VVT vs VVT delete
#21
LS1Tech Premium Sponsor
iTrader: (5)

If anyone should have some before and after track times it should be Texas Speed. Your Cams are the ones I have been looking at.
.62 is a lot of lift for a VVT system. Have you had any problems? Is it true that the stronger springs have an effect on the VVT system? If someone buys the hollow stem valves what kind of spring set up can they get away with.
This next question might be a dumb one but I don't care I have been wanting to ask it ever since I started reading about VVT. From what I understand the VVT system works off oil pressure. Why don't they install a DC servo motor with a shaft encoder that works off the ECM instead of the oil system?
.62 is a lot of lift for a VVT system. Have you had any problems? Is it true that the stronger springs have an effect on the VVT system? If someone buys the hollow stem valves what kind of spring set up can they get away with.
This next question might be a dumb one but I don't care I have been wanting to ask it ever since I started reading about VVT. From what I understand the VVT system works off oil pressure. Why don't they install a DC servo motor with a shaft encoder that works off the ECM instead of the oil system?
You'd have to get in touch with someone at GM for answers on why this vs that. I bet the guys who CAN answer that question, don't take phone calls though.
__________________
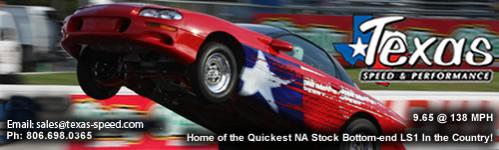
Largest Stocking Distributor of LS-x Engines / CHECK OUT OUR NEW WEBSITE!
COMP - FAST - PACESETTER - DIAMOND RACING - EAGLE SPECIALTY PRODUCTS - CALLIES - COMETIC GASKETS
RAM CLUTCHES - MOSER ENGINEERING - KOOK'S HEADERS - ARP - GM BOLTS AND GASKETS - MSD - NGK
POWERBOND - ASP - AND MORE!
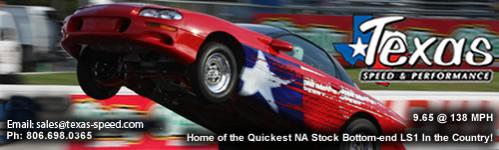
Largest Stocking Distributor of LS-x Engines / CHECK OUT OUR NEW WEBSITE!
COMP - FAST - PACESETTER - DIAMOND RACING - EAGLE SPECIALTY PRODUCTS - CALLIES - COMETIC GASKETS
RAM CLUTCHES - MOSER ENGINEERING - KOOK'S HEADERS - ARP - GM BOLTS AND GASKETS - MSD - NGK
POWERBOND - ASP - AND MORE!
#22
Launching!
Thread Starter
Join Date: Jan 2012
Location: Disneyland or St Louis
Posts: 234
Likes: 0
Received 0 Likes
on
0 Posts

The lifters in the VVT only combo's are not problematic. We have had success with the stock LS7 lifters, Comp 850's, Lunati TieBar lifters, etc. It's really only the stock AFM lifters that suck. With the VVT only cams we offer, we've been running the PRC .650" and .675" lift spring kits with no adverse conditions arising from the extra spring pressure. But again, we don't have any reason to suspect those lifters would have problems, because everyone else without VVT are running the same lifters with these springs too.
You'd have to get in touch with someone at GM for answers on why this vs that. I bet the guys who CAN answer that question, don't take phone calls though.
You'd have to get in touch with someone at GM for answers on why this vs that. I bet the guys who CAN answer that question, don't take phone calls though.
The AFM/DOD will be deleted for sure. I have read many times that the AFM lifters suck, but why do they suck? Is it just because they tick? Any problems with them and forced induction?
The .650 and .675 lift spring kit was what I was wondering about.
I e-mailed two automotive engineers about the VVT system and got no response.
Last edited by No Hope; 01-19-2012 at 05:56 PM.
#23
Launching!
Thread Starter
Join Date: Jan 2012
Location: Disneyland or St Louis
Posts: 234
Likes: 0
Received 0 Likes
on
0 Posts

