I keep breaking rocker arm bolts...
#23

got my pushrod length checker today, and this is what I came up with:
6.800 (length of pushrod tool)
0.5125 (10.25 turns)
7.3125
.060-.100 lifter preload (ls7 lifters)
desired pushrod length - 7.3725-7.4125
purchased 7.375 pushrods to give me .0625 of lifter preload.
This will be a total of .05 shorter than my current setup. Here's a few pictures of the difference.
6.800 (length of pushrod tool)
0.5125 (10.25 turns)
7.3125
.060-.100 lifter preload (ls7 lifters)
desired pushrod length - 7.3725-7.4125
purchased 7.375 pushrods to give me .0625 of lifter preload.
This will be a total of .05 shorter than my current setup. Here's a few pictures of the difference.
#24

i want to drop this here, as well, i made a video of the "play" in the rocker arms after snugging the bolt down, and adjusting the pushrod length checker until it could just BARELY spin.
The cam was on the base circle at the time I did this, obviously.
The cam was on the base circle at the time I did this, obviously.
Last edited by RADEoN; 10-28-2014 at 09:46 PM.
#25
8 Second Club
iTrader: (3)

Couple of things.
If the bolt is bottoming, the Trunion won't be clamped to the pedestal. The whole assembly will move around. Puts all the stress on the bolt.
Also, since you also busted a bolt with YT rockers, have you checked for coil bind?
Did you set up the spring installed height yourself?
Pushrods still straight?
Take a look at the stock bolt. See how long the shank is compared to the hardware store parts the rocker suppliers provide? The stock bolt is a better part.
But prob too long.
If the bolt is bottoming, the Trunion won't be clamped to the pedestal. The whole assembly will move around. Puts all the stress on the bolt.
Also, since you also busted a bolt with YT rockers, have you checked for coil bind?
Did you set up the spring installed height yourself?
Pushrods still straight?
Take a look at the stock bolt. See how long the shank is compared to the hardware store parts the rocker suppliers provide? The stock bolt is a better part.
But prob too long.
Last edited by RonSSNova; 10-29-2014 at 02:10 AM.
#27
That's MISTER MODERATOR
iTrader: (9)

I don't believe the manner in which this bolt has broken has anything to do with how or the depth that it was threaded into the head.
These bolts have a rather high sideways force working on them, not necessarily a tension force trying to pull it out of the head.
I'll say the pushrods were a bit too long.
These bolts have a rather high sideways force working on them, not necessarily a tension force trying to pull it out of the head.
I'll say the pushrods were a bit too long.
#28

I don't believe the manner in which this bolt has broken has anything to do with how or the depth that it was threaded into the head.
These bolts have a rather high sideways force working on them, not necessarily a tension force trying to pull it out of the head.
I'll say the pushrods were a bit too long.
These bolts have a rather high sideways force working on them, not necessarily a tension force trying to pull it out of the head.
I'll say the pushrods were a bit too long.
#29

each rocker has it's own pedestal, like in this picture:
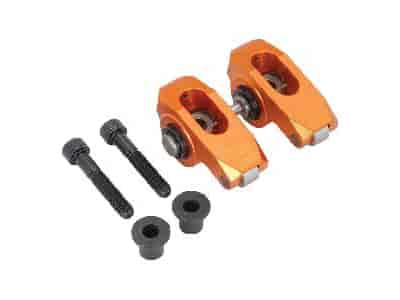
the bolt goes through the rocker, into the pedestal, then into the head.
#30
TECH Fanatic

I don't know if that is the OPs problem or not, can't help there.
Last edited by RezinTexas; 10-29-2014 at 05:34 PM.
#32
TECH Junkie
iTrader: (11)

the cam is at bottom dead center with a pushrod length checker in the head with 0 preload and a bolt that was just snugged, as to help get a good read on my pushrod length.
each rocker has it's own pedestal, like in this picture:
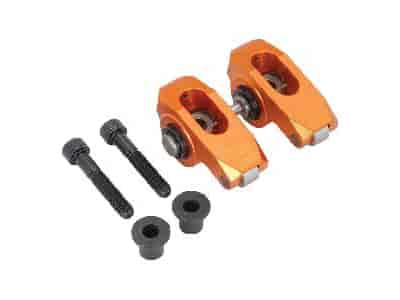
the bolt goes through the rocker, into the pedestal, then into the head.
each rocker has it's own pedestal, like in this picture:
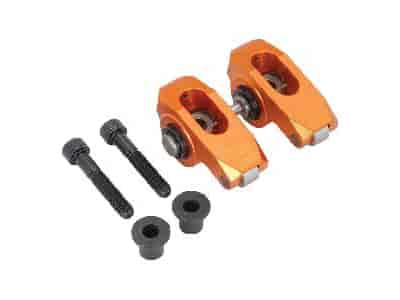
the bolt goes through the rocker, into the pedestal, then into the head.
#33
TECH Resident
iTrader: (34)

