"Flat" LT-specific Crankshaft???
#21
TECH Fanatic
iTrader: (2)

If all you really wanted was RPM you could destroke it and move your powerband up using the same top end components.
Dont forget the guy revvin to 8K has a 385 that extra cubes eats alot of that cam and brings the power band down, a 355 with the same top end should in theory make its peak power at a higher rpm should it not?
Dont forget the guy revvin to 8K has a 385 that extra cubes eats alot of that cam and brings the power band down, a 355 with the same top end should in theory make its peak power at a higher rpm should it not?
#23

As a third engineer (Mechanical - MTU 88) ALSO named "Mike" (Michael Lee actually...), I'll get us back to the original reason why I brought this up:
As was eluded to in various posts, Inertia is bad - and inertia is a product of Weight (or Mass) and Speed (or Motion), so if reducing the weight (and therefore inertia) on a valvetrain is a good thing (and it is - hense the use of light weight / expenisve materials) then why not do that same thing (i.e. - weight reduction) to a crankshaft via a single plane / Italian design (with zero counterweights) vs. the "standard" dual-plain 90 degree crank with heavy, mass-adding counterweights?
That's all.
Yes, I understand one school of thought says why do that 'wierd thing' if you can achieve the same goal via a more standard path; but my original thought was (if it's not too much: trouble / additional expense / etc...) then why not dare to be different?
So, to use the valvetrain example one more time:
Some people fight inertia by using massive valve springs, and overcome the problem with excessive force in the opposite direction (at the risk of reduced cam lobe life thru excessive wear); while others fight that same battle by hollowing out steel parts to reduce the overall weight (at the risk of overstressed / undersized component failure); still others use ultra lightweight / ultra expensive materials to again reduce valvetrain interia (and also their wallet) - three ways to get to the same goal (valvetrain stability) and nobody here seems to have problems with any of those choices.
I just wanted to get to that same goal (8K) a little differently than everybody else...
As was eluded to in various posts, Inertia is bad - and inertia is a product of Weight (or Mass) and Speed (or Motion), so if reducing the weight (and therefore inertia) on a valvetrain is a good thing (and it is - hense the use of light weight / expenisve materials) then why not do that same thing (i.e. - weight reduction) to a crankshaft via a single plane / Italian design (with zero counterweights) vs. the "standard" dual-plain 90 degree crank with heavy, mass-adding counterweights?
That's all.
Yes, I understand one school of thought says why do that 'wierd thing' if you can achieve the same goal via a more standard path; but my original thought was (if it's not too much: trouble / additional expense / etc...) then why not dare to be different?
So, to use the valvetrain example one more time:
Some people fight inertia by using massive valve springs, and overcome the problem with excessive force in the opposite direction (at the risk of reduced cam lobe life thru excessive wear); while others fight that same battle by hollowing out steel parts to reduce the overall weight (at the risk of overstressed / undersized component failure); still others use ultra lightweight / ultra expensive materials to again reduce valvetrain interia (and also their wallet) - three ways to get to the same goal (valvetrain stability) and nobody here seems to have problems with any of those choices.
I just wanted to get to that same goal (8K) a little differently than everybody else...

#24
9 Second Club
iTrader: (7)

As a third engineer (Mechanical - MTU 88) ALSO named "Mike" (Michael Lee actually...), I'll get us back to the original reason why I brought this up:
As was eluded to in various posts, Inertia is bad - and inertia is a product of Weight (or Mass) and Speed (or Motion), so if reducing the weight (and therefore inertia) on a valvetrain is a good thing (and it is - hense the use of light weight / expenisve materials) then why not do that same thing (i.e. - weight reduction) to a crankshaft via a single plane / Italian design (with zero counterweights) vs. the "standard" dual-plain 90 degree crank with heavy, mass-adding counterweights?
That's all.
Yes, I understand one school of thought says why do that 'wierd thing' if you can achieve the same goal via a more standard path; but my original thought was (if it's not too much: trouble / additional expense / etc...) then why not dare to be different?
So, to use the valvetrain example one more time:
Some people fight inertia by using massive valve springs, and overcome the problem with excessive force in the opposite direction (at the risk of reduced cam lobe life thru excessive wear); while others fight that same battle by hollowing out steel parts to reduce the overall weight (at the risk of overstressed / undersized component failure); still others use ultra lightweight / ultra expensive materials to again reduce valvetrain interia (and also their wallet) - three ways to get to the same goal (valvetrain stability) and nobody here seems to have problems with any of those choices.
I just wanted to get to that same goal (8K) a little differently than everybody else...
As was eluded to in various posts, Inertia is bad - and inertia is a product of Weight (or Mass) and Speed (or Motion), so if reducing the weight (and therefore inertia) on a valvetrain is a good thing (and it is - hense the use of light weight / expenisve materials) then why not do that same thing (i.e. - weight reduction) to a crankshaft via a single plane / Italian design (with zero counterweights) vs. the "standard" dual-plain 90 degree crank with heavy, mass-adding counterweights?
That's all.
Yes, I understand one school of thought says why do that 'wierd thing' if you can achieve the same goal via a more standard path; but my original thought was (if it's not too much: trouble / additional expense / etc...) then why not dare to be different?
So, to use the valvetrain example one more time:
Some people fight inertia by using massive valve springs, and overcome the problem with excessive force in the opposite direction (at the risk of reduced cam lobe life thru excessive wear); while others fight that same battle by hollowing out steel parts to reduce the overall weight (at the risk of overstressed / undersized component failure); still others use ultra lightweight / ultra expensive materials to again reduce valvetrain interia (and also their wallet) - three ways to get to the same goal (valvetrain stability) and nobody here seems to have problems with any of those choices.
I just wanted to get to that same goal (8K) a little differently than everybody else...