The lifters in the VVT only combo's are not problematic. We have had success with the stock LS7 lifters, Comp 850's, Lunati TieBar lifters, etc. It's really only the stock AFM lifters that suck. With the VVT only cams we offer, we've been running the PRC .650" and .675" lift spring kits with no adverse conditions arising from the extra spring pressure. But again, we don't have any reason to suspect those lifters would have problems, because everyone else without VVT are running the same lifters with these springs too.
You'd have to get in touch with someone at GM for answers on why this vs that. I bet the guys who CAN answer that question, don't take phone calls though.
You'd have to get in touch with someone at GM for answers on why this vs that. I bet the guys who CAN answer that question, don't take phone calls though.
#24
12 Second Club
iTrader: (4)

Long story short, I know a guy, who knows the people that make the AFM lifters for GM. I was told the story but have since forgot most of it. Something about seperation of parts and destruction is possible when you got much past .500" lift, from what I remember. It wasnt really important to me sine I wont ever run a cam with AFM lifters.
Last edited by SweetS10V8; 01-19-2012 at 08:36 PM.
#26
Launching!
Thread Starter
Join Date: Jan 2012
Location: Disneyland or St Louis
Posts: 234
Likes: 0
Received 0 Likes
on
0 Posts

Ive done this testing, my results showed a slight loss of phaser control when you put in a stiffer dual spring. I recorded the commanded vs. the actual, and noticed with the dual springs it didnt go exactly where I commanded it and would continue to drift away the farther I got into the pull.
Long story short, I know a guy, who knows the people that make the AFM lifters for GM. I was told the story but have since forgot most of it. Something about seperation of parts and destruction is possible when you got much past .500" lift, from what I remember. It wasnt really important to me sine I wont ever run a cam with AFM lifters.
Long story short, I know a guy, who knows the people that make the AFM lifters for GM. I was told the story but have since forgot most of it. Something about seperation of parts and destruction is possible when you got much past .500" lift, from what I remember. It wasnt really important to me sine I wont ever run a cam with AFM lifters.
Any reading suggestions to help me understand the VVT systems?
#27

Any reading suggestions to help me understand the VVT systems?
#28
On The Tree

Call New Era, they have been working on VVT and have a step or two above from Comp's work. They of course are keeping it G14 classified and will only work on it themselves. I heard from Morgan's posting that it is bad **** and I agree with SweetS10 it's is like a holy grail!! I wouldn't remove it, I'd exploit it!
I'm surprized with it's potential, and the fact it can be adapted to any LSX engine, that it's not a common upgrade. Guess people are afraid of new things.
I have an LS1 apart in my garage right now, and I'm gonna be different and add VVT. Do the same, keep it. With it already there, you can always upgrade and adjust as new tech comes out for VVT.
#29
12 Second Club
iTrader: (4)

http://www.gmhightechperformance.com...all/index.html
#30
Launching!
Thread Starter
Join Date: Jan 2012
Location: Disneyland or St Louis
Posts: 234
Likes: 0
Received 0 Likes
on
0 Posts

Read captions of pictures explains its basic operations;
http://www.gmhightechperformance.com...all/index.html
http://www.gmhightechperformance.com...all/index.html
I take it the biggest problem the aftermarket Cam people are having is matching the exact RPM to the exact Degree on the phaser for the Cam? They are not getting a smooth curve?
Last edited by No Hope; 01-20-2012 at 10:44 AM.
#31
12 Second Club
iTrader: (4)

Getting it smooth isnt hard. Just take a little more time to optimise since you have an entirely new dimension in tuning.
Tune VVT at 0 full time
Tune VVT at 3 full time
And so on till 20...
You get a overlayed graph of all the pulls, and you find the break points in your tune. Then look at your overlayed dyno graph and input the value of the VVT pulls that had the most power/torque at that given break point in the tune.
Look at this torque change on a 3v 4.6 Mustang. This is zoomed each line is a different run while moving the commanded phaser angle.

Nope, havent been paying much attention lately, my testing and studies of VVT ended a few years ago. New era Probably gets their cams from Comp like almost everyone else does right?
Tune VVT at 0 full time
Tune VVT at 3 full time
And so on till 20...
You get a overlayed graph of all the pulls, and you find the break points in your tune. Then look at your overlayed dyno graph and input the value of the VVT pulls that had the most power/torque at that given break point in the tune.
Look at this torque change on a 3v 4.6 Mustang. This is zoomed each line is a different run while moving the commanded phaser angle.

