3/8 Pushrod Clearance on Unmilled 243
#21
On The Tree
Thread Starter
iTrader: (7)
Join Date: Jun 2012
Location: San Diego
Posts: 140
Likes: 0
Received 0 Likes
on
0 Posts

According to Comp there .105" wall 5/16 pushrod is 17% stiffer than the .080 wall .
http://www.compperformancegroupstore...e=GEN3Pushrods
http://www.compperformancegroupstore...e=GEN3Pushrods
You want larger dia. rather than wall thickness
11/32 .120" is about 50% stiffer than 5/15 .080" from what i research and of course 3/8th was even more stiffer than and so on
#22
TECH Senior Member
iTrader: (4)

I posted this originally on another forum and will re-post original here. I had to split it into two since there is a word limitation on ls1tech per post.
---------------------------------------------------------------------------------------------
A few guys have asked why I went through all of this, after all the car ran great with the 5/16" OD 0.080" wall pushrods. There are three answers. First, all of the Spintron testing I have read about on the LS1 series of motors conclude the pushrods are too flexible. Second, I wanted to minimize the risk that I would have long term problems with my motor. Lets face it, GM spends countless hours testing to ensure our stock motors will last a long time. I am hoping this change will extend the life of my modified motor over what it would have been with the smaller pushrods. Finally, I just like messing with the motor
As part of my heads and cam installation last fall, my original plans were to install Manton 11/32” OD pushrods to reduce pushrod flex and maximize valve motion. Any pushrod flex can reduce the valve lift but can also have other consequences such as lofting of the lifter or valve bounce. While pushrod length is a major contributor to pushrod flex, the inertial properties are the only things that you have control of since the length is dictated by the installation setup. The inertial properties are controlled by the OD and ID of the pushrod but it is the OD that will result in the largest net change.
My AFR heads were not modified for running a straight 3/8” OD pushrod prior to installation. Since the motor is together and running well, about the last thing I wanted to do was take it apart again to machine the heads for larger pushrods. However, I did want to ensure I had the most stable valve train I could get and this includes pushrod stiffness and well as correct rocker geometry and lifter preload. Knowing I couldn’t put a straight 3/8” OD pushrod in the motor, I was left with a couple of choices. First, I could use 5/16” OD pushrods with a thicker wall. The net result is a minimal gain in stiffness with a gain in weight, not a good trade-off. The second option was to increase the OD to 11/32”, which are available from Terry Manton who custom fabricates to any length and his turn-around is quick and prices are reasonable. My third choice was a tapered pushrod, specifically a double taper. A double taper design would ensure the pushrod is near the 5/16” OD where it passes through the head just under the rocker arm, which coincidentally is where the most lateral motion takes place due to the motion of the rocker arm. The double tapered pushrod provides maximum OD in the middle where the maximum lateral bending displacement will occur. Finally, a double tapered pushrod doesn’t forfeit much stiffness for the lower weight involved as compared to a same straight pushrod of the same OD and thickness.
I contacted John at Trend pushrods and spoke to him on several occasions while deciding which direction I wanted to go with my setup. The 3/8”-5/16” double tapered pushrods come in two wall thicknesses from Trend. The first is a 0.080” wall, which when tapered leaves a thinner ball end on the pushrod, which is a formed end. The second option was a 0.135” wall thickness, which are available in any custom length and are CNC machined including the ball ends. After speaking with John, I spent some time on the computer to review my options to make what I hoped would be a good trade-off and informed decision. Plus it was fun.
I ended up building a number of models of each pushrod option and examining the stiffness and weight in order to figure out my best option. Based on my required length of 7.475”, I came up with the following based on the first bending harmonic of each pushrod. The first bending harmonic provides a good initial indication of stiffness but it does not directly provide a stiffness value. These are comparisons to the 5/16” – 0.080” wall thickness baseline pushrod that I was running (as are most here on the forum who run aftermarket cams).
All percentages are measured compared to the first harmonic of a 5/16” – 0.080” wall pushrod:
11/32”, 0.120” wall: 5% greater
3/8”, 0.080” wall: 23% greater
3/8”, 0.135” wall: 13% greater
3/8”-5/16”, 0.080” wall, double tapered: 33% greater
3/8”-5/16”, 0.135” wall, double tapered: 17% greater
One would expect that the 11/32” OD pushrod would be quite a bit stiffer then the 5/16” OD pushrod, and it is. The problem is the harmonic calculations also include the weight of the pushrod so the additional weight provided by the larger OD and thicker wall result in what appears to be a minimal gain in stiffness, which is not the case since the first harmonic is being used as the basis of comparison. As a result, I modified all the pushrod models so they weighed the same and then computed the stiffness from the first bending response. The results for the straight pushrods were then compared to closed form solutions to verify the results.
11/32”, 0.120” wall: 59% greater
3/8”, 0.080” wall: 92% greater
3/8”, 0.135” wall: 122% greater
3/8”-5/16”, 0.080” wall, double tapered: 72% greater
3/8”-5/16”, 0.135” wall, double tapered: 97% greater
These results are a bit more telling and a better reflection of the relative pushrod stiffness. Simply switching to the 11/32”, 0.120” wall pushrod provides a substantial gain in pushrod stiffness and from what I have been told by a number of people running them, they fit most any head including GM without modifications. As expected, the 3/8”, 0.135” wall pushrod is the stiffest of those examined. The 3/8”-5/16”, 0.135” wall double tapered the second stiffest of the group but when compared to the 3/8”, 0.135” wall straight pushrod is 18% less weight. The 3/8”-5/16”, 0.135” wall double tapered is actually the same weight as the 11/32”, 0.120” wall pushrod while providing markedly better stiffness.
