HP vs TQ Theory
#1
Moderator
Thread Starter
iTrader: (4)
Join Date: Jul 2014
Location: My own internal universe
Posts: 10,446
Received 1,838 Likes
on
1,146 Posts


I've seen the horsepower vs torque threads, and this is not intended to be one of those. Yes, HP = TQ x RPM / 5252. And, I know how it was derived from a 1-ft lever arm and 33,000 pound feet of work per minute. So, that's not the point. You can't directly measure HP, so you measure TQ and use the equation. This is more about the underlying physics of it.
One thing we've learned is that intake runner length, intake valve timing seem to affect when the peaks are hit, so here is what I'm seeing...
1. Peak torque coincides with the highest VE's in the tuning tables. This is telling me peak torque is determined by the RPM's at which cylinder filling is the greatest?
--Torque = force x radial distance. Force = pressure x area.
--So, to put it in engine terms,
--Torque = cylinder pressure x (bore/2)^2 x pi x stroke. (check my math?)
--bore, stroke, and pi are constants, so only pressure can change.
Is it fair to say the above question is answered "yes, the RPM at which the cylinder fills the most on a single intake stroke determines peak torque rpm"?
2. Peak horsepower is a bit tougher to wrap my head around. I know the equation, but there seems to be some interaction going on between RPM and airflow. I'm going to assume a 6300 peak HP for this:
--Above 4800 (peak TQ) and below 6300 (peak HP), the effect of increasing RPM is greater than the effect of reduced cylinder fill efficiency.
--Above 6300 (peak HP), the effect of reduced cylinder fill efficiency is greater than the effect of increased RPM.
--The only thing I can come up with is that 6300 (peak HP) is the point at which total airflow per unit time is the highest. Reducing RPM reduces total airflow, reducing total power output. Increasing RPM reduces total airflow, reducing power output. I can't find a model to explain this, but I think the question here is --
Is peak HP RPM determined by peak airflow or is it something else?
3. Assuming the above two are correct, then is it fair to say that when you do things to change the power band of an engine, you're really just changing when you get peak airflow and when you get peak cylinder fill?
--Example1. Delaying IVC to move peak HP to 6600 RPM works because the this change allows total airflow to continue to increase at higher RPM?
--Example2. Moving to a single plane intake moves peak torque higher by shortening the intake runners, thus moving peak cylinder fill to a higher RPM?
--Example3. The age old SBC vs LS1 peak low end torque, top end power thing. Is the design of a SBC/LT1 such that the peak cylinder fill is occurring at a very low RPM, and this impedes the ability of the engine to flow at higher RPM?
One thing we've learned is that intake runner length, intake valve timing seem to affect when the peaks are hit, so here is what I'm seeing...
1. Peak torque coincides with the highest VE's in the tuning tables. This is telling me peak torque is determined by the RPM's at which cylinder filling is the greatest?
--Torque = force x radial distance. Force = pressure x area.
--So, to put it in engine terms,
--Torque = cylinder pressure x (bore/2)^2 x pi x stroke. (check my math?)
--bore, stroke, and pi are constants, so only pressure can change.
Is it fair to say the above question is answered "yes, the RPM at which the cylinder fills the most on a single intake stroke determines peak torque rpm"?
2. Peak horsepower is a bit tougher to wrap my head around. I know the equation, but there seems to be some interaction going on between RPM and airflow. I'm going to assume a 6300 peak HP for this:
--Above 4800 (peak TQ) and below 6300 (peak HP), the effect of increasing RPM is greater than the effect of reduced cylinder fill efficiency.
--Above 6300 (peak HP), the effect of reduced cylinder fill efficiency is greater than the effect of increased RPM.
--The only thing I can come up with is that 6300 (peak HP) is the point at which total airflow per unit time is the highest. Reducing RPM reduces total airflow, reducing total power output. Increasing RPM reduces total airflow, reducing power output. I can't find a model to explain this, but I think the question here is --
Is peak HP RPM determined by peak airflow or is it something else?
3. Assuming the above two are correct, then is it fair to say that when you do things to change the power band of an engine, you're really just changing when you get peak airflow and when you get peak cylinder fill?
--Example1. Delaying IVC to move peak HP to 6600 RPM works because the this change allows total airflow to continue to increase at higher RPM?
--Example2. Moving to a single plane intake moves peak torque higher by shortening the intake runners, thus moving peak cylinder fill to a higher RPM?
--Example3. The age old SBC vs LS1 peak low end torque, top end power thing. Is the design of a SBC/LT1 such that the peak cylinder fill is occurring at a very low RPM, and this impedes the ability of the engine to flow at higher RPM?
#2

Nice discussion 
Lots of ways to go about this discussion also.
As we all have some level of understanding of the cylinder filling theory and it's relationship to time....here is mine.
Yes, the volume (depressed cylinder) has a specific amount of time (airspeed with in the port) to be filled efficiently (VE).....now if the port is designed correctly (length, csa ,taper...etc) you will hit the target airspeed and have proper velocity leaving the throat and diffusing into the cylinder.
To much ...and you end up with a lazy runner/ port for the cube/rpm of the build, and visa verse (starving the cylinder). This is the very reason why choosing a head based on cfm can lead to undesirable results.
Cfm is a by product of a correct port/runner....not the other way around.
So the recap is.....once you know the volume (bore x stroke) you can calculate back up the port and the runner to provide a specific amount of air in a specific amount of time.
As the time gets shorter, the runner must also to be able to move the column of air into the depression. Thus more rpm = shorter runner...basic physics.
As your probably well aware of....it's all driven by differential pressure. That's it, no more no less.
And it's the cams job to trap and release this air during the largest differential pressure swings for best results. So the valve events need to be timed to take full advantage of ram effects happening in the induction system.
And as far as hp climbing....as long as torque falls slower than rpm gain, hp will continue to climb....or so the math shows.
Larry Meaux, Darin Morgan and Curtis Boggs all have great articles explaining their induction theories. Very, very interesting reads....
And yes, peak tq is where cylinder filling is most efficient (this is where the induction system design and IVO & IVC are working harmoniously together). It's also where your the most detonation sensitive because of maximum cylinder pressure occurring at this moment.
Again, this is just my $0.02....not to be confused with the facts....lol
.
.

