Lingenfelter conversion box users
#21
8 Second Club
iTrader: (4)

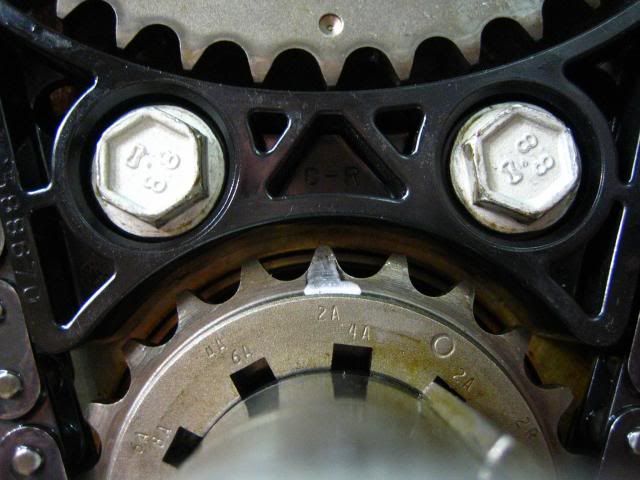
Still having power issues... though the reving issue appears to be fixed. Easily down 100hp NA from last years 8.7:1, 317 headed 5.3 with a zr1 cam. (installed straight up)
The only thinkg I can think of is I installed an aftermarket cloyes “9 position” timing set this year. I advanced the crank gear 2*. Which should in turn give me 1* of advance on my cam for a little more bottom end.
Would advancing the crank 2* cause the crank/cam signals to be out of phase? Or maybe cause some sort of issue with the signal box? Or is it pretty standard practice to advance/retard the crank timing gear on LS engines?
Can’t imagine it would make a difference, but Something is still “off”.
#22
LS1Tech Sponsor

