Simple yet Strong. 550/500 418"/243/Fast 102
#41
TECH Fanatic
Join Date: Jun 2006
Location: Hayward CA
Posts: 1,326
Likes: 0
Received 0 Likes
on
0 Posts


What block was used?
I normally don't post many engine combinations here anymore, but this one surprised me for sure. A lot of attention to detail was spent in the planning stages of this build so that the customer could capitalize on parts he already had and make the most of them.
Run down on the combination:
C5 Corvette platform with TR-6060 swap and 4.10 differential
-4.080" bore
-4.0" stroke
-6.125" rod length
-11.6:1 Static Compression
-Livernois Stage 3 243 heads milled .030" additional port work performed by Thompson Motorsports
-Comp Ultra Gold 1.7 ratio rockers
-PAC 1207X springs 1.72" installed height 190psi seated /475psi open
-Custom Trend 5/16" dual tapered 3/8" diameter .135" wall 7.32" length push rods
-Comp Cams "Short Travel" hydraulic roller lifters @.030" pre-load
-Custom Tick Performance Cam Motion 247/251 .660/.640 112+2 camshaft with Tick Performance proprietary lobe design
-Fast 102 unported
-NW 102 unported
-Kooks 1.75" x 3.0" long tube headers
-Kooks Off Road 3" X-pipe
-Corsa Tiger Shark 2.5" cat-back exhaust
Shout out to Frank@Corvette World in Dallas, TX and Kyle@Thompson Motorsports as well. Two great guys to work with in this industry.
STD graph(SAE it made 535/495):
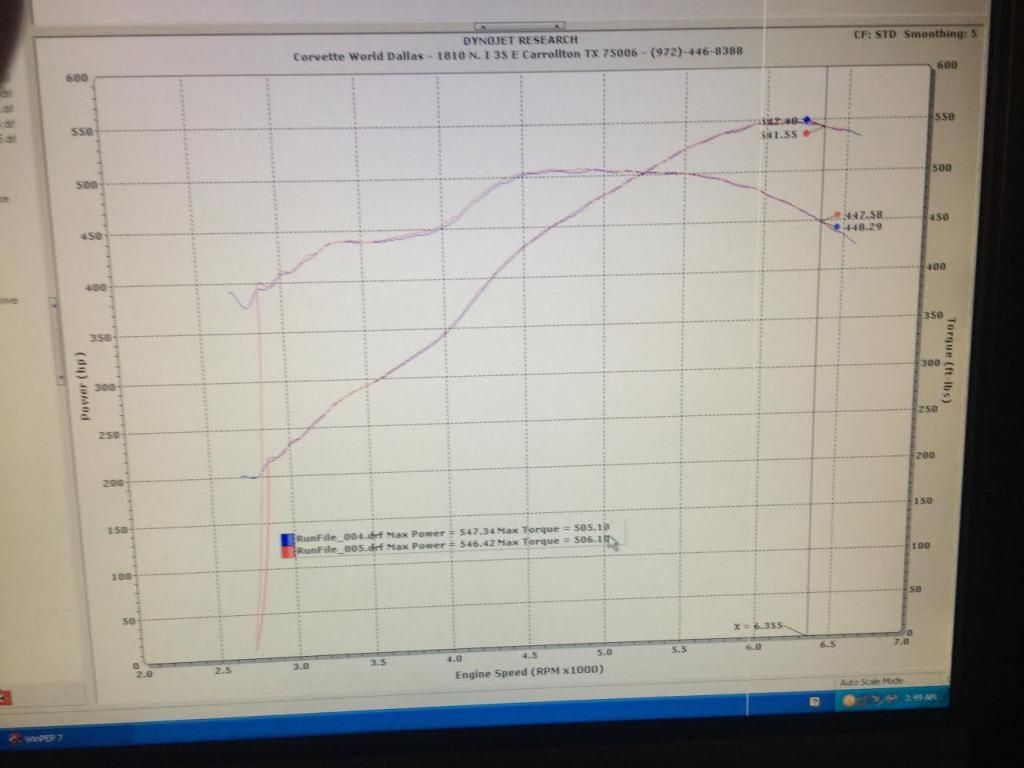
I know it's not outrageous HP/TQ figures, but what impressed me the most was that this was done with stock casting 243 heads albeit worked over and 1.75" primary diameter long tube headers.
I was also impressed by the torque this combination produces. 400rwtq from jump street, 450rwtq@4000rpm and it holds 500rwtq for 1000rpm. Should be a very fun street car rowing gears!