Lots of ways to go about this discussion also.
As we all have some level of understanding of the cylinder filling theory and it's relationship to time....here is mine.
Yes, the volume (depressed cylinder) has a specific amount of time (airspeed with in the port) to be filled efficiently (VE).....now if the port is designed correctly (length, csa ,taper...etc) you will hit the target airspeed and have proper velocity leaving the throat and diffusing into the cylinder.
To much ...and you end up with a lazy runner/ port for the cube/rpm of the build, and visa verse (starving the cylinder). This is the very reason why choosing a head based on cfm can lead to undesirable results.
Cfm is a by product of a correct port/runner....not the other way around.
So the recap is.....once you know the volume (bore x stroke) you can calculate back up the port and the runner to provide a specific amount of air in a specific amount of time.
As the time gets shorter, the runner must also to be able to move the column of air into the depression. Thus more rpm = shorter runner...basic physics.
As your probably well aware of....it's all driven by differential pressure. That's it, no more no less.
And it's the cams job to trap and release this air during the largest differential pressure swings for best results. So the valve events need to be timed to take full advantage of ram effects happening in the induction system.
And as far as hp climbing....as long as torque falls slower than rpm gain, hp will continue to climb....or so the math shows.
Larry Meaux, Darin Morgan and Curtis Boggs all have great articles explaining their induction theories. Very, very interesting reads....
And yes, peak tq is where cylinder filling is most efficient (this is where the induction system design and IVO & IVC are working harmoniously together). It's also where your the most detonation sensitive because of maximum cylinder pressure occurring at this moment.
Again, this is just my $0.02....not to be confused with the facts....lol
.
.
Last edited by LSOHOLIC; 10-23-2015 at 01:38 AM.
#3
TECH Senior Member

--Torque = cylinder pressure x (bore/2)^2 x pi x stroke. (check my math?)
or actually stroke/2 * cos(A)
and cylinder pressure would be cylinder_pressure(A) i.e. as a function of crank angle A
( but this is just math details )
Last edited by joecar; 10-23-2015 at 05:22 AM.
#4
TECH Senior Member

Torque follows cylinder fill airmass (which looks like VE table).
Power follows air flowrate which in turn follows both RPM and cylinder fill airmass.
Power follows air flowrate which in turn follows both RPM and cylinder fill airmass.
#5

Feel like may not have answered your question directly.
1) yes, peak tq is determined by the rpm where the maximum induction efficiency is taking place (valve events timed correctly to a induction system tuned to the specific cube and rpm of the engine and application of said engine).
Also keep in mind, the higher you push peak rpm the greater the hp will be.
Prostock has traditionally not made anymore power over the last several years. But they have figured out how to move their peak torque higher, thus makes more peak hp.
2) the better an engine can hang on to its efficiency past peak tq the slower it will fall, thus hp will continue to climb, mathematical speaking.
Darrin explains a lot of this very well in his tech talk section.
And remember to keep your eyes on the prize....lol
Cfm = rpm
More rpm = allows more gear
More gear = greater rear wheel torque
More rear wheel torque = greater acceleration
Greater acceleration = quicker ET
Pretty simple stuff.....
.
1) yes, peak tq is determined by the rpm where the maximum induction efficiency is taking place (valve events timed correctly to a induction system tuned to the specific cube and rpm of the engine and application of said engine).
Also keep in mind, the higher you push peak rpm the greater the hp will be.
Prostock has traditionally not made anymore power over the last several years. But they have figured out how to move their peak torque higher, thus makes more peak hp.
2) the better an engine can hang on to its efficiency past peak tq the slower it will fall, thus hp will continue to climb, mathematical speaking.
Darrin explains a lot of this very well in his tech talk section.
And remember to keep your eyes on the prize....lol
Cfm = rpm
More rpm = allows more gear
More gear = greater rear wheel torque
More rear wheel torque = greater acceleration
Greater acceleration = quicker ET
Pretty simple stuff.....

.
#6
Old School Heavy
iTrader: (16)

