Huge F'ing Issue - Broken Head Bolt
#41
TECH Enthusiast
iTrader: (5)
Join Date: Apr 2008
Location: Hemet
Posts: 663
Likes: 0
Received 0 Likes
on
0 Posts

I know this is a big f*c*ing issue and do not let the negative people get to you. Post a pic of what the hole looks like and which hole it is so we can grasp the situation better. If I did this on a customers car I would have to fix it for free so the more we know the better. Most of us just want to help so we need to look at it in the big picture. Worst case scenario it might be possible to do the head gaskets like a Northstar engine. Whenever you pull a Northstar head all the threads leave with the bolts guarenteed. The solution is to drill the threads out. Get an insert thread kit and thread the larger hole with larger threads. Then install a head stud to fix it. The head bolts for a 4.6 northstar are likely the same size as a ls1 but I do know for sure. The case time serts as they are called might work if your last solution is to drill the bolt out and damage the threads. Just trying to help with my knowledge of what happens when head bolt holes and threads gets fu*k*d on GM engines. The northstar thread job must be done with the engine out and unless the hole is in the front yours is likely the same if you cannot easy out the bolt. Research Northstar time certs and it might give you some help. The Northstar head gasket pays like 25-30 hours for a reason because it is hard because every hole must have thread inserts. But the fact is it is done on a regular basis around the country so do not think it is the end of the world. I have been drinking and thinking about your problem because it is the kind of person I am so just keep trying an answer will emerge.
#42
TECH Enthusiast
iTrader: (5)
Join Date: Apr 2008
Location: Hemet
Posts: 663
Likes: 0
Received 0 Likes
on
0 Posts

To compare head bolt size you should go to a Cadillac dealer in your area and see if the head bolt size are the same if you have to. Your thing says north houston and I really do not know any good dealers in your area. I have experience with Lone Star Chevy, Mac Haik, and Robbins and cannot say any good things. I have some good experience with El Dorado in Mckinney and Peters Chevrolet in Longview but they are somewhat far.
#43

Texan GMC... ask for Buddy there... he'll set you straight... I actually work there and he knows his ****... was his helper for 2 months.
#44
On The Tree
Thread Starter
iTrader: (1)
Join Date: Oct 2010
Location: Dallas Texas
Posts: 118
Likes: 0
Received 0 Likes
on
0 Posts


I am going with the easy-out option? I have the set and its made in the USA of course. No Made in China... I just need to select a drill bit now and get two different sizes of them so I punch a starter hole and then a proper sized hole for the easy out. I did a few practice holes on my old head bolts just to make sure it was not impossible but the drill bit I used was not enough to get thru the hardened steel of the bolt. It did work, just not very well.
How do I add photo's to a post like the guy did on page one of this post?
How do I add photo's to a post like the guy did on page one of this post?
#46
TECH Enthusiast
iTrader: (5)
Join Date: Apr 2008
Location: Hemet
Posts: 663
Likes: 0
Received 0 Likes
on
0 Posts

If you want to post pics get a photobucket account and use the html link in the icon next to the hyperlink in the quick reply. I also just thought about this but in your area are some good ls1 race builders that are also sponsors like LME and Thunder Racing you should call them for some input they likely do not look at this section of ls1 tech in detail.
#47
On The Tree
Thread Starter
iTrader: (1)
Join Date: Oct 2010
Location: Dallas Texas
Posts: 118
Likes: 0
Received 0 Likes
on
0 Posts


Here are the few test runs I did last night.
First pics, I ran a magnet in the hole first to pull out any pieces that were in the hole and now you can see where the bolt goes and how far down it is. I did not do anything other than some testing.
First pics, I ran a magnet in the hole first to pull out any pieces that were in the hole and now you can see where the bolt goes and how far down it is. I did not do anything other than some testing.
#48
On The Tree
Thread Starter
iTrader: (1)
Join Date: Oct 2010
Location: Dallas Texas
Posts: 118
Likes: 0
Received 0 Likes
on
0 Posts


Testing part 1.
SO I bought a punch set, and some titanium drill bits. I started off with the punch but there is no way I can punch the hardened steel with a punch...so I found out. So I started off with a small drill bit and stepped it up after I went into the bolt about 1/2" with each one. Then I used the easyout and screwed that in the hole and spun the bolt while it was clamped in the vise. Worked great but now its doing all this in that small little hole. My only issue is that I cant seem to figure out how to get the bolt extracter down the hole and screw it in???
SO I bought a punch set, and some titanium drill bits. I started off with the punch but there is no way I can punch the hardened steel with a punch...so I found out. So I started off with a small drill bit and stepped it up after I went into the bolt about 1/2" with each one. Then I used the easyout and screwed that in the hole and spun the bolt while it was clamped in the vise. Worked great but now its doing all this in that small little hole. My only issue is that I cant seem to figure out how to get the bolt extracter down the hole and screw it in???
Last edited by Texas-Firehawk; 03-16-2011 at 12:38 PM.
#50
On The Tree
Thread Starter
iTrader: (1)
Join Date: Oct 2010
Location: Dallas Texas
Posts: 118
Likes: 0
Received 0 Likes
on
0 Posts


http://upload.wikimedia.org/wikipedi...d_T-wrench.jpg
I need one of these but it has to be skinny all the way down. That center section will not fit down the bolt hole.
I need one of these but it has to be skinny all the way down. That center section will not fit down the bolt hole.
#51
TECH Resident
iTrader: (12)

