Just Venting
#41
TECH Veteran
iTrader: (40)

This is interesting. The "helper" I mentioned above was a friend of mine who's an MB certified professional tech, also experienced with advanced driveability diagnostics. After evaluating the situation, knowing what I'd already done and seeing what was happening under load, it was he who suggested that I should move the ground strap off of that area of the alternator.
So I guess we have multiple professionals involved in this, some with different opinions. No need for a pissing match though, I'm just glad that the problem is LONG gone - which is ultimately all that matters.
So I guess we have multiple professionals involved in this, some with different opinions. No need for a pissing match though, I'm just glad that the problem is LONG gone - which is ultimately all that matters.

GM engineered the car with that bare ground strap in that location knowing full well that it was likely to touch things.
I think we can all agree the engineers at GM with their collective pool of knowledge to pull from (over 100 years of R&D experience) trump all of our guess work.
I generally agree with everyone and try to get along here, it rubs me the wrong way when someone comes in barking about their credentials and how people should listen to them, especially when I see that member posting from a position of theory all over the board. I've hired and fired many of these guys and I've learned that anyone that forces their credentials down your throat cant seem to get even the most basic things right once you put them in the shop. Let your work do your talking for you.
And if there's any truth to his post I'm a master of this and that and this and that. You can't be a true craftsman/specialist in that many fields. That's a jack of all trades and a master of nothing, but running mouth and a big ego.
#42
LS1Tech Administrator
iTrader: (3)
Join Date: Nov 2001
Location: Schiller Park, IL Member: #317
Posts: 32,299
Likes: 0
Received 1,726 Likes
on
1,238 Posts


GM engineered the car with that bare ground strap in that location knowing full well that it was likely to touch things.
I think we can all agree the engineers at GM with their collective pool of knowledge to pull from (over 100 years of R&D experience) trump all of our guess work.
I think we can all agree the engineers at GM with their collective pool of knowledge to pull from (over 100 years of R&D experience) trump all of our guess work.
Yeah, that's exactly why I didn't mention anything about my helper being a trained and experienced career professional, and the advice originally coming from him. I didn't think credentials would matter so much since not all professionals always agree on all points anyway, nor is any one person always going to get it right. What's nice about this site is that both pros and hobbyists can share unique experience and general information which might help point someone else in the right direction.
#43
TECH Veteran
iTrader: (40)

This happened in 2005 or '06, so I don't remember the conversation word for word, but I recall that his idea was what I mentioned above; that the ground strap, when moving under load, was likely making contact with (providing ground to) something on or around the alternator that it shouldn't be. But all obvious connections and wires had already been checked on both the harness and alternator side (plus two different good alternators that presented the same issue), so if there was a marginal flaw in some other component it was too minor to be easily found and no longer an issue once the ground strap was moved.
My issue with that is that the case itself is metal and conducts electricity. It is grounded to the block, the entire case conducts and is one gigantic ground itself, and a ground wire was touching it... That is literally no different than the wire not being there at all. Unless something was awry with the wire. And i'm still waiting for jack of all trades to explain how a ground wire touching a gigantic round case that is 100% a ground itself would cause more issue than the case itself being a ground. If the ground wire being near the "electromatic field" or faraday cage or what have you would cause an issue, then the case would be an issue as well. No engineering degree needed for that logic.
I don't think that any company, no matter how big, is able or willing to account for every possible scenario of potential issues (recalls are an excellent macro illustration of such). In this case, there may have been some other minor flaw that caused the location of that ground to be an issue where it otherwise wouldn't have been. If such is the case, and if that minor flaw presents no other issues once the ground is moved, then moving the ground is effectively a solution. And if this happened on one example, it's possible that it could happen on another - which is why I posted about my issue in the first place.
Can't argue with you about there being mistakes and the recalls being the proof, however in this case it wasn't a mistake, if it were there would be issues all abound due to that wire on these cars. The rest I agree with you about.
Yeah, that's exactly why I didn't mention anything about my helper being a trained and experienced career professional, and the advice originally coming from him. I didn't think credentials would matter so much since not all professionals always agree on all points anyway, nor is any one person always going to get it right. What's nice about this site is that both pros and hobbyists can share unique experience and general information which might help point someone else in the right direction.
My issue with that is that the case itself is metal and conducts electricity. It is grounded to the block, the entire case conducts and is one gigantic ground itself, and a ground wire was touching it... That is literally no different than the wire not being there at all. Unless something was awry with the wire. And i'm still waiting for jack of all trades to explain how a ground wire touching a gigantic round case that is 100% a ground itself would cause more issue than the case itself being a ground. If the ground wire being near the "electromatic field" or faraday cage or what have you would cause an issue, then the case would be an issue as well. No engineering degree needed for that logic.
I don't think that any company, no matter how big, is able or willing to account for every possible scenario of potential issues (recalls are an excellent macro illustration of such). In this case, there may have been some other minor flaw that caused the location of that ground to be an issue where it otherwise wouldn't have been. If such is the case, and if that minor flaw presents no other issues once the ground is moved, then moving the ground is effectively a solution. And if this happened on one example, it's possible that it could happen on another - which is why I posted about my issue in the first place.
Can't argue with you about there being mistakes and the recalls being the proof, however in this case it wasn't a mistake, if it were there would be issues all abound due to that wire on these cars. The rest I agree with you about.
Yeah, that's exactly why I didn't mention anything about my helper being a trained and experienced career professional, and the advice originally coming from him. I didn't think credentials would matter so much since not all professionals always agree on all points anyway, nor is any one person always going to get it right. What's nice about this site is that both pros and hobbyists can share unique experience and general information which might help point someone else in the right direction.

