Bay-to-bay breathing question
#21
TECH Senior Member

Oil can "get there", but it's not under pressure, and it wouldn't be a deluge. It will drain to the bottom, then to the pan.
The following users liked this post:
grinder11 (01-22-2022)
#22
11 Second Club
iTrader: (3)

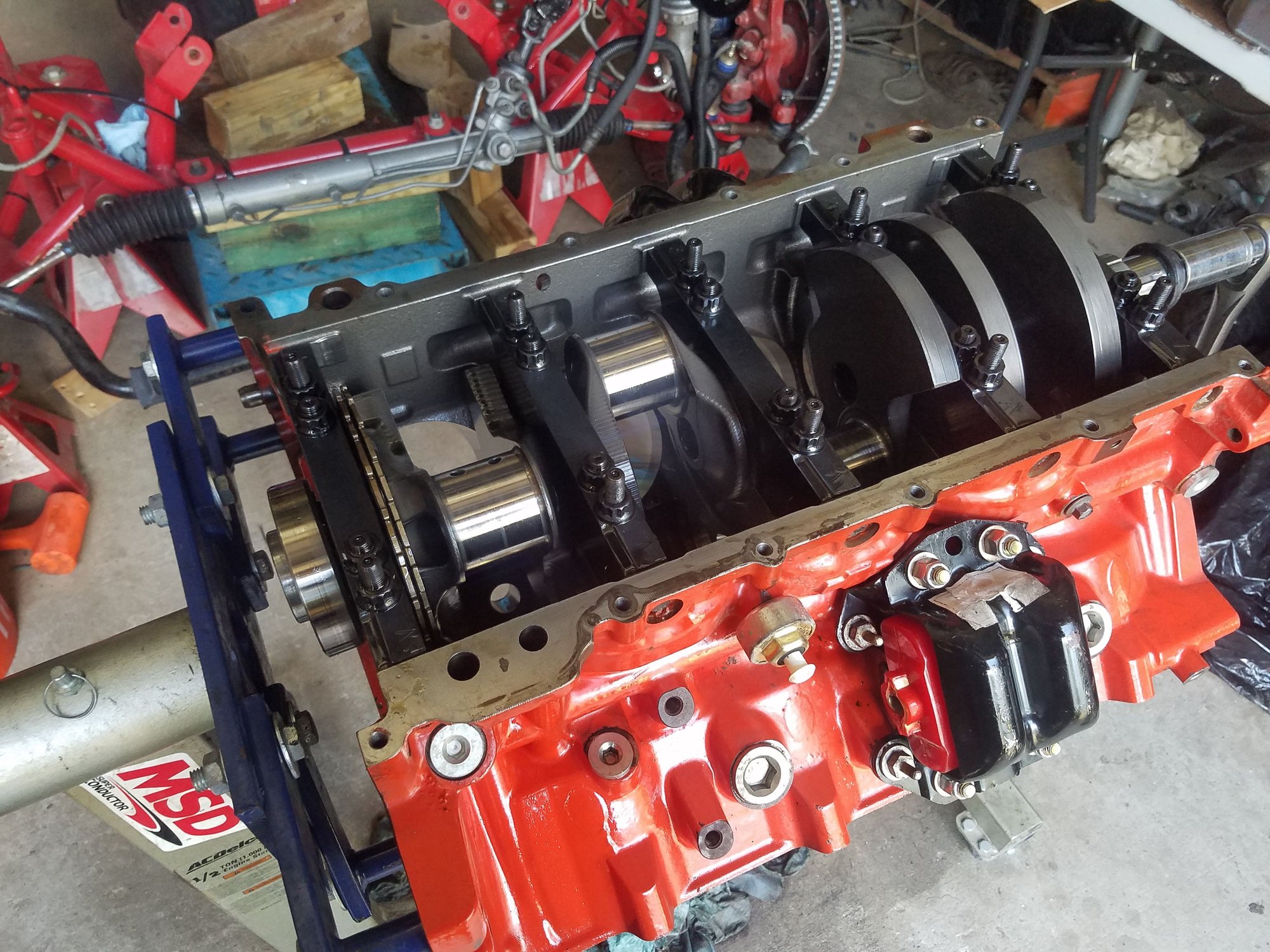
Here's a good look at the bay-to-bay breathing on an LSX block outfitted with a Callies Dragonslayer crankshaft.
#23
TECH Addict
iTrader: (1)

I was thinking about using a small angle grinder with a short drill bit, then a small burr. I'm not sure how much room is in there though. I don't have a big enough drill to go in from the ends.
It just looks like the holes in the end would allow oil to get into the front and back covers. I know those covers can leak, and I wouldn't want to encourage them more. I probably won't try this after all. It looks like something that is better left to the professionals.
It just looks like the holes in the end would allow oil to get into the front and back covers. I know those covers can leak, and I wouldn't want to encourage them more. I probably won't try this after all. It looks like something that is better left to the professionals.

#24
LS1TECH Sponsor
iTrader: (1)

Youre making the right decision. With all due respect, and coming from a retired Toolmaker, this isn't a DIY project with a Black and Decker drill motor. The holes are drilled in a specific location, with a specific size, one that engineers designed. I'm sure that's why Steve drills/bores them in the same location, and size, that GM used. You would need a Boring Mill, or some sort of horizontal milling machine, to do a job of this magnitude. Drills can wander. They can also cause stress. I know I'm picky, but if I did this job in the toolroom I worked in, I'd run the drill in like Steve does, but use a drill bit at least 1/4" undersize. Then I'd bore the holes to the correct size, say+-.005". Send it to Steve. He does damn good work. My .02.......

__________________
Steve Demirjian
Race Engine Development
Oceanside, Ca.
760-630-0450
web: www.raceenginedevelopment.com/
e-mail: race-engine-development@***.net
Steve Demirjian
Race Engine Development
Oceanside, Ca.
760-630-0450
web: www.raceenginedevelopment.com/
e-mail: race-engine-development@***.net
#25
TECH Addict
iTrader: (1)

Thanks for you comments. My CNC (Chevalier) has sufficient spindle to table to stand the block up to do the drilling. First the block is indicated in off the pan rails and clamped in place on the machine table. I know the offset position for the breather hole from the main bearing bore, front and back of the block from an LS1 block. The holes in the front and rear of the block are milled via circular interpolation. I drill the second and third (thrust bearing) bulkheads with a long half inch drill. Then I switch to a long 1" drill to drill those two bulkheads. Now the block is unbolted, flipped upside down and indicated in again. The rear hole is milled out and a half inch drill is used to drill the hole in bulkhead four then switched out for a 1" drill. It takes around three hours and is not a money making job for the $200 I'm currently charging. The way this was most likely done at GM was on big horizontal mill using a through coolant long gun drill or drills in a few minutes time.

#27
TECH Addict
iTrader: (1)

Anything is possible. GM, and all manufacturers, try to produce the best product they can, as cheaply as they can. The newer blocks have cast in "windows" above the main saddles. Saves a machining operation, so that's the way they do it now. But in FI setups, the aluminum blocks main saddles are slightly weakend, and they have been known to "let go" when into 4 figure horsepower. For guys under, say 900 crank hp, its not so much an issue....