---------------------------------------------------------------------------------------------
A few guys have asked why I went through all of this, after all the car ran great with the 5/16" OD 0.080" wall pushrods. There are three answers. First, all of the Spintron testing I have read about on the LS1 series of motors conclude the pushrods are too flexible. Second, I wanted to minimize the risk that I would have long term problems with my motor. Lets face it, GM spends countless hours testing to ensure our stock motors will last a long time. I am hoping this change will extend the life of my modified motor over what it would have been with the smaller pushrods. Finally, I just like messing with the motor

As part of my heads and cam installation last fall, my original plans were to install Manton 11/32” OD pushrods to reduce pushrod flex and maximize valve motion. Any pushrod flex can reduce the valve lift but can also have other consequences such as lofting of the lifter or valve bounce. While pushrod length is a major contributor to pushrod flex, the inertial properties are the only things that you have control of since the length is dictated by the installation setup. The inertial properties are controlled by the OD and ID of the pushrod but it is the OD that will result in the largest net change.
My AFR heads were not modified for running a straight 3/8” OD pushrod prior to installation. Since the motor is together and running well, about the last thing I wanted to do was take it apart again to machine the heads for larger pushrods. However, I did want to ensure I had the most stable valve train I could get and this includes pushrod stiffness and well as correct rocker geometry and lifter preload. Knowing I couldn’t put a straight 3/8” OD pushrod in the motor, I was left with a couple of choices. First, I could use 5/16” OD pushrods with a thicker wall. The net result is a minimal gain in stiffness with a gain in weight, not a good trade-off. The second option was to increase the OD to 11/32”, which are available from Terry Manton who custom fabricates to any length and his turn-around is quick and prices are reasonable. My third choice was a tapered pushrod, specifically a double taper. A double taper design would ensure the pushrod is near the 5/16” OD where it passes through the head just under the rocker arm, which coincidentally is where the most lateral motion takes place due to the motion of the rocker arm. The double tapered pushrod provides maximum OD in the middle where the maximum lateral bending displacement will occur. Finally, a double tapered pushrod doesn’t forfeit much stiffness for the lower weight involved as compared to a same straight pushrod of the same OD and thickness.
I contacted John at Trend pushrods and spoke to him on several occasions while deciding which direction I wanted to go with my setup. The 3/8”-5/16” double tapered pushrods come in two wall thicknesses from Trend. The first is a 0.080” wall, which when tapered leaves a thinner ball end on the pushrod, which is a formed end. The second option was a 0.135” wall thickness, which are available in any custom length and are CNC machined including the ball ends. After speaking with John, I spent some time on the computer to review my options to make what I hoped would be a good trade-off and informed decision. Plus it was fun.

I ended up building a number of models of each pushrod option and examining the stiffness and weight in order to figure out my best option. Based on my required length of 7.475”, I came up with the following based on the first bending harmonic of each pushrod. The first bending harmonic provides a good initial indication of stiffness but it does not directly provide a stiffness value. These are comparisons to the 5/16” – 0.080” wall thickness baseline pushrod that I was running (as are most here on the forum who run aftermarket cams).
All percentages are measured compared to the first harmonic of a 5/16” – 0.080” wall pushrod:
11/32”, 0.120” wall: 5% greater
3/8”, 0.080” wall: 23% greater
3/8”, 0.135” wall: 13% greater
3/8”-5/16”, 0.080” wall, double tapered: 33% greater
3/8”-5/16”, 0.135” wall, double tapered: 17% greater
One would expect that the 11/32” OD pushrod would be quite a bit stiffer then the 5/16” OD pushrod, and it is. The problem is the harmonic calculations also include the weight of the pushrod so the additional weight provided by the larger OD and thicker wall result in what appears to be a minimal gain in stiffness, which is not the case since the first harmonic is being used as the basis of comparison. As a result, I modified all the pushrod models so they weighed the same and then computed the stiffness from the first bending response. The results for the straight pushrods were then compared to closed form solutions to verify the results.
11/32”, 0.120” wall: 59% greater
3/8”, 0.080” wall: 92% greater
3/8”, 0.135” wall: 122% greater
3/8”-5/16”, 0.080” wall, double tapered: 72% greater
3/8”-5/16”, 0.135” wall, double tapered: 97% greater
These results are a bit more telling and a better reflection of the relative pushrod stiffness. Simply switching to the 11/32”, 0.120” wall pushrod provides a substantial gain in pushrod stiffness and from what I have been told by a number of people running them, they fit most any head including GM without modifications. As expected, the 3/8”, 0.135” wall pushrod is the stiffest of those examined. The 3/8”-5/16”, 0.135” wall double tapered the second stiffest of the group but when compared to the 3/8”, 0.135” wall straight pushrod is 18% less weight. The 3/8”-5/16”, 0.135” wall double tapered is actually the same weight as the 11/32”, 0.120” wall pushrod while providing markedly better stiffness.
#23
TECH Senior Member
iTrader: (4)

2nd half of post.
-------------------------------------------------------------------------------------------
Based on all of the above, I called Trend pushrod and spoke to John one last time to obtain length tolerance information and some specifics prior to ordering. Trend holds their pushrod length to +/- 0.005”. In the end I ordered the Trend 3/8”-5/16”, 0.135” wall, double tapered pushrods seen in the photo below. It is hard to see in the photo but the ball ends are fully CNC machined plus they have the 210 degree ball rather then the formed ball end on a standard aftermarket pushrod (note the stock pushrods have a 210 degree ball end). The second photo shows a comparison between the double tapered pushrods and the straight 5/16”, 0.080” wall pushrods they replaced (also made by Trend).
