New product... What do you want to see?
#521

I'll be honest here, and I will probably sound like a dick, but please don't take it that way.
You seriously need to step up your networking game on finding better injection molding prices. I have seen that reason used countless times as the deciding factor that prevents very badass and profitable items from being created.
I would LOVE what SparkyJJO said, a higher quality door panel that's slightly updated, but looks like it belongs. I DON'T love the idea of a cover. A cover is like a band aid with the wound underneath the never heals. That feels cheap to me. That's why I would rather pay more to buy an actual dash pad over a cover. I know many many other people also share this sentiment. I don't mean this to sound like I'm being a *****, I realize that's how it sounds.
You're in a very unique position to really bring something new and unique to this market. My suggestion would be to do some preliminary market research on what the people want (just like you've done with this thread), brainstorm some ideas, somehow get some capital together and work out a deal with an injection molding company and make it happen. Maybe not something as big as a door panel right off the bat, but a few examples...
One user here recently created some light up door panel buttons. The concept is excellent and his execution was pretty good, but actual molded buttons would be far superior. Those are small, the design is simple, and the idea is simple, but it's tasteful, subtle **** like that that really sells. Little to no work should need to be done on them after creation aside from packaging, so overhead is small, and you've began establishing a relationship with a good molder. Move into something slightly bigger, like a higher quality dash replacement. I know there's that company out in Florida, but I don't like how they changed the vent. Good LORD I can't imagine how that wouldn't pay for itself in a ridiculously short time.
And then bam, you can start getting more creative and move on to bigger things with a steady stream of injection molded items already below you. Don't you guys go to SEMA every year? Surely there's someone who has the hookup out there.
Again, not criticizing but being honest and throwing it out there. There may be something I'm not aware of in the step, but that's just me.
Cheers!
You seriously need to step up your networking game on finding better injection molding prices. I have seen that reason used countless times as the deciding factor that prevents very badass and profitable items from being created.
I would LOVE what SparkyJJO said, a higher quality door panel that's slightly updated, but looks like it belongs. I DON'T love the idea of a cover. A cover is like a band aid with the wound underneath the never heals. That feels cheap to me. That's why I would rather pay more to buy an actual dash pad over a cover. I know many many other people also share this sentiment. I don't mean this to sound like I'm being a *****, I realize that's how it sounds.
You're in a very unique position to really bring something new and unique to this market. My suggestion would be to do some preliminary market research on what the people want (just like you've done with this thread), brainstorm some ideas, somehow get some capital together and work out a deal with an injection molding company and make it happen. Maybe not something as big as a door panel right off the bat, but a few examples...
One user here recently created some light up door panel buttons. The concept is excellent and his execution was pretty good, but actual molded buttons would be far superior. Those are small, the design is simple, and the idea is simple, but it's tasteful, subtle **** like that that really sells. Little to no work should need to be done on them after creation aside from packaging, so overhead is small, and you've began establishing a relationship with a good molder. Move into something slightly bigger, like a higher quality dash replacement. I know there's that company out in Florida, but I don't like how they changed the vent. Good LORD I can't imagine how that wouldn't pay for itself in a ridiculously short time.
And then bam, you can start getting more creative and move on to bigger things with a steady stream of injection molded items already below you. Don't you guys go to SEMA every year? Surely there's someone who has the hookup out there.
Again, not criticizing but being honest and throwing it out there. There may be something I'm not aware of in the step, but that's just me.
Cheers!

