tig or mig
#22
12 Second Club
iTrader: (10)
Join Date: Dec 2006
Location: Fannett, Tx
Posts: 1,316
Likes: 0
Received 0 Likes
on
0 Posts


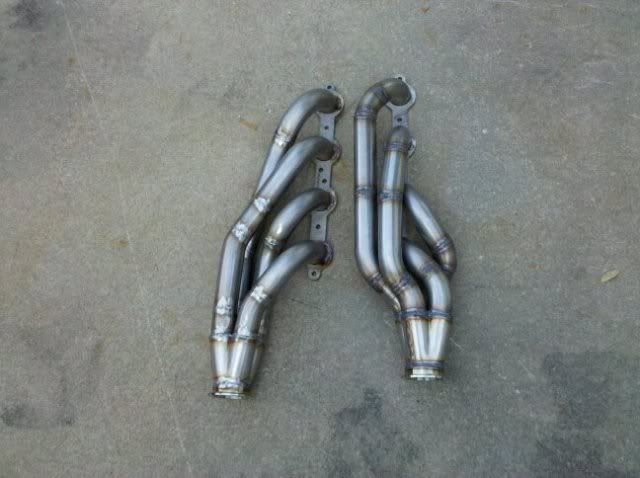
Last edited by Sluggish; 06-25-2011 at 10:45 AM.
#23

I bought an Everlast Powermaster 205 about 2 years ago. Fantastic machine! It stick welds, tig welds, and plasma cuts. The machine works great, is portable enough to move around easily, and has been very dependable. I do a lot of welding, and so far I have had absolutely no problems with it.
I got it for about $1300 with all the accessories brand new. Chinese welders have come a LONG way.
I got it for about $1300 with all the accessories brand new. Chinese welders have come a LONG way.
#26
TECH Fanatic
iTrader: (18)

I hate recommending more expensive things but in this case,
TIG IS FAR BETTER THAN MIG.
you can weld in your sunday best
if you miss the setting, you can control it easily with the foot pedal
it makes cleaner welds
it welds very quietly
no wire feed errors
can weld aluminum
TIG IS FAR BETTER THAN MIG.
you can weld in your sunday best
if you miss the setting, you can control it easily with the foot pedal
it makes cleaner welds
it welds very quietly
no wire feed errors
can weld aluminum
#28
TECH Addict
iTrader: (28)

Tig welding does require some practice, but honestly most people that tig weld are self taught or watched someone do it and tried it on their own. I watched my dad when I was 12 years old tig weld. He does it for a living on gas power turbines for Dresser Rand. I give him a call if I have a question and he gives me a recommendation. I learned and got good at it in about a month or so of trial and error. I think there is actually more room for error and more control than on a mig machine. With a foot control you can bring the amperage in more or back it off as you feel what the puddle is doing. Its not rocket science and it doesn't cost alot if you buy an older used machine. I learned on a miller cp300 machine that is still my favorite machine to weld with. It has that sweet spot that I am used to. The syncrowaves are nice machines for the money, but when it comes to aluminum I still like the old cp300 at my dads house. The amperage ramps in gradually and it just seems easier to control.
#29

TIG all the way...im in the market for one so I can do all my own welding...I hate paying for stuff that I can do myself...hell by the time you pay to get mini-tubs installed you can have a nice machine
#32
TECH Fanatic
iTrader: (18)

I bought a book lol and it recommended buying a boat load of shim stock and practicing.
the book gave guidelines on torch angle, distance,amperage, rod, tungsten type, etc, and it said practice practice practice.
I bought my tig welder without ever watching anyone weld and after 5 hours or so of welding different thicknesses of shim stock/like shim stock, and maybe a bottle of argon, I was able to weld my hotside and coldside 100%
the book gave guidelines on torch angle, distance,amperage, rod, tungsten type, etc, and it said practice practice practice.
I bought my tig welder without ever watching anyone weld and after 5 hours or so of welding different thicknesses of shim stock/like shim stock, and maybe a bottle of argon, I was able to weld my hotside and coldside 100%
#33
11 Second Club
iTrader: (43)