I've seen the horsepower vs torque threads, and this is not intended to be one of those. Yes, HP = TQ x RPM / 5252. And, I know how it was derived from a 1-ft lever arm and 33,000 pound feet of work per minute. So, that's not the point. You can't directly measure HP, so you measure TQ and use the equation. This is more about the underlying physics of it.
One thing we've learned is that intake runner length, intake valve timing seem to affect when the peaks are hit, so here is what I'm seeing...
1. Peak torque coincides with the highest VE's in the tuning tables. This is telling me peak torque is determined by the RPM's at which cylinder filling is the greatest?
--Torque = force x radial distance. Force = pressure x area.
--So, to put it in engine terms,
--Torque = cylinder pressure x (bore/2)^2 x pi x stroke. (check my math?)
--bore, stroke, and pi are constants, so only pressure can change.
Is it fair to say the above question is answered "yes, the RPM at which the cylinder fills the most on a single intake stroke determines peak torque rpm"?
2. Peak horsepower is a bit tougher to wrap my head around. I know the equation, but there seems to be some interaction going on between RPM and airflow. I'm going to assume a 6300 peak HP for this:
--Above 4800 (peak TQ) and below 6300 (peak HP), the effect of increasing RPM is greater than the effect of reduced cylinder fill efficiency.
--Above 6300 (peak HP), the effect of reduced cylinder fill efficiency is greater than the effect of increased RPM.
--The only thing I can come up with is that 6300 (peak HP) is the point at which total airflow per unit time is the highest. Reducing RPM reduces total airflow, reducing total power output. Increasing RPM reduces total airflow, reducing power output. I can't find a model to explain this, but I think the question here is --
Is peak HP RPM determined by peak airflow or is it something else?
3. Assuming the above two are correct, then is it fair to say that when you do things to change the power band of an engine, you're really just changing when you get peak airflow and when you get peak cylinder fill?
--Example1. Delaying IVC to move peak HP to 6600 RPM works because the this change allows total airflow to continue to increase at higher RPM?
--Example2. Moving to a single plane intake moves peak torque higher by shortening the intake runners, thus moving peak cylinder fill to a higher RPM?
--Example3. The age old SBC vs LS1 peak low end torque, top end power thing. Is the design of a SBC/LT1 such that the peak cylinder fill is occurring at a very low RPM, and this impedes the ability of the engine to flow at higher RPM?
One thing we've learned is that intake runner length, intake valve timing seem to affect when the peaks are hit, so here is what I'm seeing...
1. Peak torque coincides with the highest VE's in the tuning tables. This is telling me peak torque is determined by the RPM's at which cylinder filling is the greatest?
--Torque = force x radial distance. Force = pressure x area.
--So, to put it in engine terms,
--Torque = cylinder pressure x (bore/2)^2 x pi x stroke. (check my math?)
--bore, stroke, and pi are constants, so only pressure can change.
Is it fair to say the above question is answered "yes, the RPM at which the cylinder fills the most on a single intake stroke determines peak torque rpm"?
2. Peak horsepower is a bit tougher to wrap my head around. I know the equation, but there seems to be some interaction going on between RPM and airflow. I'm going to assume a 6300 peak HP for this:
--Above 4800 (peak TQ) and below 6300 (peak HP), the effect of increasing RPM is greater than the effect of reduced cylinder fill efficiency.
--Above 6300 (peak HP), the effect of reduced cylinder fill efficiency is greater than the effect of increased RPM.
--The only thing I can come up with is that 6300 (peak HP) is the point at which total airflow per unit time is the highest. Reducing RPM reduces total airflow, reducing total power output. Increasing RPM reduces total airflow, reducing power output. I can't find a model to explain this, but I think the question here is --
Is peak HP RPM determined by peak airflow or is it something else?
3. Assuming the above two are correct, then is it fair to say that when you do things to change the power band of an engine, you're really just changing when you get peak airflow and when you get peak cylinder fill?
--Example1. Delaying IVC to move peak HP to 6600 RPM works because the this change allows total airflow to continue to increase at higher RPM?
--Example2. Moving to a single plane intake moves peak torque higher by shortening the intake runners, thus moving peak cylinder fill to a higher RPM?
--Example3. The age old SBC vs LS1 peak low end torque, top end power thing. Is the design of a SBC/LT1 such that the peak cylinder fill is occurring at a very low RPM, and this impedes the ability of the engine to flow at higher RPM?
One thing I did not see you mention is the power consumed by friction and pumping losses as RPM increases. This part of the equation helps explain why the engine does not continue making more horsepower even thought it is consuming and burning more air and fuel.
#7
Moderator
Thread Starter
iTrader: (4)
Join Date: Jul 2014
Location: My own internal universe
Posts: 10,446
Received 1,838 Likes
on
1,146 Posts


As your probably well aware of....it's all driven by differential pressure. That's it, no more no less.
And it's the cams job to trap and release this air during the largest differential pressure swings for best results. So the valve events need to be timed to take full advantage of ram effects happening in the induction system.
And as far as hp climbing....as long as torque falls slower than rpm gain, hp will continue to climb....or so the math shows.
And it's the cams job to trap and release this air during the largest differential pressure swings for best results. So the valve events need to be timed to take full advantage of ram effects happening in the induction system.
And as far as hp climbing....as long as torque falls slower than rpm gain, hp will continue to climb....or so the math shows.
I think what I'm trying to ask is what causes torque to fall slower than RPM gain, reach a peak, and then fall faster than RPM gain?
One thing I did not see you mention is the power consumed by friction and pumping losses as RPM increases. This part of the equation helps explain why the engine does not continue making more horsepower even thought it is consuming and burning more air and fuel.
--For instance, as RPM increases, the acceleration forces seen by the pistons increases - probably on a quadratic curve(?).
--Since F=MA, the increased acceleration on the pistons as they reverse direction puts an increased force "load" on the engine, resulting in reduced net torque output(?)
Did you mean stroke/2...
or actually stroke/2 * cos(A)
and cylinder pressure would be cylinder_pressure(A) i.e. as a function of crank angle A
or actually stroke/2 * cos(A)
and cylinder pressure would be cylinder_pressure(A) i.e. as a function of crank angle A
I think what I meant was "some function of bore area and stroke times pressure" In the end, since bore and stroke are constant, the function is essentially constant, so the only change is the pressure, which is a direct result of cylinder fill(?)
But after reading Tigger's post, I'm thinking my assumption of the function being constant was invalid.
Trending Topics
#8
Banned
iTrader: (1)

