Started to learn tig welding today.
#23
TECH Addict
iTrader: (24)
Join Date: Oct 2006
Location: Webb City, MO...out in the garage
Posts: 2,608
Likes: 0
Received 0 Likes
on
0 Posts



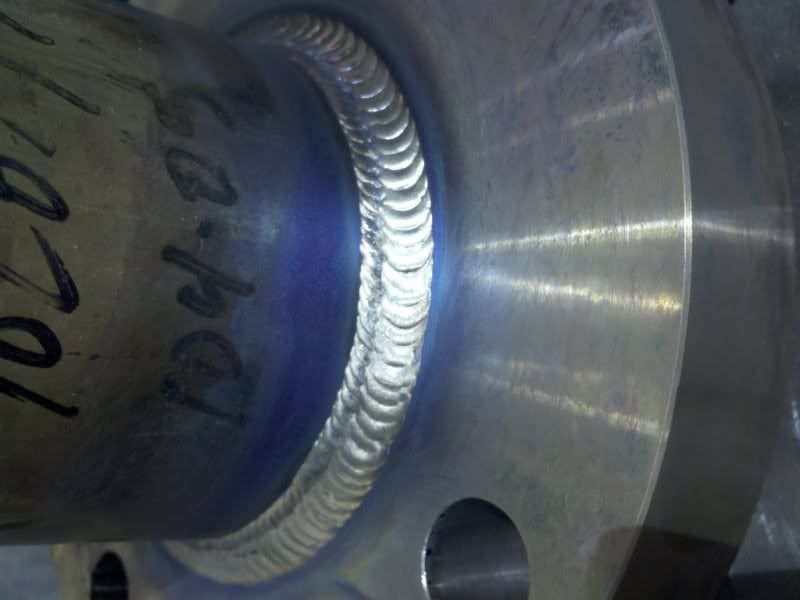
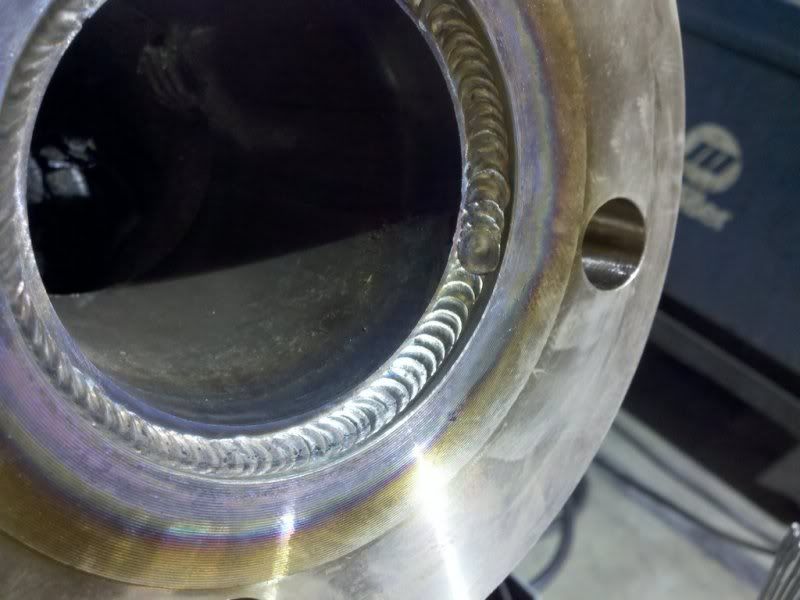
Here's a Inconel "butter pass" on a CuNi tubesheet, before a stainless panel got welded to it:
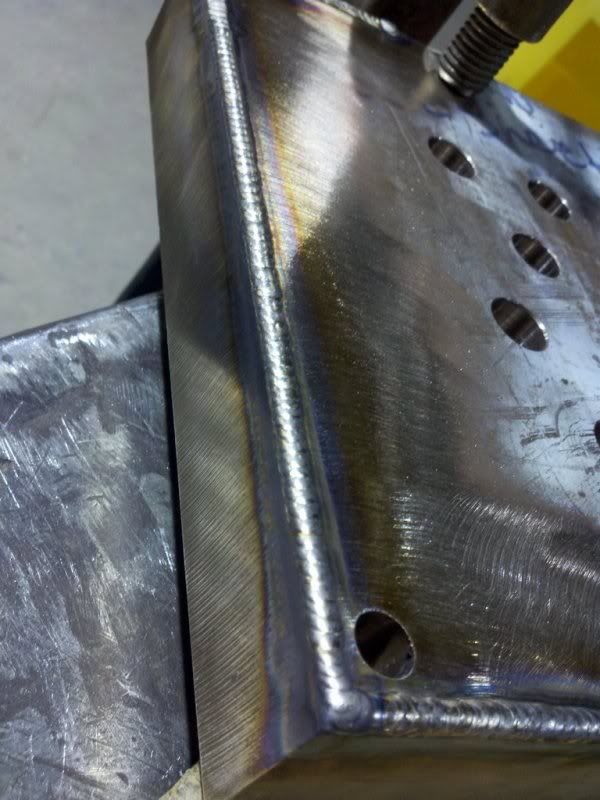
Sorry OP, not trying to hijhack

#25
TECH Resident
iTrader: (2)