Forget taking a class. All you have to do is have someone experienced show you on that machine. They get the settings right and it's easy as crap after that. I bought mine and was dicking around with it and made some pretty crappy welds that I thought were good enough and then I had a guy come by and show me a thing or too and it was night and day between the setting differences. I still used the same technique though.
#34
9 Second Club

A tig would be best if you have to money. A miller syncrowave 250 is of the best machines for the money. It can be pricey, but is a nice machine. With a good tig machine you have the ability to do aluminum. With a mig aluminum requires a spool gun that is somewhat pricey. A tig welder will provide a much cleaner weld. A mig welder can be had for $1000 or less and get you a decent machine. The downside is that the weld is not as pretty as a tig and the versatility of doing different materials is not as easy as with a tig. I have a hobart 140 with a gas setup that does a good job on exhaust tubing and will weld roll cages no problem. It is good for smaller stuff, but I would like to have a tig machine that will put out 250 amps or more for heavier stuff.
And a MIG is far handier for general automotive use. Plus cheaper.
#35
9 Second Club

I hate recommending more expensive things but in this case,
TIG IS FAR BETTER THAN MIG.
you can weld in your sunday best
if you miss the setting, you can control it easily with the foot pedal
it makes cleaner welds
it welds very quietly
no wire feed errors
can weld aluminum
TIG IS FAR BETTER THAN MIG.
you can weld in your sunday best
if you miss the setting, you can control it easily with the foot pedal
it makes cleaner welds
it welds very quietly
no wire feed errors
can weld aluminum
MIG is still relatively clean. But the same safety rules apply from exposure to the arc with regards clothing.
If you get the wrong setting, just change it
Clean weld is down to preparation more so than welding method.
I doubt anyone has ever been deafened by a MIG
Wire feed errors....occasionally it may be a problem, but only very occasionally
And only if you buy a more expensive machine.
MIG is cheaper.
MIG is faster
MIG will blast a weld with less preparation if needed on unclean metal. TIG will not
MIG is one handed, so tacking the workpiece is a doddle.
And generally I'd say more versatile for automotive use.
Also easier to produce a strong clean weld with MIG with little experience.
If you are only buying one machine for the workshop, for me MIG would always be my first choice. TIG as a second unit.
Unless of course you are buying it with very specific needs in mind.
People just get obsessed with TIG for work as the welds can look all nice when done by a skilled welder. As to whether the insides of those pipes also look so good, is another matter. Backpurging is essential if the inside isnt to go all crusty. With neat fitting MIG welds, that just doesnt happen.
#36
TECH Fanatic
iTrader: (18)