Mass flow total (total mass of air per unit time) is our horsepower number. You can forget all about what kind of engine you have (4 cylinder or V12) and go right for mass flow numbers printed on the side of a turbocharger to determine peak power potential ballparks for any engine, without giving much thought to pressure differentials at all. Or you can use the handy equation CIDxrpm/3456 = CFM * .069 = lb/min if the engine is non turbo. Adjust for VE (equation assumes 100%).
The pressure differentials themselves have more to do with individual cylinder filling (volumetric efficiency) which determines dynamic compression, fuel per cylinder, and torque output. Manufacturers like to determine optimum runner lengths in cooperation with valve timing that generate peak VE around expected operating ranges, usually idle->5000rpm for production cars.
A general rule is use the least amount of potential flow to get the mass flow number you desire. This will, to some extent, ensure maximum port velocities given the application. Exhaust length and size should also be tuned to provide scavenging (an exhaust system can provide around 15 times the pull on a cylinder during overlap that a descending piston could, and during overlap, a well timed series of valve events can purge the cylinder of residual exhaust and ensure a complete re-filling with fresh air) Again, back to the differentials we are intentionally creating to move the air around.
Other things to think about;
Q1: why does a hot engine tend to idle higher than a cold engine? Without computer control, most of the time if you set the idle on a cold engine, it will gradually rise as the engine heats up. If air is becoming less dense as it gets warmer, there should be less energy per cylinder event given the identical fuel flow and reduced air flow. Why then, does the engine seem to pick up speed even though energy output is reduced?
A: Factors we rarely think about contribute:
-As oil becomes hot and thinner and easier to pump, the engine will spin more freely/easily and losses due to pumping it around are reduced.
-Heat is energy. Having a hotter piston surface, hotter valves, hotter oil, hotter ports, as everything gets hot hot hot there is more energy in general, available.
-The process of combustion changes when temperature changes. That is, as the engine parts heat up, there is more energy to start the combustion chain reaction, and more energy nearby with which to push the reaction over the "hump" aka the reaction diagrams peak energy input necessary to start moving the electrons/bonds.
-thus, trapping heat in the exhaust system with wrap/coatings will improve exhaust gas velocity and trap more energy, with which to spin a turbo for example. The speed increase of exhaust due to excess temperature will also help to create a suction at the exhaust valve, as I mentioned above, when utilized proper.
-Trapping too much heat can lead to melted parts. As engine performance per displacement increases, generally we want to "throw away" any additional heat and depend solely on the heat generated by the act of forced induction at this level. In other words, airflow total is power output when you want to win, whereas tricks with heat is more for getting every last ounce of VE out of a naturally aspirated engine. The VE tuning tricks work on turbo engines, of course, however there is much more to gain by using the correctly sized compressor wheel and the right intercooling tech to get the air safely in and out of the engine, than there is to be gained by adjusting and researching exhaust length/design for example.
Q2: When does an engine experience peak fuel flow? When does an engine experience peak cylinder fuel pulsewidth? What is the difference between the two, why do they occur at different times, and what is the difference between pulsewidth and duty cycle?
A: Maximum injected fuel per cylinder occurs at peak torque. Maximum injector fuel TOTAL per unit time (maximum mass in grams of fuel per second) is used at peak horsepower. Thus, duty cycle is a measure against horsepower output, whereas pulsewidth is a measure against engine VE or Torque. In other words, your engine will consume less fuel per cylinder event at peak horsepower than at peak torque. Peak torque is also often the location of best Brake Specific Fuel consumption. In other words, our engines often extract the most power per fuel quantity (mass) around peak torque.
Q3: How is it that a V8 can achieve similar economy to a 4-cylinder? What factors affect fuel economy in engines that are easy to record? What factors are difficult to record/observe that affect fuel economy.
A: Fuel economy is a function of speed and weight, minus losses due to friction and rotating mass. If a V8's internals weigh more than a 4-cylinder (very likely) then at identical RPM the V8 will need more energy (fuel) to keep it moving than the 4-cylinder. However, V8 will often cruise at a much lower RPM than a 4-cylinder, which would reduce those losses. Can the V8's lower cruise RPM more than make up for the difference in rotating mass to give a better fuel economy? In some cases, YES! Furthermore, devices such as turbochargers and PCV systems that reduce the number of atmospheric molecules in the crank case also improve economy by reducing the amount of work the engine has to do just to move (the act of drawing in air requires piston to apply additional force that isnt necessary when there is a turbocharger present to raise the pressure at the intake valve accordingly) Thus, a 2500lb vehicle with a 400horsepower V8 may achieve better economy than an identical 2500lb vehicle with a 400 horsepower 4-cylinder if the cruising RPM more than makes up for the difference in rotating mass of the drivetrain. On the other hand, a 4-cylinder may also have the advantage of using much lighter rotating parts itself, making this a competition of efficiency and not so much engine size.
I can think of more Q and A if you guys are enjoying this. I know I am.

Last edited by kingtal0n; 10-23-2015 at 05:42 PM.
#9
Moderator
Thread Starter
iTrader: (4)
Join Date: Jul 2014
Location: My own internal universe
Posts: 10,446
Received 1,838 Likes
on
1,146 Posts


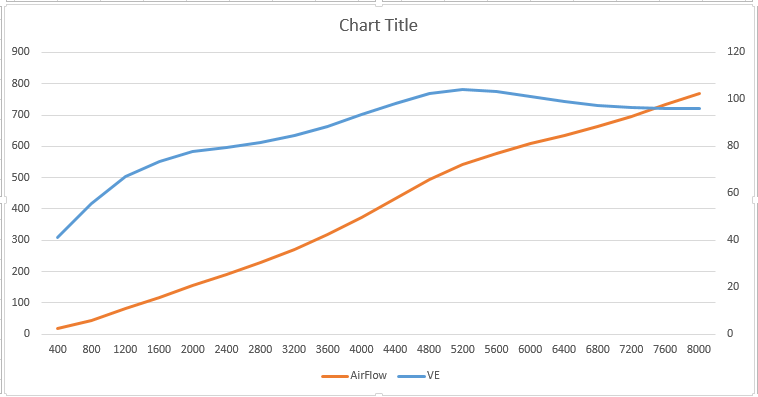
OK, so I took KingTal0n's equation for airflow and ran my VE's through it at 100KPa and I got the above chart. Orange line is airflow, blue line is VE
PCV systems that reduce the number of atmospheric molecules in the crank case also improve economy by reducing the amount of work the engine has to do just to move (the act of drawing in air requires piston to apply additional force that isnt necessary when there is a turbocharger present to raise the pressure at the intake valve accordingly)
*note to self - I might have found a use for that AIR pump I deleted

#10
11 Second Club
iTrader: (2)

Dead quench, inter ring pressure, and leakage or blow by all contribute to a higher BSFC....requiring more BTU's of heat energy to support the available horsepower/torque. Leading to dirty emissions and less efficiency.
#11
Banned
iTrader: (1)