Run down on the combination:
C5 Corvette platform with TR-6060 swap and 4.10 differential
-4.080" bore
-4.0" stroke
-6.125" rod length
-11.6:1 Static Compression
-Livernois Stage 3 243 heads milled .030" additional port work performed by Thompson Motorsports
-Comp Ultra Gold 1.7 ratio rockers
-PAC 1207X springs 1.72" installed height 190psi seated /475psi open
-Custom Trend 5/16" dual tapered 3/8" diameter .135" wall 7.32" length push rods
-Comp Cams "Short Travel" hydraulic roller lifters @.030" pre-load
-Custom Tick Performance Cam Motion 247/251 .660/.640 112+2 camshaft with Tick Performance proprietary lobe design
-Fast 102 unported
-NW 102 unported
-Kooks 1.75" x 3.0" long tube headers
-Kooks Off Road 3" X-pipe
-Corsa Tiger Shark 2.5" cat-back exhaust
Shout out to Frank@Corvette World in Dallas, TX and Kyle@Thompson Motorsports as well. Two great guys to work with in this industry.
STD graph(SAE it made 535/495):
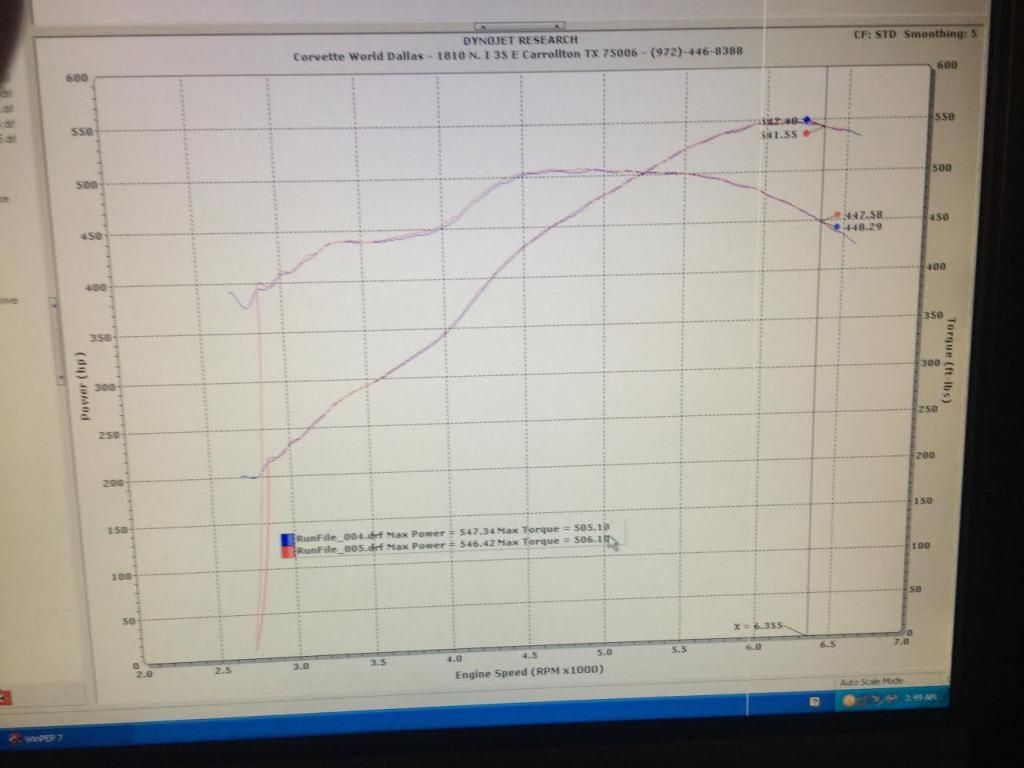
I know it's not outrageous HP/TQ figures, but what impressed me the most was that this was done with stock casting 243 heads albeit worked over and 1.75" primary diameter long tube headers.
I was also impressed by the torque this combination produces. 400rwtq from jump street, 450rwtq@4000rpm and it holds 500rwtq for 1000rpm. Should be a very fun street car rowing gears!
#47

martin.is there a way we could get the same power without 660 lift cam.i have tea stage 2 heads and the springs are only 650 lift,now if i have to change springs i would but the pac 1207x are 700 lift how would these springs do with alot of milage.i see someone put it should be 640hp@fly wheel thats really stout. martin what u think
Do you know what the open and seated pressures are on the springs you're currently running?
#49

