Problems with Harland Sharp stock rockers pics inside
#1
9 Second Club
Thread Starter
iTrader: (23)
Join Date: Oct 2002
Location: Mastic Long Island N.Y.
Posts: 1,150
Likes: 0
Received 0 Likes
on
0 Posts


I got a set of rockers off a member here and first and foremost want to state he has every intention of making good on the transaction. With that said he asked me to post pics and this thread to see if anybody else has had issues and also as an informative thread. As some of you guys are aware Harland Sharp offers a kit that replaces the stock bearing assembly on our LS series rockers.

it comes with a new set of bearings,a center shaft that they ride on washers,endclips, and bolts.
It seems this set did not hold up very well. In the pics below you can see I illustrate the areas where the bearing rollers really did a number on the shaft beating the surface up bad.
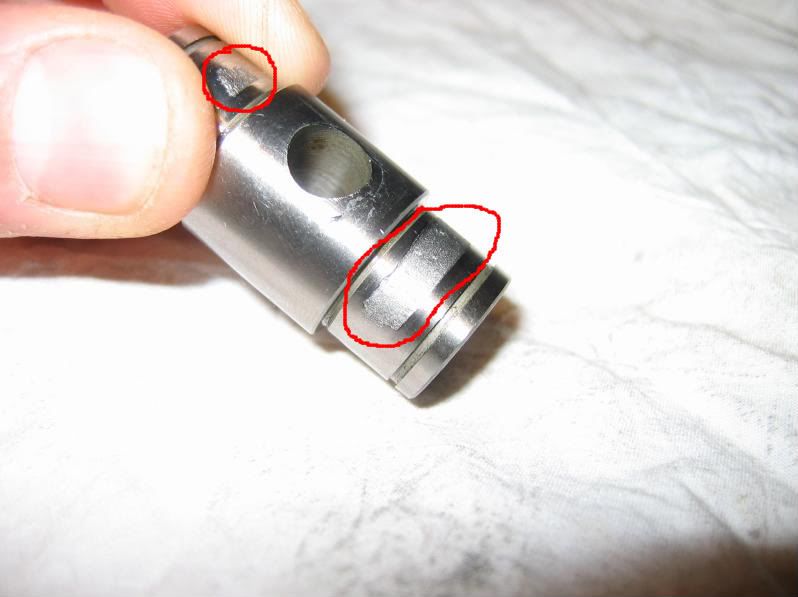
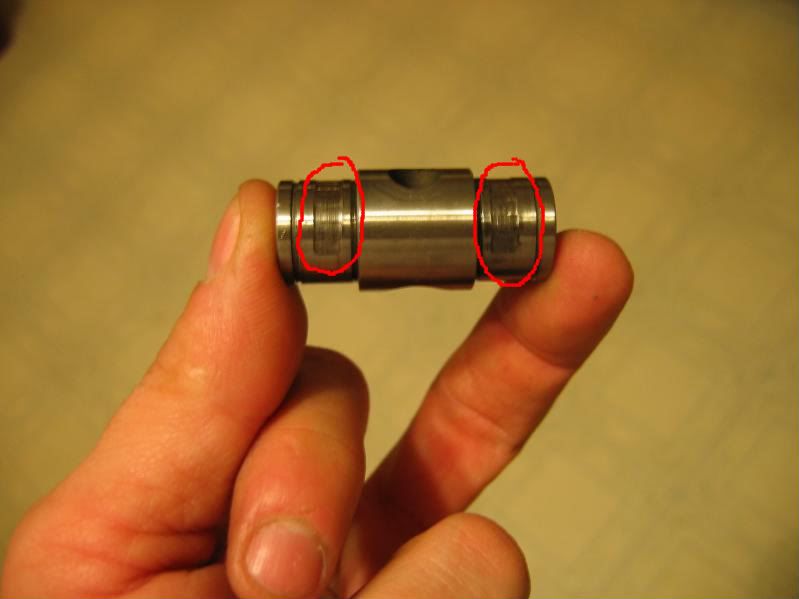
Obviously the bearing failed only the bottom half of the shafts got scored as this is where all of the pressure and forces are seen. The top halfs are fine. The bearings were coming apart. As you can see in the pic below the bearings jacket is thinner on the bottom than on the top again from all the pressure and force applied to the bottom half of the unit.
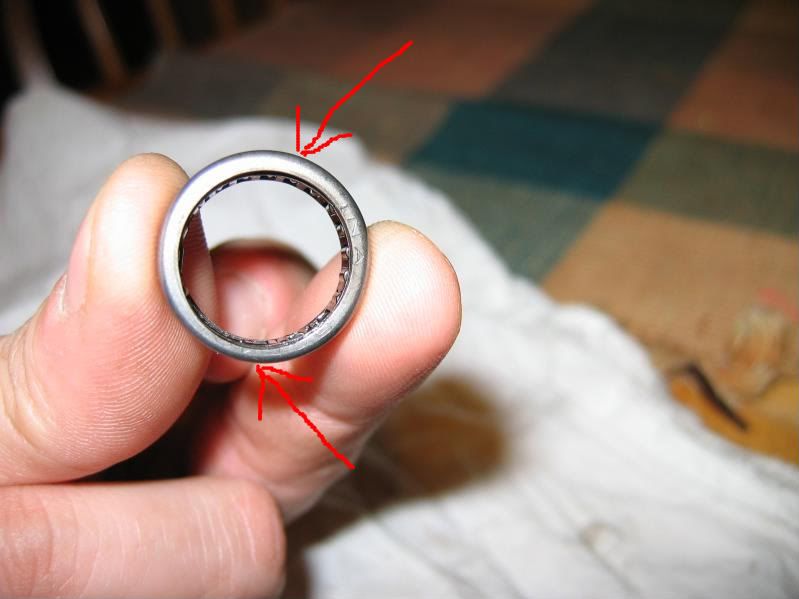
This may very well be an isolated case. I am sure Harland Sharp will be contaced about this as it is without question a problem and unacceptable. Half of the rocker arms are like this.