#25

As a third engineer (Mechanical - MTU 88) ALSO named "Mike" (Michael Lee actually...), I'll get us back to the original reason why I brought this up:
As was eluded to in various posts, Inertia is bad - and inertia is a product of Weight (or Mass) and Speed (or Motion), so if reducing the weight (and therefore inertia) on a valvetrain is a good thing (and it is - hense the use of light weight / expenisve materials) then why not do that same thing (i.e. - weight reduction) to a crankshaft via a single plane / Italian design (with zero counterweights) vs. the "standard" dual-plain 90 degree crank with heavy, mass-adding counterweights?
As was eluded to in various posts, Inertia is bad - and inertia is a product of Weight (or Mass) and Speed (or Motion), so if reducing the weight (and therefore inertia) on a valvetrain is a good thing (and it is - hense the use of light weight / expenisve materials) then why not do that same thing (i.e. - weight reduction) to a crankshaft via a single plane / Italian design (with zero counterweights) vs. the "standard" dual-plain 90 degree crank with heavy, mass-adding counterweights?
Anyway, there's a difference between reciprocating and rotating weight. I agree that reciprocating weight (valvetrain, pistons, rod little end) should be minimized. This weight directly increases stress on mechanical components and leads to valvetrain instability. However, rotating weight does not increase stress on anything. The only advantage to reducing rotating weight is reducing rotational inertia, which reduces response time.
#26
TECH Resident
iTrader: (7)

This is the first that i have heard of the flat crankshaft talk.
So please enlighten me here.
If the journals are all 180deg off of each other, vs 90deg... meaning the 1st and 3rd journal are in the same positions... wouldn't that mean that instead of 8 unique piston positions (in reference to piston position in stroke), there would only be 4 unique pistons positions... wouldn't that mean pistons would fire in pairs? Or would one be on its exhaust cycle and the other on its intake cycle?
So please enlighten me here.
If the journals are all 180deg off of each other, vs 90deg... meaning the 1st and 3rd journal are in the same positions... wouldn't that mean that instead of 8 unique piston positions (in reference to piston position in stroke), there would only be 4 unique pistons positions... wouldn't that mean pistons would fire in pairs? Or would one be on its exhaust cycle and the other on its intake cycle?
#27

If the journals are all 180deg off of each other, vs 90deg... meaning the 1st and 3rd journal are in the same positions... wouldn't that mean that instead of 8 unique piston positions (in reference to piston position in stroke), there would only be 4 unique pistons positions... wouldn't that mean pistons would fire in pairs? Or would one be on its exhaust cycle and the other on its intake cycle?
#28
TECH Resident
iTrader: (7)

On a 90 deg v8, you will always have 2 pistons at TDC at the same time. One is on TDC compression, while the other is on TDC exhaust. A 90 deg crank (conventional) puts one piston at TDC on the left bank at the same time that another is at TDC on the right bank. A 180 deg "flat" crank puts two pistons on the same bank at TDC at the same time, though they still fire 360 deg apart.
How can these cranks get by without having counterweights? It seems like that would put a lot more stress on the bearings, given that the "counterweights" are the next journal.
And if that truly does work... why wouldn't it work for a traditional 90deg crank. You have 4 journals that are at 0, 90, 180, and 270... how is it that 0, 0, 180, 180 can go without counterweights but the traditonal style couldnt?
#30
TECH Resident
iTrader: (7)

Let me reword that... it seems like there would be more stress on the main journals of the crank. In addition to them having stress exerted on them from being twisted, they would also have to transfer the stress of a rod journal that is being balances by the opposite rod journal. In a system with counterweights, the only stress is the twisting.
#31