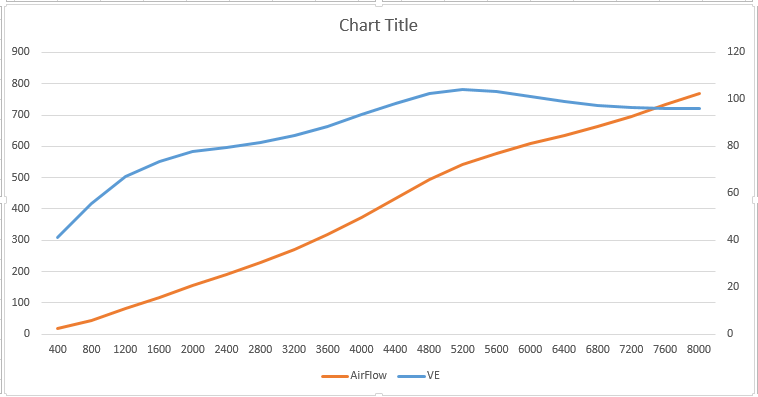
so, if I go totally apeshit, I could put a monster vacuum pump on the crankcase to draw it way down and increase efficiency of the engine? If I take that to the point of hilarity, would it reduce the oil pressure? I would think some crankcase pressure helps keep the oil pump fed?
*note to self - I might have found a use for that AIR pump I deleted

You must pay careful attention to the oil seals in such an engine. Just like boost pressure in the crank case can push oil seals out, a high vacuum can pull them in. Big displacement blower engines for racing purposes employ such vacuum pumps; they are worth 3-6% horsepower in most cases, and that can be 50-100 horsepower on some engines. Those engines get special attention to detail paid to their oil seals to withstand high the high vacuum.
On a factory engine, a couple of inches of Hg seems like it would be fine, and perhaps in some engines with Poorly constructed OEM oil seals the lower pressure will help keep oil from leaking out of the engine as easily, realizing that the reverse is also true, that is elevated pressure tends to push oil out, sometimes in a dramatic way. You can modify the inlet (air filter supplied crankcase feed, which comes off the turbocharger inlet on turbo engines) to be smaller (Restricted down in size) such that during cruise situations, vacuum supplied by the intake manifold, through the pcv valve, to the crank case, climbs more than it would otherwise (Without such a restriction) this technique is employed by the OEM manufacturer in many cases I have witnessed, such as sr20det engines, which are installed into vehicles capable of running 12's with an all original engine (just needs a tire). In other words, there are performance OEM setups out there using restrictions on their crank case vents to bump crankcase vacuum during cruise.
There are several kinds of OEM "smog pumps" and otherwise (the S2000 has some kind of pump I am aware of that may or may not be related to emissions) you might test to find one capable of pulling a reasonable vacuum on your crank case. I tend to feel like the smaller the engine volume, the easier such a device would tend to work, but there are several factors involved such as that restrictor I just mentioned that can used to aid such devices. The reason we do not simply adjust the restriction down to near nothing to elevate vacuum is because in high vacuum situations it may provide too much vacuum which can damage an oil seal, also, during WOT we may pressurize the crank case, and since the PCV valve is a one-way check valve, it will be shut during such scenarios, leaving that restricter the ONLY location for pressure in the crank case to be relieved. On a turbo engine this is directly before the turbo, pre-compressor wheel (no boost, potential vacuum) and so this space must be adequately sized for both cruise/idle/high vacuum situations AND wide open throttle situations where blow-by is accounted for, and may increase over time (keep in mind as an engine wears the blow by may increase, thus requiring larger and larger reliefs)
Last edited by kingtal0n; 10-24-2015 at 01:29 PM.
#12

There is power in crank case pressure control. As well as engine diagnosis data provided by the dynamic vacuum conditions.
The elec smog pumps are a waste of time if your serious about managing crank case pressures. I have tested quite a few; here is their typical MO....
If you kick them on before firing the engine, they will begin to pull down the crank case. To the tune of roughly 5" over a couple minutes of "headstart" before firing the engine.
Once you fire the engine they will struggle to hold 3" - 4" at idle. And once you begin to hit them with some rpm they drop relatively quickly. I was back to 0" @ 3500rpm and at 7500 the case pressure was roughly 8psi.
It boils down to, they just don't have the capacity to keep up with the rpm (being that it's a constant rpm and no linear like a belt driven pump)
I now run a 4 vane Moroso, I tend to push the envelope in all facets of this engine stuff. So, in saying that, I have my vacuum pump set to hit 15" @ 7700rpm. Which puts it roughly at 7" @ idle.
Fyi, combustion chamber stability can be translated through the rings and will traditional show up on your vacuum log.
.
The elec smog pumps are a waste of time if your serious about managing crank case pressures. I have tested quite a few; here is their typical MO....
If you kick them on before firing the engine, they will begin to pull down the crank case. To the tune of roughly 5" over a couple minutes of "headstart" before firing the engine.
Once you fire the engine they will struggle to hold 3" - 4" at idle. And once you begin to hit them with some rpm they drop relatively quickly. I was back to 0" @ 3500rpm and at 7500 the case pressure was roughly 8psi.
It boils down to, they just don't have the capacity to keep up with the rpm (being that it's a constant rpm and no linear like a belt driven pump)
I now run a 4 vane Moroso, I tend to push the envelope in all facets of this engine stuff. So, in saying that, I have my vacuum pump set to hit 15" @ 7700rpm. Which puts it roughly at 7" @ idle.
Fyi, combustion chamber stability can be translated through the rings and will traditional show up on your vacuum log.
.
Last edited by LSOHOLIC; 10-24-2015 at 03:43 PM.
#13
Moderator
Thread Starter
iTrader: (4)
Join Date: Jul 2014
Location: My own internal universe
Posts: 10,446
Received 1,838 Likes
on
1,146 Posts


There is power in crank case pressure control. As well as engine diagnosis data provided by the dynamic vacuum conditions. The elec smog pumps are a waste of time if your serious about managing crank case pressures. I have tested quite a few; here is their typical MO.... If you kick them on before firing the engine, they will begin to pull down the crank case. To the tune of roughly 5" over a couple minutes of "headstart" before firing the engine. Once you fire the engine they will struggle to hold 3" - 4" at idle. And once you begin to hit them with some rpm they drop relatively quickly. I was back to 0" @ 3500rpm and at 7500 the case pressure was roughly 8psi. It boils down to, they just don't have the capacity to keep up with the rpm. I now run a 4 vane Moroso, I tend to push the envelope in all facets of this engine stuff. So, in saying that, I have my vacuum pump set to hit 15" @ 7700rpm. Which puts it roughly at 7" @ idle. Fyi, combustion chamber stability can be translated through the rings and will traditional show up on your vacuum log. .
But I also tend to see oils thinning with heat, and also there is static and kinetic friction. Kinetic friction reduces or increases with speed?
#14

