Making My Own Front Lower Tubular A-arms
#1

Has anyone here built their own?
At first I was thinking rectangular tube, like the old LG Motorsports G2 arms.
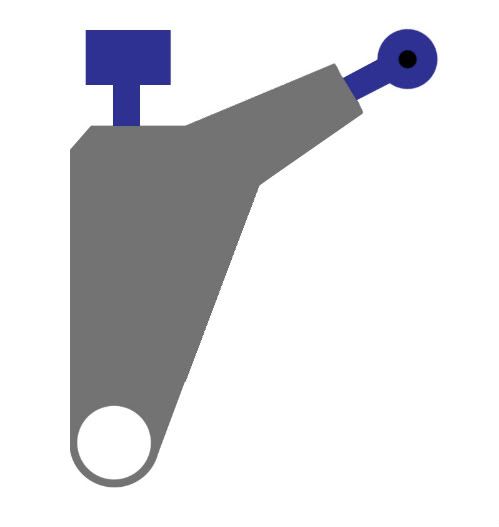
But I decided to basically copy some proven tubular designs such as the UMI and Spohn units, but with my unique requirements.
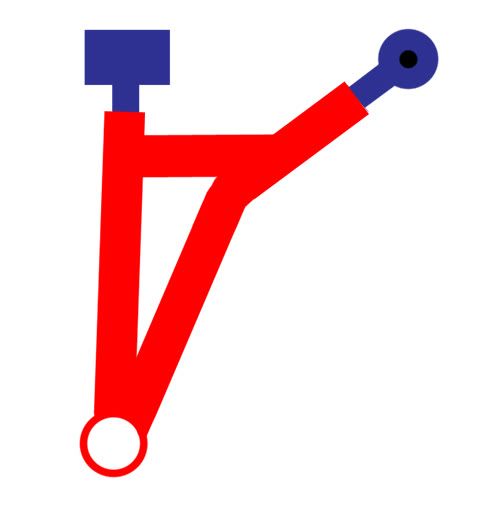
One difference is that I'm adding strength. I want it beefy. Where UMI and Spohn use 1.25" 1/8" wall DOM tubing, I want to use 1.5" 3/16" wall DOM. The problem with that is finding weld in bungs that fit.
Now the standard thread, as far as suspension bushings is concerned, is 3/4"-16.
I have 3 basic bushing material choices: Rod-end, rubber and delrin. Polyurethane is doable, but it's not to my liking.
Rubber $28

Spohn Delrin $37
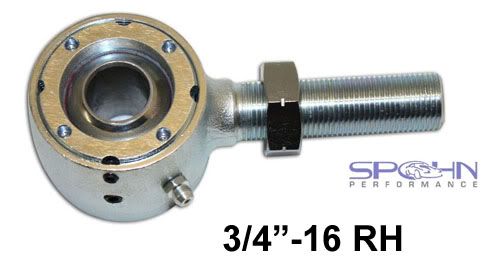
Rod-ends $15-$35
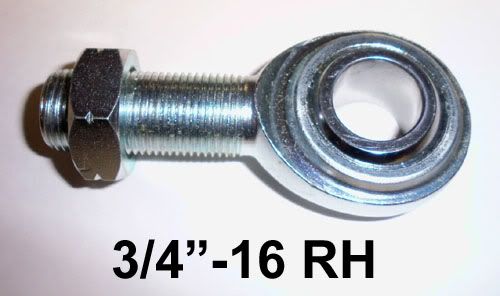
They can all be used with a 3/4"-16 weld-in bung. $6-$13
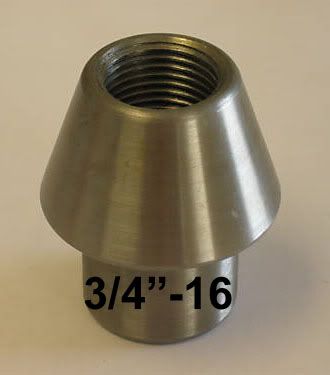
The problem I have is that most bungs are set up for 1.25" tubing, not 1.5". I think I have a source here in Houston, but not sure. Any ideas, where I can find a threaded sleeve with female threads? I can always turn it down in a lathe.