Here's an interesting article that talks about flat cranks. Apparently, they were experimented with on flathead Fords way back.
It basically said they went with a 180 crank to help out with the situation of multiple cylinders "fighting for flow" in the exhaust and intake system, as I suspected. Note that the cranks in the pictures do have counterweights.
It's also interesting that the article notes that the original v8's had flat cranks and the 90 deg cranks were a later development to reduce vibration, and that the crank makers were reluctant to adopt them since they were so much more difficult to manufacture.
http://www.midstateantiquestockcarcl...at_heads5.html
It basically said they went with a 180 crank to help out with the situation of multiple cylinders "fighting for flow" in the exhaust and intake system, as I suspected. Note that the cranks in the pictures do have counterweights.
It's also interesting that the article notes that the original v8's had flat cranks and the 90 deg cranks were a later development to reduce vibration, and that the crank makers were reluctant to adopt them since they were so much more difficult to manufacture.
http://www.midstateantiquestockcarcl...at_heads5.html
#32
TECH Resident
iTrader: (7)

Here's an interesting article that talks about flat cranks. Apparently, they were experimented with on flathead Fords way back.
It basically said they went with a 180 crank to help out with the situation of multiple cylinders "fighting for flow" in the exhaust and intake system, as I suspected. Note that the cranks in the pictures do have counterweights.
It's also interesting that the article notes that the original v8's had flat cranks and the 90 deg cranks were a later development to reduce vibration, and that the crank makers were reluctant to adopt them since they were so much more difficult to manufacture.
http://www.midstateantiquestockcarcl...at_heads5.html
It basically said they went with a 180 crank to help out with the situation of multiple cylinders "fighting for flow" in the exhaust and intake system, as I suspected. Note that the cranks in the pictures do have counterweights.
It's also interesting that the article notes that the original v8's had flat cranks and the 90 deg cranks were a later development to reduce vibration, and that the crank makers were reluctant to adopt them since they were so much more difficult to manufacture.
http://www.midstateantiquestockcarcl...at_heads5.html
#34

OK, well I'm 42 YO and I was named after my two grandfathers (Mitchell and Leland) - I'll bet that'll provide a sufficient difference... If not, we gotta talk! 
Yes, agreed.
Having said that, if you do indeed want to decrease response time (as I do) and you do not want to use a lightweight Aluminum flywheel (M6 car here), then again a single plane crankshaft is one way (NOTE: NOT the only way, but one way) to achieve that goal.
BTW - Thanks for the input E/M, I'm just trying to clarify my position - NOT start an online Mechanical Engineering Theory 301 class - or start a finger-pointing / peter-pulling contest; too much of that already by other KIAs here...

Anyway, there's a difference between reciprocating and rotating weight. I agree that reciprocating weight (valvetrain, pistons, rod little end) should be minimized. This weight directly increases stress on mechanical components and leads to valvetrain instability. However, rotating weight does not increase stress on anything. The only advantage to reducing rotating weight is reducing rotational inertia, which reduces response time.
Having said that, if you do indeed want to decrease response time (as I do) and you do not want to use a lightweight Aluminum flywheel (M6 car here), then again a single plane crankshaft is one way (NOTE: NOT the only way, but one way) to achieve that goal.
BTW - Thanks for the input E/M, I'm just trying to clarify my position - NOT start an online Mechanical Engineering Theory 301 class - or start a finger-pointing / peter-pulling contest; too much of that already by other KIAs here...
#35
Launching!
iTrader: (14)