#44
TECH Veteran
iTrader: (40)

By the way, y'all seen this thread? It's 8 years old and 50 pages long. Since we're tooting horns now lol.
I've have my fair share of alternator experience with F body cars.
https://ls1tech.com/forums/generatio...failure-s.html
I've have my fair share of alternator experience with F body cars.
https://ls1tech.com/forums/generatio...failure-s.html
#45
TECH Senior Member
iTrader: (96)
Join Date: Aug 2007
Location: Turnin' Wrenches Infractions: 005
Posts: 24,240
Likes: 0
Received 81 Likes
on
72 Posts


I was having issues with a TA where the ALT would light up and overcharge for a few seconds, Cost me many headlamps from the voltage surge. Before replacing anything I simply removed all the wiring from the ALT inspected them and reinstalled them with silicone grease to seal the atmosphere out from letting small amounts of moisture to react to the electrons moving through the connections that cause slight resistance in the circuits causing electronic devices to misinterpret circuit values causing charging spikes . Problem solved.



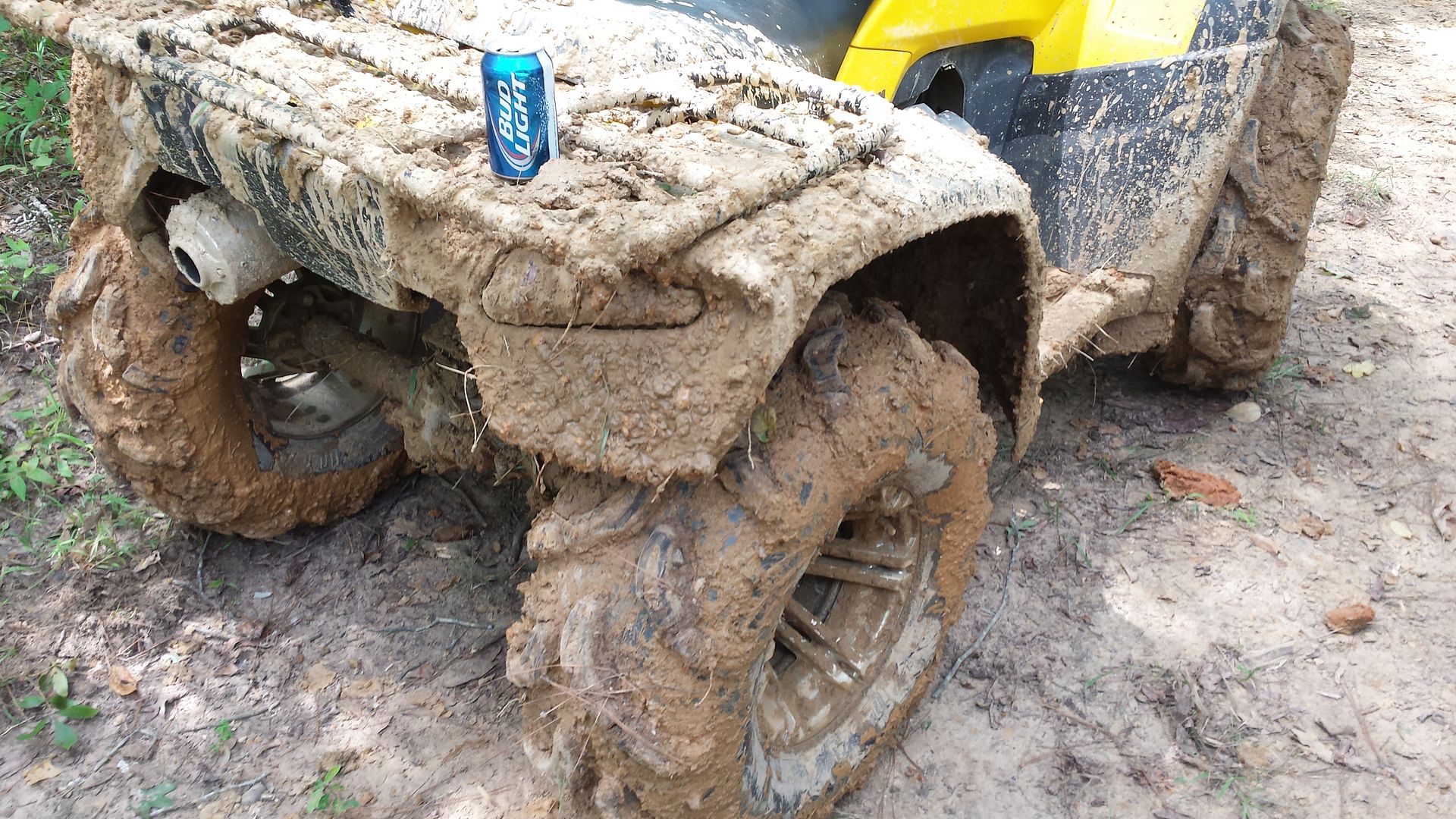
Thats a buddy, and yes its a FI bike with a PCM.
#47
TECH Veteran
iTrader: (40)