I hear ya....start looking at rod angles and stroke...as far a frictional losses are concerned.
Imo, it's common sense that all frictional and windage losses go up with rpm
But that's not what causes hp to drop quicker than the rpm it's trying to out run.
It's all in the induction system rpm efficiency window and valve train stability. Raise the rpm window in which peak tq is made and watch peak hp rise accordingly, as long as the valve train is up to the demand.
When the efficiency rpm window starts to fade tq will begin to fall quickly. Thus will produce your peak hp rpm.
Darrin Morgan
"Here is another fact. A good engine will only fall 50ft/lbs from peak TQ to peak power. Bracket engines that make about 1.45ft/lbs per-cid all fall about 60 ft/lbs from Tq peak to power peak over there power band. If they fall more than that it indicates a problem in the tuning or the engines design or combination."
.
Imo, it's common sense that all frictional and windage losses go up with rpm
But that's not what causes hp to drop quicker than the rpm it's trying to out run.
It's all in the induction system rpm efficiency window and valve train stability. Raise the rpm window in which peak tq is made and watch peak hp rise accordingly, as long as the valve train is up to the demand.
When the efficiency rpm window starts to fade tq will begin to fall quickly. Thus will produce your peak hp rpm.
Darrin Morgan
"Here is another fact. A good engine will only fall 50ft/lbs from peak TQ to peak power. Bracket engines that make about 1.45ft/lbs per-cid all fall about 60 ft/lbs from Tq peak to power peak over there power band. If they fall more than that it indicates a problem in the tuning or the engines design or combination."
.
Last edited by LSOHOLIC; 10-24-2015 at 04:46 PM.
#15

I hear ya....start looking at rod angles and stroke...as far a frictional losses are concerned.
Imo, it's common sense that all frictional and windage losses go up with rpm
But that's not what causes hp to drop quicker than the rpm it's trying to out run.
It's all in the induction system rpm efficiency window and valve train stability. Raise the rpm window in which peak tq is made and watch peak hp rise accordingly, as long as the valve train is up to the demand.
When the efficiency rpm window starts to fade tq will begin to fall quickly. Thus will produce your peak hp rpm.
Darrin Morgan
"Here is another fact. A good engine will only fall 50ft/lbs from peak TQ to peak power. Bracket engines that make about 1.45ft/lbs per-cid all fall about 60 ft/lbs from Tq peak to power peak over there power band. If they fall more than that it indicates a problem in the tuning or the engines design or combination."
.
Imo, it's common sense that all frictional and windage losses go up with rpm
But that's not what causes hp to drop quicker than the rpm it's trying to out run.
It's all in the induction system rpm efficiency window and valve train stability. Raise the rpm window in which peak tq is made and watch peak hp rise accordingly, as long as the valve train is up to the demand.
When the efficiency rpm window starts to fade tq will begin to fall quickly. Thus will produce your peak hp rpm.
Darrin Morgan
"Here is another fact. A good engine will only fall 50ft/lbs from peak TQ to peak power. Bracket engines that make about 1.45ft/lbs per-cid all fall about 60 ft/lbs from Tq peak to power peak over there power band. If they fall more than that it indicates a problem in the tuning or the engines design or combination."
.
The 416 I just built and documented here in Gen III internal was tested on an engine dyno (more accurate IMO for pure engine related data) and it lost 48 ft/lbs (570 peak....522 at peak power). But I always thought it was more of a percentage and would say a really good engine loses 9 -10% of its peak torque at peak power. On larger higher torque engines 50 ft/lbs wouldn't be nearly enough.
Whats interesting is a hundred RPM higher its at 514 TQ and making the exact same power due to the RPM multiplier. Averaging both numbers puts this engine at 518 Ft.lbs.....52 lb off its peak or 9% (51 is technically exactly 9%).
But....lets take a look at a BBC that was recently tested with my new MMS 360 heads.....this was a single 4BBL drag race engine, high compression, huge cam, and a very detailed build (582 CID). It made 837 ft/lbs peak torque and 1023 HP at 756 ft.lbs (huge power and torque for this type of application). Note a loss there of 81 ft/lbs but this motor couldn't have posted better results and carried like a champion. If you subscribe to my percentage theory however, that is still only a very modest loss of 9.5%. I think that a percentage loss is going to cover alot more ground (on varied displacement engines) and be much more repeatable. In fact I bet smaller motors would probably lose closer to 35-40 ft/lbs and still carry very well past peak....once again still only representing say 9-10% of peak torque.
Darth....regarding the power rolling off deal, it is the point where the RPM multiplier cant cover the slow roll off of the engines efficiency level (aka torque figures) as it fights frictional losses associated with crank speed, windage, etc. The better you can build the shortblock (light tension rings, dry sump, vacuum pump and other tricks etc.), the more you can hold that RPM point off and power continues to climb.....the better your heads and camshaft valve events the better the torque output which helps your cause extending that roll over point as well.....handling both (like the BBC I mentioned earlier) nets you results that are significantly better than average as the engine is able to RPM higher where you keep getting more power per each ft/lb you can hang on to....meaning 500 ft/lbs at 6000 RPM nets you 571 ponies.... at 6500 the same 500 ft/lbs nets you 618 HP, and build an engine that can hang that 500 ft/lbs to 7K and you just made 666 HP with only 500 ft/lbs of torque (at peak power).
Better understood this way perhaps...at 5K 1 ft/lb = 1 HP (close enough)
At 6K the same single ft/lb = 1.14 HP
At 7K one ft/lb of torque is worth an additional 1.33 HP
Figuring out how to get an engine to hang on as the RPM increases is a sure fire way of generating big power.....the trick is to do that without obliterating your lower/midrange power and drivability
OR....the other solution is CUBES....where the gains in TQ become the big multiplier and you don't need alot of RPM to see respectable power figures!
Good stuff guys.....carry on!!