it comes with a new set of bearings,a center shaft that they ride on washers,endclips, and bolts.
It seems this set did not hold up very well. In the pics below you can see I illustrate the areas where the bearing rollers really did a number on the shaft beating the surface up bad.
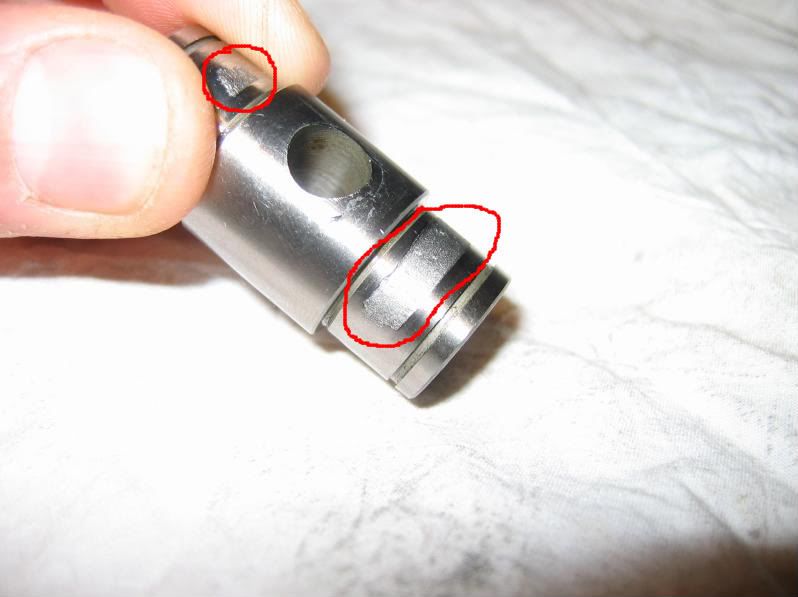
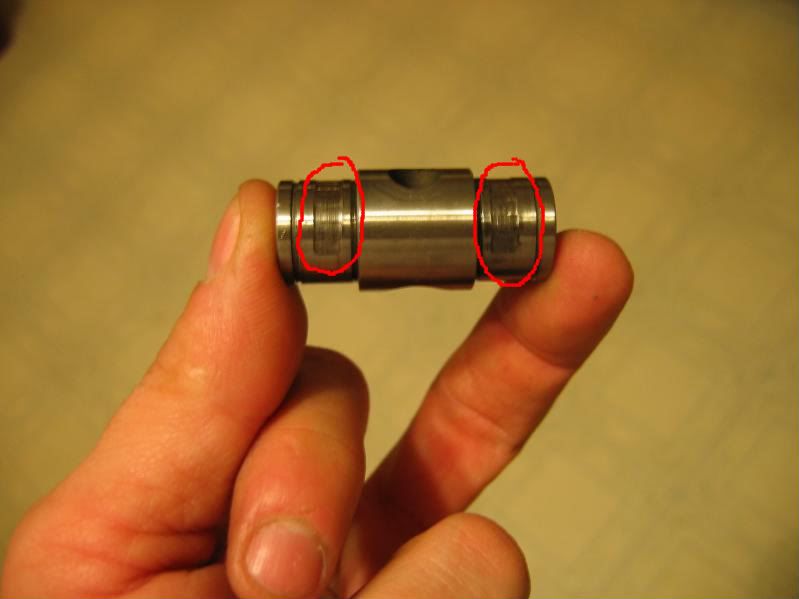
Obviously the bearing failed only the bottom half of the shafts got scored as this is where all of the pressure and forces are seen. The top halfs are fine. The bearings were coming apart. As you can see in the pic below the bearings jacket is thinner on the bottom than on the top again from all the pressure and force applied to the bottom half of the unit.
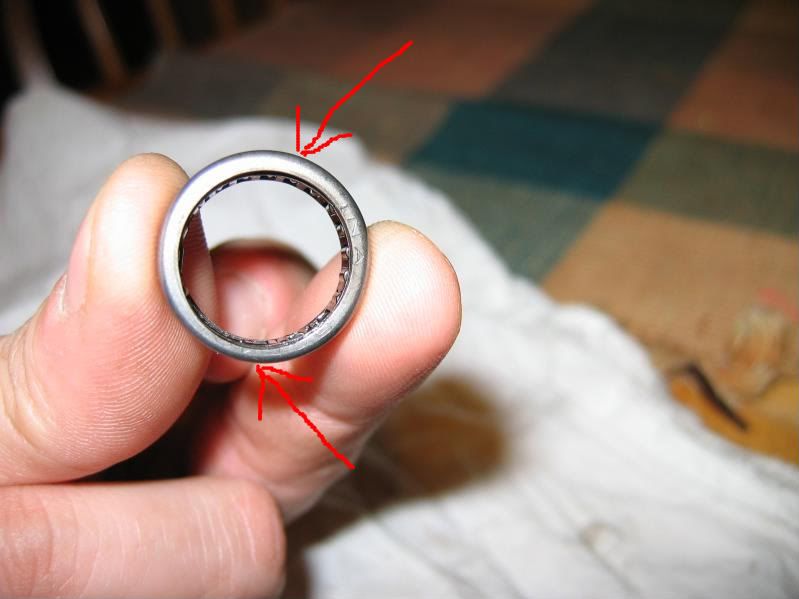
This may very well be an isolated case. I am sure Harland Sharp will be contaced about this as it is without question a problem and unacceptable. Half of the rocker arms are like this.
#3
9 Second Club
Thread Starter
iTrader: (23)
Join Date: Oct 2002
Location: Mastic Long Island N.Y.
Posts: 1,150
Likes: 0
Received 0 Likes
on
0 Posts