Ah, a topic that is right up my alley. 
I have been researching and compiling info regarding Single plane/Flat plane/180 degree crankshafts used in V8 engines since the late ‘90’s even had a nice long phone conversation with Mr David Vizard on this topic.
Being a professional engine builder/machinist has allowed me to keep a relatively realistic perspective regarding the single plane V-8 crankshaft used in street application.
I have documented much of the issues, obstacles, complexities etc associated with a 180 degree crankshaft in this link;
http://forums.hybridz.org/showthread.php?t=139545
To the original poster, yes you can install a single plane SBC crank in your GEN-II engine. Is it practical from a performance or budgetary stand point? Absolutely NOT! You have to be bent to a level that could be deemed certifiable to go through with such a project.
As a matter fact, I finally acquired a single plane Small Block Chevy crankshaft myself, (been on the look out for one since the late ‘90’s) that I intend to use in either an “87+ roller block or Gen-II block, that will end up in my Datsun 280-Z project car, (built and owned a few V-8 Datsun Z cars). I acquired my crank used. This Billet single plane crankshaft manufactured by Bryant Racing was part of the Late John Lingenfelters Pro Stock truck engine program. 3.240” stroke, Small journal mains and rods, small block snout, 2 piece rear main seal. I intend to use a 2 piece rear main seal adapter for the later model one piece rear main blocks and the Clevite M1110-H bearings, (allows small journal cranks in medium journal blocks). Plenty of off the shelf 6” and 6.125” small journal rods available.
You can have a custom single plane V-8 crankshaft manufactured, looking at $3000-$5000+. Camshaft will be a custom one off billet, cost for that is $1000+. Everything else can be traditional small block if you maintain a common stroke length for off the shelf rods and pistons.
A lot of people ask what are the benefits of such as deign? For mild to even relatively hot street application based on a domestic V-8, the short answer, is none, other than it is a costly way to have a “different” small block then most any other small block you will encounter! No it wont perform any better than comparably built dual plane version, but it will be buzzier.
This quote from the thread linked above should help answer the Pro’s and Con’s question more definitively;
Here are some pics of my Single plane Small Block Chevy crankshaft.
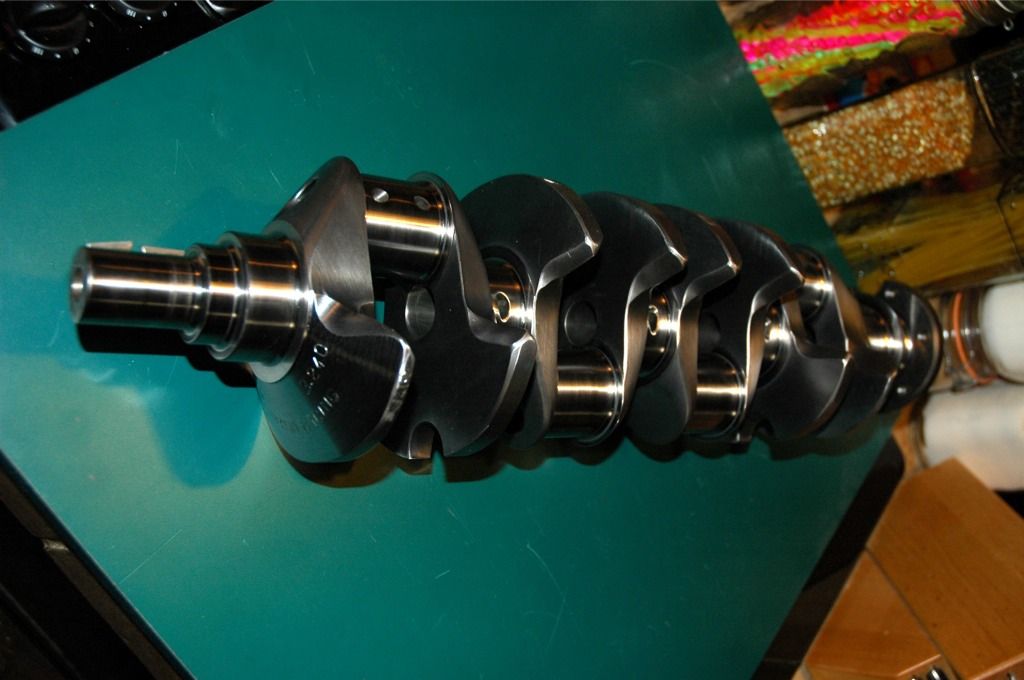