-Tony
__________________

www.mamomotorsports.com
Tony@MamoMotorsports.com
Anything worth doing is worth doing well. Build it right the first time....its alot cheaper than building it twice!!

www.mamomotorsports.com
Tony@MamoMotorsports.com
Anything worth doing is worth doing well. Build it right the first time....its alot cheaper than building it twice!!

#17
Moderator
Thread Starter
iTrader: (4)
Join Date: Jul 2014
Location: My own internal universe
Posts: 10,446
Received 1,838 Likes
on
1,146 Posts


This is helping. I got into a discussion with a friend about peak torque vs peak horsepower, and I think I got him thinking, but I don't think I convinced him
His theory was that an engine will accelerate best at peak torque, since F=ma and T=Fr, so effectively, torque = mass x acceleration x radius.
So, by his logic, I should time shift points to straddle the torque peak. Because in any gear, peak torque would be peak acceleration
My counter argument was that I don't see this in the real world. The car accelerates best at peak power whether I'm talking same gear or different gears. To me, at 5000 rpm, the car is just getting into its sweet spot. And from discussions with Tony and others, the shift points should be timed to straddle peak power.
And he agreed that when he drives cars, they always move the fastest near peak power, but he can't make sense of it in the physics. All. I could tell him was empirically, the evidence supports peak power, not peak torque.
Now, if I'm towing, I want the motor at peak torque, not peak power, right?
So I'm really trying to understand what drives peak power, to understand the foundation of why a motor does what it does. And it makes sense that it's really just the point at which losses exceed gains, so net output drops.
As I type this I'm dusting off my diff eq books and calc 2,3 to try to derive some kind of equation that can account for these variables.
Anyone know the MOI of a stock LS1 rotating assembly?
His theory was that an engine will accelerate best at peak torque, since F=ma and T=Fr, so effectively, torque = mass x acceleration x radius.
So, by his logic, I should time shift points to straddle the torque peak. Because in any gear, peak torque would be peak acceleration
My counter argument was that I don't see this in the real world. The car accelerates best at peak power whether I'm talking same gear or different gears. To me, at 5000 rpm, the car is just getting into its sweet spot. And from discussions with Tony and others, the shift points should be timed to straddle peak power.
And he agreed that when he drives cars, they always move the fastest near peak power, but he can't make sense of it in the physics. All. I could tell him was empirically, the evidence supports peak power, not peak torque.
Now, if I'm towing, I want the motor at peak torque, not peak power, right?
So I'm really trying to understand what drives peak power, to understand the foundation of why a motor does what it does. And it makes sense that it's really just the point at which losses exceed gains, so net output drops.
As I type this I'm dusting off my diff eq books and calc 2,3 to try to derive some kind of equation that can account for these variables.
Anyone know the MOI of a stock LS1 rotating assembly?
#18

Torque is meaningless when discussing acceleration contests (aka drag racing.....roll racing, etc.). Horsepower wins races.....torque pulls trailers but let me try to explain it in different terms cause if you've been around the block a few times you may have heard what I just said even though you were unsure how valid it is.
Torque is a measurement of static state....its a given twisting force that's applied to something that may not even be moving. Horsepower is dynamic as it now adds in the element of time as it relates to RPM (movement). Its how much work/energy can be produced in a certain amount of time and think about what a drag race is....I want to get from point A to point B in a certain amount of time (the shorter the better requiring more power to pull it off!). Its a very dynamic situation. Now if I wanted to pull a trailer up a steep grade at a constant 50 MPH, the engine with the most available torque is going to have a better chance doing that. BUT....if I wanted to accelerate that trailer a given distance and had the right gearing to cover that distance, the engine with the most average power is going to win.
More real world examples of how big torque #'s are meaningless in a dragrace....to help drive my point home.
Two 7000 lb Chevy crew cab pick ups are about to race....one has a heavily modded diesel that rolls 1200 RWTQ on the dyno and 550 RWHP (pretty stout biotch!)
The other a 434 stroker (naturally aspirated that runs on gasoline) that makes 470 RWTQ and the same 550 RWHP
Who wins the race and how bad a blow out is it?? If you subscribe to the torque wins races camp could there be a better scenario in your favor?? (Two really heavy vehicles and one of them with a 600 RWTQ advantage!!). Drumroll please.....about 12.5 seconds later, the gasoline engine wins but by a small margin and the reason is it has a broader flatter power curve so while the peak numbers were the same, the gasoline engine produced more average power. The retarded torque advantage meant nothing....it was meaningless. I have friends the hot rod and race insanely powered diesel trucks and when you punch in all the stats they don't run any faster than "X" pounds of vehicle producing "X" amounts of horsepower. Now a truck with more torque might make more power and go faster because it does, but at the end of the day its all the same.....acceleration contests are about how much mass your trying to move and how much power you have to move it. Not a single slide rule or computer program will want to know how much torque the engine makes, or I should see its really only there to help plot the actual power curve in applications that request it. Moroso slide rule.....anyone reading this post that doesn't have one should be ashamed....LOL
Best damn $10 tool you will ever have in your toolbox. It requires two inputs to spit out accurate performance results.....weight.....and horsepower....if torque was relevant you know it would need to be there but its not. Torque is STATIC.....pulling at the SAME speed.....Horsepower is DYNAMIC.....Acceleration/changing speed being involved. Its kind of an easy way to wrap your head around it. Or.....simply look at torque as low/middle RPM power.....because technically that's what it is.....but you want to straddle the high RPM power to win a race cause that's where the highest average power resides.
I could go on and on but I need to get back to a few projects here.....I will revisit this at another time
-Tony
Torque is a measurement of static state....its a given twisting force that's applied to something that may not even be moving. Horsepower is dynamic as it now adds in the element of time as it relates to RPM (movement). Its how much work/energy can be produced in a certain amount of time and think about what a drag race is....I want to get from point A to point B in a certain amount of time (the shorter the better requiring more power to pull it off!). Its a very dynamic situation. Now if I wanted to pull a trailer up a steep grade at a constant 50 MPH, the engine with the most available torque is going to have a better chance doing that. BUT....if I wanted to accelerate that trailer a given distance and had the right gearing to cover that distance, the engine with the most average power is going to win.
More real world examples of how big torque #'s are meaningless in a dragrace....to help drive my point home.
Two 7000 lb Chevy crew cab pick ups are about to race....one has a heavily modded diesel that rolls 1200 RWTQ on the dyno and 550 RWHP (pretty stout biotch!)
The other a 434 stroker (naturally aspirated that runs on gasoline) that makes 470 RWTQ and the same 550 RWHP
Who wins the race and how bad a blow out is it?? If you subscribe to the torque wins races camp could there be a better scenario in your favor?? (Two really heavy vehicles and one of them with a 600 RWTQ advantage!!). Drumroll please.....about 12.5 seconds later, the gasoline engine wins but by a small margin and the reason is it has a broader flatter power curve so while the peak numbers were the same, the gasoline engine produced more average power. The retarded torque advantage meant nothing....it was meaningless. I have friends the hot rod and race insanely powered diesel trucks and when you punch in all the stats they don't run any faster than "X" pounds of vehicle producing "X" amounts of horsepower. Now a truck with more torque might make more power and go faster because it does, but at the end of the day its all the same.....acceleration contests are about how much mass your trying to move and how much power you have to move it. Not a single slide rule or computer program will want to know how much torque the engine makes, or I should see its really only there to help plot the actual power curve in applications that request it. Moroso slide rule.....anyone reading this post that doesn't have one should be ashamed....LOL
Best damn $10 tool you will ever have in your toolbox. It requires two inputs to spit out accurate performance results.....weight.....and horsepower....if torque was relevant you know it would need to be there but its not. Torque is STATIC.....pulling at the SAME speed.....Horsepower is DYNAMIC.....Acceleration/changing speed being involved. Its kind of an easy way to wrap your head around it. Or.....simply look at torque as low/middle RPM power.....because technically that's what it is.....but you want to straddle the high RPM power to win a race cause that's where the highest average power resides.
I could go on and on but I need to get back to a few projects here.....I will revisit this at another time
-Tony
__________________

