cutting primary tubes off header flange
#1

Whats the best method for cutting 351w primary tubes from their flanges? Would a cut off wheel on a grinder remove too much material?
I may need to do a 351w ls1 flange swap inorder to keep my 67 mustang project rolling.
I may need to do a 351w ls1 flange swap inorder to keep my 67 mustang project rolling.
#5
TECH Fanatic
iTrader: (16)
Join Date: Dec 2005
Location: Alvarado, Texas
Posts: 1,299
Likes: 0
Received 0 Likes
on
0 Posts


Nope, let the flange be a guide, cut it right up close. BTW, 16 gauge mild steel will have plenty of play to line the up perfect with LSx flange. Spaced almost perfect as I have done the same thing with my old ls1 notch. I used hooker super comp LT's for 351 swap, cut em off and welded on a set of SDPC LSx flanges.
Trending Topics
#10

There was an article in one of the car mags about building custom headers. One trick for matching the flanges are to slit the primary tubes for a little bit to make it easier to shape the pieces to the flange, using a hammer and punch to shape the tubes. Then just weld up the slits and smooth things all out at the ends.
#11

also i take it your rounding pipe was 1-3/4 and flattened to fit inside the square flange. do you think a cheap pipe expander from harbor freight would be enough to round the tubes out? wouldn't necessarily be stretching the pipe beyond its natural diameter.
#12
TECH Junkie
iTrader: (11)

Thank you for the pictures they help out so much. well i see you needed to weld up a 1/8 gap difference from your flanges and your primary tubes. If i go with 1-3/4 flanges i will have the same size gap. did you weld from the inside of the tubes or outside? I have read some people bolt the flange to a head for finish welding to keep the flange from warping. that would be impossible to weld from the inside that way. the flanges i was looking into are 3/8 thick.
also i take it your rounding pipe was 1-3/4 and flattened to fit inside the square flange. do you think a cheap pipe expander from harbor freight would be enough to round the tubes out? wouldn't necessarily be stretching the pipe beyond its natural diameter.
also i take it your rounding pipe was 1-3/4 and flattened to fit inside the square flange. do you think a cheap pipe expander from harbor freight would be enough to round the tubes out? wouldn't necessarily be stretching the pipe beyond its natural diameter.
Rounding the tube is not rocket science, just brute force. Whatever works best for you. I used a piece of 1" pipe flattened to 1 3/4" wide so the wide edge just fit into the diagonal of the square tube, then just work it around until it's close to round. Liberal use of a 2# ball-peen hammer helps.
#14
TECH Enthusiast
iTrader: (3)

https://ls1tech.com/forums/conversio...ice-9c1-3.html
midway down this page goes over making a set...I use an old GM sway bar with end ground into a wedge shape, works great for shaping the tubes. I also use a acetylene torch, propane hand held doesn't get hot enough.
midway down this page goes over making a set...I use an old GM sway bar with end ground into a wedge shape, works great for shaping the tubes. I also use a acetylene torch, propane hand held doesn't get hot enough.
#15