If the head you're using flows laminar well past .700" lift and the valve train is built to work with .650-.675" lift I don't see any reason not to take advantage of the added HP/TQ that could be made.
Do you know what the open and seated pressures are on the springs you're currently running?
Do you know what the open and seated pressures are on the springs you're currently running?
#51
FormerVendor
iTrader: (1)

No reason to feel bad. We have tons of customers out there with our excelent performing heads. This is just another case that's getting some light shed on it. We are happy this car is making good power and glad to hear your is running well. It's hard to beat the flow #'s and workmanship for the $
#52

Won't you get much better life out of the springs and valvetrain if you keep it under 630 lift though? even if the springs are rated for 650-675? My springs are the PRC EHT .675 springs, stock rockers with trunion upgrade and ls7 lifters , but i wanted to stay under 630 for that reason. Was i wrong to have not gone with a 660 lift cam then? would the springs, rockers and lifters last just as long regardless?
The only thing I can possibly see that would get worn out faster by added lift are the valve guides and valve stems as there is more lift to travel up and down.
Lifters, push rods, valve springs, rockers are stressed much higher in my opinion from accelerating those parts up to max accel/velocity and then bringing them to a stop than they are by lifting the valve further.
I have my own lobe designs that utilize a lot of lift, but are extremely smooth and will RPM very well. These lobes are an excellent example of just that. Look how the power carries even with heavy roller rockers and what would at first glance judging by the lift seem to be a very aggressive lobe.
In reality this lobe has a much slower opening and seating ramp due to manipulation of duration that has been designed into the lobe between certain lobe lift values. This slows down the acceleration of the lifter and thus the valve motion.
Last edited by Sales@Tick; 12-19-2014 at 07:48 AM.
#54

I understand what you are saying about the limit of intake manifold flow but lets look at it another way. If the intake limits flow to 280cfm at say .450" lift, which is where most ported heads flow at least 280cfm, then the longer we leave the valve open the more time we have to cram 280cfm in cylinder. The piston/port velocity isn't really moving very fast for the first .350-.400 lift or so, possibly up to .500 lift depending on when your intake valve opens. After that is almost a vertical climb of velocity to peak lift. So when the cylinder is at it's peak filling capability you need to keep the intake valve open. I would rather cram a capped 280cfm into a cylinder over a longer period of time then shutting it off when it hits 280cfm. The argument is always to bump up the mid lift flow since the valve passes that point twice. If we are capped to a certain CFM by our intake or head flow then we are essentially doing the same thing with keeping the valve open longer by using higher lifts. We could do this same thing with duration but duration leads to all sorts of other problems with drivability and where an engine makes power ect, ect. If the intake manifold was a hard and fast wall of cfm then we wouldn't gain any power from ported heads that flow over what the intake manifold will flow.
A comparison would be running a big old cam on LS6 heads. The head caps out at .500 lift at 260cfm. Diminishing return logic says to cap lift at .500 lift and then manipulate durationssince the head literally stalls by .550 lift. But for some reason, bigger cams make more power with the stock heads.
In the end I always suggest a ported intake manifold and TB (of any brand or type) to get the most out of heads and cam on any car I do.
Last edited by Pray; 12-19-2014 at 07:24 AM.
#55