www.mamomotorsports.com
Tony@MamoMotorsports.com
Anything worth doing is worth doing well. Build it right the first time....its alot cheaper than building it twice!!

www.mamomotorsports.com
Tony@MamoMotorsports.com
Anything worth doing is worth doing well. Build it right the first time....its alot cheaper than building it twice!!

Last edited by Tony @ Mamo Motorsports; 10-26-2015 at 12:54 AM.
#19

Darth v8r & Tony Mamo......
From what I'm reading in both of your last post, I disagree to a certain extent.
Do me a favor....lay your g-meter/accelerometer graph over your rwtq math. And there is your answer.
Unless you think lower g's are accelerating the car quicker than more g's.
Rear wheel tq is the key, period. It's what drives all racing.
Cfm = rpm
More rpm = allows more gear
More gear = greater rear wheel torque
More rear wheel torque = greater acceleration
Greater acceleration = quicker ET
Pretty simple stuff....
Also, a simple sanity check is the age old question.
When do you shift and why, you'd be surprised how many people either don't know or bs their answer.
On my lunch break.....but will post a dyno graph with the correlated math this evening.
.
From what I'm reading in both of your last post, I disagree to a certain extent.
Do me a favor....lay your g-meter/accelerometer graph over your rwtq math. And there is your answer.
Unless you think lower g's are accelerating the car quicker than more g's.
Rear wheel tq is the key, period. It's what drives all racing.
Cfm = rpm
More rpm = allows more gear
More gear = greater rear wheel torque
More rear wheel torque = greater acceleration
Greater acceleration = quicker ET
Pretty simple stuff....
Also, a simple sanity check is the age old question.
When do you shift and why, you'd be surprised how many people either don't know or bs their answer.
On my lunch break.....but will post a dyno graph with the correlated math this evening.
.
Last edited by LSOHOLIC; 10-26-2015 at 12:20 PM.
#20
Moderator
Thread Starter
iTrader: (4)
Join Date: Jul 2014
Location: My own internal universe
Posts: 10,446
Received 1,838 Likes
on
1,146 Posts


Darth v8r & Tony Mamo......
From what I'm reading in both of your last post, I disagree to a certain extent.
Do me a favor....lay your g-meter/accelerometer graph over your rwtq math. And there is your answer.
Unless you think lower g's are accelerating the car quicker than more g's.
Rear wheel tq is the key, period. It's what drives all racing.
Cfm = rpm
More rpm = allows more gear
More gear = greater rear wheel torque
More rear wheel torque = greater acceleration
Greater acceleration = quicker ET
Pretty simple stuff....
Also, a simple sanity check is the age old question.
When do you shift and why, you'd be surprised how many people either don't know or bs their answer.
On my lunch break.....but will post a dyno graph with the correlated math this evening.
.
From what I'm reading in both of your last post, I disagree to a certain extent.
Do me a favor....lay your g-meter/accelerometer graph over your rwtq math. And there is your answer.
Unless you think lower g's are accelerating the car quicker than more g's.
Rear wheel tq is the key, period. It's what drives all racing.
Cfm = rpm
More rpm = allows more gear
More gear = greater rear wheel torque
More rear wheel torque = greater acceleration
Greater acceleration = quicker ET
Pretty simple stuff....
Also, a simple sanity check is the age old question.
When do you shift and why, you'd be surprised how many people either don't know or bs their answer.
On my lunch break.....but will post a dyno graph with the correlated math this evening.
.
I know this sounds way nerdy and academic, but I really want to see some sort of equation based on the LS1 that I can take a quick derivative, and have it equal zero at 6300 rpm. Zero on a derivative indicates no slope, which gives you the X-axis point of the maximum of a curve.
So, the maths will be very interesting when you post them!