You are running the same heads that i am running on my 408. The intake is cnc'd enough that the bolt sticks through. The exhaust bolts will have a bottom in those heads.
22ftlbs is the correct torque for those rockers. Which rocker broke? Intake or exhaust? What does the tie bar look like between the rockers?
I have a modified set of these rockers with different pedestals and bolt to achieve the correct wipe pattern. I can measure the original bolts to see if they are the same as yours, pedestal appear to be the correct ones.
If you measured pushrod length before, with the correct preload added, that would be .080 of preload + the .050 that you say they need to be shorter, correct me if i am wrong, but you may be over the plunger limit of the lifters? I know some run .100 preload. Not all lifters will have the same exact tolerance for "preload-ability" so its possible to break the bolt since there is no more give?
Just running ideas, not sure what to think yet.
I ran those same bolts on a 235/240 650/609 112lsa cam in my old 346 with no problem, and my new setup has the same bolts but longer, and the head diameter machined down i think .040 smaller and have worked fine untill my damn reluctor wheel spun which is why i am currently putting the motor back together again. But the 70 break in miles had no problem with bolts.
I just use high temp thread sealer, no locker. I dont think they would work correctly if mixed.
Now that i think about it, i would think the back of the rocker would snap off before a bolt would break. I will have to think on it some tomorrow
Good luck
Idea:
Put the bolt through the rocker and pedastal and measure how much thread protrudes with a caliper. Then use the caliper and measure the depth of the hole for the exhaust rocker and this will tell you right away if your bolt is bottoming out.
22ftlbs is the correct torque for those rockers. Which rocker broke? Intake or exhaust? What does the tie bar look like between the rockers?
I have a modified set of these rockers with different pedestals and bolt to achieve the correct wipe pattern. I can measure the original bolts to see if they are the same as yours, pedestal appear to be the correct ones.
If you measured pushrod length before, with the correct preload added, that would be .080 of preload + the .050 that you say they need to be shorter, correct me if i am wrong, but you may be over the plunger limit of the lifters? I know some run .100 preload. Not all lifters will have the same exact tolerance for "preload-ability" so its possible to break the bolt since there is no more give?
Just running ideas, not sure what to think yet.
I ran those same bolts on a 235/240 650/609 112lsa cam in my old 346 with no problem, and my new setup has the same bolts but longer, and the head diameter machined down i think .040 smaller and have worked fine untill my damn reluctor wheel spun which is why i am currently putting the motor back together again. But the 70 break in miles had no problem with bolts.
I just use high temp thread sealer, no locker. I dont think they would work correctly if mixed.
Now that i think about it, i would think the back of the rocker would snap off before a bolt would break. I will have to think on it some tomorrow
Good luck
Idea:
Put the bolt through the rocker and pedastal and measure how much thread protrudes with a caliper. Then use the caliper and measure the depth of the hole for the exhaust rocker and this will tell you right away if your bolt is bottoming out.
Last edited by BlackDuk98; 10-31-2014 at 11:54 PM.
#34
TECH Fanatic
iTrader: (10)
Join Date: Mar 2011
Location: Miami gardens FL 33055
Posts: 1,023
Likes: 0
Received 0 Likes
on
0 Posts

Looks like a geometry problem easy to find if you knew what to look for or how to check your valve train, not to worry these problems take care of the school side of racing.
You know you'll get your ride back the minute you figure it out lol.
Here's a tip, when cam on base circle install push rod and both rockers, after the rocker arm latch goes to zero turn only 1/2 turn you should now have about the rite preload, if you can still turn way more than that chances are you are bottoming out on your lifters, at these time something will have to give sooner or later.
You know you'll get your ride back the minute you figure it out lol.
Here's a tip, when cam on base circle install push rod and both rockers, after the rocker arm latch goes to zero turn only 1/2 turn you should now have about the rite preload, if you can still turn way more than that chances are you are bottoming out on your lifters, at these time something will have to give sooner or later.
#36

I probably should have updated you guys. I bought a pushrod length checker, turns out my pushrods were about a quarter inch too long. Went from 7.425 to 7.375. When I first put these heads on my ls6, that was the length I measured, then I switched cams and blocks, and didn't think much about the pushrod length. Dimwitted move. That's why I wiped out the comp trunnion upgrade. It's all on me.
Yella Terras customer support is ******* OUTSTANDING. It's unfortunate that I already threw them under the bus and bought harland sharps. After dealing with Roger over there, I know 110 percent what my next purchase will be. He even sent me a pair of bolts.
We talked in depth about what the rockers were through, and he thinks they're going to be just fine. Pretty good news.
Yella Terras customer support is ******* OUTSTANDING. It's unfortunate that I already threw them under the bus and bought harland sharps. After dealing with Roger over there, I know 110 percent what my next purchase will be. He even sent me a pair of bolts.
We talked in depth about what the rockers were through, and he thinks they're going to be just fine. Pretty good news.