I will let the smart people on here explain it better but here is how I see the issue of diminishing returns.
I understand what you are saying about the limit of intake manifold flow but lets look at it another way. If the intake limits flow to 280cfm at say .450" lift, which is where most ported heads flow at least 280cfm, then the longer we leave the valve open the more time we have to cram 280cfm in cylinder. The piston/port velocity isn't really moving very fast for the first .350-.400 lift or so, possibly up to .500 lift depending on when your intake valve opens. After that is almost a vertical climb of velocity to peak lift. So when the cylinder is at it's peak filling capability you need to keep the intake valve open. I would rather cram a capped 280cfm into a cylinder over a longer period of time then shutting it off when it hits 280cfm. The argument is always to bump up the mid lift flow since the valve passes that point twice. If we are capped to a certain CFM by our intake or head flow then we are essentially doing the same thing with keeping the valve open longer by using higher lifts. We could do this same thing with duration but duration leads to all sorts of other problems with drivability and where an engine makes power ect, ect. If the intake manifold was a hard and fast wall of cfm then we wouldn't gain any power from ported heads that flow over what the intake manifold will flow.
A comparison would be running a big old cam on LS6 heads. The head caps out at .500 lift at 260cfm. Diminishing return logic says to cap lift at .500 lift and then manipulate durationssince the head literally stalls by .550 lift. But for some reason, bigger cams make more power with the stock heads.
In the end I always suggest a ported intake manifold and TB (of any brand or type) to get the most out of heads and cam on any car I do.
I understand what you are saying about the limit of intake manifold flow but lets look at it another way. If the intake limits flow to 280cfm at say .450" lift, which is where most ported heads flow at least 280cfm, then the longer we leave the valve open the more time we have to cram 280cfm in cylinder. The piston/port velocity isn't really moving very fast for the first .350-.400 lift or so, possibly up to .500 lift depending on when your intake valve opens. After that is almost a vertical climb of velocity to peak lift. So when the cylinder is at it's peak filling capability you need to keep the intake valve open. I would rather cram a capped 280cfm into a cylinder over a longer period of time then shutting it off when it hits 280cfm. The argument is always to bump up the mid lift flow since the valve passes that point twice. If we are capped to a certain CFM by our intake or head flow then we are essentially doing the same thing with keeping the valve open longer by using higher lifts. We could do this same thing with duration but duration leads to all sorts of other problems with drivability and where an engine makes power ect, ect. If the intake manifold was a hard and fast wall of cfm then we wouldn't gain any power from ported heads that flow over what the intake manifold will flow.
A comparison would be running a big old cam on LS6 heads. The head caps out at .500 lift at 260cfm. Diminishing return logic says to cap lift at .500 lift and then manipulate durationssince the head literally stalls by .550 lift. But for some reason, bigger cams make more power with the stock heads.
In the end I always suggest a ported intake manifold and TB (of any brand or type) to get the most out of heads and cam on any car I do.
The more high lift area present from adding lift, the more duration(area) the lobe has at higher lift. This will give the induction system more area and time to fill the cylinder while the demand in the cylinder for airflow is greatest. The induction system has the highest capability of meeting that airflow demand at a higher lift since the intake port flows more air at higher lift. The piston really doesn't start to demand a lot of airflow until the valve is lifted .300"-.400". This airflow demand is a direct result of piston speed and piston position in the cylinder.
When the piston is @ TDC with this camshaft, the valve is already open roughly .200" of an inch. When the piston reaches 70-75 degrees ATDC, this is where piston CFM demand is greatest. CFM demand is greatest at this piston position due to the piston speed attained. As a result of the piston speed attained at this piston position, this is where the depression(vacuum) in the cylinder reaches its highest point. By the time this happens, the valve is open almost .550" of an inch.
As you can see, the valve goes from .200" lift to .550" lift in 70-75 crank degrees. At BDC on the intake stroke with this camshaft the valve is now on the closing ramp, but it's still open roughly .500" of an inch. This shows how many crank degrees the valve is above .500" lift on the intake stroke. From 70* ATDC to 180* ATDC 110 crank degrees the valve is open for more than .500" lift. It only takes 70-75 crank degrees though for it to go from .200" to .550" showing how important it is for the valve to get the hell out of the way and get to the higher lift regions where more airflow is more available to meet the demand created by the piston in the cylinder.
This should also show how low and mid lift flow is made out to be more important than it really is. I do consider .400-.500" to still be "mid lift", but .100, .200, .300 really isn't THAT important, again at least not as important as it is made out to be. I'd say .300" is starting to have good merit in a street application, but in a race application it doesn't carry much if any weight at all. I know some head porters that don't even turn the bench on until .200" lift.
What I have said here should make it clear that if the head is still laminar at higher lifts such as above .600" and is not turbulent, using more valve lift will always make more power. If the head stalls or is turbulent above .600" lift, adding more lift isn't going to make much if any more power and you'd have to fix the intake port first. Giving the engine more curtain area(function of lift and valve diameter) when the piston is demanding these high amounts of airflow is always going to make more power.
Now that you can visualize how long the valve is open above .400-.500" lift on the intake stroke you can see how important higher lift flow and giving the valve more area at these higher lifts can benefit power production even if the intake is a restriction. Adding more peak lift creates more high lift area so that the valve dwells for more duration at these higher lifts giving the induction system more time and area to utilize its higher flow capabilities to fill the cylinder. If the head can supply it, and doesn't choke, spit, spudder, stall or go turbulent, the valve train is up to the task and the lobe design is stable...I will always use more lift.
Hope this helps.
#56