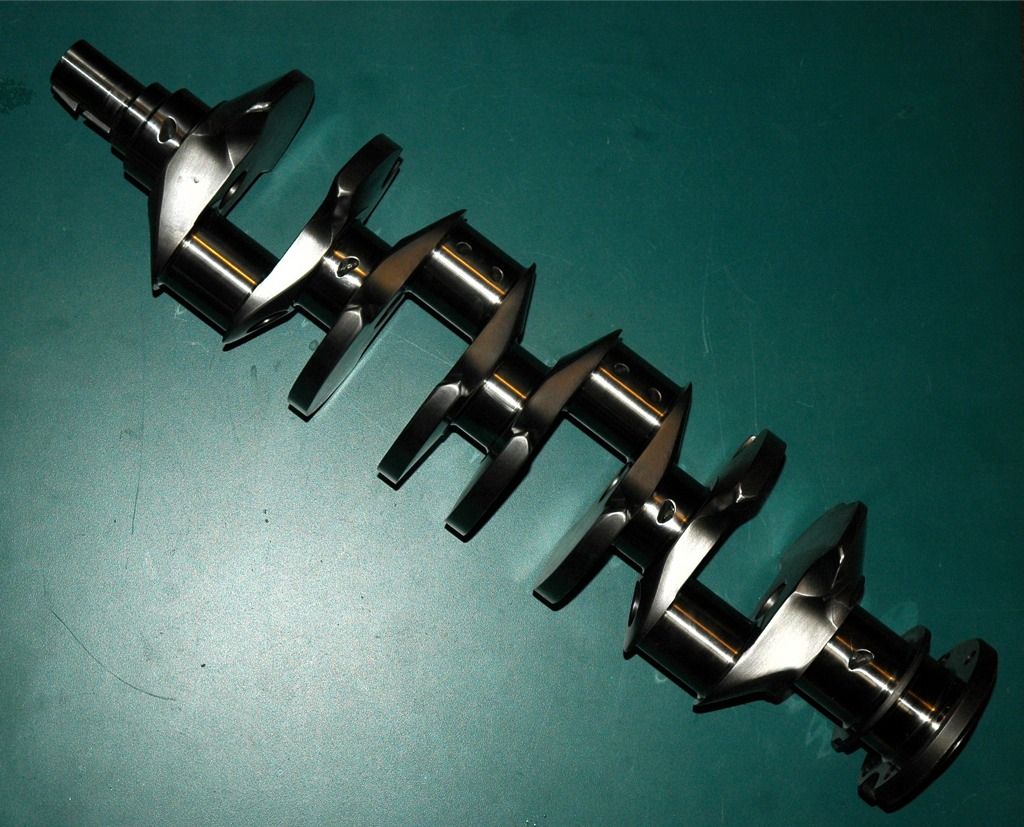
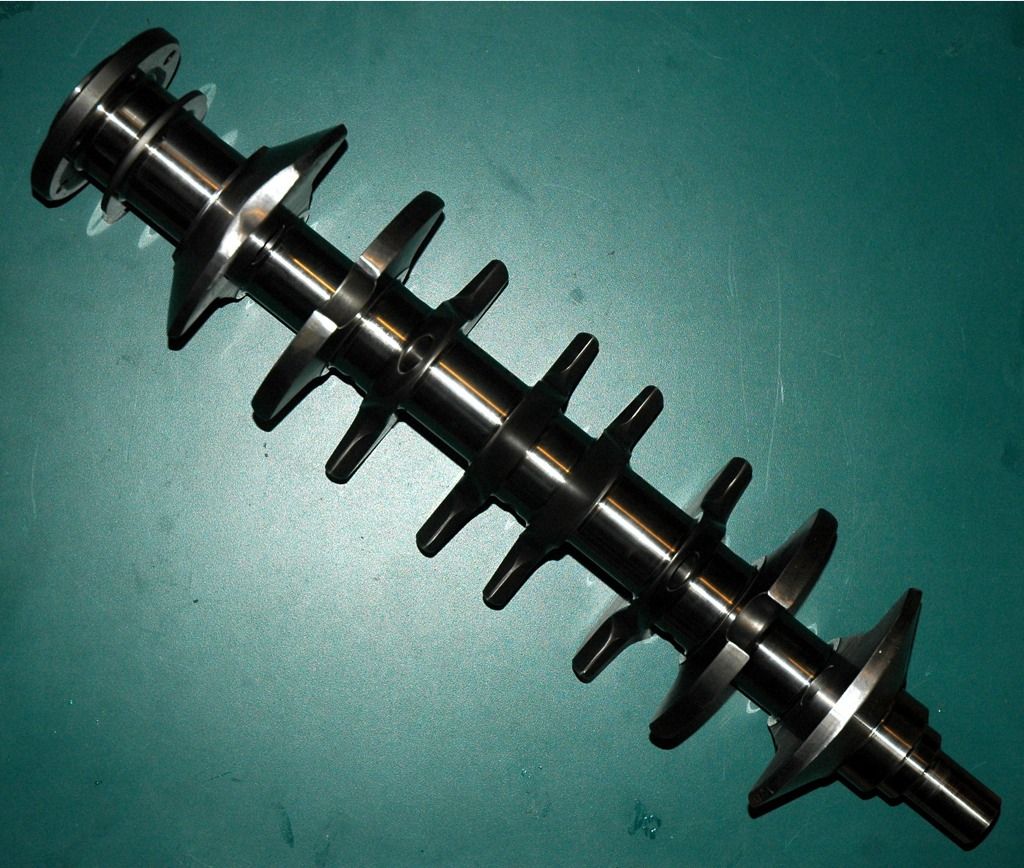

I have been researching and compiling info regarding Single plane/Flat plane/180 degree crankshafts used in V8 engines since the late ‘90’s even had a nice long phone conversation with Mr David Vizard on this topic.
Being a professional engine builder/machinist has allowed me to keep a relatively realistic perspective regarding the single plane V-8 crankshaft used in street application.
I have documented much of the issues, obstacles, complexities etc associated with a 180 degree crankshaft in this link;
http://forums.hybridz.org/showthread.php?t=139545
To the original poster, yes you can install a single plane SBC crank in your GEN-II engine. Is it practical from a performance or budgetary stand point? Absolutely NOT! You have to be bent to a level that could be deemed certifiable to go through with such a project.