Let's say they were super cheap, $15 each, and we sold them stupid expensive, $250 each (so $500 for a PAIR of doorpanels, stupid but follow me here)... we'd have to sell 213 to break even.
Doesn't sound horrible... until you consider the market. We haven't sold 213 of ANY ONE PRODUCT in OVER FIVE YEARS...
Here's a screen shot from right now of our back end...
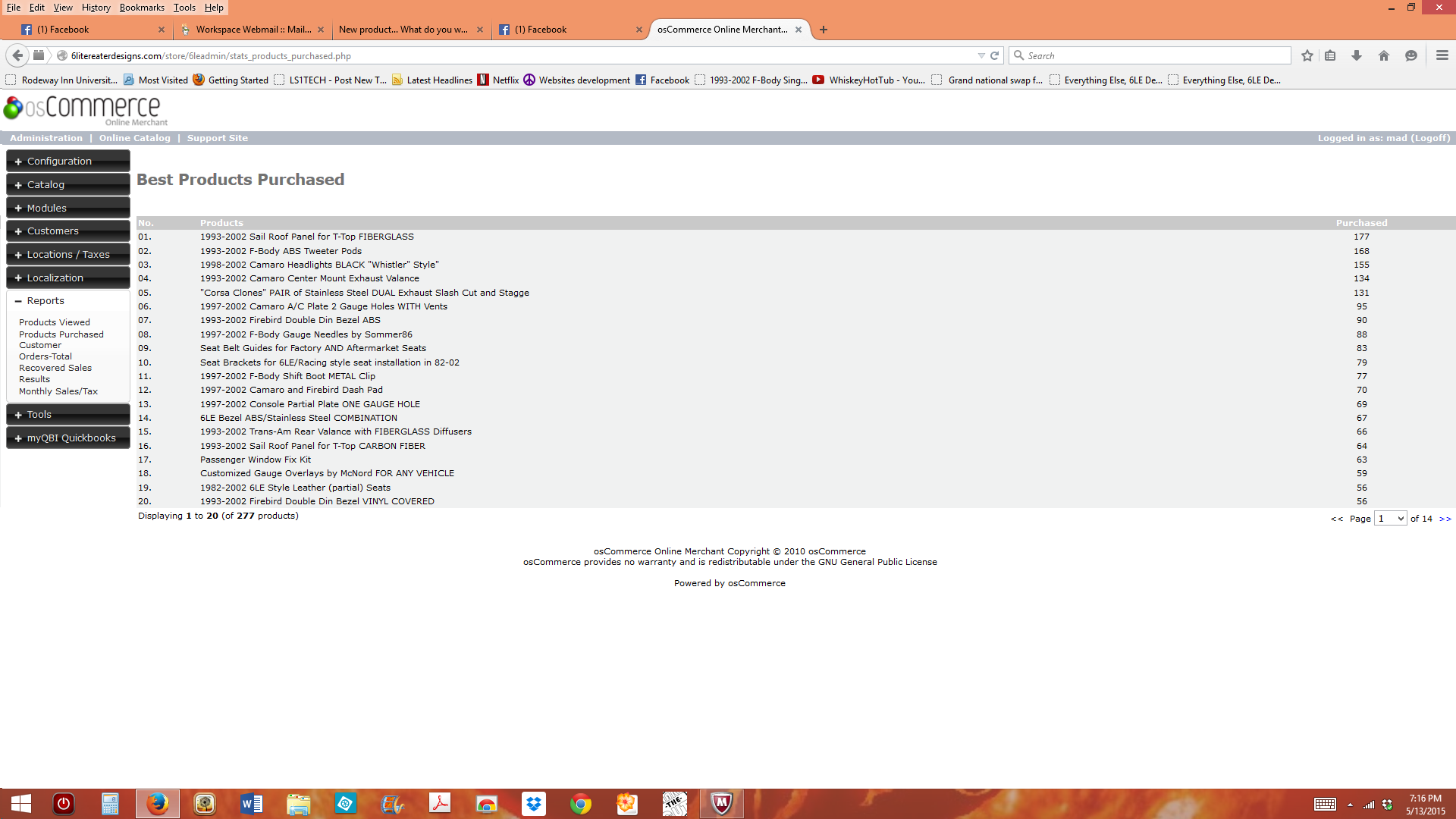
Our highest seller is the t-top roof which all 1999+ cars NEED and we haven't sold over 200 of them.
No way in hell we'd EVER break even, even with China prices, on anything like this.
There's a reason large companies WITH MAJOR VOLUME (and better deals) in injection molds already, WITH the money to just make things people MIGHT buy and average out with their 1000's of other products, HAVEN'T done this either.
Now you also see why we try not to invest in ANYTHING without at least 10 pre-orders as a proof of concept that it will sell, just look how the numbers on the screen shot drop out of the triple digits by only the SIXTH item...
#527
TECH Veteran
iTrader: (14)

Door panels would be more challenging sure, dash pads would be pretty easy. I've been doing it for several years but with much smaller items for another hobby, but I also use pressure pots to keep air bubbles to a minimum.
I'll shoot you an email tomorrow and share some info if interested
I'll shoot you an email tomorrow and share some info if interested
#528