The crank gear method of adjusting the camshaft position does move the camshaft reluctor in relation to the crank reluctor and create a potential error in the expected camshaft position sensor signal.
Since you are using our TRG-002 on your engine, if that angle is too large our module will set an internal code (cam synch code).
We allow for a certain amount of variation so 1 degree shouldn't cause a problem unless you were at the far end of the tolerance already in terms of actual crank gear and cam gear location.
If our module is not setting a synch code (blinking LED pattern) then this shouldn't be the cause of your power loss because our module uses the crankshaft position as the primary reference and is providing the camshaft signal based on the crankshaft reluctor wheel so your ignition timing should not be impacted by adjustment you made.
Old school but if you really want to verify all of this, put a TDC mark on the damper, get a pointer and a timing light and check actual timing.
Any chance you installed the camshaft a tooth off so the camshaft is timed wrong?
BTW - if you aren't using our module moving the camshaft via the crankshaft gear can potentially cause an error with the OEM ECM as well (not sure what the offset limit is an it may vary in the software diagnostics between different years/controllers etc.).
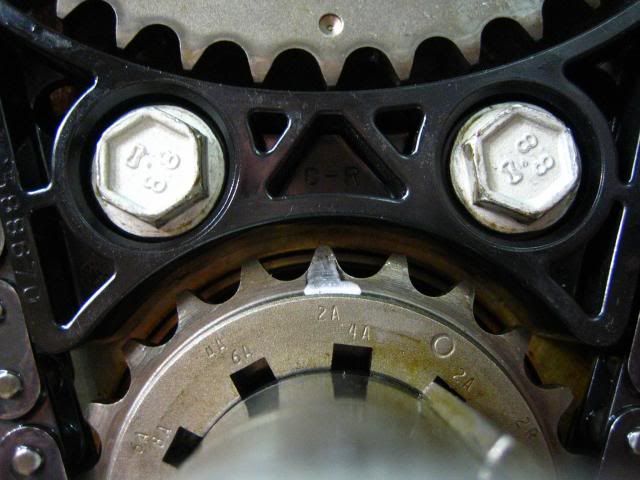
Still having power issues... though the reving issue appears to be fixed. Easily down 100hp NA from last years 8.7:1, 317 headed 5.3 with a zr1 cam. (installed straight up)
The only thinkg I can think of is I installed an aftermarket cloyes “9 position” timing set this year. I advanced the crank gear 2*. Which should in turn give me 1* of advance on my cam for a little more bottom end.
Would advancing the crank 2* cause the crank/cam signals to be out of phase? Or maybe cause some sort of issue with the signal box? Or is it pretty standard practice to advance/retard the crank timing gear on LS engines?
Can’t imagine it would make a difference, but Something is still “off”.
Since you are using our TRG-002 on your engine, if that angle is too large our module will set an internal code (cam synch code).
We allow for a certain amount of variation so 1 degree shouldn't cause a problem unless you were at the far end of the tolerance already in terms of actual crank gear and cam gear location.
If our module is not setting a synch code (blinking LED pattern) then this shouldn't be the cause of your power loss because our module uses the crankshaft position as the primary reference and is providing the camshaft signal based on the crankshaft reluctor wheel so your ignition timing should not be impacted by adjustment you made.
Old school but if you really want to verify all of this, put a TDC mark on the damper, get a pointer and a timing light and check actual timing.
Any chance you installed the camshaft a tooth off so the camshaft is timed wrong?
BTW - if you aren't using our module moving the camshaft via the crankshaft gear can potentially cause an error with the OEM ECM as well (not sure what the offset limit is an it may vary in the software diagnostics between different years/controllers etc.).
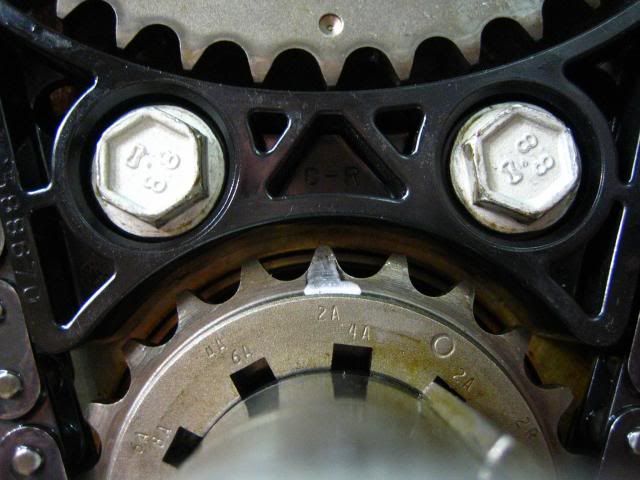
Still having power issues... though the reving issue appears to be fixed. Easily down 100hp NA from last years 8.7:1, 317 headed 5.3 with a zr1 cam. (installed straight up)
The only thinkg I can think of is I installed an aftermarket cloyes “9 position” timing set this year. I advanced the crank gear 2*. Which should in turn give me 1* of advance on my cam for a little more bottom end.
Would advancing the crank 2* cause the crank/cam signals to be out of phase? Or maybe cause some sort of issue with the signal box? Or is it pretty standard practice to advance/retard the crank timing gear on LS engines?
Can’t imagine it would make a difference, but Something is still “off”.
#23
8 Second Club
iTrader: (4)