Applying silicone grease to connectors is one of the tale tale signs of a rookie "repair". I am the lead tech over 7 shops and I run 6 bays at my shop alone, plus the alignment bay (I'm actually a stand alone tech doing two people's job). When the techs at the other shops can't get things right they tow cars to me. I have one in the shop right now with silicone grease smeared all over everything and nothing fixed.
At best it's a band aid, not a repair, and it's actually just a coincidental repair because the silicone grease application isn't actually what fixed the connection. Unplugging a connector and plugging it back in causes the terminal to scrape the pin and "clean" the connection which "fixes" it. But it still needs to be lightly sanded/filed to fully resore the connection and remove build up/burning. I "fix" cars often by unplugging and re plugging connectors. When I see it makes a change I go back in and do a real repair. Whether it be replacing pins and or tabs or diamond filing them and then using a needle to return the sprung tab to it's original location to make a positive connection. There have been times I simply unplugged the connector and reconnected it and let it roll though, not gonna lie. Had countless jeeps that this worked on.
There's a reason not a single OEM manufacturer uses silicone grease in their connections, it's not needed for standard usage, bury the car under water, it could help. But otherwise the multi rib seals they use work damn well for sealing out water and moisture. They even work quite well against the power washer I use at work all the time (I don't hold it down directly on the connector but they do experience a good blast of pressure).
At best it's a band aid, not a repair, and it's actually just a coincidental repair because the silicone grease application isn't actually what fixed the connection. Unplugging a connector and plugging it back in causes the terminal to scrape the pin and "clean" the connection which "fixes" it. But it still needs to be lightly sanded/filed to fully resore the connection and remove build up/burning. I "fix" cars often by unplugging and re plugging connectors. When I see it makes a change I go back in and do a real repair. Whether it be replacing pins and or tabs or diamond filing them and then using a needle to return the sprung tab to it's original location to make a positive connection. There have been times I simply unplugged the connector and reconnected it and let it roll though, not gonna lie. Had countless jeeps that this worked on.
There's a reason not a single OEM manufacturer uses silicone grease in their connections, it's not needed for standard usage, bury the car under water, it could help. But otherwise the multi rib seals they use work damn well for sealing out water and moisture. They even work quite well against the power washer I use at work all the time (I don't hold it down directly on the connector but they do experience a good blast of pressure).
Last edited by 00pooterSS; 01-01-2018 at 07:58 PM.
#48
TECH Veteran
iTrader: (40)