Door panels would be more challenging sure, dash pads would be pretty easy. I've been doing it for several years but with much smaller items for another hobby, but I also use pressure pots to keep air bubbles to a minimum.
I'll shoot you an email tomorrow and share some info if interested
I'll shoot you an email tomorrow and share some info if interested
#529
TECH Veteran
iTrader: (14)

That's the beauty of the silicone it has a high tear strength and is forgiving enough to cast some intricate part and remove them while keeping the mold intact though the more intricate the shorter the mold life. The issue is proper venting to keep air bubbles to a minimum in parts. I'll shoot you an email tomorrow
#534
12 Second Club
iTrader: (28)

I'm not sure silicone/urethane molding is the right technique for heavy-abuse items like door panels or high-UV exposure combined with snap-clips like dash pads. I haven't really seen any cast rigid plastic parts that have the flexibility and durability and UV resistance necessary for either task. If you have, I'd like to see more info.
#535
TECH Veteran
iTrader: (14)

Its just a matter of using a uv resistant pigment as far as the color fade goes.
there's actually a video on youtube of a ureathane bumper being cast with this process, but im not sure of the materials used as it looks like they are using plastic repair guns to fill the mold.
I have similar concerns about interior panels, but we are talking about a pretty low cost investment to see if it works. I personally think a material i have been using could hold up, but I would be a bit concerned about the high heat deformation, as well as how they would the clips would hold up to removing and installing the part repeatedly.
The stuff I use is used for bust's, movie props, stuatues, movie makeup. Has a wide range of materials for different applications rangine from flexible to super rigid (to detriment at times)
most people think of casting they think of the stuff you get at hobby lobby that isnt suited for much more than model making. Its rigid, brittle and really not intended for much outside the hobby realm.
there's actually a video on youtube of a ureathane bumper being cast with this process, but im not sure of the materials used as it looks like they are using plastic repair guns to fill the mold.
I have similar concerns about interior panels, but we are talking about a pretty low cost investment to see if it works. I personally think a material i have been using could hold up, but I would be a bit concerned about the high heat deformation, as well as how they would the clips would hold up to removing and installing the part repeatedly.
The stuff I use is used for bust's, movie props, stuatues, movie makeup. Has a wide range of materials for different applications rangine from flexible to super rigid (to detriment at times)
most people think of casting they think of the stuff you get at hobby lobby that isnt suited for much more than model making. Its rigid, brittle and really not intended for much outside the hobby realm.
#536
12 Second Club
iTrader: (28)

It's more of a structural concern than a color concern as many plastics can become brittle/disintegrate with high temps and high UV exposure. I lived in the high desert for a while and my parents live out there. Not many molded/cast plastics can withstand the UV exposure. It'd be exciting to see if one of the products you are thinking of will work. My girlfriend works with fiberglass and casting materials every day at her job and she could probably help me make something as a test piece.
#538
TECH Veteran
iTrader: (14)

It's more of a structural concern than a color concern as many plastics can become brittle/disintegrate with high temps and high UV exposure. I lived in the high desert for a while and my parents live out there. Not many molded/cast plastics can withstand the UV exposure. It'd be exciting to see if one of the products you are thinking of will work. My girlfriend works with fiberglass and casting materials every day at her job and she could probably help me make something as a test piece.
Yeah not all plastics are created equal, I offered this suggestion with no certainty that it will work in the end. I have never used it in an automotive capacity nor have I ever left any of it in the sun long enough to matter. Only thing to do is try it with something small and see what happens. Ive never delt with molding with fiberglass stuff, I've made one offs with it before and its not my favorite material to work with haha.
as long as something i smooth on both sides though, it wouldnt be hard to make a mold of. The perfect test piece would be something small enough to not need a lot of material but also have some thinner areas to see how it would hold up to the high heat of an interior, as well as if there would be any UV degradation.
#539
TECH Fanatic
iTrader: (3)