Another issue is the ball joint sleeve. Looks like .375" wall seamless mechanical tubing is the way to go. Not sure where to get it though. Speedy Metals has 12" length, but it's $50. Kinda steep.
Does anyone see any problems with my design or have any suggestions for me?
At first I was thinking rectangular tube, like the old LG Motorsports G2 arms.
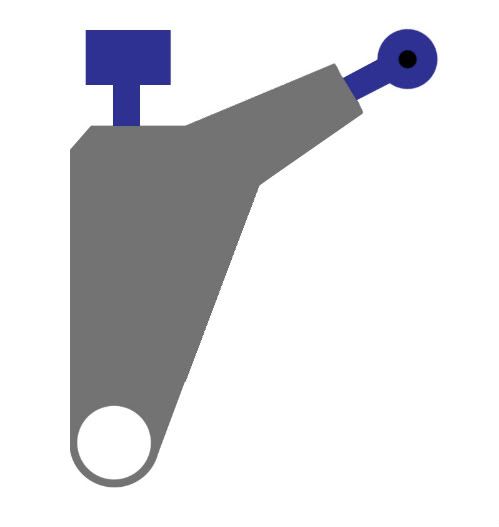
But I decided to basically copy some proven tubular designs such as the UMI and Spohn units, but with my unique requirements.
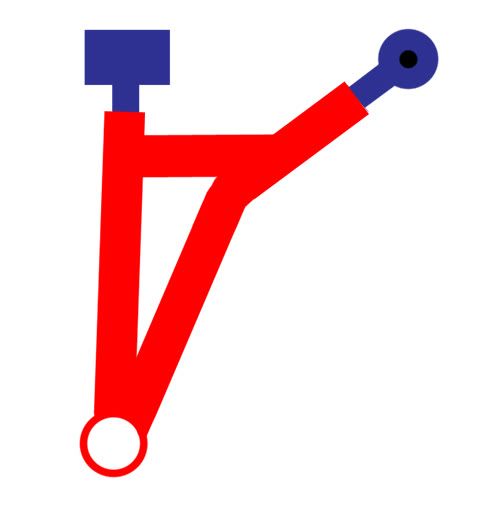
One difference is that I'm adding strength. I want it beefy. Where UMI and Spohn use 1.25" 1/8" wall DOM tubing, I want to use 1.5" 3/16" wall DOM. The problem with that is finding weld in bungs that fit.
Now the standard thread, as far as suspension bushings is concerned, is 3/4"-16.
I have 3 basic bushing material choices: Rod-end, rubber and delrin. Polyurethane is doable, but it's not to my liking.
Rubber $28

Spohn Delrin $37
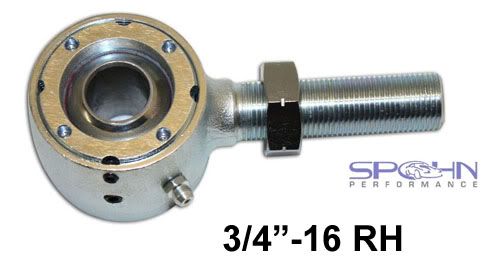
Rod-ends $15-$35
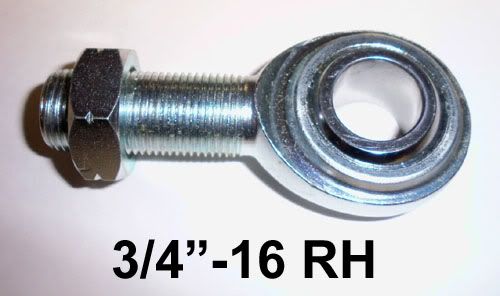
They can all be used with a 3/4"-16 weld-in bung. $6-$13
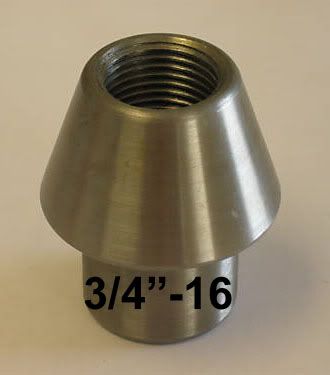
The problem I have is that most bungs are set up for 1.25" tubing, not 1.5". I think I have a source here in Houston, but not sure. Any ideas, where I can find a threaded sleeve with female threads? I can always turn it down in a lathe.