Ive found the hardest material to TIG weld is the stuff that requires you to hang upside down squeeze the pedal between your knees...have a buddy hold a mirrior while you attempt to weld something that wont fall off or leak or in worse case situation have your buddy run the pedal while you give instructions....
#26
TECH Addict
iTrader: (24)
Join Date: Oct 2006
Location: Webb City, MO...out in the garage
Posts: 2,608
Likes: 0
Received 0 Likes
on
0 Posts


yes...that DOES suck....now imagine doing it in a nuclear powerplant with some lazy-*** boilermaker you've never met before and it's his first day on the job....
#29
12 Second Club
iTrader: (6)
Join Date: Nov 2010
Location: Killeen,TX
Posts: 201
Likes: 0
Received 0 Likes
on
0 Posts

i wish i could weld like that, picked up a tig welder about a year ago and still haven't gotten even proficient at it. thinking i need to take a class, but there's none available here.
#32
TECH Addict
iTrader: (24)
Join Date: Oct 2006
Location: Webb City, MO...out in the garage
Posts: 2,608
Likes: 0
Received 0 Likes
on
0 Posts


put a song with a steady, drving beat on the radio. set your amps where you can travel fast enough to dip your rod to the beat of the music. I find Godsmack works really well for this (although i can't stand Godsmack).
I don't use this method, but i did when i was learning. Now it comes naturally from years of practice/experience. you just need to get to the point where you know what a puddle should look like, how to tell when you're getting good penetration or when you're burning through, and then you'll be able to work on making pretty welds.
i didn't go to school for welding. i guess i was what you would call a natural, but even so, it took me a considerable amount of time to get really good. i learned on aluminum and thin guage stainless. I worked backwards to tig welding thicker mild steel. Finally, i picked up MIG welding after years of TIG experience and that was a breeze by that point. i can stick weld too, but i'm by no means a master of that process.
I don't use this method, but i did when i was learning. Now it comes naturally from years of practice/experience. you just need to get to the point where you know what a puddle should look like, how to tell when you're getting good penetration or when you're burning through, and then you'll be able to work on making pretty welds.
i didn't go to school for welding. i guess i was what you would call a natural, but even so, it took me a considerable amount of time to get really good. i learned on aluminum and thin guage stainless. I worked backwards to tig welding thicker mild steel. Finally, i picked up MIG welding after years of TIG experience and that was a breeze by that point. i can stick weld too, but i'm by no means a master of that process.
#36
Staging Lane
iTrader: (10)
Join Date: Dec 2010
Location: Wasaga Beach, Ont, Canada
Posts: 97
Likes: 0
Received 0 Likes
on
0 Posts

Man you guys make it look easy I ve tried tig a few times and its not easy at all. I mig down in a few days but tig is sooo much harder to do. I hang out at my buddys speed shop all the time and see him doin it on custon exhausts and old harleys making parts for them. Tig is by far the cleanest welding out there and im determinded to learn it. After seeing this thread im gonna try learning it for sure. Thanks for the inspiration guys.
#37
TECH Regular
iTrader: (5)
Join Date: Apr 2008
Location: Miami, Florida
Posts: 474
Likes: 0
Received 0 Likes
on
0 Posts

Tig just takes a while. Pay really close attention and watch what the puddle is doing, keep at it for a long time and you'll get the hang of it. Mild steel is great to start on, stainless is a little more difficult to see whats going on, and aluminum is pretty strange and you do it more by "feel" than anything, while still paying attention. I've been tigging for around 2-3 years and I still screw up now and then. Keep at it and you'll get the hang of it. One thing I recommend is to practice welding in all kinds of strange positions. Sometimes you can't move the piece to where its at any sane angle. Tigging upside down is interesting lol.

One of my better stretches lol

absurdly long frame run

One of my better stretches lol

absurdly long frame run
#38
Staging Lane
iTrader: (10)
Join Date: Dec 2010
Location: Wasaga Beach, Ont, Canada
Posts: 97
Likes: 0
Received 0 Likes
on
0 Posts

Looks amazing man I was at my buddys shop sunday learning from him again on some old harley frames he was streching for his customer for a custom project. Turned out alright but I will need all the practice time I can get for sure
#39
TECH Regular
iTrader: (5)
Join Date: Apr 2008
Location: Miami, Florida
Posts: 474
Likes: 0
Received 0 Likes
on
0 Posts

What he said- and with welds like that good lord! You're damn good!
It's all time, practice, and patience. And surface preparation is very important too =) Dirty surface= dirty weld. usually anyway, you can pedal it to have the impurities come out more on the top but I digress. Keep practicing and weld whatever you can get your hands on, thin stainless, aluminum, pot metal, engine blocks, everything.
It's all time, practice, and patience. And surface preparation is very important too =) Dirty surface= dirty weld. usually anyway, you can pedal it to have the impurities come out more on the top but I digress. Keep practicing and weld whatever you can get your hands on, thin stainless, aluminum, pot metal, engine blocks, everything.
#40
TECH Addict
iTrader: (24)
Join Date: Oct 2006
Location: Webb City, MO...out in the garage
Posts: 2,608
Likes: 0
Received 0 Likes
on
0 Posts


It's all time, practice, and patience. And surface preparation is very important too =) Dirty surface= dirty weld. usually anyway, you can pedal it to have the impurities come out more on the top but I digress. Keep practicing and weld whatever you can get your hands on, thin stainless, aluminum, pot metal, engine blocks, everything.
...BUT, a good habit to get into is to treat every joint you weld like its going on the space shuttle, no matter what the material or application is. Make the surface and up to an inch around it as close to virgin metal as possible. a good wire brush and some acetone or isopropyl alcohol go a long way, as well as clean sharp tungsten and filler rod.
try taking a brand new rod out of a box and wipe a white cloth with some acetone down the rod...there will be a nice black stripe left over on the rag. that little bit of contamination can/does make a difference in some instances. again, not so much on mild steel, but that doesn't mean it isn't a good habit to form.