Wonder where I get all this good information from. Lol. See, I do listen.
One thing I was looking at this morning though was port velocity vs. Piston position as it pertains to the exhaust valve and flow. The article was saying that the exhaust can create negative pressure that can accelerate the intake charge to 120fps with the piston at TDC. If that is the case I can see where .50-.150 lift numbers could come into effect to allow the largest advantage to be taken of the low pressure vacuum. I guess seat and chamber shape could also effect this more than an actual cfm value but the two could be one in the same. The article said that if IVO and EVC were not sorted, 100% VE could not be achieved since the low pressure/vacuum time had been passed.
One thing I was looking at this morning though was port velocity vs. Piston position as it pertains to the exhaust valve and flow. The article was saying that the exhaust can create negative pressure that can accelerate the intake charge to 120fps with the piston at TDC. If that is the case I can see where .50-.150 lift numbers could come into effect to allow the largest advantage to be taken of the low pressure vacuum. I guess seat and chamber shape could also effect this more than an actual cfm value but the two could be one in the same. The article said that if IVO and EVC were not sorted, 100% VE could not be achieved since the low pressure/vacuum time had been passed.
#57
Moderator
iTrader: (9)

Martin,
I had a discussion with a well known and respected individual the other day as I am changing the cam in my truck (you know him and I have seen your replies to his comments, you have shown a lot of respect towards him as well).
I am having something ground that I think will work good (259/274 LSK/LSL) but he has his concerns, not so much with the valve events, but more the lobes I chose. He doesn't feel I will gain much from the added lift. So, he is sending me one too and I will be doing back to back dyno testing same day.
Even though my heads flow fairly well up to .700 (https://ls1tech.com/forums/generatio...take-well.html) He feels the added lift will put more parasitic loss and my net gain over my existing will be negligible.
I'd like to hear your thoughts on this.
Same spring .675 PRC
Same turned down LS3 valve
3/8 push rod
Same valve events
IVO 20.5
IVC 58.5
EVO 74
EVC 20
With my heads on a 13-1cr 418" motor and lift being the only difference (.675 vs .625 on the intake) what gains do you think would show?
I had a discussion with a well known and respected individual the other day as I am changing the cam in my truck (you know him and I have seen your replies to his comments, you have shown a lot of respect towards him as well).
I am having something ground that I think will work good (259/274 LSK/LSL) but he has his concerns, not so much with the valve events, but more the lobes I chose. He doesn't feel I will gain much from the added lift. So, he is sending me one too and I will be doing back to back dyno testing same day.
Even though my heads flow fairly well up to .700 (https://ls1tech.com/forums/generatio...take-well.html) He feels the added lift will put more parasitic loss and my net gain over my existing will be negligible.
I'd like to hear your thoughts on this.
Same spring .675 PRC
Same turned down LS3 valve
3/8 push rod
Same valve events
IVO 20.5
IVC 58.5
EVO 74
EVC 20
With my heads on a 13-1cr 418" motor and lift being the only difference (.675 vs .625 on the intake) what gains do you think would show?
#58