Another issue is the ball joint sleeve. Looks like .375" wall seamless mechanical tubing is the way to go. Not sure where to get it though. Speedy Metals has 12" length, but it's $50. Kinda steep.
Does anyone see any problems with my design or have any suggestions for me?
Last edited by JasonWW; 04-23-2011 at 05:43 AM.
#3

I'm looking, but the nuts I see aren't large enough in their OD.
Hey, they actually have some bungs for 1.5" 1/8" wall tubing for $6ea. I can turn that down to fit my thicker wall tubing or else I can switch over to 1.5" 1/8" wall tubing. Nice. Now I know I can get those for sure.
Now I need to bring down the cost of the ball joint sleeve.
Last edited by JasonWW; 04-23-2011 at 06:38 AM.
#4

Judging by your name, GTMLS3, I assume you built custom lower arms for a Factory Five GTM? If you used the C5 spindles, then you probably used the C5 lower ball joint (or a monoball). That's the same ball joint I'm using, but I won't get them until next week. Do you happen to know the tube ID size those ball joints need?
Trending Topics
#8

Turning down an existing piece on a lathe is cake by comparison.

I've got a cousin who works at a fab shop and he's a better welder than me, so I'll have him do all the welding. Maybe the bending, too. If not, there is a company that specializes in bending a couple miles away.
I also know of some local powder coaters as well. I think I have all the bases covered. Time will tell.
I just need to finalize my shock and sway bar mounts next.
Last edited by JasonWW; 04-23-2011 at 07:52 AM.
#12

As time goes on I'm leaning back to the rectangular tubing construction. The materials are cheaper, the end product will be stronger and the fabrication needed is less in comparison to the round tube designs. Plus it can look really nice once it's powdercoated. Check the next post to see just how nice the new UMI arms look.
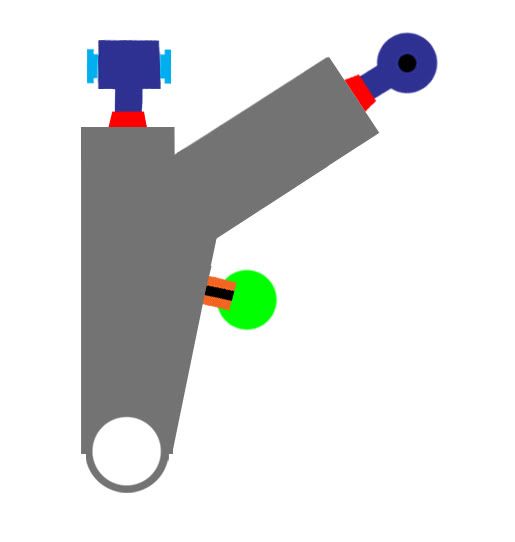
It uses 3 main sections plus the bungs/endcaps, the shock mount and eventually the sway bar mount.
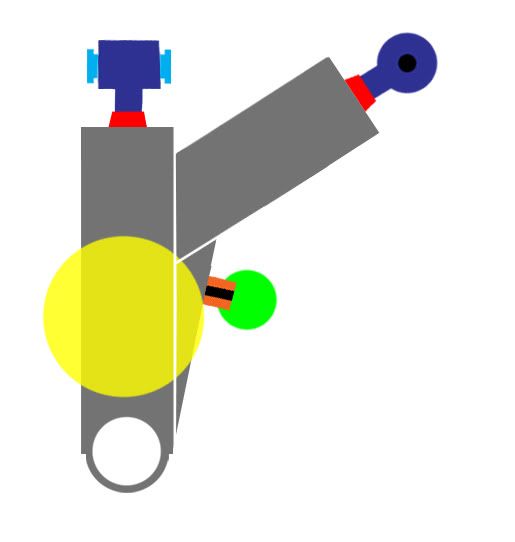
I got my ball joint cups in from Spohn. It's a really nice piece.