Nope, havent been paying much attention lately, my testing and studies of VVT ended a few years ago. New era Probably gets their cams from Comp like almost everyone else does right?
Last edited by SweetS10V8; 01-20-2012 at 01:09 PM.
#32
TECH Addict
iTrader: (1)

Ive done this testing, my results showed a slight loss of phaser control when you put in a stiffer dual spring. I recorded the commanded vs. the actual, and noticed with the dual springs it didnt go exactly where I commanded it and would continue to drift away the farther I got into the pull.
#33
12 Second Club
iTrader: (4)

Yes full oil pressure, yes the phaser would have less control as I got higher in the RPM range. To put into focus though, Im only talking 1-3 degrees. It was a drift, Not a total loss of control.
The beehives were much more accurate in following my commanded VVT movement.
The beehives were much more accurate in following my commanded VVT movement.
#35
TECH Addict
iTrader: (4)

In the 70s people took of their HEIs and put back on points
In the 80-90s people removed their fuel injection and went back to a carb.
Today people remove VVT, because they dont understand it. Have fun removing awesome technology. Ive heard many many stories of guys that raced in the 70s trying to make their engines VVT, but couldnt. Because they understood the advantages of having the cam advanced for low end and retarding it to keep top end performance. Now that the OEMs have spent millions and brought the technology to the masses everyone is afraid of it.
In the 80-90s people removed their fuel injection and went back to a carb.
Today people remove VVT, because they dont understand it. Have fun removing awesome technology. Ive heard many many stories of guys that raced in the 70s trying to make their engines VVT, but couldnt. Because they understood the advantages of having the cam advanced for low end and retarding it to keep top end performance. Now that the OEMs have spent millions and brought the technology to the masses everyone is afraid of it.
#37