Drill the hole bigger.I believe when you center punch,the area becomes hardened and more difficult to drill.I have never had any luck with those titanium bits either.Self center/split point cobalt or high speed steel.Drill the hole bigger but not into the threads.Put some heat to it (only the bolt) if you can,then spray it with oil,pound the easy out in and slowly turn,if you feel alot of resistance stop and re heat/oil and you may have to do this multiple times.Do not break the easy out off in the hole.Place the drill bit you intend to use in one of the good holes and mark it with tape so you know how far to drill.
#54
TECH Fanatic
iTrader: (361)

http://upload.wikimedia.org/wikipedi...d_T-wrench.jpg
I need one of these but it has to be skinny all the way down. That center section will not fit down the bolt hole.
I need one of these but it has to be skinny all the way down. That center section will not fit down the bolt hole.
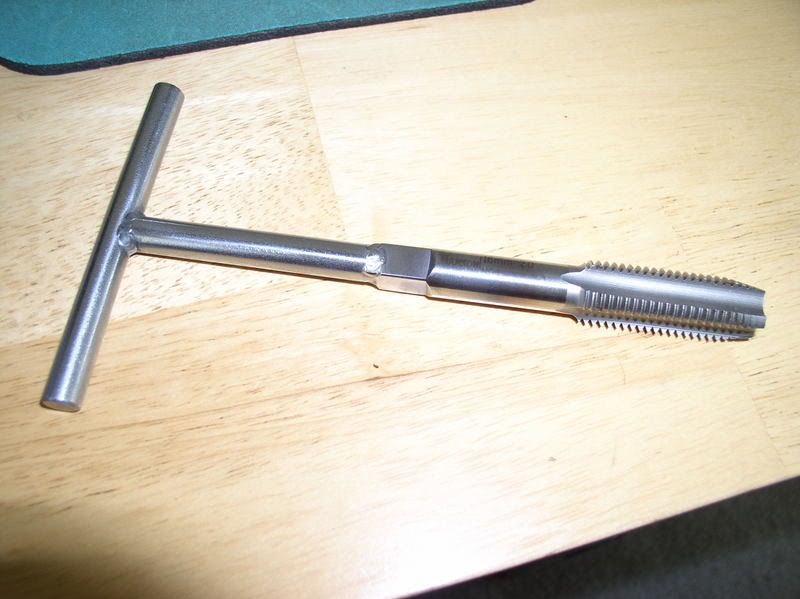
#55
On The Tree
Thread Starter
iTrader: (1)
Join Date: Oct 2010
Location: Dallas Texas
Posts: 118
Likes: 0
Received 0 Likes
on
0 Posts


in this case with the extracor being to short if you cannot find a longer one. Your next choice would be to find a good local weld-fab shop to tig weld a small exstension of round stock better yet a "t" handle to the end of the extractor. I have made a few of these taps in the past to clean out the crank snought, due to the recessed threads. Same idea be it a tap or eaze out/extractor.


#57
TECH Junkie
iTrader: (11)

Couple of things. First, I don't believe the bolt material is hardened. Second, you bought a "pin punch" set and you need a center punch. You can make one from one of your pin punches by grinding the end to a point, heating it red hot and quenching it in oil.
It appears the remains of the bolt are deep in the block, that could work in your favor. Look for a punch that's the same diameter as the bolt shank. This will allow you to punch the actual center of the broken stub of the bolt. Once punched, I'd make a bushing that has the ID of your drill bit and the OD of the bolt hole. This will keep the bit centered as you drill the stub. You might look for a LH drill bit, torquing the bolt in the "unscrew" direction while you drill can't hurt.
For the threads to break midway down the bolt means some kind of interference, and that could make removing the stub with the easy-out the hard part. Worst case scenario, you could drill with a bit just a tad smaller than the bolt threads and use a tap to clean out the rest. Get your hole drilled and post back.
It appears the remains of the bolt are deep in the block, that could work in your favor. Look for a punch that's the same diameter as the bolt shank. This will allow you to punch the actual center of the broken stub of the bolt. Once punched, I'd make a bushing that has the ID of your drill bit and the OD of the bolt hole. This will keep the bit centered as you drill the stub. You might look for a LH drill bit, torquing the bolt in the "unscrew" direction while you drill can't hurt.
For the threads to break midway down the bolt means some kind of interference, and that could make removing the stub with the easy-out the hard part. Worst case scenario, you could drill with a bit just a tad smaller than the bolt threads and use a tap to clean out the rest. Get your hole drilled and post back.
#58
That's MISTER MODERATOR
iTrader: (9)