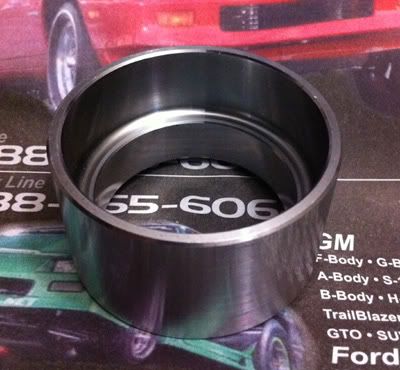
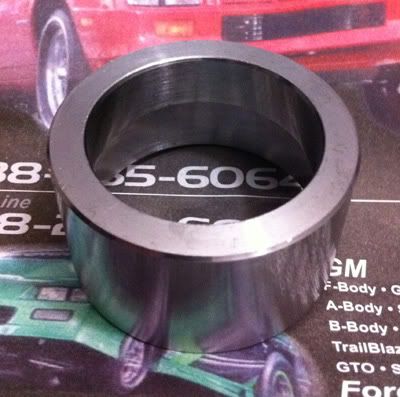
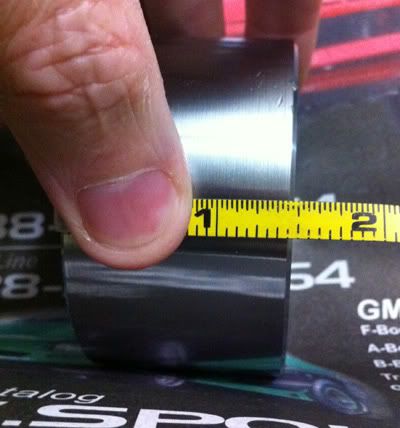
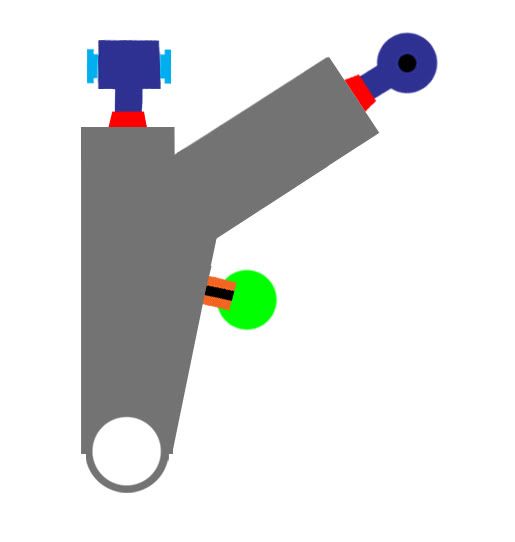
It uses 3 main sections plus the bungs/endcaps, the shock mount and eventually the sway bar mount.
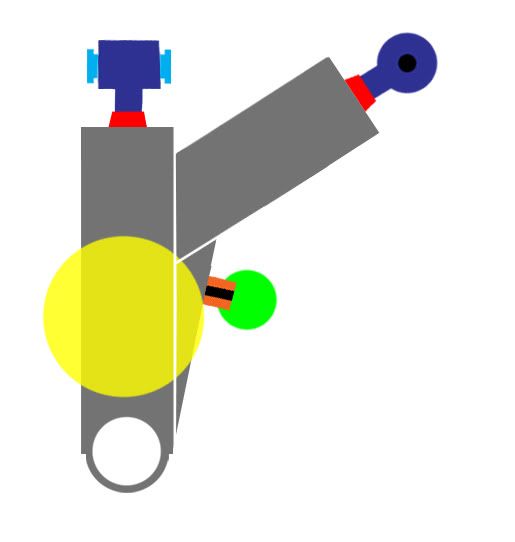
I got my ball joint cups in from Spohn. It's a really nice piece.