Dont really think any of those make it far better ?
MIG is still relatively clean. But the same safety rules apply from exposure to the arc with regards clothing.
If you get the wrong setting, just change it
Clean weld is down to preparation more so than welding method.
I doubt anyone has ever been deafened by a MIG
Wire feed errors....occasionally it may be a problem, but only very occasionally
And only if you buy a more expensive machine.
MIG is cheaper.
MIG is faster
MIG will blast a weld with less preparation if needed on unclean metal. TIG will not
MIG is one handed, so tacking the workpiece is a doddle.
And generally I'd say more versatile for automotive use.
Also easier to produce a strong clean weld with MIG with little experience.
If you are only buying one machine for the workshop, for me MIG would always be my first choice. TIG as a second unit.
Unless of course you are buying it with very specific needs in mind.
People just get obsessed with TIG for work as the welds can look all nice when done by a skilled welder. As to whether the insides of those pipes also look so good, is another matter. Backpurging is essential if the inside isnt to go all crusty. With neat fitting MIG welds, that just doesnt happen.
MIG is still relatively clean. But the same safety rules apply from exposure to the arc with regards clothing.
If you get the wrong setting, just change it
Clean weld is down to preparation more so than welding method.
I doubt anyone has ever been deafened by a MIG
Wire feed errors....occasionally it may be a problem, but only very occasionally
And only if you buy a more expensive machine.
MIG is cheaper.
MIG is faster
MIG will blast a weld with less preparation if needed on unclean metal. TIG will not
MIG is one handed, so tacking the workpiece is a doddle.
And generally I'd say more versatile for automotive use.
Also easier to produce a strong clean weld with MIG with little experience.
If you are only buying one machine for the workshop, for me MIG would always be my first choice. TIG as a second unit.
Unless of course you are buying it with very specific needs in mind.
People just get obsessed with TIG for work as the welds can look all nice when done by a skilled welder. As to whether the insides of those pipes also look so good, is another matter. Backpurging is essential if the inside isnt to go all crusty. With neat fitting MIG welds, that just doesnt happen.
how about pulsing for thin sheet metal?
change the settings? when you are welding aluminum and the workpiece is getting hotter by the second thus requiring less input are you going to stop and wait for it to cool every 20 seconds or will you be continually changing settings at the machine? with tig you just feed less and less input at the foot pedal
nobody ever got deaf with mig. try telling that to your wife when you are welding in the middle of the night.
you never have wire feed errors with tig. with some stainless steel exhaust work (409 eg) you dont even need wire. you cant do that with a mig
tig welds look a lot better and that is important to some people.
most importantly, it is easier to learn to tig than to mig. because you have a lot more CONTROL, from the foot pedal, and you manually feed the wire as needed.
#37
TECH Addict
iTrader: (28)

Unless you are skilled with a TIG, then TIG is a waste of time. MIG is just as strong, faster and easier. And far less chance of intrusion inside the pipe ( TIG requires backpurge to ensure internals remain good )
And a MIG is far handier for general automotive use. Plus cheaper.
And a MIG is far handier for general automotive use. Plus cheaper.
#38
9 Second Club

you didnt address aluminum welding with mig. most any tig welder over 1k is set up for mig
how about pulsing for thin sheet metal?
change the settings? when you are welding aluminum and the workpiece is getting hotter by the second thus requiring less input are you going to stop and wait for it to cool every 20 seconds or will you be continually changing settings at the machine? with tig you just feed less and less input at the foot pedal
nobody ever got deaf with mig. try telling that to your wife when you are welding in the middle of the night.
you never have wire feed errors with tig. with some stainless steel exhaust work (409 eg) you dont even need wire. you cant do that with a mig
tig welds look a lot better and that is important to some people.
most importantly, it is easier to learn to tig than to mig. because you have a lot more CONTROL, from the foot pedal, and you manually feed the wire as needed.
how about pulsing for thin sheet metal?
change the settings? when you are welding aluminum and the workpiece is getting hotter by the second thus requiring less input are you going to stop and wait for it to cool every 20 seconds or will you be continually changing settings at the machine? with tig you just feed less and less input at the foot pedal
nobody ever got deaf with mig. try telling that to your wife when you are welding in the middle of the night.
you never have wire feed errors with tig. with some stainless steel exhaust work (409 eg) you dont even need wire. you cant do that with a mig
tig welds look a lot better and that is important to some people.
most importantly, it is easier to learn to tig than to mig. because you have a lot more CONTROL, from the foot pedal, and you manually feed the wire as needed.
As for strength. We arent putting together aircraft or space rockets here. Show me a car part that has failed due to actual welding technique ( ie MIG or TIG ) then I'll believe that one is actually worth having over the other.
The simple fact is, such a scenario will never happen. The person doing it might do a ***** job, but that is not down to the welding machine or style of welding.
Obviously if you need to weld aluminium then there is no question the only option is TIG.
If you can get a dual machine MIG/TIG for sensible money, then yes that would be great. But even a decent Mig here would cost around UK £600 ( circa US$900 ) and a relatively basic AC/DC TIG UK £1200 ( circa US$1800 )
Unless you opt for the really cheap chinese stuff.
For general automotive and workshop use, MIG is still no 1 for me
#40