3/8”-5/16” Double Taper Trend Pushrods
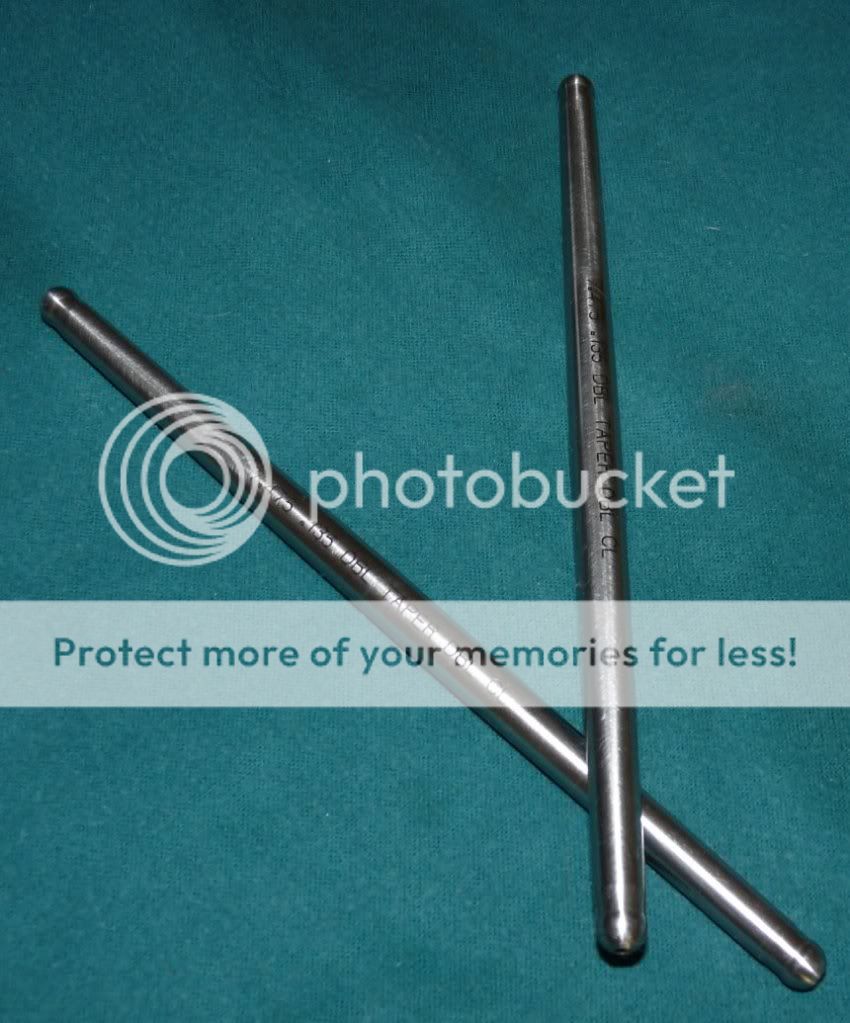
Comparison to 5/16”, 0.080” Wall Straight Pushrod
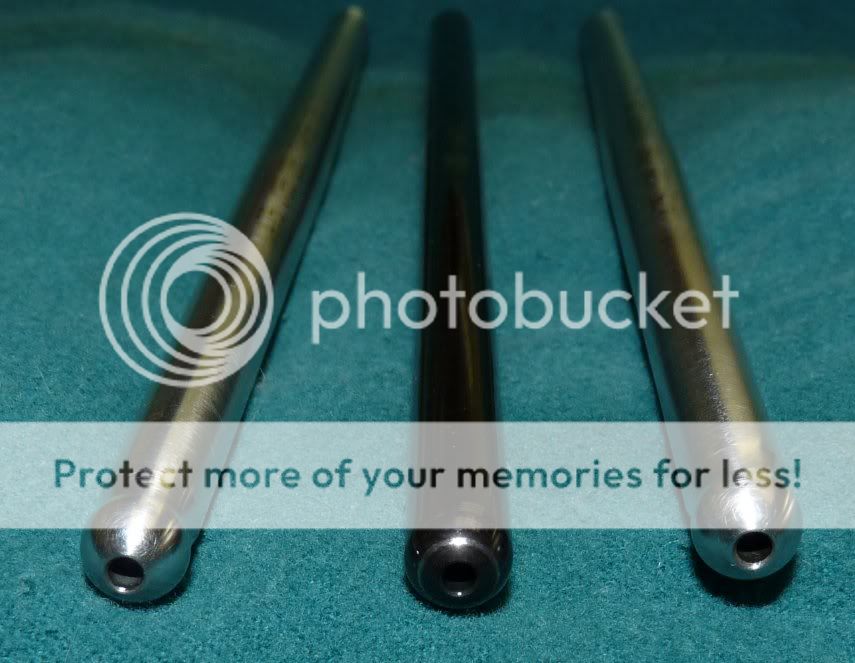
The next step in the process was to make sure they fit without interference. There was a bit of a learning curve on my part so I will let you know what worked in the end. Lets just say without very careful installation and removal your results could be wrong. To verify that the pushrods would not contact the heads or any internals of the motor, I used bluing to coat two pushrods that would be used in cylinder #1 for the intake and exhaust valve (see photo below). I made a sleeve to insert into the pushrod hole and then after coating the pushrods with bluing and allowing it time to dry, each pushrod is carefully inserted into the sleeve and then the sleeve is removed (see photo below). This eliminates any scraping that can occur during insertion of the coated pushrod giving the false indication that it contacts during valve operation. On my first two attempts it was an installation issue (and my learning curve) that was removing the bluing. The next step was to install the rocker set (Yella Terra) and spin the motor with the starter several times. Once the rockers were tightened in place, I used the starter to spin the motor and made sure there was oil pressure during this operation to obtain full valve lift (a bled down rocker will reduce valve lift and rocker motion potentially indicating no interference when there could in fact be interference). Once the motor was spun several times with the starter (28 psi of oil pressure was obtained), the rockers were removed and the sleeve was slid over each pushrod prior to removal to ensure no contact with the heads and the sleeve and pushrod are removed together. Once out of the motor, the sleeve is removed so the bluing can be examined. There was no contact anywhere along the length of the pushrod and therefore they cleared and could be used (the photo below is actually the post clearance check photo). A second check was done while rolling the motor over by hand with a wrench and verifying that there was no contact between the pushrod and the point of exit in the head just under the rocker arm. Also, with Yella Terra rocker arms, each cylinder must be placed in its firing position to install the rocker pair. As the motor is rotated the prior installed pushrod can be watched for any interference issues.