Wonder where I get all this good information from. Lol. See, I do listen.
One thing I was looking at this morning though was port velocity vs. Piston position as it pertains to the exhaust valve and flow. The article was saying that the exhaust can create negative pressure that can accelerate the intake charge to 120fps with the piston at TDC. If that is the case I can see where .50-.150 lift numbers could come into effect to allow the largest advantage to be taken of the low pressure vacuum. I guess seat and chamber shape could also effect this more than an actual cfm value but the two could be one in the same. The article said that if IVO and EVC were not sorted, 100% VE could not be achieved since the low pressure/vacuum time had been passed.
One thing I was looking at this morning though was port velocity vs. Piston position as it pertains to the exhaust valve and flow. The article was saying that the exhaust can create negative pressure that can accelerate the intake charge to 120fps with the piston at TDC. If that is the case I can see where .50-.150 lift numbers could come into effect to allow the largest advantage to be taken of the low pressure vacuum. I guess seat and chamber shape could also effect this more than an actual cfm value but the two could be one in the same. The article said that if IVO and EVC were not sorted, 100% VE could not be achieved since the low pressure/vacuum time had been passed.
With a well tuned primary length and collector design, it is possible to drop the pressure in the cylinder below atmospheric during the overlap event at certain RPM's where the engine comes into tune. This allows the now higher pressure intake charge to accelerate in the intake port and into the cylinder during overlap while the piston is on the exhaust stroke. That is before it's even started to draw on the intake stroke and created any depression in the cylinder.
Without harnessing this phenomenon, a N/A engine will never approach or exceed 100% VE. Since we can jump start cylinder fill and velocity in the intake port before the piston has created any depression, VE% can now increase much higher than it could before. If you read my thread I mentioned, I show some in cylinder pressure diagrams that show how an engine running out of tune(where no negative pressure exists in the cylinder during overlap) cannot even come close to achieving the same cylinder pressure as an engine running in tune.
The same can be said about an engine that uses no overlap, or very little overlap as well.
As far as intake flow at .050-.150, you don't want a lot of intake flow at these lifts...at least IMO. The more the port flows forward at this lift, the better it will flow backwards. There are things you can do with back cuts, seat angles and chamber shape to limit this, but a port that flows really well at low lift doesn't need nearly as much overlap as a head that doesn't. If you used a lot of overlap on a head that flows well at low lift, you can run into issues with reversion during the overlap event. Another unwanted trait of a cylinder head that flows well at low lift is reversion on the IC event. Not something we want if we're to trap as much mixture before the IC event as possible.
Standing up the valve job with steeper angles helps to kill off flow at low lift which is something a lot of head porters employ, especially on the exhaust valve job.
Martin,
I had a discussion with a well known and respected individual the other day as I am changing the cam in my truck (you know him and I have seen your replies to his comments, you have shown a lot of respect towards him as well).
I am having something ground that I think will work good (259/274 LSK/LSL) but he has his concerns, not so much with the valve events, but more the lobes I chose. He doesn't feel I will gain much from the added lift. So, he is sending me one too and I will be doing back to back dyno testing same day.
Even though my heads flow fairly well up to .700 (https://ls1tech.com/forums/generatio...take-well.html) He feels the added lift will put more parasitic loss and my net gain over my existing will be negligible.
I'd like to hear your thoughts on this.
Same spring .675 PRC
Same turned down LS3 valve
3/8 push rod
Same valve events
IVO 20.5
IVC 58.5
EVO 74
EVC 20
With my heads on a 13-1cr 418" motor and lift being the only difference (.675 vs .625 on the intake) what gains do you think would show?
I had a discussion with a well known and respected individual the other day as I am changing the cam in my truck (you know him and I have seen your replies to his comments, you have shown a lot of respect towards him as well).
I am having something ground that I think will work good (259/274 LSK/LSL) but he has his concerns, not so much with the valve events, but more the lobes I chose. He doesn't feel I will gain much from the added lift. So, he is sending me one too and I will be doing back to back dyno testing same day.
Even though my heads flow fairly well up to .700 (https://ls1tech.com/forums/generatio...take-well.html) He feels the added lift will put more parasitic loss and my net gain over my existing will be negligible.
I'd like to hear your thoughts on this.
Same spring .675 PRC
Same turned down LS3 valve
3/8 push rod
Same valve events
IVO 20.5
IVC 58.5
EVO 74
EVC 20
With my heads on a 13-1cr 418" motor and lift being the only difference (.675 vs .625 on the intake) what gains do you think would show?
I would use a lobe with at least 53-56* cam duration between .006 and .050 lobe lift. Something like a HUC, QXX, QNX, EHX etc. would be my preference. All of those lobes still have exceptional high lift cylinder fill area and will make MUCH more power than the LSK/LSL lobes at high RPM. There is a big difference between a high lift lobe like a LSK and a high lift lobe like a QXX, QNX, high lift HUC etc. etc. etc.
I also think your IVC event is a bit too early for a 13:1 engine and you will incur pumping losses because of it. If the piston is forced to pump against a closed cylinder for too long, and the pressure inside of that cylinder is really high there is a good chance you'll not gain the full benefit from the added compression if the IC event occurs too early. You'll gain something versus a lower compression deal, but if you really want that added compression to make more torque and HP, I'd close the intake later.
Do you have a flow sheet that shows airflow to at least .750-.800" lift?
Also, airflow at 28" is not the same as airflow at 60", 80" or even 100" depression. A running engine will achieve much higher depression than a flow bench can, and on a running engine a port will stall or go turbulent much sooner than it will on a bench. That is why it is a good practice to use a head that flows laminar past your intended cam lift.
If your intake port flows to .700" lift, a .640" lift cam will most likely make more power than a .620" lift cam if the valve train is stable and the lobe design is good for the application. If the intake port flows to .750" lift, then it's a good line of thought that a .660" lift cam, possibly even a .675" lift cam will make more power than a .640" lift cam.
The main thing I'd do is change the lobe design to a much slower seat to seat ramp rate. That doesn't mean you have to lower the valve lift, but the valve train has to be under control or else valve timing will never operate around the parameters it was designed.
If all of this comes together as designed, and the head continues to flow laminar at or above .700" lift I could see a gain of 10-20hp over your current camshaft. If the head is not laminar and goes turbulent at or before .700" lift, I don't see you gaining any power at all. Maybe 3-5hp if that.
#59
Moderator
iTrader: (9)