You can always tell when someone uses a lot of big words to sound smart and when they actually know what they're doing. Electrons in the atmosphere moving across the solar planes into the megasphere crawled into my analshpere and my voltotron spark capacitor returned to it's normal state of transfunction!!!
#49
TECH Veteran
iTrader: (40)

RockinWS6 Your description of it sealing out "moisture in the air" is absolutely retarded. Electricity follows the path of least resistance. In your connector you have direct metal to metal contact and "moisture in the air", the electricity will flow through the pins. However, if there is solid water in there, it will cause some light shorting, but metal is a better conductor than water, so your moisture explanation doesn't hold... water. Again, I thought you were an electrical engineer?? If moisture in the air shorted out connections every house and business in the world would go down on a humid day.
Ever washed an engine off with a water hose and got water on the battery? Why didn't it short out??
By the way I've experienced this. I did a repair on a vehicle recently that the customer had backed the rear of the car into the ocean water numerous times over a couple of years and most of the connections in the rear of the car were completely full of water. And for the most part, the car functioned as normal. I would have periodic raises and spikes in the 5 volt reference though.
http://www.ellsworth.com.my/news/sil...onegrease.html
Ever washed an engine off with a water hose and got water on the battery? Why didn't it short out??
By the way I've experienced this. I did a repair on a vehicle recently that the customer had backed the rear of the car into the ocean water numerous times over a couple of years and most of the connections in the rear of the car were completely full of water. And for the most part, the car functioned as normal. I would have periodic raises and spikes in the 5 volt reference though.
http://www.ellsworth.com.my/news/sil...onegrease.html
Last edited by 00pooterSS; 01-01-2018 at 08:00 PM.
#50
FormerVendor
iTrader: (1)
Join Date: Nov 2008
Location: Santa Ana, CA. USA
Posts: 2,157
Likes: 0
Received 17 Likes
on
17 Posts


Hi WS-6 & Reda, I have customers who race in the BAJA with FOUR INCHES THICK of MUD (witnessed) covering every part of the car/driver caused WHEN the "locals" aka FARMERS flood THEIR FIELDS. (reference to your ATV picture)
THUS Silicon Grease "saves the day".
Next as an EE (WS-6), you would agree there are TWO types of Grounds, the Power Ground AND the High Frequency Ground.
This IS the MAIN REASON the PCMs are connected to the Battery Negative.
Most here agree that current flow is from atom/atom in the solid copper.
Few here understand the HF "noise" current flows on the outside of the copper.
Air is a great conductor, known by those who make current flow.
When I invented modern DIS in 1984, I wrote a paper about HF Grounds holding MORE true to this day as the noise frequencies are increased.
EXAMPLE : A new GM car has the Sound System "upgraded" by a Audio Shop. The car will not run correctly at times or not at all with cause found of the EMI (speaker current) causing changes within the CAN signals.
I have Marine/Air Boat ECU customers that REQUIRE placement of a Non-Conductive Grease to keep SEALED connectors from internal damage.
My OWN Escalade 2007 required a Spark Plug Change with 40K miles, a CA car, with four Spark Plug Boots remaining attached to the Sparkplug. (damaging boots, cause no grease)
There is another difference, I work more in the Professional Motorsport area.
Lance
THUS Silicon Grease "saves the day".
Next as an EE (WS-6), you would agree there are TWO types of Grounds, the Power Ground AND the High Frequency Ground.
This IS the MAIN REASON the PCMs are connected to the Battery Negative.
Most here agree that current flow is from atom/atom in the solid copper.
Few here understand the HF "noise" current flows on the outside of the copper.
Air is a great conductor, known by those who make current flow.
When I invented modern DIS in 1984, I wrote a paper about HF Grounds holding MORE true to this day as the noise frequencies are increased.
EXAMPLE : A new GM car has the Sound System "upgraded" by a Audio Shop. The car will not run correctly at times or not at all with cause found of the EMI (speaker current) causing changes within the CAN signals.
I have Marine/Air Boat ECU customers that REQUIRE placement of a Non-Conductive Grease to keep SEALED connectors from internal damage.
My OWN Escalade 2007 required a Spark Plug Change with 40K miles, a CA car, with four Spark Plug Boots remaining attached to the Sparkplug. (damaging boots, cause no grease)
There is another difference, I work more in the Professional Motorsport area.
Lance