Bluing Applied
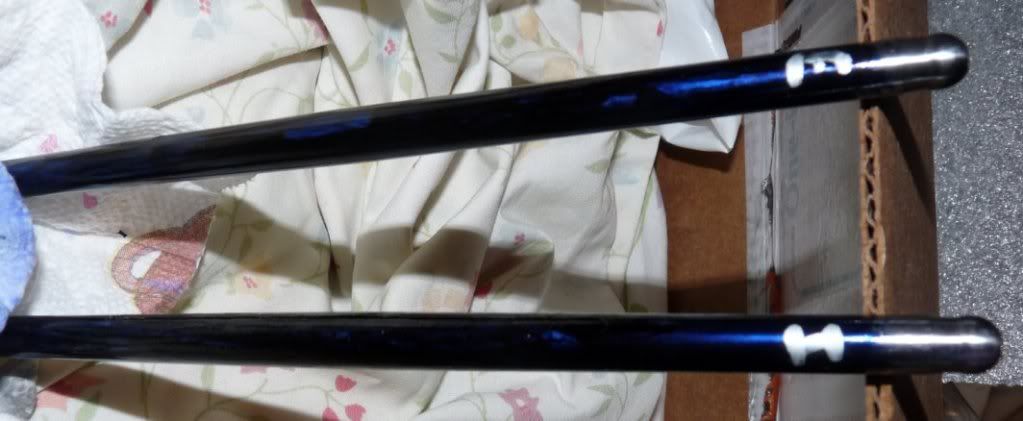
Protective Sleeve
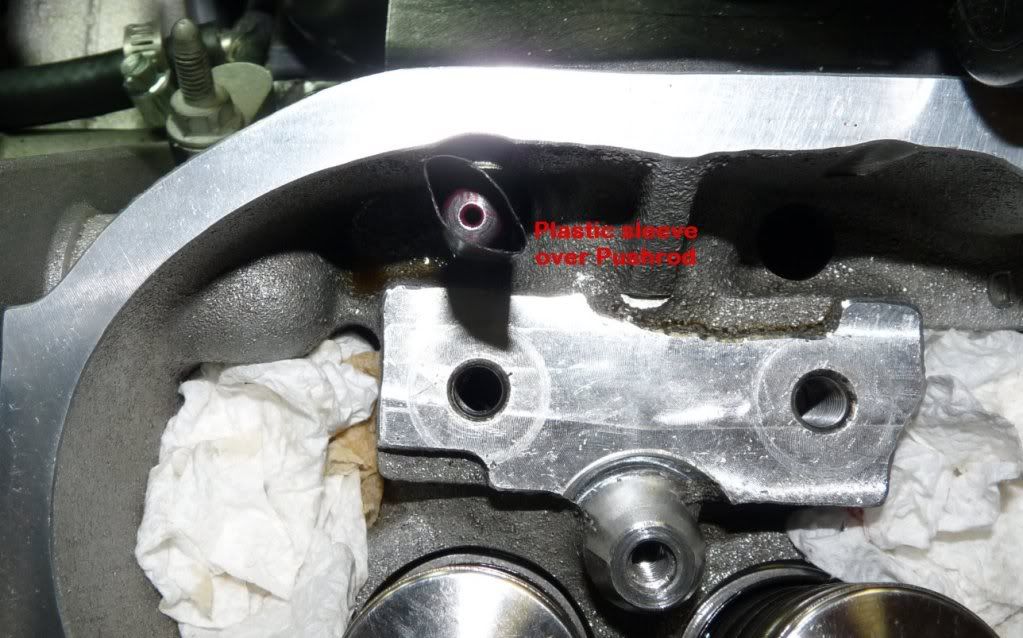
With the clearance verified, the pushrods were thoroughly cleaned and then immersed in oil to fill them for installation. This will aid with getting the oil to the rockers quickly on initial start. Also, a dab of Redline Assembly Lube is applied to the ball end of the pushrod and the top of the valve stem to ensure good lubrication until the oil starts flowing again. Startup was quiet with no lifter ticking.
I took the car back to the dyno to ensure the valve train was stable and see if there was any power difference. There was actually quite a difference, but the wrong way. After sorting things out, we attributed the power loss to the switch to winter blend fuel so for now the experiment was a bust in the power department. However, these pushrods should add to the longevity of the valve train life by minimizing flex and the potential issues that can occur as a result. My goal is a problem free long engine life with good street manners and plenty of power. Right now I know I have the power and the street manners, the longevity won’t be known for a while.
Update:
Gained 7hp due to increased valve train stability and the shape of the curve doesn't roll over above 6,200 RPM like the prior 5/16" pushrod setup. While not a lot of power, it does show I did have some pushrod flex.