I would not use those lobes. In a high RPM hydraulic roller application I do everything I can to slow down the ramp rate of the lobe so that stability is great even at high RPM. Keeping a hydraulic stable is like skating on ice. You can do it with great control, but if you get out of sync or too aggressive you'll fall and bust your hind end.

I would use a lobe with at least 53-56* cam duration between .006 and .050 lobe lift. Something like a HUC, QXX, QNX, EHX etc. would be my preference. All of those lobes still have exceptional high lift cylinder fill area and will make MUCH more power than the LSK/LSL lobes at high RPM. There is a big difference between a high lift lobe like a LSK and a high lift lobe like a QXX, QNX, high lift HUC etc. etc. etc.
I could try retarding the cam 2 and even 4 degrees on another dyno session to see what that does. Doing this will obviously change the EVO from 74 to 72 or even 70, but I think that will have less effect than the change in IVC positioning.
Also, airflow at 28" is not the same as airflow at 60", 80" or even 100" depression. A running engine will achieve much higher depression than a flow bench can, and on a running engine a port will stall or go turbulent much sooner than it will on a bench. That is why it is a good practice to use a head that flows laminar past your intended cam lift.
No intake 343.8 to 365
Intake 330.5 to 337
If the valvetrain is stable, would the increased duration seen at all lifts >.050 not help to fill the Cyl?
If all of this comes together as designed, and the head continues to flow laminar at or above .700" lift I could see a gain of 10-20hp over your current camshaft. If the head is not laminar and goes turbulent at or before .700" lift, I don't see you gaining any power at all. Maybe 3-5hp if that.
Understood.
As always, I enjoy these discussions with you and the others like Mamo, Tooley, Patrick etc..
Shaun
#60
Moderator
iTrader: (9)

Let me add one comment on the IVC. The other person I am referring to thought the truck was a bit heavier than it is and by moving the IVC sooner I could potentially create more low end TQ netting a better 60' which could potentially provide a better overall ET.
I did explain that with the 2-step set at 3,500 the verter only flashes to 4,600 (5k with the 2-step out of the way). I am sure that with a NA converter there is a much better 60' just as it sits.
I did explain that with the 2-step set at 3,500 the verter only flashes to 4,600 (5k with the 2-step out of the way). I am sure that with a NA converter there is a much better 60' just as it sits.