Here is some DOD information for some looking for it. This is strait from SI.
To provide maximum fuel economy under light load driving conditions, the engine control module (ECM) will command the cylinder deactivation system ON to deactivate engine cylinders 1, 7, 6, and 4, switching to a V4 mode. The engine will operate on 8 cylinders, or V8 mode, during engine starting, engine idling, and medium to heavy throttle applications.
Manifold absolute pressure (MAP) and the conditions listed below determine when cylinder deactivation is enabled.
•
Engine has been running for greater than 30 s
•
Engine speed is between 700 and 2800rpm
•
Engine oil pressure is between 187–455 kPa (27–66 psi)
•
Engine coolant temperature is between 40–129°C (100–264°F)
•
Engine oil temperature is between 16–128°C (61–263°F)
•
Throttle angle is 6% or less
•
Ignition voltage is greater than 11 V
•
Transmission is not in first, second, or reverse gear
•
Vehicle speed is greater than 25 kph (15.5 mph)
•
Brake booster pressure is greater than 42.0 kPa (6 psi)
•
Vehicle is not in fuel shut of mode
•
Vehicle is not in heater performance mode
•
Vehicle is not in tip in bump acceleration mode
•
Vehicle is not in oil aeration mode
•
Vehicle is not in low range (if equipped)
When cylinder deactivation is commanded, the ECM will determine what cylinder is firing and begin deactivation on the next closest deactivated cylinder in firing order sequence. For example, if cylinder number 1 is on its combustion event when cylinder deactivation is commanded ON, the next cylinder in the firing order sequence that can be deactivated is cylinder number 7. If cylinder number 5 is on its combustion event when cylinder deactivation is commanded ON, then the next cylinder in the firing order sequence that can be deactivated is cylinder number 4.
Cylinder deactivation is accomplished by not allowing the intake and exhaust valves to open on the selected cylinders by using special valve lifters. The deactivation lifters contain spring loaded locking pins that connect the internal pin housing of the lifter to the outer housing.
The pin housing contains the lifter plunger and pushrod seat which interfaces with the pushrod. The outer housing contacts the camshaft lobe through a roller. During V8 mode, when all cylinders are active, the locking pins are pushed outward by spring force, locking the pin housing and outer housing together causing the lifter to function as a normal lifter. When cylinder deactivation is commanded ON, the locking pins are pushed inward with engine oil pressure directed from the valve lifter oil manifold (VLOM) assembly solenoids. When the lifter pin housing is unlocked from the outer housing, the pin housing will remain stationary, while the outer housing will move with the profile of the camshaft lobe, which results in the valve remaining closed. One VLOM solenoid controls both the intake and exhaust valves for each deactivating cylinder. There are 2 distinct oil passages going to each cylinder deactivation lifter bore, one for the hydraulic lash-adjusting feature of the lifter, and one for controlling the locking pins used for cylinder deactivation.
Although both intake and exhaust valve lifters are controlled by the same solenoid in the VLOM, the intake and exhaust valves do not become deactivated at the same time. Cylinder deactivation is timed so that the cylinder is on an intake event. During an intake event, the intake cam lobe is pushing the valve lifter upwards to open the intake valve against the force of the valve spring. The force exerted by the valve spring is acting on the side of the lifter locking pins, preventing them from moving until the intake valve has closed. When the intake valve lifter reaches the base circle of the camshaft lobe, the valve spring force is reduced, allowing the locking pins to move, deactivating the intake valve. However, when cylinder deactivation is commanded ON, the exhaust valve for the deactivated cylinder is in the closed position, allowing the locking pins on the valve lifter to move immediately, and deactivate the exhaust valve.
By deactivating the exhaust valve first, this allows the capture of a burnt air/fuel charge, or exhaust gas charge, in the combustion chamber. The capture of exhaust gases in the combustion chamber will contribute to a reduction in oil consumption, noise and vibration levels, and exhaust emissions when operating in V4 mode cylinder deactivation mode.
During the transition from V8 to V4 mode, the fuel injectors will be turned OFF on the deactivated cylinders. To help prevent spark plug fouling, the ignition system secondary voltage or spark is still present across the spark plug electrodes on the deactivated cylinders. If all enabling conditions are met and maintained for cylinder deactivation operation, the ECM calibrations will limit cylinder deactivation to a cycle time of 10 minutes in V4 mode, then return to V8 mode for 1 minute.
Switching between V8 and V4 modes is accomplished in less than 250 milliseconds, making the transitions seamless and transparent to the vehicle operator. The 250 milliseconds includes the time for the ECM to sequence the transitions, the response time for the VLOM solenoids to energize, and the time for the valve lifters to deactivate, all within 2 revolutions of the engine crankshaft.
Valve Lifter Oil Manifold (VLOM) Assembly
The cylinder deactivation system uses an electro-hydraulic actuator device called the valve lifter oil manifold (VLOM) assembly. The VLOM is bolted to the top of the engine valley, below the intake manifold assembly. The VLOM consists of 4 electrically operated normally closed solenoids. Each solenoid controls the application of engine oil pressure to the intake and exhaust valve lifters on the cylinders selected to deactivate. Engine oil pressure is routed to the VLOM assembly from an internal oil passage on the rear of the cylinder block.