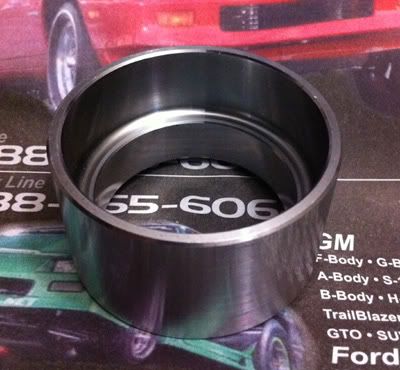
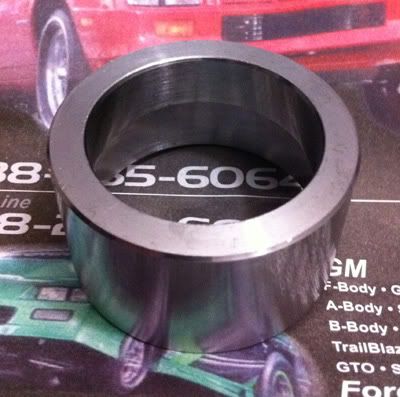
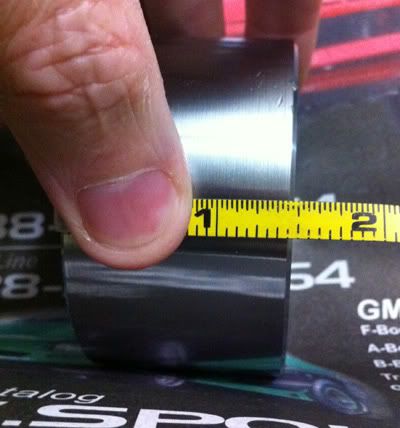
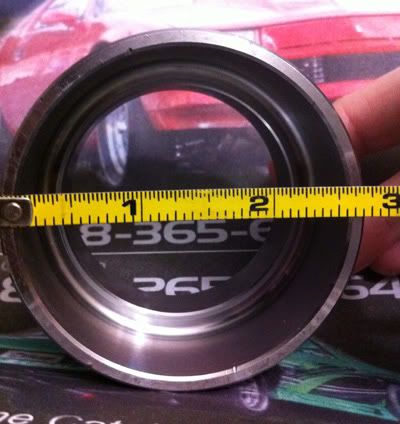
Last edited by JasonWW; 05-16-2011 at 06:42 AM.
#16

I ordered this:
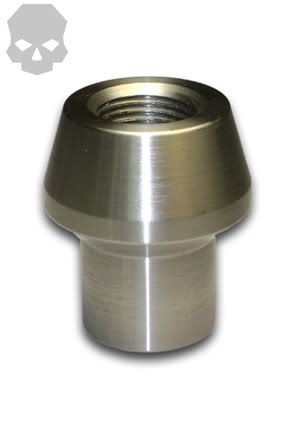
And recieved this:
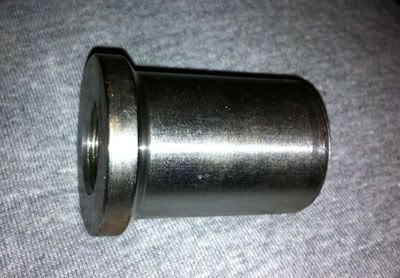
These are the correct bungs. It turns out Ballistic Fab has changed their design. I'm a little bummed, but I think I can tweak my arm design to compensate.
Oh yeah, I also decided on 1.5" x 3" x 1/8" wall tubing and got me a 12' length for $38.
Here's my design to fit the bungs into place and shape the arms to not only be strong, but to look good as well.
Even though it's 1/8" wall, these arms are going to be beefy.