As a matter fact, I finally acquired a single plane Small Block Chevy crankshaft myself, (been on the look out for one since the late ‘90’s) that I intend to use in either an “87+ roller block or Gen-II block, that will end up in my Datsun 280-Z project car, (built and owned a few V-8 Datsun Z cars). I acquired my crank used. This Billet single plane crankshaft manufactured by Bryant Racing was part of the Late John Lingenfelters Pro Stock truck engine program. 3.240” stroke, Small journal mains and rods, small block snout, 2 piece rear main seal. I intend to use a 2 piece rear main seal adapter for the later model one piece rear main blocks and the Clevite M1110-H bearings, (allows small journal cranks in medium journal blocks). Plenty of off the shelf 6” and 6.125” small journal rods available.
You can have a custom single plane V-8 crankshaft manufactured, looking at $3000-$5000+. Camshaft will be a custom one off billet, cost for that is $1000+. Everything else can be traditional small block if you maintain a common stroke length for off the shelf rods and pistons.
A lot of people ask what are the benefits of such as deign? For mild to even relatively hot street application based on a domestic V-8, the short answer, is none, other than it is a costly way to have a “different” small block then most any other small block you will encounter! No it wont perform any better than comparably built dual plane version, but it will be buzzier.
This quote from the thread linked above should help answer the Pro’s and Con’s question more definitively;
Single Plane;
Pros;
1) Exhaust pipe length tuning due to the even pulses per bank of cylinders, (on a 400 HP engine could be worth 5-10 HP).
2) Exhaust note, (this is more of a personal taste thing)
3) Lighter weight crank due to less mass needed in the counterweights for a given stroke. Faster revs, though not as smooth.
4) It’s different!
Cons;
1) 2nd order harmonics. Those harmonics are exaggerated with displacement, rod to stroke ratio determining how much 2nd order vibration, as well as how much stroke impacting the amplitude of those harmonics, (buzzy like big displacement four cylinder engines).
2) Cost of the crank and slightly more cost for the custom cam.
3) Complexity added to the project.
Dual Plane;
Pros;
1) Much smoother from a vibration/harmonics standpoint.
2) Readily available.
3) Exhaust note, (this is more of a personal taste thing)
4) Longer stroke/larger displacements without added buzziness.
Cons;
1) For given stroke, has more mass in the counterweights. Slower revs, but smoother.
2) For me anyhow, the exhaust note is a con. (Again, this is more of a personal taste than a performance aspect)
…
Pros;
1) Exhaust pipe length tuning due to the even pulses per bank of cylinders, (on a 400 HP engine could be worth 5-10 HP).
2) Exhaust note, (this is more of a personal taste thing)
3) Lighter weight crank due to less mass needed in the counterweights for a given stroke. Faster revs, though not as smooth.
4) It’s different!
Cons;
1) 2nd order harmonics. Those harmonics are exaggerated with displacement, rod to stroke ratio determining how much 2nd order vibration, as well as how much stroke impacting the amplitude of those harmonics, (buzzy like big displacement four cylinder engines).
2) Cost of the crank and slightly more cost for the custom cam.
3) Complexity added to the project.
Dual Plane;
Pros;
1) Much smoother from a vibration/harmonics standpoint.
2) Readily available.
3) Exhaust note, (this is more of a personal taste thing)
4) Longer stroke/larger displacements without added buzziness.
Cons;
1) For given stroke, has more mass in the counterweights. Slower revs, but smoother.
2) For me anyhow, the exhaust note is a con. (Again, this is more of a personal taste than a performance aspect)
…
Here are some pics of my Single plane Small Block Chevy crankshaft.
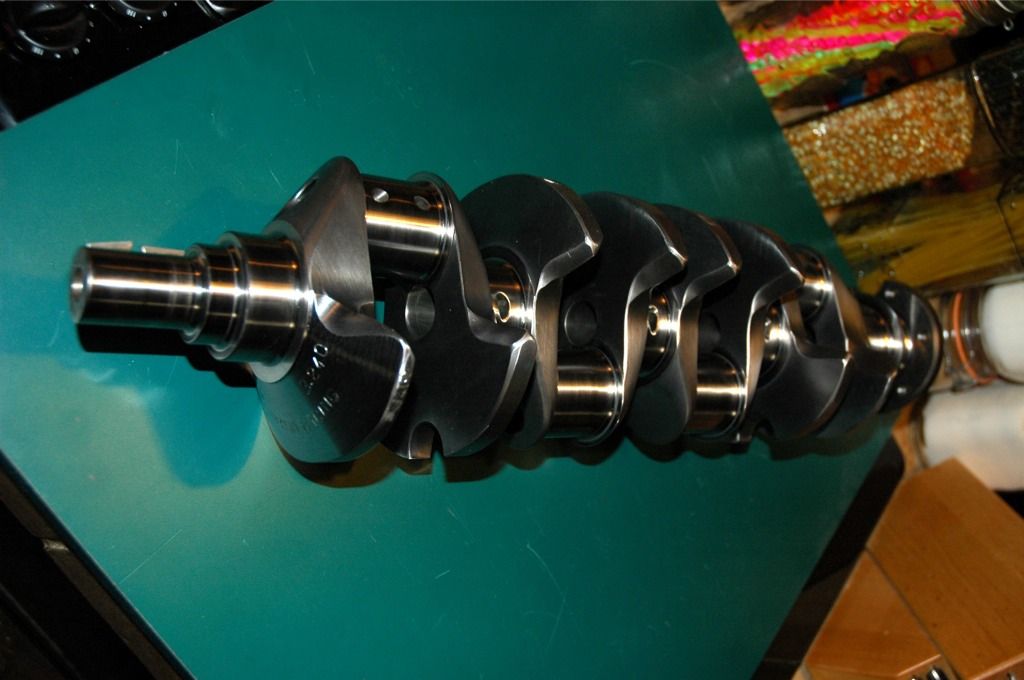