Oil Bath
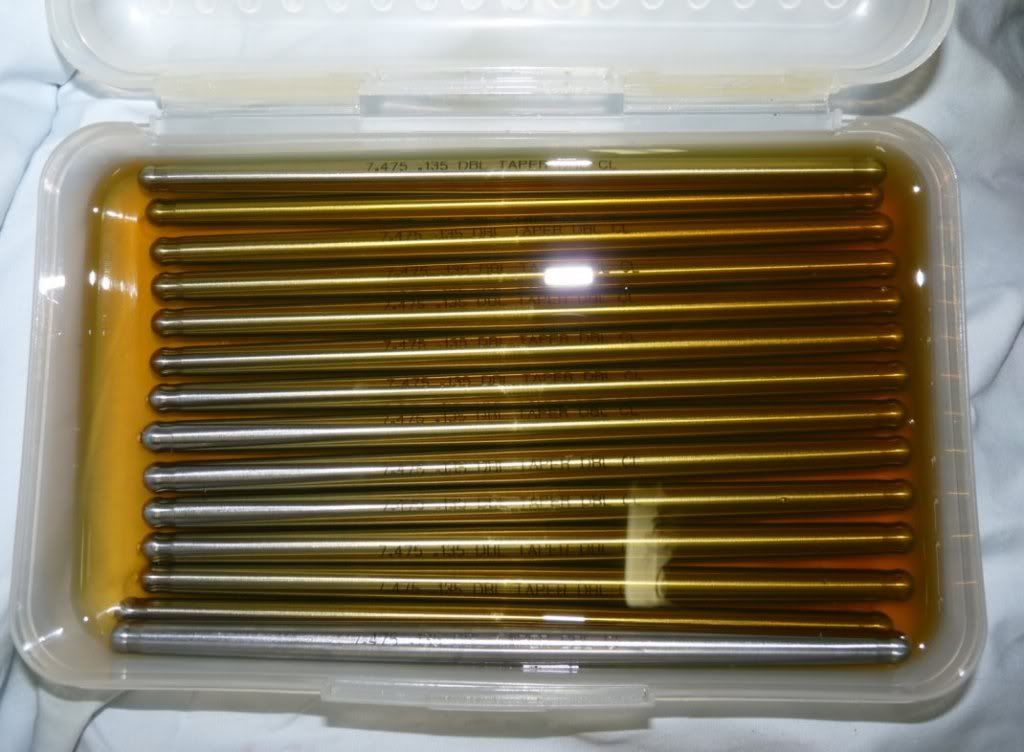
Application of Redline Assembly Lube
-------------------------------------------------------------------------------------------
Based on all of the above, I called Trend pushrod and spoke to John one last time to obtain length tolerance information and some specifics prior to ordering. Trend holds their pushrod length to +/- 0.005”. In the end I ordered the Trend 3/8”-5/16”, 0.135” wall, double tapered pushrods seen in the photo below. It is hard to see in the photo but the ball ends are fully CNC machined plus they have the 210 degree ball rather then the formed ball end on a standard aftermarket pushrod (note the stock pushrods have a 210 degree ball end). The second photo shows a comparison between the double tapered pushrods and the straight 5/16”, 0.080” wall pushrods they replaced (also made by Trend).
3/8”-5/16” Double Taper Trend Pushrods
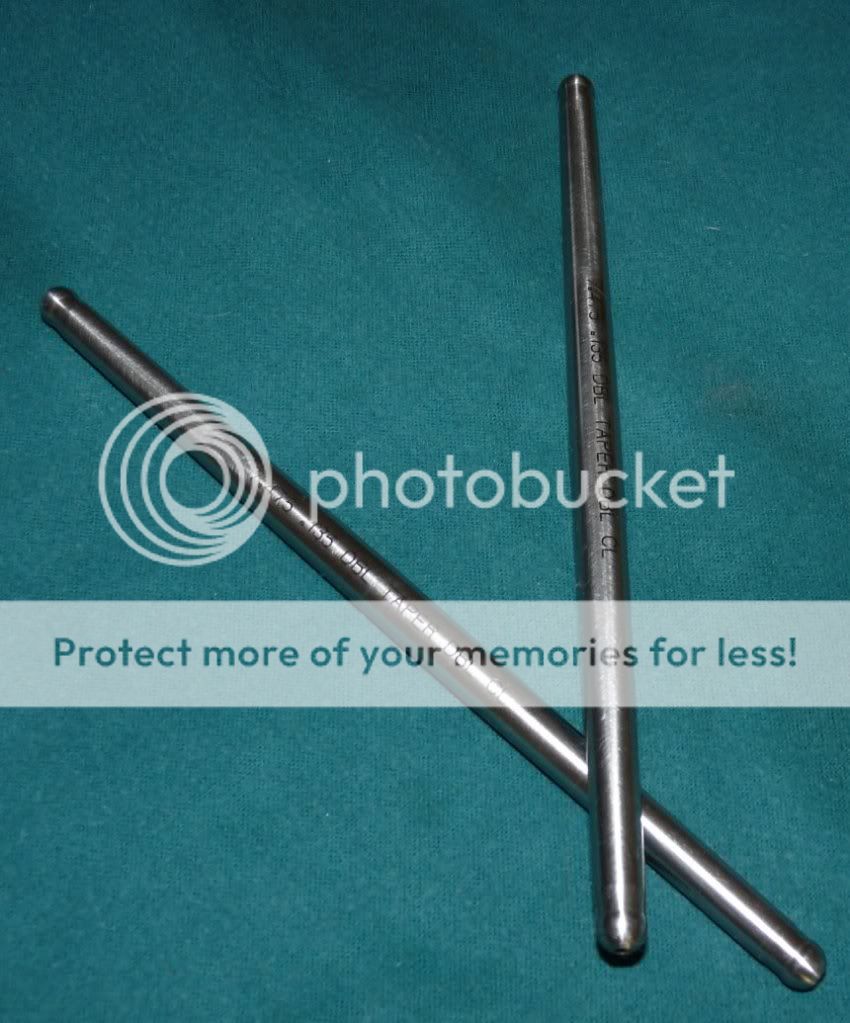
Comparison to 5/16”, 0.080” Wall Straight Pushrod
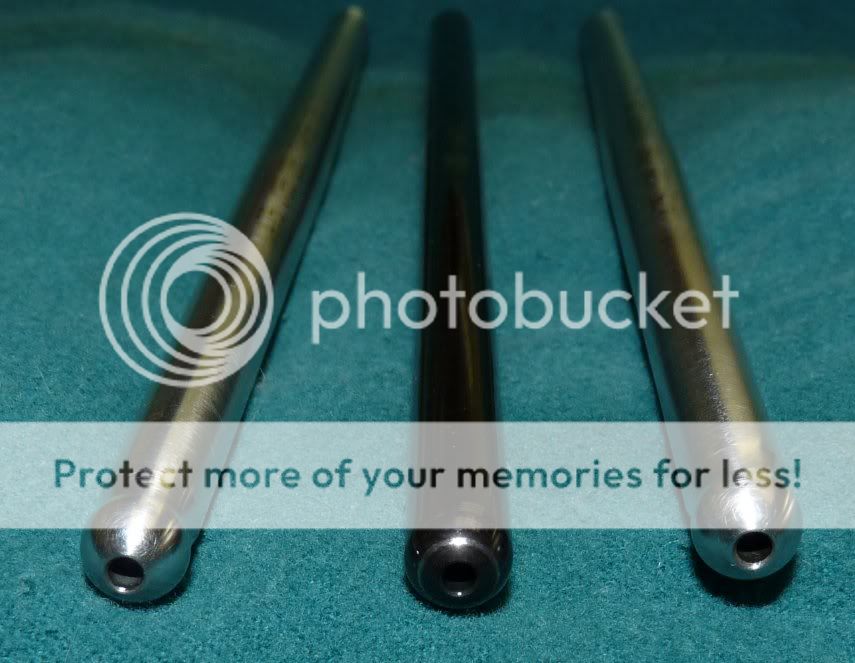
The next step in the process was to make sure they fit without interference. There was a bit of a learning curve on my part so I will let you know what worked in the end. Lets just say without very careful installation and removal your results could be wrong. To verify that the pushrods would not contact the heads or any internals of the motor, I used bluing to coat two pushrods that would be used in cylinder #1 for the intake and exhaust valve (see photo below). I made a sleeve to insert into the pushrod hole and then after coating the pushrods with bluing and allowing it time to dry, each pushrod is carefully inserted into the sleeve and then the sleeve is removed (see photo below). This eliminates any scraping that can occur during insertion of the coated pushrod giving the false indication that it contacts during valve operation. On my first two attempts it was an installation issue (and my learning curve) that was removing the bluing. The next step was to install the rocker set (Yella Terra) and spin the motor with the starter several times. Once the rockers were tightened in place, I used the starter to spin the motor and made sure there was oil pressure during this operation to obtain full valve lift (a bled down rocker will reduce valve lift and rocker motion potentially indicating no interference when there could in fact be interference). Once the motor was spun several times with the starter (28 psi of oil pressure was obtained), the rockers were removed and the sleeve was slid over each pushrod prior to removal to ensure no contact with the heads and the sleeve and pushrod are removed together. Once out of the motor, the sleeve is removed so the bluing can be examined. There was no contact anywhere along the length of the pushrod and therefore they cleared and could be used (the photo below is actually the post clearance check photo). A second check was done while rolling the motor over by hand with a wrench and verifying that there was no contact between the pushrod and the point of exit in the head just under the rocker arm. Also, with Yella Terra rocker arms, each cylinder must be placed in its firing position to install the rocker pair. As the motor is rotated the prior installed pushrod can be watched for any interference issues.