The crank gear method of adjusting the camshaft position does move the camshaft reluctor in relation to the crank reluctor and create a potential error in the expected camshaft position sensor signal.
Since you are using our TRG-002 on your engine, if that angle is too large our module will set an internal code (cam synch code).
We allow for a certain amount of variation so 1 degree shouldn't cause a problem unless you were at the far end of the tolerance already in terms of actual crank gear and cam gear location.
If our module is not setting a synch code (blinking LED pattern) then this shouldn't be the cause of your power loss because our module uses the crankshaft position as the primary reference and is providing the camshaft signal based on the crankshaft reluctor wheel so your ignition timing should not be impacted by adjustment you made.
Old school but if you really want to verify all of this, put a TDC mark on the damper, get a pointer and a timing light and check actual timing.
Any chance you installed the camshaft a tooth off so the camshaft is timed wrong?
BTW - if you aren't using our module moving the camshaft via the crankshaft gear can potentially cause an error with the OEM ECM as well (not sure what the offset limit is an it may vary in the software diagnostics between different years/controllers etc.).
Since you are using our TRG-002 on your engine, if that angle is too large our module will set an internal code (cam synch code).
We allow for a certain amount of variation so 1 degree shouldn't cause a problem unless you were at the far end of the tolerance already in terms of actual crank gear and cam gear location.
If our module is not setting a synch code (blinking LED pattern) then this shouldn't be the cause of your power loss because our module uses the crankshaft position as the primary reference and is providing the camshaft signal based on the crankshaft reluctor wheel so your ignition timing should not be impacted by adjustment you made.
Old school but if you really want to verify all of this, put a TDC mark on the damper, get a pointer and a timing light and check actual timing.
Any chance you installed the camshaft a tooth off so the camshaft is timed wrong?
BTW - if you aren't using our module moving the camshaft via the crankshaft gear can potentially cause an error with the OEM ECM as well (not sure what the offset limit is an it may vary in the software diagnostics between different years/controllers etc.).
The cam gear has a dowel and can only be installed one way. #1 was TDC in the images. Don't think the cam gear could be off.
Back to the drawing board... Thanks for the help!
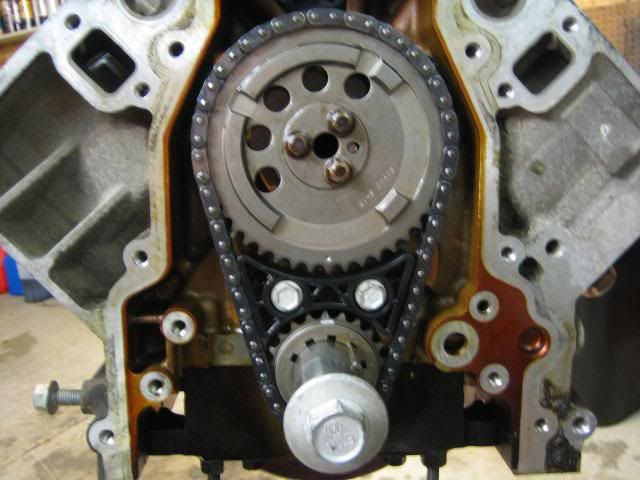
#24
8 Second Club
iTrader: (4)

The crank gear method of adjusting the camshaft position does move the camshaft reluctor in relation to the crank reluctor and create a potential error in the expected camshaft position sensor signal.
Since you are using our TRG-002 on your engine, if that angle is too large our module will set an internal code (cam synch code).
We allow for a certain amount of variation so 1 degree shouldn't cause a problem unless you were at the far end of the tolerance already in terms of actual crank gear and cam gear location.
.
Since you are using our TRG-002 on your engine, if that angle is too large our module will set an internal code (cam synch code).
We allow for a certain amount of variation so 1 degree shouldn't cause a problem unless you were at the far end of the tolerance already in terms of actual crank gear and cam gear location.
.
Reason I ask is my timing set is “off”. I have to run the 8*adv keyway in the crank sprocket to hit the numbers on the cam card. I figure as you say this will throw a cam code. I need to know if your trigger box will continue to output a useable crank signal after it sees this error.
#25
LS1Tech Sponsor