Actually, the difference to make up is 1/16" (1/8" dia /2) and it's negligible. I put the flanges on the motor (in the car), stuck the tubes into the flanges, positioned them to clear everything, and tacked them on the outside. Then pulled them off, welded the outside tubes, test fit again, pulled them off, welded the insides, then ground the insides to suit the ports.
did you mig or tig? i only have a mig using .025 wire. just wondering if it is enough to close the gaps out from the outside. do you have any pictures of your finished welds?
btw. i have all my parts.
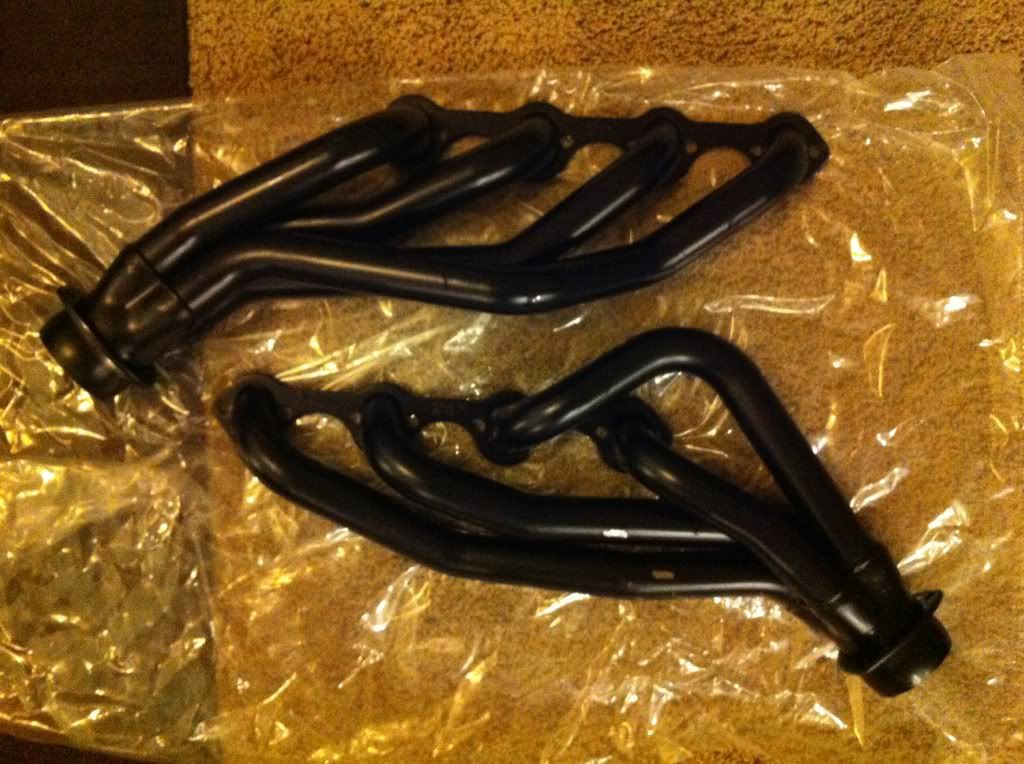
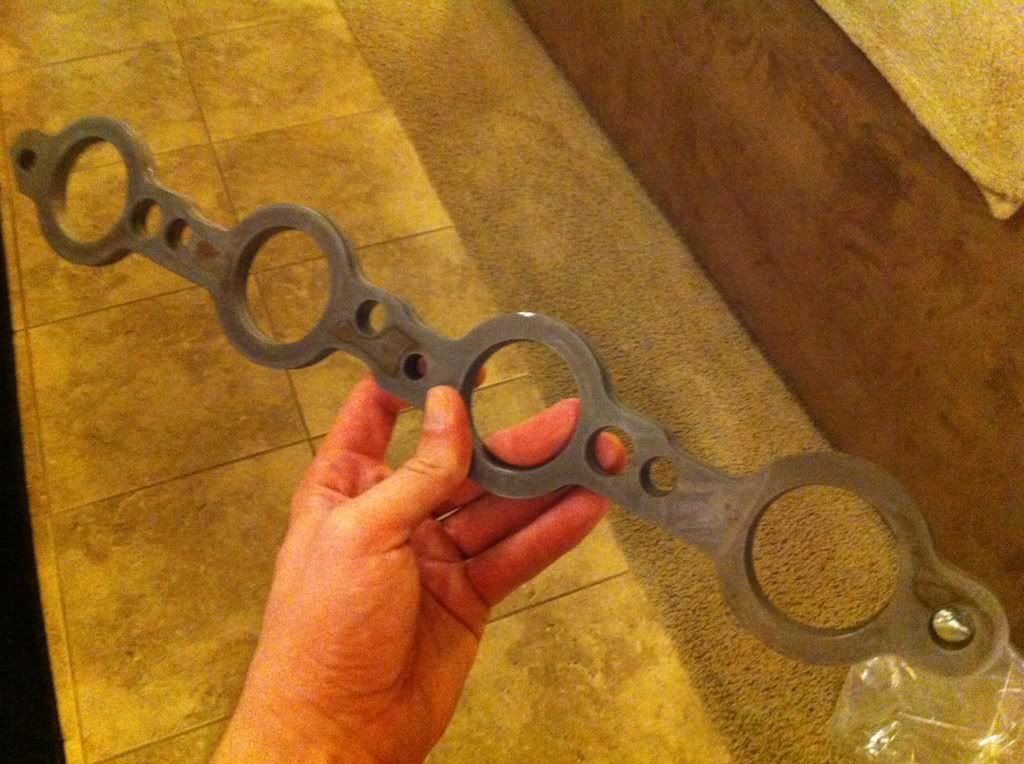
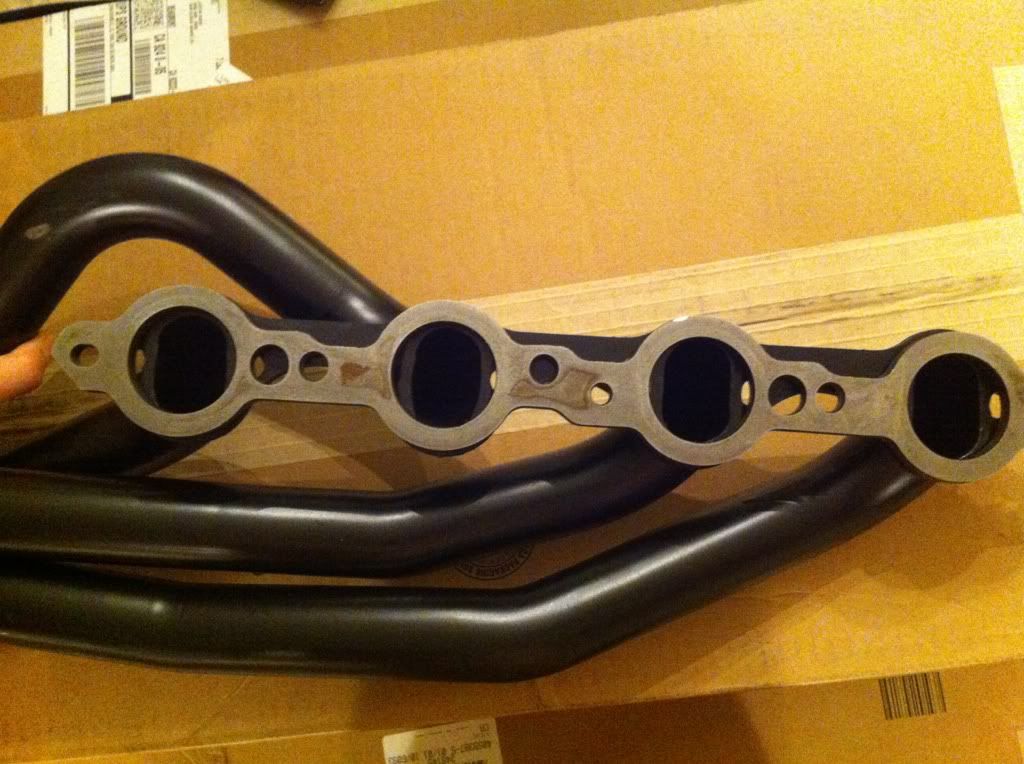
oops the flange is upside down...
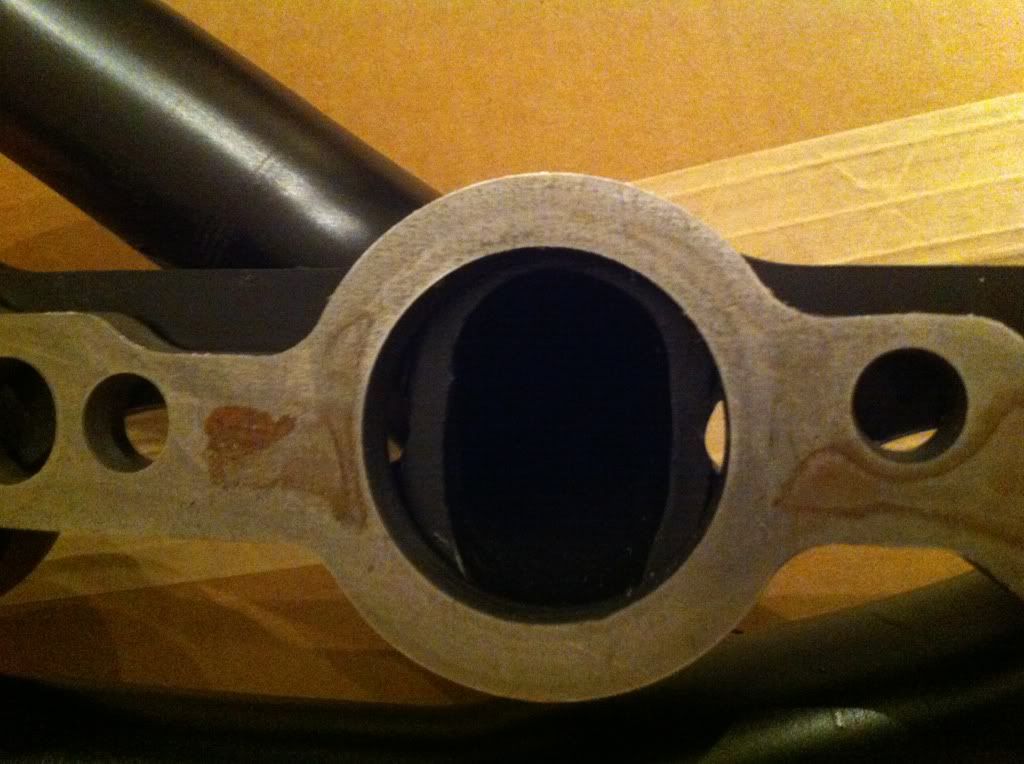