I was VERY suprised to see this as well. Now I dont know how much milage was on them what kinda spring pressures these saw,cam lift etc. Even with all that said these rockers had a great reputation for a nice affordable alternative to a more expensive rocker arm that sometimes create more problems and dont work as well as the stockers do.
#4
9 Second Club
Thread Starter
iTrader: (23)
Join Date: Oct 2002
Location: Mastic Long Island N.Y.
Posts: 1,150
Likes: 0
Received 0 Likes
on
0 Posts


heres an update. I spoke with a rep from HS that was very helpfull. He did admit a problem with SOME of the early run units. The bearing choice had to be changed becuase of this. It seemed to me like he would be willing to help out. The guy I bought them from is the original purchaser and will needto deal with them. In the meantime the member issued me a prompt refund. Nice to see members here doing the right thing.
#6
TECH Fanatic

I agree that it's either a hardness or DEPTH of hardness issue.
JFM-jr, try to cut the metal with a file. If it doesn't cut on the unworn surface, but does on the worn area, the depth of the hardness was probably too little. If the flat side of a file cuts into the unworn surface opposite the worn area instead of just sliding across it, the whole trunnion end part is probably too soft.
Heat treating quality control can be a problem anytime. Most manufacturers do not heat treat in house. That's why many people perform a destructive (cut apart and measure) test on each batch of parts. I'm not sure how HS heat treats the trunions, but they could be induction hardened only on the ends where the bearings roll, or they could be case hardened all over. It mght be interesting to check this. Try the file test on the large center diameter which is not a rubbing/wear surface. If it is soft enough to cut with a file and the bearing trunnions are not, there was selective heat treating done.
I'm sure HS will stand behind their products. Keep us all informed as to how it progresses.
Good luck.
Jon
Trending Topics
#9
9 Second Club
Thread Starter
iTrader: (23)
Join Date: Oct 2002
Location: Mastic Long Island N.Y.
Posts: 1,150
Likes: 0
Received 0 Likes
on
0 Posts


I was told the bearings they now use are different. Not sure on production dates he did say that not all of them had problems still plenty out there going strong. SS tried the file test seems pretty hard to me file glides off it. Did not matter where I tried it seemed the same as when I did it on the lock shackle of a Kryptonite lock. Even so Looks like a hardness battle took place and the trunions lost to the bearing rollers. I am going to call HS back tomorrow as I purchased a 2nd set of brand new units go figure..... HS said they would replace them if they were the older style bearing I got them today and they are the same as the ones in the pics above. Obviously I am not running these in my motor. So far HS seems to be on point with customer service I will discuss the hardness issue with them tomorrow and report back.
#11
9 Second Club
Thread Starter
iTrader: (23)
Join Date: Oct 2002
Location: Mastic Long Island N.Y.
Posts: 1,150
Likes: 0
Received 0 Likes
on
0 Posts


Customer service thus far has been excellent no complaints there thats for certain. This is not an isolated instance as I was told there were issues with other sets. No harm no foul they are standing behind it I will keep this thread updated.
#12
9 Second Club
Thread Starter
iTrader: (23)
Join Date: Oct 2002
Location: Mastic Long Island N.Y.
Posts: 1,150
Likes: 0
Received 0 Likes
on
0 Posts


Spoke with the tech there again today super informative guy. He explained that for the last 4 years or so they have been using a trunion made from 52100 that are minumum 60-65 Rockwell. The older trunions (wich the ones pictured may very well be) are 8620 wich is not as hard. After the trunion material change the bearings were also changed. The older bearings (wich I am postive are the ones in the pictures) were a caged design. This results in smaller rollers and less surface area for contact. The newer bearings have much bigger rollers and results in more surface area for bearing contact and less overall wear. He said he has not had a set come back to him since these changes due to failure but that does not mean it cant happen. With the conditions we put these parts in nothing is indestructable is what I took away from that and I fully agree. In a nutshell thats the story. I sent back the new set and he said they will gladly swap them out for a newly eqpt set and I could not ask for any better from a company. I was NOT the original purchaser they are brand new in the package but lets face it there are companies out there that would not be as willing to help as these guys.
#13
TECH Fanatic