I'll be honest here, and I will probably sound like a dick, but please don't take it that way.
You seriously need to step up your networking game on finding better injection molding prices. I have seen that reason used countless times as the deciding factor that prevents very badass and profitable items from being created.
I would LOVE what SparkyJJO said, a higher quality door panel that's slightly updated, but looks like it belongs. I DON'T love the idea of a cover. A cover is like a band aid with the wound underneath the never heals. That feels cheap to me. That's why I would rather pay more to buy an actual dash pad over a cover. I know many many other people also share this sentiment. I don't mean this to sound like I'm being a *****, I realize that's how it sounds.
You're in a very unique position to really bring something new and unique to this market. My suggestion would be to do some preliminary market research on what the people want (just like you've done with this thread), brainstorm some ideas, somehow get some capital together and work out a deal with an injection molding company and make it happen. Maybe not something as big as a door panel right off the bat, but a few examples...
One user here recently created some light up door panel buttons. The concept is excellent and his execution was pretty good, but actual molded buttons would be far superior. Those are small, the design is simple, and the idea is simple, but it's tasteful, subtle **** like that that really sells. Little to no work should need to be done on them after creation aside from packaging, so overhead is small, and you've began establishing a relationship with a good molder. Move into something slightly bigger, like a higher quality dash replacement. I know there's that company out in Florida, but I don't like how they changed the vent. Good LORD I can't imagine how that wouldn't pay for itself in a ridiculously short time.
And then bam, you can start getting more creative and move on to bigger things with a steady stream of injection molded items already below you. Don't you guys go to SEMA every year? Surely there's someone who has the hookup out there.
Again, not criticizing but being honest and throwing it out there. There may be something I'm not aware of in the step, but that's just me.
Cheers!
You seriously need to step up your networking game on finding better injection molding prices. I have seen that reason used countless times as the deciding factor that prevents very badass and profitable items from being created.
I would LOVE what SparkyJJO said, a higher quality door panel that's slightly updated, but looks like it belongs. I DON'T love the idea of a cover. A cover is like a band aid with the wound underneath the never heals. That feels cheap to me. That's why I would rather pay more to buy an actual dash pad over a cover. I know many many other people also share this sentiment. I don't mean this to sound like I'm being a *****, I realize that's how it sounds.
You're in a very unique position to really bring something new and unique to this market. My suggestion would be to do some preliminary market research on what the people want (just like you've done with this thread), brainstorm some ideas, somehow get some capital together and work out a deal with an injection molding company and make it happen. Maybe not something as big as a door panel right off the bat, but a few examples...
One user here recently created some light up door panel buttons. The concept is excellent and his execution was pretty good, but actual molded buttons would be far superior. Those are small, the design is simple, and the idea is simple, but it's tasteful, subtle **** like that that really sells. Little to no work should need to be done on them after creation aside from packaging, so overhead is small, and you've began establishing a relationship with a good molder. Move into something slightly bigger, like a higher quality dash replacement. I know there's that company out in Florida, but I don't like how they changed the vent. Good LORD I can't imagine how that wouldn't pay for itself in a ridiculously short time.
And then bam, you can start getting more creative and move on to bigger things with a steady stream of injection molded items already below you. Don't you guys go to SEMA every year? Surely there's someone who has the hookup out there.
Again, not criticizing but being honest and throwing it out there. There may be something I'm not aware of in the step, but that's just me.
Cheers!

And in the end, the market is just not there to make it finacially feasible. It may seem like its there because it very easy for people to like things and verbally say they want or will purchase. But when its time to open the wallet or scan the credit card, very little actually pony up.
#540
Copy & Paste Moderator

For small parts like the switches, we should be thinking 3D printing instead of molding.
Especially since some printers can handle multiple kinds of plastic stock in one forming so you could have light guides molded in.
At a minimum, a simple/cheap hobby-grade $300 printer that can handle only 1 kind of plastic at a time can be used to make frosted buttons that are later sanded and painted/printed.
The end result will still be a relatively expensive part (the plastic is the relatively expensive part and the printing/painting can add up too), but the upfront/ramp-up cost for the vender will be minimal compared to a traditional mold.
Especially since some printers can handle multiple kinds of plastic stock in one forming so you could have light guides molded in.
At a minimum, a simple/cheap hobby-grade $300 printer that can handle only 1 kind of plastic at a time can be used to make frosted buttons that are later sanded and painted/printed.
The end result will still be a relatively expensive part (the plastic is the relatively expensive part and the printing/painting can add up too), but the upfront/ramp-up cost for the vender will be minimal compared to a traditional mold.