“Drilling out” broken bolts is something I’m good at. I used to work at Kennedy Airport and successfully drilled out many broken bolts in runway centerline fixtures. I even welded up a drill press gig to get them drilled perfectly.
I quote drilling out because you don’t really want to drill it out, you want to use a reverse extractor in a hole in the bolt that’s smaller than the bolt to turn it out. “Drilling out” means completely removing it, it’s threads and the threads of what it’s threaded into (the engine block).
To drill the hole in the broken bolt, you first must grind a flat on the broken end of the broken bolt then center punch it ***** on dead center. Then you drill successfully larger holes until you get to the size needed for the extractor. The bit must stay ***** on dead center of the bolt. If the drill is off center even slightly, it will wander. If and when it hits a softer material, it's threads or in this case the aluminum engine block, it will continue towards it-no matter what you do.
As this bolt is broken below the deck, you have no way to grind flat the end of the broken bolt. Without this first and very important step, I don’t think you have a chance of doing the job. You’ll never get a starter drill bit where it belongs let alone any larger bits. If you do manage to get a bit started, it’ll surely wander right into the block. Too many times when this happens, trying the extractor will result in the extractor being partially in the bolt and partially in the block. Fail.
These bolts are most certainly rated hardened bolts-they’re at least class 10.9 which is roughly equal to a grade 8 standard bolt.
This might be a solution:
This bolt broke under tension while installing the head. It did not break because it bottomed out. I’m of the opinion that the broken section is simply sitting in the threaded hole in the block, not necessarily locked in the threads or stuck in the block. Is there any possible way to grab the jagged end of the bolt with say some needle nose pliers to see if it’ll turn?
I quote drilling out because you don’t really want to drill it out, you want to use a reverse extractor in a hole in the bolt that’s smaller than the bolt to turn it out. “Drilling out” means completely removing it, it’s threads and the threads of what it’s threaded into (the engine block).
To drill the hole in the broken bolt, you first must grind a flat on the broken end of the broken bolt then center punch it ***** on dead center. Then you drill successfully larger holes until you get to the size needed for the extractor. The bit must stay ***** on dead center of the bolt. If the drill is off center even slightly, it will wander. If and when it hits a softer material, it's threads or in this case the aluminum engine block, it will continue towards it-no matter what you do.
As this bolt is broken below the deck, you have no way to grind flat the end of the broken bolt. Without this first and very important step, I don’t think you have a chance of doing the job. You’ll never get a starter drill bit where it belongs let alone any larger bits. If you do manage to get a bit started, it’ll surely wander right into the block. Too many times when this happens, trying the extractor will result in the extractor being partially in the bolt and partially in the block. Fail.
These bolts are most certainly rated hardened bolts-they’re at least class 10.9 which is roughly equal to a grade 8 standard bolt.
This might be a solution:
This bolt broke under tension while installing the head. It did not break because it bottomed out. I’m of the opinion that the broken section is simply sitting in the threaded hole in the block, not necessarily locked in the threads or stuck in the block. Is there any possible way to grab the jagged end of the bolt with say some needle nose pliers to see if it’ll turn?
Last edited by Paul Bell; 03-16-2011 at 08:58 PM.
#59
On The Tree
Thread Starter
iTrader: (1)
Join Date: Oct 2010
Location: Dallas Texas
Posts: 118
Likes: 0
Received 0 Likes
on
0 Posts


No way man, its way down there but I have some knowledge that will assist anyone needing to do this.
First just to get the hole started you cant take a 4mm socket for a 1/4" ratchet and drop it int the hole (trust me it fits). Make sure you put it in there with the small side first. This will hit the broken part of the bolt dead center. Then you can get your first drill bit out and proceed to drill inside thru the socket and into the dead center of the broken bolt and just proceed with the step up in sizes until you get to a drill bit that will not fit thru the 4mm socket head but you will want to use some cutting oil(about a drop) and use a screwdriver magnet to get the cuttings out every few minutes of drilling. Once you have gotten to that next size over 4mm you have already drilled your pilot hole and then almost any bit will work after that. I drilled mine about 1/2" deep into the bolt and the guide of the socket makes sure it went straight. This is as far as I went tonight but it should be a snap from here as far as drilling goes. then the extraction process...ill explain further when I get there.
First just to get the hole started you cant take a 4mm socket for a 1/4" ratchet and drop it int the hole (trust me it fits). Make sure you put it in there with the small side first. This will hit the broken part of the bolt dead center. Then you can get your first drill bit out and proceed to drill inside thru the socket and into the dead center of the broken bolt and just proceed with the step up in sizes until you get to a drill bit that will not fit thru the 4mm socket head but you will want to use some cutting oil(about a drop) and use a screwdriver magnet to get the cuttings out every few minutes of drilling. Once you have gotten to that next size over 4mm you have already drilled your pilot hole and then almost any bit will work after that. I drilled mine about 1/2" deep into the bolt and the guide of the socket makes sure it went straight. This is as far as I went tonight but it should be a snap from here as far as drilling goes. then the extraction process...ill explain further when I get there.