1970 GTO Version 2.0
#361
TECH Senior Member
Thread Starter
iTrader: (7)

I don't know about the 73-77 a-bodies. Since you have stock suspension I would look over the stock parts very carefully before purchasing any aftermarket components.
Andrew
#362
TECH Regular
iTrader: (5)
Join Date: Mar 2010
Location: Vancouver area, West coast Canada
Posts: 405
Likes: 0
Received 32 Likes
on
21 Posts


That must mean there is a left and right version of the stockers, and those aftermarket units. I wonder how many have been put back on the wrong sides inadvertently.
#363
TECH Senior Member
Thread Starter
iTrader: (7)

Andrew
#364

Great build! I've been reading and searched but dont see it...what computer are you using? I ask because of the Monte DBW throttle pedal. Its what I have in my car also. Havent been able to start the car yet, Trying to decide if I picked the correct pedal or not.
#365
TECH Junkie
iTrader: (1)

Dammit, I just put another brand of adjustable upper arms in my 72 cutlass to get the pinion angle correct. Guess I'll be measuring the right/left offset tomorrow......
There was only one part number for stock control arms, no left and right. The reason being is that they can only go on one way due to the design. The stock arms are stamped in a U-shaped channel and they can only slip over the bushings on the rear end in one way. So arms are made only one way because they can't be flipped upside down by mistake. The RideTech arms are built in a similar way. The part that slips over the rear end bushing only goes on one way. This insures that the offset is always to the driver's side of the car.
Andrew
Andrew
#368
TECH Senior Member
Thread Starter
iTrader: (7)

Last Thursday I finished my last final, so I am officially done with the spring semester. I am ready to relax and get back to my GTO. It's hard to imagine, but it was three years ago that I completed the L92 engine swap. My, how time flies. In the summer of 2008 I put about 6,000 miles on the car. The plans for this summer are more modest, but I would like to attend a couple of events and maybe visit some friends out west. After much deliberation and for a lack of simple options, I have decided to get the Richmond 6 speed rebuilt. Richmond Gear has been working with me and we came to an agreement. They are currently in possession of my transmission and will give it a thorough inspection. All the gears will be magnufluxed and all parts that are damaged will be replaced. I never had any fundamental objections to the Richmond. I always felt that it shifted fine and offered an awesome, close-ratio gear spread for gears 1-5 and a comfortable .62 overdrive. Keeping the same transmissions will also allow me to keep my current crossmember and not worry about an alternate shifter location.
With road trips planned for the summer, I once again turned to a problem that has plagued my car since day one. Despite numerous efforts I have been unable to completely eliminate the high speed vibration that my car exhibits at speeds about 75 mph. It's really frustrating on long highway trips, because the car feels amazing cruising at speeds between 75 and 80 mph.
I have already posted what my thoughts are regarding the rear end position. I will be swapping out the current rear upper control arms for ones made by RideTech. I firmly believe that while the rear end position may not be entirely responsible for my vibration, it is certainly a factor. I will also be doing other driveline upgrades at the same time. What I have planned may be a little overboard, but I believe that it will completely eliminate any driveline alignment and vibration issues in the future. Here is the plan....
The first step is to get a rear pinion yoke that is machined with the kind of tolerances that are required to achieve smooth operation at sustained high speeds. I chose a 1350 billet yoke from Mark Williams:

With the rear taken care of, the next item to tackle is the driveshaft. There are many fine companies that make driveshafts, but given my alignment issues, I wanted to pick a vendor that was able to offer something unique. I have worked with Frank at The DriveShaft Shop (DSS) in the past when I needed custom axles for my RX7. Frank has always been attentive to my needs and has provided a quality product that has met and exceeded my expectations. The DSS is widely known in the sport compact world for making bullet proof CV axles, and recently they have also been doing some innovative work on the many modern muscle cars that use independent rear suspensions. Cars like the new Camaro, Dodge Charger, GTOs, and Cadillac CTS-V are rear drive, high HP, and heavy. That combination is the perfect storm for breaking driveline components, and DSS has stepped up to the plate with upgraded CV shafts, driveshafts, and complete 9" IRS swap packages.
After deliberating with Frank about my GTO and the issues that I am having we came up with a very elegant solution. Frank will make me a custom driveshaft with a CV joint in the front. People in the 4x4 world have used double cardon CV joint driveshafts for a long time to deal with extreme driveline angles. But double cardon joints are bulky and heavy, and just didn't seem appropriate for a car. What will be used in the front is a 6 ball, Porsche 930 style CV. Like this:
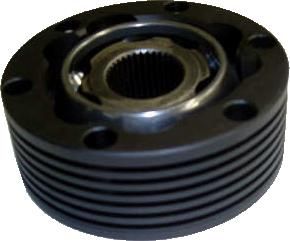
CV joints are designed to operate at high speeds and at extreme operating angles. Furthermore, there is no need to match the front and rear angles, as you need with a shaft that uses u-joints on both ends. With the CV joint in the front I will adjust my pinion angle so that the pinion and the driveshaft have almost a zero working angle. A slight angle is required only to make sure that the needles in the u-joint caps get lubricated. The rear working angle will be less than .5 degrees.
Since a new shaft will need to be fabricated, I have also decided to go a little overboard and opt for a carbon fiber tube. This may be a little over kill, but I am not taking any chances. In fact, Frank felt that my problems can be solved by using a driveshaft made from aluminum. However, a CF driveshaft is lighter than aluminum and offers plenty of torque capacity. Using a carbon fiber driveshaft also tends to significantly lessen the noise generated by the driveline. In some ways its like Dynomat for the driveline. I had the opportunity to drive a friends RX7 with a carbon driveshaft and it felt amazing. When cycling the driveline from load to coast the sensation was like there was a piece of plastic between the rear and and the transmission. It was a firm feeling, yet it lacked the sharpness that is felt with metal components. It was quite amazing.
With my current combination of gears and tire size the driveshaft will be spinning 3675 RPM at 80mph. While this doesn't seem like a lot, when you consider that my old driveshaft was made from mild steel and was 3.5" in diameter, the forces that were generated by such a heavy shaft were significant, even with a properly balanced driveshaft. The DSS has recently installed a new balancing machine that has the ability to spin a shaft to 9500RPM. They have been working with some NASCAR teams to solve some of the driveline issues that they face. Keep in mind that NASCAR race cars operate with the driveline spinning anywhere from 7500-9600RPM. Balancing driveshafts at that speed is a whole different ballgame than your typical 1000 RPM balance job at your local driveline shop.
The resulting driveshaft will be very similar to the shaft that they sell for 2010+ Camaros.

Instead of the billet adapters that are seen in the picture, my shaft will be connected to a modified slip yoke. The rest should be very similar. The finished shaft should be about 17 pounds with the slip yoke. Here are pictures of the components that are used in making the driveshaft. The parts on the left are used for carbon shafts, and the parts on the right are for aluminum shafts:

The bars that mate with the CV are 30 spline and are made out of a high tech 4130 alloy. The dimensions are similar to a Viper T56 output shaft. DSS has gone to great lengths to validate all the components that are used in making the CF driveshafts. This includes destructive testing, which few manufacturers ever do:

As you can see, the 1350 u-joint failed before the tube or the aluminum yoke. I feel very confident that this shaft will outlast every other component in my driveline. I can't wait....
Andrew
With road trips planned for the summer, I once again turned to a problem that has plagued my car since day one. Despite numerous efforts I have been unable to completely eliminate the high speed vibration that my car exhibits at speeds about 75 mph. It's really frustrating on long highway trips, because the car feels amazing cruising at speeds between 75 and 80 mph.
I have already posted what my thoughts are regarding the rear end position. I will be swapping out the current rear upper control arms for ones made by RideTech. I firmly believe that while the rear end position may not be entirely responsible for my vibration, it is certainly a factor. I will also be doing other driveline upgrades at the same time. What I have planned may be a little overboard, but I believe that it will completely eliminate any driveline alignment and vibration issues in the future. Here is the plan....
The first step is to get a rear pinion yoke that is machined with the kind of tolerances that are required to achieve smooth operation at sustained high speeds. I chose a 1350 billet yoke from Mark Williams:

With the rear taken care of, the next item to tackle is the driveshaft. There are many fine companies that make driveshafts, but given my alignment issues, I wanted to pick a vendor that was able to offer something unique. I have worked with Frank at The DriveShaft Shop (DSS) in the past when I needed custom axles for my RX7. Frank has always been attentive to my needs and has provided a quality product that has met and exceeded my expectations. The DSS is widely known in the sport compact world for making bullet proof CV axles, and recently they have also been doing some innovative work on the many modern muscle cars that use independent rear suspensions. Cars like the new Camaro, Dodge Charger, GTOs, and Cadillac CTS-V are rear drive, high HP, and heavy. That combination is the perfect storm for breaking driveline components, and DSS has stepped up to the plate with upgraded CV shafts, driveshafts, and complete 9" IRS swap packages.
After deliberating with Frank about my GTO and the issues that I am having we came up with a very elegant solution. Frank will make me a custom driveshaft with a CV joint in the front. People in the 4x4 world have used double cardon CV joint driveshafts for a long time to deal with extreme driveline angles. But double cardon joints are bulky and heavy, and just didn't seem appropriate for a car. What will be used in the front is a 6 ball, Porsche 930 style CV. Like this:
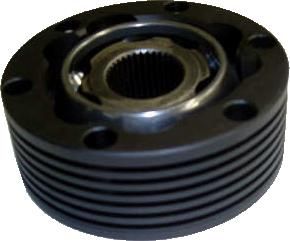
CV joints are designed to operate at high speeds and at extreme operating angles. Furthermore, there is no need to match the front and rear angles, as you need with a shaft that uses u-joints on both ends. With the CV joint in the front I will adjust my pinion angle so that the pinion and the driveshaft have almost a zero working angle. A slight angle is required only to make sure that the needles in the u-joint caps get lubricated. The rear working angle will be less than .5 degrees.
Since a new shaft will need to be fabricated, I have also decided to go a little overboard and opt for a carbon fiber tube. This may be a little over kill, but I am not taking any chances. In fact, Frank felt that my problems can be solved by using a driveshaft made from aluminum. However, a CF driveshaft is lighter than aluminum and offers plenty of torque capacity. Using a carbon fiber driveshaft also tends to significantly lessen the noise generated by the driveline. In some ways its like Dynomat for the driveline. I had the opportunity to drive a friends RX7 with a carbon driveshaft and it felt amazing. When cycling the driveline from load to coast the sensation was like there was a piece of plastic between the rear and and the transmission. It was a firm feeling, yet it lacked the sharpness that is felt with metal components. It was quite amazing.
With my current combination of gears and tire size the driveshaft will be spinning 3675 RPM at 80mph. While this doesn't seem like a lot, when you consider that my old driveshaft was made from mild steel and was 3.5" in diameter, the forces that were generated by such a heavy shaft were significant, even with a properly balanced driveshaft. The DSS has recently installed a new balancing machine that has the ability to spin a shaft to 9500RPM. They have been working with some NASCAR teams to solve some of the driveline issues that they face. Keep in mind that NASCAR race cars operate with the driveline spinning anywhere from 7500-9600RPM. Balancing driveshafts at that speed is a whole different ballgame than your typical 1000 RPM balance job at your local driveline shop.
The resulting driveshaft will be very similar to the shaft that they sell for 2010+ Camaros.