No, if the error is too large it will not output a signal and will set a sync error.
If you set a sync code you can still get our box to output a crank signal though - unplug the cam sensor input. Then our box will output the crank data (and will set a cam code in our module).
On a standard OEM ECU engine this will cause a long crank to occur on some start-ups (roughly 50%) since the ECU doesn't know which cycle you are on (compression or exhaust).
If you set a sync code you can still get our box to output a crank signal though - unplug the cam sensor input. Then our box will output the crank data (and will set a cam code in our module).
On a standard OEM ECU engine this will cause a long crank to occur on some start-ups (roughly 50%) since the ECU doesn't know which cycle you are on (compression or exhaust).
If your module sets a cam code will it continue to output a crank signal? I can set my aftermarket ECU to ignore the cam signal so I could care less about it.
Reason I ask is my timing set is “off”. I have to run the 8*adv keyway in the crank sprocket to hit the numbers on the cam card. I figure as you say this will throw a cam code. I need to know if your trigger box will continue to output a useable crank signal after it sees this error.
Reason I ask is my timing set is “off”. I have to run the 8*adv keyway in the crank sprocket to hit the numbers on the cam card. I figure as you say this will throw a cam code. I need to know if your trigger box will continue to output a useable crank signal after it sees this error.
#26
8 Second Club
iTrader: (4)

No, if the error is too large it will not output a signal and will set a sync error.
If you set a sync code you can still get our box to output a crank signal though - unplug the cam sensor input. Then our box will output the crank data (and will set a cam code in our module).
On a standard OEM ECU engine this will cause a long crank to occur on some start-ups (roughly 50%) since the ECU doesn't know which cycle you are on (compression or exhaust).
If you set a sync code you can still get our box to output a crank signal though - unplug the cam sensor input. Then our box will output the crank data (and will set a cam code in our module).
On a standard OEM ECU engine this will cause a long crank to occur on some start-ups (roughly 50%) since the ECU doesn't know which cycle you are on (compression or exhaust).
I believe I can select the "inject all" option on startup and bypass the long start sequence. I think this may be a better option than installing the cam 3* retarded.
Thank you!
#27
LS1Tech Sponsor

Yes, our module will always show a cam error but it will continue to output the crank signal.
Once I unplug the cam signal I'm done then? from that point on it will always just throw a cam code and continue to output the crank signal?
I believe I can select the "inject all" option on startup and bypass the long start sequence. I think this may be a better option than installing the cam 3* retarded.
Thank you!
I believe I can select the "inject all" option on startup and bypass the long start sequence. I think this may be a better option than installing the cam 3* retarded.
Thank you!
#29
LS1Tech Sponsor

We never released our 24x to 58x module to the public. We made prototypes and sent some to beta customers but we decided to not move forward with that product for sales volume and technical reasons.
When you say operate and OEM Vette tach, are you just trying to send a tachometer signal to the Corvette instrument cluster? If so, the tachometer signal output from the 2008 ECM to the dash is not a 58x signal anyway.
When you say operate and OEM Vette tach, are you just trying to send a tachometer signal to the Corvette instrument cluster? If so, the tachometer signal output from the 2008 ECM to the dash is not a 58x signal anyway.
#31

I'm also having a problem with the conversion box as well... I think.
I had an LS1 stock bottom end with MTI CNC ported heads, Comp Cam 233/239 .600 lift, and FAST intake and T/B. I just recently swapped out the bottom end and put a stock LS3 bottom end and re-used heads and intake, but went with bigger cam.
At first I got a used crank sensor from a local shop in GA. It would crank but not allow me to rev past like 2k, sounded like I had 2 step. So I figured since it was used, I should try another one. And got one from my buddies running built LS3, and with that one, it wouldn't even start. So I just decided to buy a new crank sensor from GM.
NOW, it cranks normal and rev's normal. BUT, it would idle for about 10 to 15 minutes and then just die. It'll crank back up but it'll throw CRANK synch code (red, red, red, green). It'll crank maybe one more time or two more times, but after that it wont crank, til after it cools back down.
Any ideas on this issue? Box getting hot?
I had an LS1 stock bottom end with MTI CNC ported heads, Comp Cam 233/239 .600 lift, and FAST intake and T/B. I just recently swapped out the bottom end and put a stock LS3 bottom end and re-used heads and intake, but went with bigger cam.
At first I got a used crank sensor from a local shop in GA. It would crank but not allow me to rev past like 2k, sounded like I had 2 step. So I figured since it was used, I should try another one. And got one from my buddies running built LS3, and with that one, it wouldn't even start. So I just decided to buy a new crank sensor from GM.
NOW, it cranks normal and rev's normal. BUT, it would idle for about 10 to 15 minutes and then just die. It'll crank back up but it'll throw CRANK synch code (red, red, red, green). It'll crank maybe one more time or two more times, but after that it wont crank, til after it cools back down.
Any ideas on this issue? Box getting hot?
#32
LS1Tech Sponsor