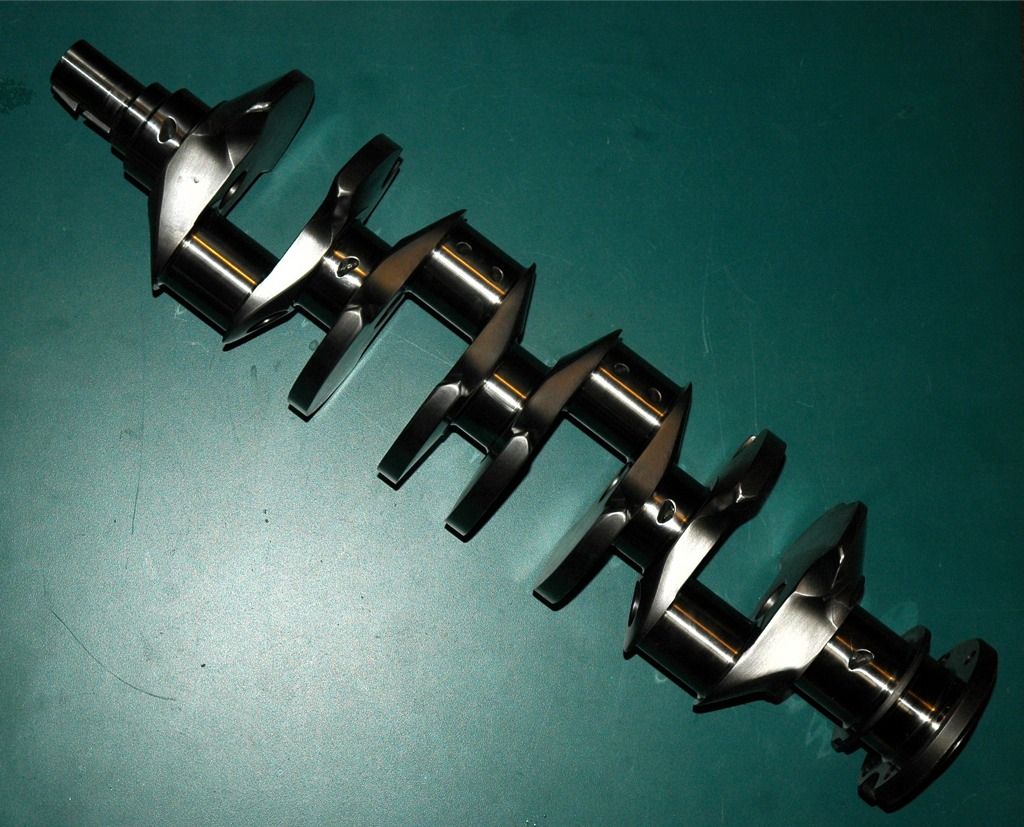
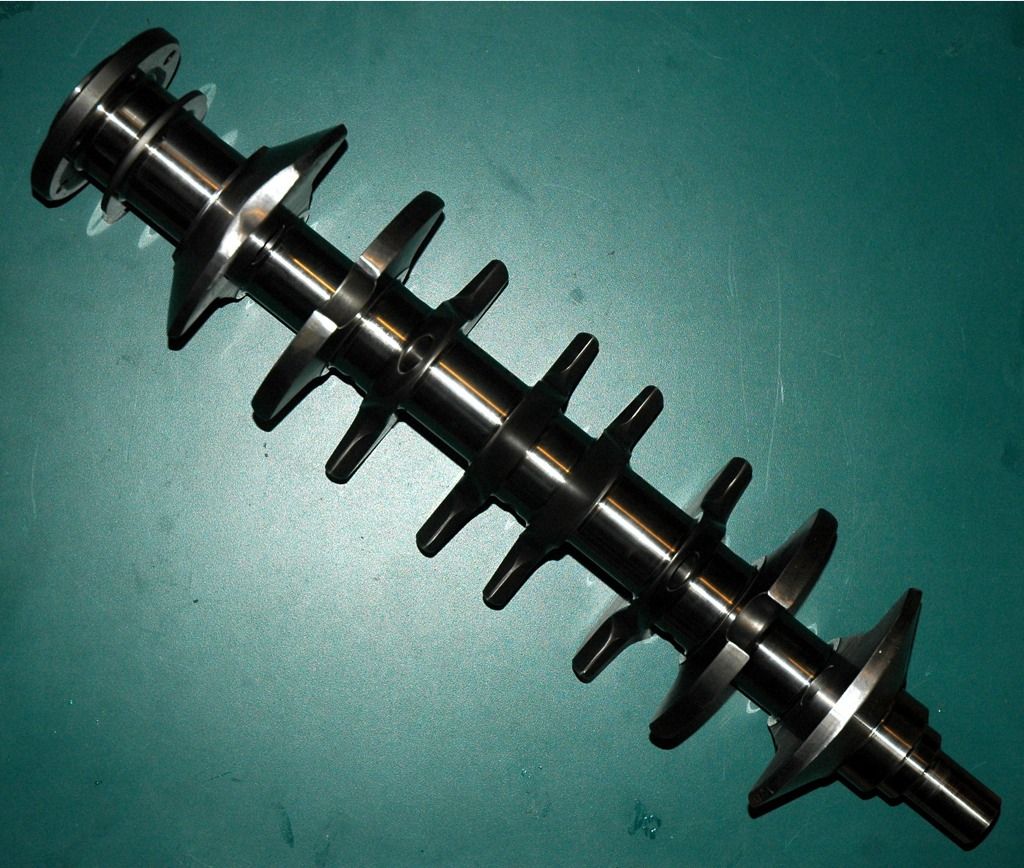