Bluing Applied
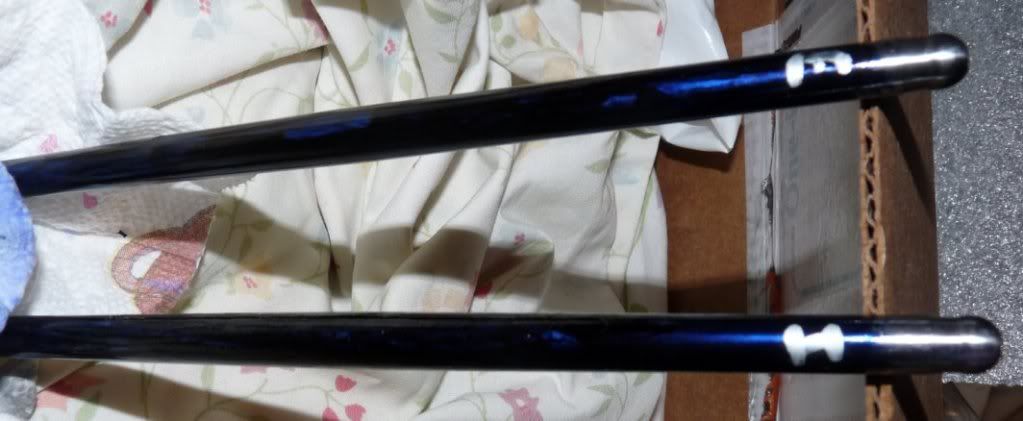
Protective Sleeve
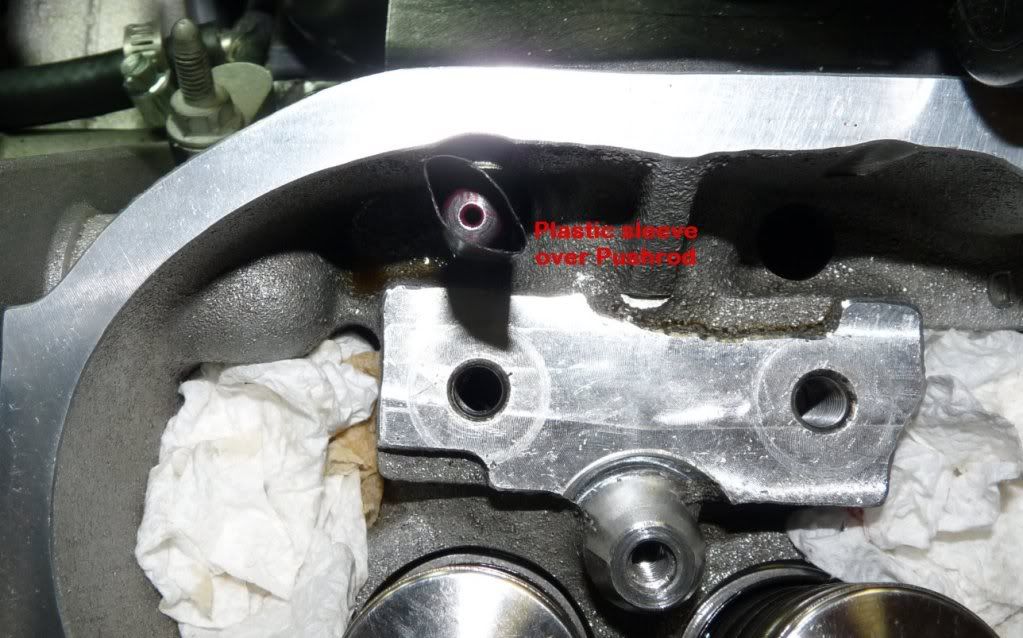
With the clearance verified, the pushrods were thoroughly cleaned and then immersed in oil to fill them for installation. This will aid with getting the oil to the rockers quickly on initial start. Also, a dab of Redline Assembly Lube is applied to the ball end of the pushrod and the top of the valve stem to ensure good lubrication until the oil starts flowing again. Startup was quiet with no lifter ticking.
I took the car back to the dyno to ensure the valve train was stable and see if there was any power difference. There was actually quite a difference, but the wrong way. After sorting things out, we attributed the power loss to the switch to winter blend fuel so for now the experiment was a bust in the power department. However, these pushrods should add to the longevity of the valve train life by minimizing flex and the potential issues that can occur as a result. My goal is a problem free long engine life with good street manners and plenty of power. Right now I know I have the power and the street manners, the longevity won’t be known for a while.

Update:
Gained 7hp due to increased valve train stability and the shape of the curve doesn't roll over above 6,200 RPM like the prior 5/16" pushrod setup. While not a lot of power, it does show I did have some pushrod flex.
Oil Bath
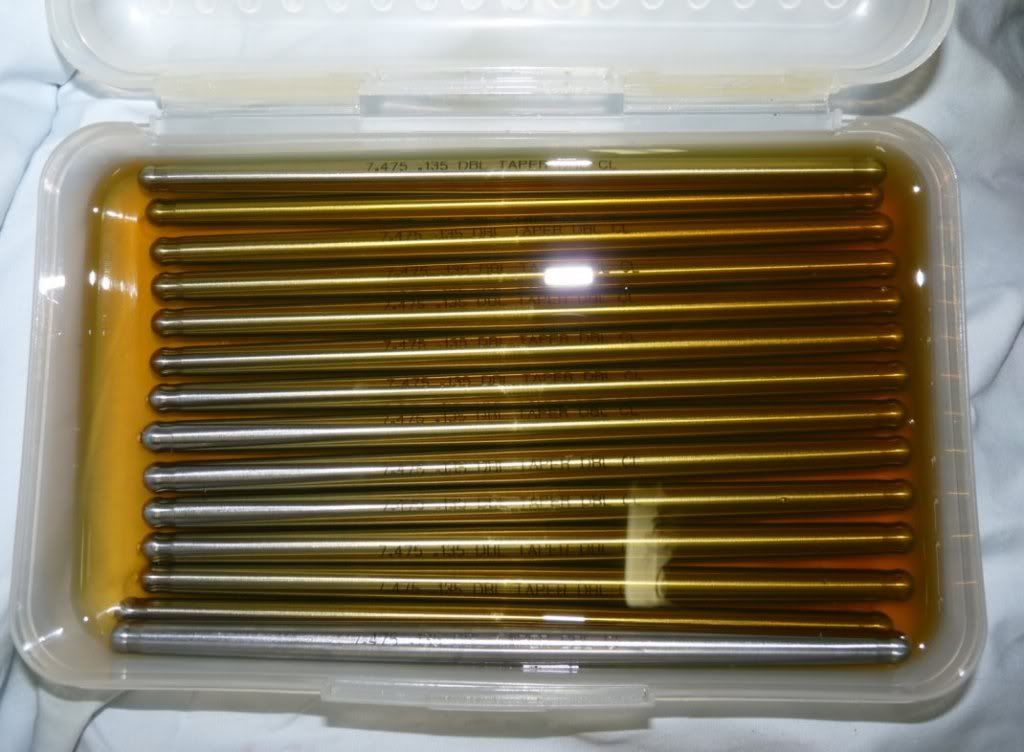
Application of Redline Assembly Lube
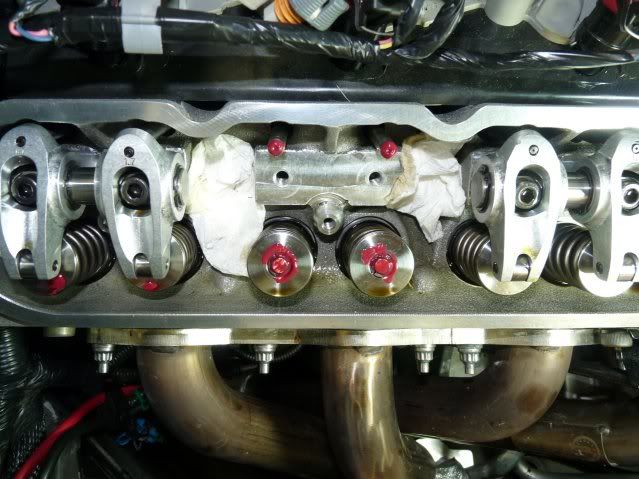
#24
On The Tree
Thread Starter
iTrader: (7)
Join Date: Jun 2012
Location: San Diego
Posts: 140
Likes: 0
Received 0 Likes
on
0 Posts

Good reading ..