Spoke with the tech there again today super informative guy. He explained that for the last 4 years or so they have been using a trunion made from 52100 that are minumum 60-65 Rockwell. The older trunions (wich the ones pictured may very well be) are 8620 wich is not as hard. After the trunion material change the bearings were also changed. The older bearings (wich I am postive are the ones in the pictures) were a caged design. This results in smaller rollers and less surface area for contact. The newer bearings have much bigger rollers and results in more surface area for bearing contact and less overall wear. He said he has not had a set come back to him since these changes due to failure but that does not mean it cant happen. With the conditions we put these parts in nothing is indestructable is what I took away from that and I fully agree. In a nutshell thats the story. I sent back the new set and he said they will gladly swap them out for a newly eqpt set and I could not ask for any better from a company. I was NOT the original purchaser they are brand new in the package but lets face it there are companies out there that would not be as willing to help as these guys.
Either could be improperly heat treated and end up with a lower hardness. It gets more complex, however:
If the 52100 was selectively hardened in the bearing area only, which would be a good idea, that would be done by induction hardening. The result would be a hard surface and a gradual decrease in hardness to the tough core. If the induction heating was not done properly or for a long enough time (seconds, not minutes nor hours), the depth of harnesss might be too shallow. Some material is (ground) off the trunnions after heat treating, and if the depth of hardness was shallow the hardest part would be removed (typically about .005) and the surface might be below HRC 60 and the hardness would drop below HRC 50 before you got too much deeper into the part.
The same thing could happen with 8620 if it wasn't left in the carburizing furnace long enough, like 10++ hours. The depth the carbon penetrates 8620 drops off rapidly with time. IOW, 10 hours might only give twice as much depth as 2-3 hours.
One other problem for either material could be too much stock removal after heat treating if the pre-heat treat diameter was machined too large. In this case you would grind deeper into the case.
If the case depth and/or surface hardness were marginal, and the blank diameter was big, the combination could have caused the problem. I have seen such things happen. Surface harndess and effective case depth could have been right on the low limit after heat treating, and the blank could have been a tad oversize and when all of this happens at one time,you just fell into the Bermuda Triangle of making heat treated parts.
FWIW, the industry standard for the needles is thru-hardened 52100. The full complement (no cage) does help a lot spreading out the load.
This is just one possible explanation, and probably more than you wanted to know. I do see how it could happen.
My $.02
Jon
#14
11 Second Club
iTrader: (19)

