
Likes: 0
Received 0 Likes
on
0 Posts

wow, i jsut read all that and go no definate answer from any of it lol. i have a mild pulsating whine when i am at speed. im not sure if the tunnel mount torque arm is transmitting the minor rear end harmonics to the cab, or if my pinion angle is doing this? i didnt get a chance to set my tranny angle or even check it, but my rear is set at -2 maybe -2.5
i wish i could mount a camera under there and then punch it and see just what goes on under there in the front and the back
i also had a fitment issue between the front of my driveshaft right after the yoke and my spohn tunnel mount driveshaft loop. i had to take the loop off because it fit fine at ride height, but if the car hit a bump and the rear end was bounced above normal operating height it made the ds hit the loop. something in my car is fishy..............
i wish i could mount a camera under there and then punch it and see just what goes on under there in the front and the back
i also had a fitment issue between the front of my driveshaft right after the yoke and my spohn tunnel mount driveshaft loop. i had to take the loop off because it fit fine at ride height, but if the car hit a bump and the rear end was bounced above normal operating height it made the ds hit the loop. something in my car is fishy..............
#55
TECH Apprentice
iTrader: (6)
Join Date: Oct 2007
Location: Pittsburgh
Posts: 373
Likes: 0
Received 0 Likes
on
0 Posts

now i just read about thirty threads from all over the net.
bmr says to measure the driveshaft angle, then measure the face of the rear end yoke and subtract the two numbers........example......driveshaft -6, pinion +4 = -2
this seems totally different from just reading off the rear yoke
bmr says to measure the driveshaft angle, then measure the face of the rear end yoke and subtract the two numbers........example......driveshaft -6, pinion +4 = -2
this seems totally different from just reading off the rear yoke
#56
TECH Apprentice
iTrader: (6)
Join Date: Oct 2007
Location: Pittsburgh
Posts: 373
Likes: 0
Received 0 Likes
on
0 Posts

sorry for being a post ***** but im really trying to get to the bottom of this
"Put angle finder on driveshaft, lining it up along the very bottom. Read angle = DS°
Put angle finder along flat bracket along bottom of TA. Read angle = PA°
Calculate TPA° = DS°-PA°
This value, TPA° is your pinion angle. It doesn't really matter what the actual value of DS° or TA° is, because they're dependent on the angle your car is currently jacked up to (or the angle of your floor or lift). The difference between them is the critical number."
that makes the most sense to me. this method above is also setting just by the rear end and not even worrying about the tranny.
i also read that if the angle of the ds to rear end is different than the angle of the ds to the tailshaft this will result in vibration because the two u joints are not rotating on the same angle. basically the difference in ds to rear end and ds to tail shaft have to be equal whatever the number may be.
"Put angle finder on driveshaft, lining it up along the very bottom. Read angle = DS°
Put angle finder along flat bracket along bottom of TA. Read angle = PA°
Calculate TPA° = DS°-PA°
This value, TPA° is your pinion angle. It doesn't really matter what the actual value of DS° or TA° is, because they're dependent on the angle your car is currently jacked up to (or the angle of your floor or lift). The difference between them is the critical number."
that makes the most sense to me. this method above is also setting just by the rear end and not even worrying about the tranny.
i also read that if the angle of the ds to rear end is different than the angle of the ds to the tailshaft this will result in vibration because the two u joints are not rotating on the same angle. basically the difference in ds to rear end and ds to tail shaft have to be equal whatever the number may be.
#57
#58

1. When you measured the .0015" clearance, did you mic the ID of the bushing and the OD of the shaft, and then subtract the values prior to bushing install? If so, the .0015" value is actually the diametrical clearance, and the radial clearance (which is what you want & is half that value or .00075") MUCH too tight for they type/class of fit required in this application.
Plus, after the bushing is pressed into the housing the ID will be even smaller yet, reducing the clearance due to slight distortion of bushing regardless of what type mandrel is used.
Plus, after the bushing is pressed into the housing the ID will be even smaller yet, reducing the clearance due to slight distortion of bushing regardless of what type mandrel is used.
I also sent the drive-shaft off to PST to have them properly balance it. When it cam back the one weight had been tweaked compared to other needless trips to the local guys who checked the balance. I now have total confidence that the DS is properly balanced.
I drove the car and the vibes were now gone at least up to 70 MPH. During the test drive the throw out bearing decided to explode so now I have to address that. Thankfully, the drive shaft slid out of the tranny like it should so there is not an issue with the new tailshaft bushing.
I am currently addressing the throw out bearing problem now. I am beefing it up some by tack welding the pull flange together to help ensure that this does not happen again.
Hopefully I can get more test time this weekend to determine if the vibes are actually gone and hopefully nothing else will blow up.