I like messing with stuff too ..always getting in trouble with the with for not leaving stuff alone LOL
I want also a very quiet engine ..stealthy and match with my cam and exhuast setup should but quite stealthy setup ..and not loud obnoxious dinosaur.. hopfully setup works out to include longevity and reliability and future ability to support more power if i wasnt one to leave things alone in the future i think 5/16 or even 11/32 would do just fine lol
Thanks Zach
I like messing with stuff too ..always getting in trouble with the with for not leaving stuff alone LOL
I want also a very quiet engine ..stealthy and match with my cam and exhuast setup should but quite stealthy setup ..and not loud obnoxious dinosaur.. hopfully setup works out to include longevity and reliability and future ability to support more power if i wasnt one to leave things alone in the future i think 5/16 or even 11/32 would do just fine lol
Thanks Zach
#25
TECH Junkie
iTrader: (17)
Join Date: Aug 2006
Location: Rapid City, SD
Posts: 3,161
Likes: 0
Received 0 Likes
on
0 Posts


Comp Cams sells their 5/16" .105" wall for $189, and you can get Manton 11/32" .120" wall for $184.. Why would anyone get the Comp 5/16"?
Vettenuts, I read that same article you posted last week on a different forum and it definitely got me thinking about my setup. I think I'm going to proactively replace my 35k-mile cammed valve springs, and install the trunion bearings on my rockers, and I figured while I have them out, I would upgrade my stock pushrods. I believe I'll be getting the Manton 11/32 .120 pushrods. Excellent article!
It does seem the 11/32 .120 rods have a smaller oil hole. Will that be anything to be concerned about?
Vettenuts, I read that same article you posted last week on a different forum and it definitely got me thinking about my setup. I think I'm going to proactively replace my 35k-mile cammed valve springs, and install the trunion bearings on my rockers, and I figured while I have them out, I would upgrade my stock pushrods. I believe I'll be getting the Manton 11/32 .120 pushrods. Excellent article!
It does seem the 11/32 .120 rods have a smaller oil hole. Will that be anything to be concerned about?

#26
On The Tree
Thread Starter
iTrader: (7)
Join Date: Jun 2012
Location: San Diego
Posts: 140
Likes: 0
Received 0 Likes
on
0 Posts

From what I seen there's not much difference from 5/16 too 11/32 yes 11/32 is stiffer and but there's still abit of flexing last dyno chart there was like 2hp gain past 6k .so its s toss up there..there are company's that provided 5/16 rods I think brian tooly has them for 90 something iIRC .. but seems like your running stock so anything would be better.
Comp Cams sells their 5/16" .105" wall for $189, and you can get Manton 11/32" .120" wall for $184.. Why would anyone get the Comp 5/16"?
Vettenuts, I read that same article you posted last week on a different forum and it definitely got me thinking about my setup. I think I'm going to proactively replace my 35k-mile cammed valve springs, and install the trunion bearings on my rockers, and I figured while I have them out, I would upgrade my stock pushrods. I believe I'll be getting the Manton 11/32 .120 pushrods. Excellent article!
It does seem the 11/32 .120 rods have a smaller oil hole. Will that be anything to be concerned about?

Vettenuts, I read that same article you posted last week on a different forum and it definitely got me thinking about my setup. I think I'm going to proactively replace my 35k-mile cammed valve springs, and install the trunion bearings on my rockers, and I figured while I have them out, I would upgrade my stock pushrods. I believe I'll be getting the Manton 11/32 .120 pushrods. Excellent article!
It does seem the 11/32 .120 rods have a smaller oil hole. Will that be anything to be concerned about?

#29
TECH Senior Member
iTrader: (4)

PS: Trend also has good tech support, I spoke at length with them about length tolerance, how they are fabricated, etc. The ones I have were machined from solid billet steel blanks so the ends are not attached, they are machined as part of the pushrod itself.
#30
On The Tree
Thread Starter
iTrader: (7)
Join Date: Jun 2012
Location: San Diego
Posts: 140
Likes: 0
Received 0 Likes
on
0 Posts

I have to agree.. Trend tech support was really good and answered all questions i had ...
They have common lengths in stock and can make custom lengths also so will take little longer to get sent out ..2-3 days from what they told me
They have common lengths in stock and can make custom lengths also so will take little longer to get sent out ..2-3 days from what they told me