Instead of the billet adapters that are seen in the picture, my shaft will be connected to a modified slip yoke. The rest should be very similar. The finished shaft should be about 17 pounds with the slip yoke. Here are pictures of the components that are used in making the driveshaft. The parts on the left are used for carbon shafts, and the parts on the right are for aluminum shafts:

The bars that mate with the CV are 30 spline and are made out of a high tech 4130 alloy. The dimensions are similar to a Viper T56 output shaft. DSS has gone to great lengths to validate all the components that are used in making the CF driveshafts. This includes destructive testing, which few manufacturers ever do:

As you can see, the 1350 u-joint failed before the tube or the aluminum yoke. I feel very confident that this shaft will outlast every other component in my driveline. I can't wait....
Andrew
#369
TECH Fanatic
iTrader: (15)
Join Date: Jun 2006
Location: Janesville WI
Posts: 1,155
Likes: 0
Received 0 Likes
on
0 Posts


Cool stuff!
I read the text of your post on my phone (subscription email), but came to the computer for the pics. Seems like a worthwhile place to spend some money. I will file this info away for when I get back to my Buick project.
I'm a little depressed to know the L92 has been on a stand for 3 years now...
I read the text of your post on my phone (subscription email), but came to the computer for the pics. Seems like a worthwhile place to spend some money. I will file this info away for when I get back to my Buick project.
I'm a little depressed to know the L92 has been on a stand for 3 years now...
#370
TECH Senior Member
Thread Starter
iTrader: (7)

Cool stuff!
I read the text of your post on my phone (subscription email), but came to the computer for the pics. Seems like a worthwhile place to spend some money. I will file this info away for when I get back to my Buick project.
I'm a little depressed to know the L92 has been on a stand for 3 years now...
I read the text of your post on my phone (subscription email), but came to the computer for the pics. Seems like a worthwhile place to spend some money. I will file this info away for when I get back to my Buick project.
I'm a little depressed to know the L92 has been on a stand for 3 years now...
Andrew
#372
TECH Senior Member
Thread Starter
iTrader: (7)

It has an equally impressive price tag (about $1450). I know that is a lot of money, considering that I have already had 2 different driveshafts in the car and I have gone through 2 slip yokes and a pinion yoke. Had I done this from the start, I would have spent way less in the long run. Also keep in mind that in that price there is about $200 in labor to make a custom slip yoke. I am hoping that either DSS or another vendor like Mark Williams of Strange, will step up to the plate and offer slip yokes with the CV heads. The CV head style yoke should be easier to manufacture than a u-joint style yoke.
The first part of the driveline project arrived yesterday. The Mark Williams billet pinion yoke is a work of art. There are numerous machined surfaces that can be used to measure runout.


Andrew
The first part of the driveline project arrived yesterday. The Mark Williams billet pinion yoke is a work of art. There are numerous machined surfaces that can be used to measure runout.


Andrew
#373
TECH Senior Member
Thread Starter
iTrader: (7)

I am once again impressed by Frank at The Driveshaft Shop. He had the yoke done by last Friday and today he was able to have it black oxide coating applied to it and have pictures taken.
Here is the modified Spicer yoke:



The gold colored part is a cap that keeps the grease from leaking out the back of the CV:

This is a detailed shot of the modified yoke with the CV and front of the driveshaft:

Finally, a shot of the complete assembly. Interestingly, Frank was building a shaft just like mine for another project that had similar driveline alignment issues. It's a custom 1961 Corvette that will get a monster twin turbo engine.
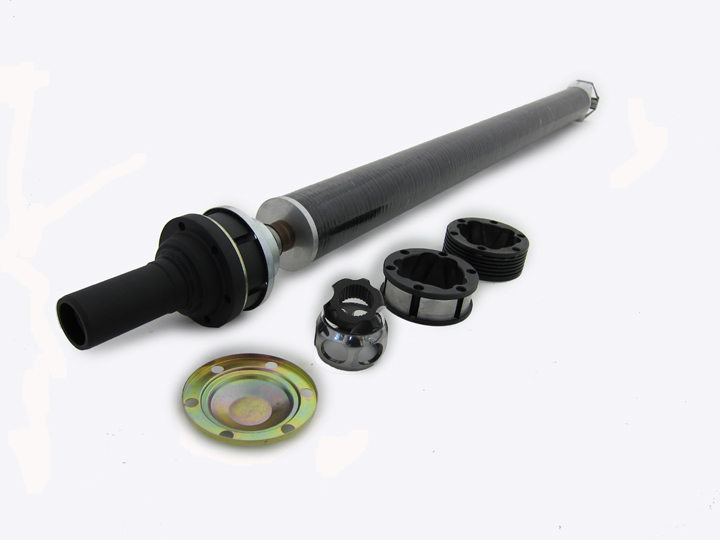
Frank will send me the slip yoke so that I can give him the final measurement for the driveshaft.
Andrew
Here is the modified Spicer yoke:



The gold colored part is a cap that keeps the grease from leaking out the back of the CV:

This is a detailed shot of the modified yoke with the CV and front of the driveshaft:

Finally, a shot of the complete assembly. Interestingly, Frank was building a shaft just like mine for another project that had similar driveline alignment issues. It's a custom 1961 Corvette that will get a monster twin turbo engine.
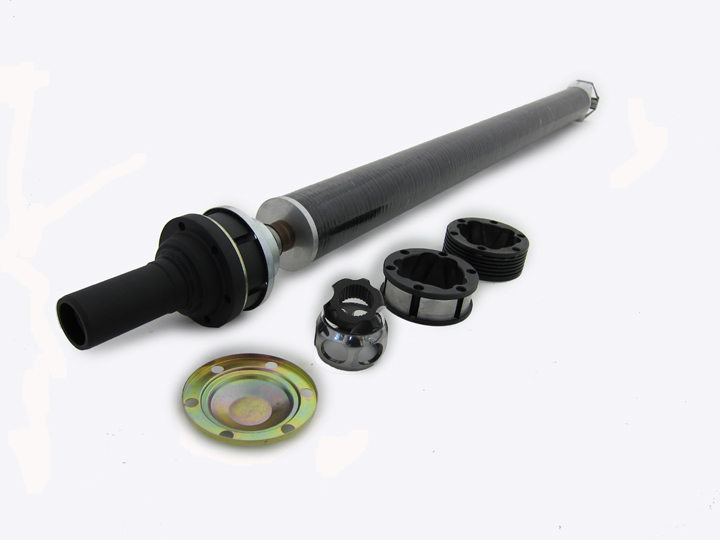
Frank will send me the slip yoke so that I can give him the final measurement for the driveshaft.
Andrew
#375
TECH Senior Member
Thread Starter
iTrader: (7)

The carbon fiber tube negates the need for a two-piece shaft. The critical speed for a 54" CF shaft is over 8000 RPM. My car will never get that that high.
Andrew
#377
TECH Senior Member
Thread Starter
iTrader: (7)

It's $1450 total with the CF tube. I think the problem could have been solved with an aluminum tube, but I didn't want to take the chance.
Using a two piece shaft actually would not solve the driveline angle issues, but it would certainly help with the length issue.
Andrew
Using a two piece shaft actually would not solve the driveline angle issues, but it would certainly help with the length issue.
Andrew
#378

I bought the TBSS pedal and it is nowhere near as easy to install as the monte pedal. I had to cut it and now will take it to get re-welded and then make a bracket to install it.
Thanks for the info.
#379
TECH Senior Member
Thread Starter
iTrader: (7)

Hmmm interesting. Speartech told me that I absolutely had to use the TBSS throttle pedal with my setup. He seemed very put off that I would suggest that others had used the Monte pedal. The TBSS uses the E67 also.
I bought the TBSS pedal and it is nowhere near as easy to install as the monte pedal. I had to cut it and now will take it to get re-welded and then make a bracket to install it.
Thanks for the info.
I bought the TBSS pedal and it is nowhere near as easy to install as the monte pedal. I had to cut it and now will take it to get re-welded and then make a bracket to install it.
Thanks for the info.
http://www.pro-touring.com/showthrea...-6l90-Chevelle
Andrew
#380
TECH Senior Member
Thread Starter
iTrader: (7)

I am getting my transmission back today and hopefully install it on Friday. Once the transmission is installed I can measure for the driveshaft length and have the DSS build the shaft. I am very excited to get the car on the road again.
Andrew
Andrew