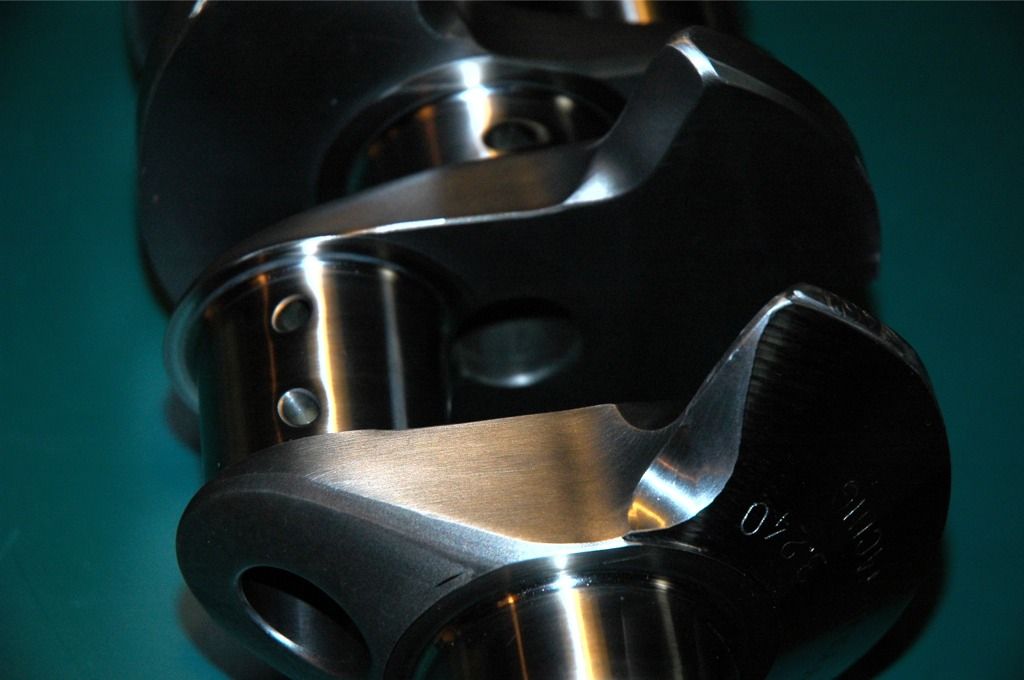
Last edited by BRAAPZ; 12-18-2009 at 08:28 PM. Reason: Typo's