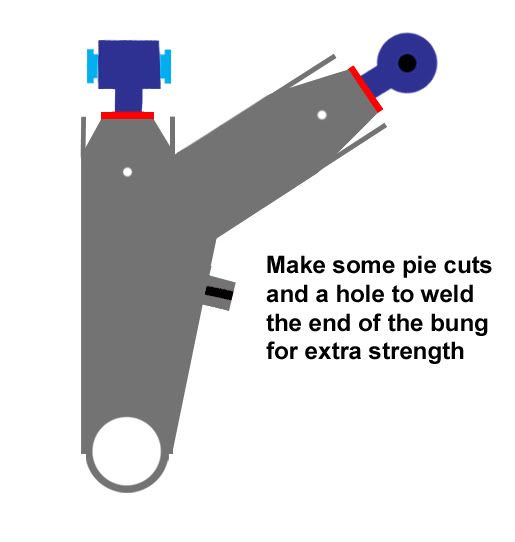
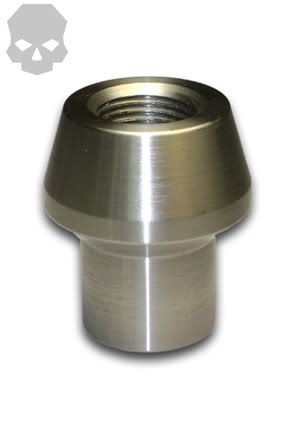
And recieved this:
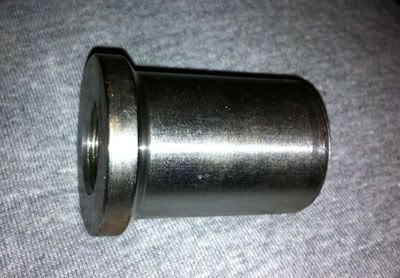
These are the correct bungs. It turns out Ballistic Fab has changed their design. I'm a little bummed, but I think I can tweak my arm design to compensate.
Oh yeah, I also decided on 1.5" x 3" x 1/8" wall tubing and got me a 12' length for $38.
Here's my design to fit the bungs into place and shape the arms to not only be strong, but to look good as well.
Even though it's 1/8" wall, these arms are going to be beefy.

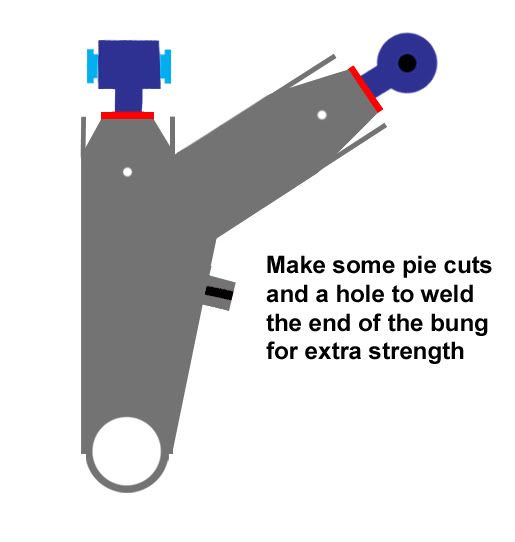
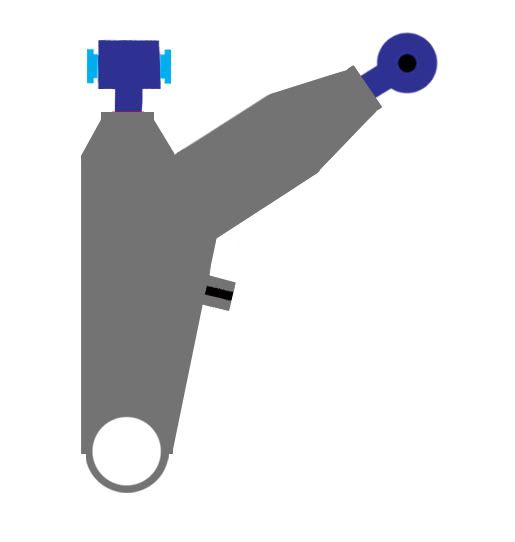
Last edited by JasonWW; 05-30-2011 at 07:07 PM.