All 4 VLOM solenoids are connected in parallel to a fused ignition 1 voltage circuit, supplied by the powertrain relay. The ground or control circuit for each solenoid is connected to a low side driver internal to the engine control module (ECM).
When all enabling conditions are met for cylinder deactivation, the ECM will ground each solenoid control circuit in firing order sequence, allowing current to flow through the solenoid windings. With the coil windings energized, the solenoid valve opens, redirecting engine oil pressure through the VLOM into 8 separate vertical passages in the engine lifter valley. The 8 vertical passages, 2 per cylinder, are connected to the valve lifter bores of the cylinders to be deactivated. When vehicle-operating conditions require a return to V8 mode, the ECM will turn OFF the control circuit for the solenoids, allowing the solenoid valves to close. With the solenoid valves closed, engine oil pressure in the control ports is exhausted through the body of the solenoids into the engine block lifter valley. The housing of the VLOM incorporates several bleeds in the oil passages to purge any air trapped in the VLOM or engine block.
To help control contamination to the hydraulic circuits, a small replaceable oil screen is located in the VLOM oil inlet passage, below the oil pressure sensor. The oil pressure sensor is a 3-wire sensor which provides oil pressure information to the ECM.
During service, use extreme care in keeping the VLOM assembly free of any contamination or foreign material.
Cylinder deactivation may be inhibited for many reasons including the following:
•
Engine coolant temperature out of range for cylinder activation
•
Engine vacuum out of range
•
Brake booster vacuum out of range
•
Transmission gear incorrect or shift in progress
•
Accelerator pedal out of range or rate of pedal application to fast
•
Engine oil pressure and temperature out of range
•
Engine speed out of range
•
Vehicle speed out of range
•
Minimum time in V8 mode not met
•
Maximum V4 mode time exceeded
•
Decel fuel cutoff is active
•
Reduced engine power is active
•
Torque management is active
•
Catalytic converter over temperature protection is active
•
Piston protection is active, knock detected
•
Cylinder deactivation solenoid driver circuit faults
To provide maximum fuel economy under light load driving conditions, the engine control module (ECM) will command the cylinder deactivation system ON to deactivate engine cylinders 1, 7, 6, and 4, switching to a V4 mode. The engine will operate on 8 cylinders, or V8 mode, during engine starting, engine idling, and medium to heavy throttle applications.
Manifold absolute pressure (MAP) and the conditions listed below determine when cylinder deactivation is enabled.
•
Engine has been running for greater than 30 s
•
Engine speed is between 700 and 2800rpm
•
Engine oil pressure is between 187–455 kPa (27–66 psi)
•
Engine coolant temperature is between 40–129°C (100–264°F)
•
Engine oil temperature is between 16–128°C (61–263°F)
•
Throttle angle is 6% or less
•
Ignition voltage is greater than 11 V
•
Transmission is not in first, second, or reverse gear
•
Vehicle speed is greater than 25 kph (15.5 mph)
•
Brake booster pressure is greater than 42.0 kPa (6 psi)
•
Vehicle is not in fuel shut of mode
•
Vehicle is not in heater performance mode
•
Vehicle is not in tip in bump acceleration mode
•
Vehicle is not in oil aeration mode
•
Vehicle is not in low range (if equipped)
When cylinder deactivation is commanded, the ECM will determine what cylinder is firing and begin deactivation on the next closest deactivated cylinder in firing order sequence. For example, if cylinder number 1 is on its combustion event when cylinder deactivation is commanded ON, the next cylinder in the firing order sequence that can be deactivated is cylinder number 7. If cylinder number 5 is on its combustion event when cylinder deactivation is commanded ON, then the next cylinder in the firing order sequence that can be deactivated is cylinder number 4.
Cylinder deactivation is accomplished by not allowing the intake and exhaust valves to open on the selected cylinders by using special valve lifters. The deactivation lifters contain spring loaded locking pins that connect the internal pin housing of the lifter to the outer housing.
The pin housing contains the lifter plunger and pushrod seat which interfaces with the pushrod. The outer housing contacts the camshaft lobe through a roller. During V8 mode, when all cylinders are active, the locking pins are pushed outward by spring force, locking the pin housing and outer housing together causing the lifter to function as a normal lifter. When cylinder deactivation is commanded ON, the locking pins are pushed inward with engine oil pressure directed from the valve lifter oil manifold (VLOM) assembly solenoids. When the lifter pin housing is unlocked from the outer housing, the pin housing will remain stationary, while the outer housing will move with the profile of the camshaft lobe, which results in the valve remaining closed. One VLOM solenoid controls both the intake and exhaust valves for each deactivating cylinder. There are 2 distinct oil passages going to each cylinder deactivation lifter bore, one for the hydraulic lash-adjusting feature of the lifter, and one for controlling the locking pins used for cylinder deactivation.