Either 52100, a direct-hardening bearing steel or 8620 a carburizing bearing steel can be heat treated to HRC 60-65. The 8620 needs to be carburized (carbon added to some depth) to produce the hard "case". 52100 alreeady has enough carbon to be direct hardened.
Either could be improperly heat treated and end up with a lower hardness. It gets more complex, however:
If the 52100 was selectively hardened in the bearing area only, which would be a good idea, that would be done by induction hardening. The result would be a hard surface and a gradual decrease in hardness to the tough core. If the induction heating was not done properly or for a long enough time (seconds, not minutes nor hours), the depth of harnesss might be too shallow. Some material is (ground) off the trunnions after heat treating, and if the depth of hardness was shallow the hardest part would be removed (typically about .005) and the surface might be below HRC 60 and the hardness would drop below HRC 50 before you got too much deeper into the part.
The same thing could happen with 8620 if it wasn't left in the carburizing furnace long enough, like 10++ hours. The depth the carbon penetrates 8620 drops off rapidly with time. IOW, 10 hours might only give twice as much depth as 2-3 hours.
One other problem for either material could be too much stock removal after heat treating if the pre-heat treat diameter was machined too large. In this case you would grind deeper into the case.
If the case depth and/or surface hardness were marginal, and the blank diameter was big, the combination could have caused the problem. I have seen such things happen. Surface harndess and effective case depth could have been right on the low limit after heat treating, and the blank could have been a tad oversize and when all of this happens at one time,you just fell into the Bermuda Triangle of making heat treated parts.
FWIW, the industry standard for the needles is thru-hardened 52100. The full complement (no cage) does help a lot spreading out the load.
This is just one possible explanation, and probably more than you wanted to know. I do see how it could happen.
My $.02
Jon
Either could be improperly heat treated and end up with a lower hardness. It gets more complex, however:
If the 52100 was selectively hardened in the bearing area only, which would be a good idea, that would be done by induction hardening. The result would be a hard surface and a gradual decrease in hardness to the tough core. If the induction heating was not done properly or for a long enough time (seconds, not minutes nor hours), the depth of harnesss might be too shallow. Some material is (ground) off the trunnions after heat treating, and if the depth of hardness was shallow the hardest part would be removed (typically about .005) and the surface might be below HRC 60 and the hardness would drop below HRC 50 before you got too much deeper into the part.
The same thing could happen with 8620 if it wasn't left in the carburizing furnace long enough, like 10++ hours. The depth the carbon penetrates 8620 drops off rapidly with time. IOW, 10 hours might only give twice as much depth as 2-3 hours.
One other problem for either material could be too much stock removal after heat treating if the pre-heat treat diameter was machined too large. In this case you would grind deeper into the case.
If the case depth and/or surface hardness were marginal, and the blank diameter was big, the combination could have caused the problem. I have seen such things happen. Surface harndess and effective case depth could have been right on the low limit after heat treating, and the blank could have been a tad oversize and when all of this happens at one time,you just fell into the Bermuda Triangle of making heat treated parts.
FWIW, the industry standard for the needles is thru-hardened 52100. The full complement (no cage) does help a lot spreading out the load.
This is just one possible explanation, and probably more than you wanted to know. I do see how it could happen.
My $.02
Jon
#17
TECH Enthusiast
iTrader: (21)
Join Date: Jul 2006
Location: Tellico Plains, TN
Posts: 609
Likes: 0
Received 0 Likes
on
0 Posts

Means either type of steel could be used. Just the hardening process is different. FWIW, the HRC spec of 60-65 is the same hardness spec that's used in a lot rack bars that go in the rack and pinion setup steering in your car. I work in the quality lab at a rack and pinion company and what we do to check the case depth, or depth to which it's been hardened, is take a finished piece that we did the HRC testing on and cut key areas. In this case it would be the area that the bearing rides on. We then smooth it up with progressive rates of sand paper and, once smooth, put on 3% nitrile acid on it and measure under a micro scope. This way we can ensure that the hardening process isn't going to deep or shallow. Hope this helps!
#18
TECH Fanatic

Means either type of steel could be used. Just the hardening process is different. FWIW, the HRC spec of 60-65 is the same hardness spec that's used in a lot rack bars that go in the rack and pinion setup steering in your car. I work in the quality lab at a rack and pinion company and what we do to check the case depth, or depth to which it's been hardened, is take a finished piece that we did the HRC testing on and cut key areas. In this case it would be the area that the bearing rides on. We then smooth it up with progressive rates of sand paper and, once smooth, put on 3% nitrile acid on it and measure under a micro scope. This way we can ensure that the hardening process isn't going to deep or shallow. Hope this helps!
Excellent explanation! Perhaps whoever heat treated the "bad" trunnions failed to do the "micro".
RZRSEDGE, do you check effective case depth? We usually define that where the hardness drops to HRC 50.
Jon
#19
TECH Enthusiast
iTrader: (21)
Join Date: Jul 2006
Location: Tellico Plains, TN
Posts: 609
Likes: 0
Received 0 Likes
on
0 Posts

Thanks! We do on some of the pinions we produce. We have a little different procedure for checking them, aka pain in the but.
Last edited by RZRSEDGE; 03-14-2009 at 05:24 PM. Reason: clarification