#18

Your higher end rodends are almost always internally lubed with a Teflon liner. Those are great for use in areas where they're not under constant load and are not always exposed to dirt. The panhard bar is a great example. A good rodend can last years in that location and never make noise.
Btw, when they start making noise is when they need to be changed. Cheap rodends have a pretty short lifespan.
I know of 3 very similar Delrin joints. The Spohn Del-Sphere, the UMI Roto-Joint and Rusty's Offroad Forged Flex. The Rusty's joint uses a 1.25x12 thread so it's out as far as I'm concerned.
Between the UMI and the Spohn joint I like that Spohn offers every little piece of the joint available separately if you should need it, so I'm leaning towards them at the moment.
UMI pics:
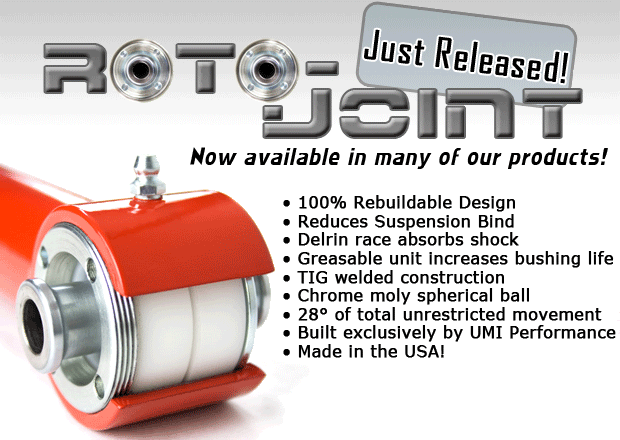
Btw, when they start making noise is when they need to be changed. Cheap rodends have a pretty short lifespan.
I know of 3 very similar Delrin joints. The Spohn Del-Sphere, the UMI Roto-Joint and Rusty's Offroad Forged Flex. The Rusty's joint uses a 1.25x12 thread so it's out as far as I'm concerned.
Between the UMI and the Spohn joint I like that Spohn offers every little piece of the joint available separately if you should need it, so I'm leaning towards them at the moment.
UMI pics:
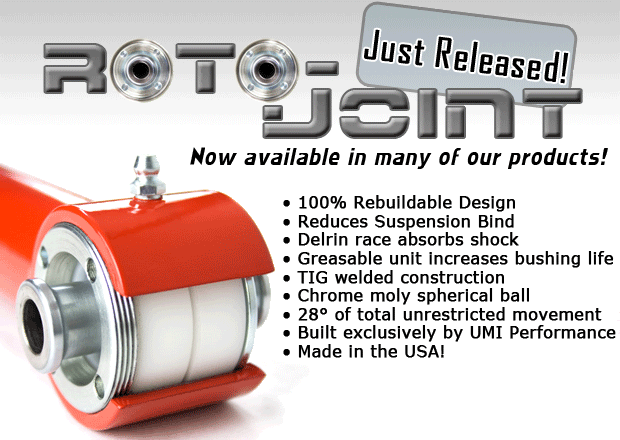

Last edited by JasonWW; 05-30-2011 at 07:16 PM.
#20

I've been reading up on bushing designs to find what would be best for my needs.
The Del-Spheres and Roto Joints seem to both suffer from high wear rates sometimes needing tightening every few weeks and I just don't like that.
Rod ends perform well, but of course wear quickly and need to be replaced often and ride harshly.
So I got to thinking of a hybrid design that uses a rod end for the camber bushing and rubber for the caster bushing. That will give really good cornering feel and still soak up the bumps.
Now instead of an actual rod end, I'll replace it with a much bigger, cheaper and longer wearing ball joint.
So in the pic below, the red dots are the ball joints and the blue dots are rubber bushings.