Although both intake and exhaust valve lifters are controlled by the same solenoid in the VLOM, the intake and exhaust valves do not become deactivated at the same time. Cylinder deactivation is timed so that the cylinder is on an intake event. During an intake event, the intake cam lobe is pushing the valve lifter upwards to open the intake valve against the force of the valve spring. The force exerted by the valve spring is acting on the side of the lifter locking pins, preventing them from moving until the intake valve has closed. When the intake valve lifter reaches the base circle of the camshaft lobe, the valve spring force is reduced, allowing the locking pins to move, deactivating the intake valve. However, when cylinder deactivation is commanded ON, the exhaust valve for the deactivated cylinder is in the closed position, allowing the locking pins on the valve lifter to move immediately, and deactivate the exhaust valve.
By deactivating the exhaust valve first, this allows the capture of a burnt air/fuel charge, or exhaust gas charge, in the combustion chamber. The capture of exhaust gases in the combustion chamber will contribute to a reduction in oil consumption, noise and vibration levels, and exhaust emissions when operating in V4 mode cylinder deactivation mode.
During the transition from V8 to V4 mode, the fuel injectors will be turned OFF on the deactivated cylinders. To help prevent spark plug fouling, the ignition system secondary voltage or spark is still present across the spark plug electrodes on the deactivated cylinders. If all enabling conditions are met and maintained for cylinder deactivation operation, the ECM calibrations will limit cylinder deactivation to a cycle time of 10 minutes in V4 mode, then return to V8 mode for 1 minute.
Switching between V8 and V4 modes is accomplished in less than 250 milliseconds, making the transitions seamless and transparent to the vehicle operator. The 250 milliseconds includes the time for the ECM to sequence the transitions, the response time for the VLOM solenoids to energize, and the time for the valve lifters to deactivate, all within 2 revolutions of the engine crankshaft.
Valve Lifter Oil Manifold (VLOM) Assembly
The cylinder deactivation system uses an electro-hydraulic actuator device called the valve lifter oil manifold (VLOM) assembly. The VLOM is bolted to the top of the engine valley, below the intake manifold assembly. The VLOM consists of 4 electrically operated normally closed solenoids. Each solenoid controls the application of engine oil pressure to the intake and exhaust valve lifters on the cylinders selected to deactivate. Engine oil pressure is routed to the VLOM assembly from an internal oil passage on the rear of the cylinder block.
All 4 VLOM solenoids are connected in parallel to a fused ignition 1 voltage circuit, supplied by the powertrain relay. The ground or control circuit for each solenoid is connected to a low side driver internal to the engine control module (ECM).
When all enabling conditions are met for cylinder deactivation, the ECM will ground each solenoid control circuit in firing order sequence, allowing current to flow through the solenoid windings. With the coil windings energized, the solenoid valve opens, redirecting engine oil pressure through the VLOM into 8 separate vertical passages in the engine lifter valley. The 8 vertical passages, 2 per cylinder, are connected to the valve lifter bores of the cylinders to be deactivated. When vehicle-operating conditions require a return to V8 mode, the ECM will turn OFF the control circuit for the solenoids, allowing the solenoid valves to close. With the solenoid valves closed, engine oil pressure in the control ports is exhausted through the body of the solenoids into the engine block lifter valley. The housing of the VLOM incorporates several bleeds in the oil passages to purge any air trapped in the VLOM or engine block.
To help control contamination to the hydraulic circuits, a small replaceable oil screen is located in the VLOM oil inlet passage, below the oil pressure sensor. The oil pressure sensor is a 3-wire sensor which provides oil pressure information to the ECM.
During service, use extreme care in keeping the VLOM assembly free of any contamination or foreign material.
Cylinder deactivation may be inhibited for many reasons including the following:
•
Engine coolant temperature out of range for cylinder activation
•
Engine vacuum out of range
•
Brake booster vacuum out of range
•
Transmission gear incorrect or shift in progress
•
Accelerator pedal out of range or rate of pedal application to fast
•
Engine oil pressure and temperature out of range
•
Engine speed out of range
•
Vehicle speed out of range
•
Minimum time in V8 mode not met
•
Maximum V4 mode time exceeded
•
Decel fuel cutoff is active
•
Reduced engine power is active
•
Torque management is active
•
Catalytic converter over temperature protection is active
•
Piston protection is active, knock detected
•
Cylinder deactivation solenoid driver circuit faults
#40

I'm keeping the VVT in my L92 for my chevelle. I agree with S10 how hot rodders typically fear the unknown and revert to known parts/practices until they have a better understanding. I worked as a tech for BMW for years and saw the benefits from double vanos (vvt) on their engines and how well they performed with a given cam and could still meet ulev emissions with 500+hp.
Here's another good writeup about it if you haven't read up on it much.
http://www.hotrod.com/techarticles/e...t/viewall.html
And another here:
http://www.gmhightechperformance.com...ges/index.html
Here's another good writeup about it if you haven't read up on it much.
http://www.hotrod.com/techarticles/e...t/viewall.html
And another here:
http://www.gmhightechperformance.com...ges/index.html