The crank output signal doesn't go to the tachometer. The tachometer can't read the 58x (or 24x) crank signal. It is expected an ECM processed tachometer signal. That is why I am asking what you are really trying to do. Getting the tachometer to work is usually much easier than getting the engine to run properly. Do you have a 24x crank/1x cam signal engine in a 2008 vehicle with the OEM ECM?
#33
8 Second Club
iTrader: (4)

I don’t understand why you’d want a 58x ecu in the first place? If you have a 24t crank wheel now, use a 24x ECU. Then use the tach output pin on the ecu. This signal is half the normal V8 signal. I ran that to my tach and set the tach up to receive a 4 cyl signal. Worked great on my autometer monster tach anyway.
#35
LS1Tech Sponsor

I would think the Big Stuff should be able to drive the factory tachometer. As someone else pointed out, the pulse output is more similar to what a 4 cylinder engine normally puts out (from a frequency) but other than that it is a fairly normal signal input (not CAN or anything like that).
If the Big Stuff can't do it we could probably get you a prototype of our 24x to 58x box if all it has to do it make the factory ECM see an RPM signal (PM me).
If the Big Stuff can't do it we could probably get you a prototype of our 24x to 58x box if all it has to do it make the factory ECM see an RPM signal (PM me).
#36
TECH Senior Member
iTrader: (59)

thanks i will keep that in mind.
you can get a traditional v8 signal out of the bs3 box.
but you would still have to turn it around through an adapter for the factory computer to read as 4.
if its cheaper to buy your other box to that does that then cool, i need one or the other.
you can get a traditional v8 signal out of the bs3 box.
but you would still have to turn it around through an adapter for the factory computer to read as 4.
if its cheaper to buy your other box to that does that then cool, i need one or the other.
#37
LS1Tech Sponsor

Never used one but I think Autometer and maybe some other companies make modules that will convert the crank signal or the coil signal into a tachometer signal.
You would have to make sure that these devices didn't cause any problems for the Big Stuff ECU (getting a good crank signal and the coils working correctly is probably more important than your dash working).
You would have to make sure that these devices didn't cause any problems for the Big Stuff ECU (getting a good crank signal and the coils working correctly is probably more important than your dash working).
thanks i will keep that in mind.
you can get a traditional v8 signal out of the bs3 box.
but you would still have to turn it around through an adapter for the factory computer to read as 4.
if its cheaper to buy your other box to that does that then cool, i need one or the other.
you can get a traditional v8 signal out of the bs3 box.
but you would still have to turn it around through an adapter for the factory computer to read as 4.
if its cheaper to buy your other box to that does that then cool, i need one or the other.
#38
LS1Tech Sponsor

So the BS3 is using a 24x reluctor off of the torsional damper. Do you still have a 58x reluctor wheel on the crankshaft? If so, then you could feed that crank signal to the OEM ECU (much better than trying to send the same single to multiple devices).
thanks i will keep that in mind.
you can get a traditional v8 signal out of the bs3 box.
but you would still have to turn it around through an adapter for the factory computer to read as 4.
if its cheaper to buy your other box to that does that then cool, i need one or the other.
you can get a traditional v8 signal out of the bs3 box.
but you would still have to turn it around through an adapter for the factory computer to read as 4.
if its cheaper to buy your other box to that does that then cool, i need one or the other.