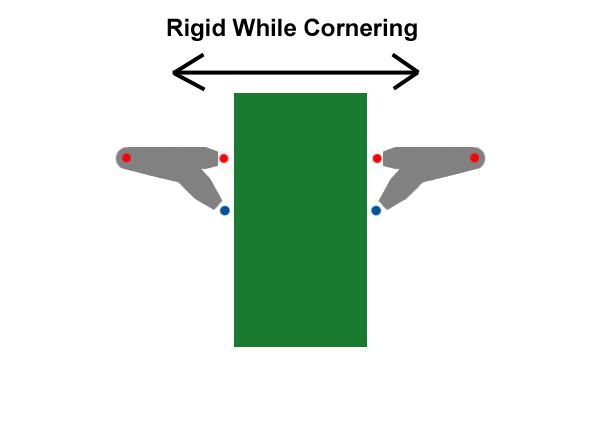
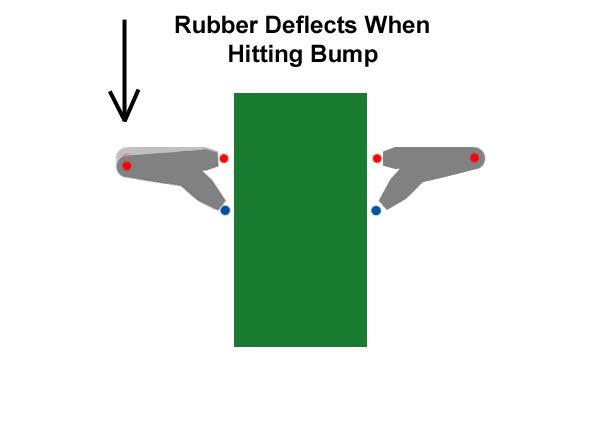
What do you guys think of this design?
The Del-Spheres and Roto Joints seem to both suffer from high wear rates sometimes needing tightening every few weeks and I just don't like that.
Rod ends perform well, but of course wear quickly and need to be replaced often and ride harshly.
So I got to thinking of a hybrid design that uses a rod end for the camber bushing and rubber for the caster bushing. That will give really good cornering feel and still soak up the bumps.
Now instead of an actual rod end, I'll replace it with a much bigger, cheaper and longer wearing ball joint.
So in the pic below, the red dots are the ball joints and the blue dots are rubber bushings.
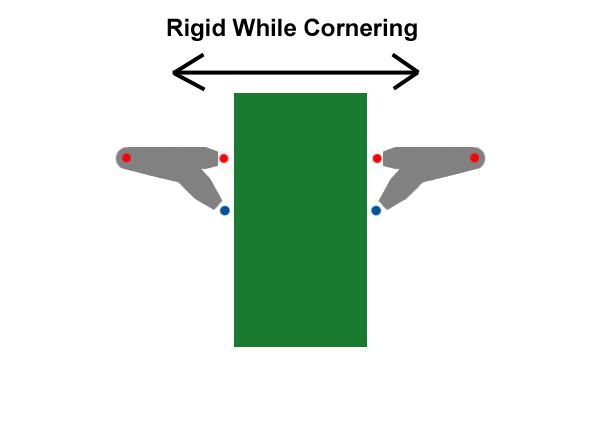
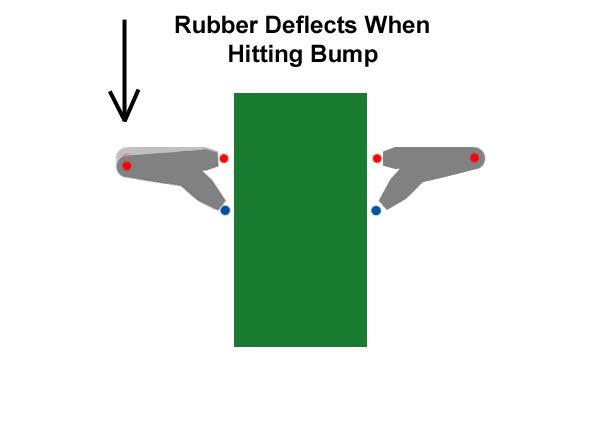
What do you guys think of this design?