Why is (re)sleeving recommended at high bores?
#1

I see this all the time "if you are going to go 0.125 then you should sleeve it" or "the only time i will go "0.125 is if i sleeve it"
I've searched and searched...and then searched some more. But i can't find the answer.
How does sleeving make it OK?? As far as i know, the liner is just like the cylinder wall. If going 0.125 is not safe without a sleeve, then how is it safer to go that far with a sleeve?? I mean...what difference does it make whether it is the surface of a sleeve or the surface of the cylinder wall??
I've searched and searched...and then searched some more. But i can't find the answer.
How does sleeving make it OK?? As far as i know, the liner is just like the cylinder wall. If going 0.125 is not safe without a sleeve, then how is it safer to go that far with a sleeve?? I mean...what difference does it make whether it is the surface of a sleeve or the surface of the cylinder wall??
#2
11 Second Club
iTrader: (2)

when GM was designing the LS1 (gen III) small block they used a new and
propriatary casting procedure with the cylinder liners (sleeves) in place as
opposed to the old way of casting the aluminum block...machining it....then
pressing in the liners. They then began experiencing knock sensor issues
because the liners were thick...which caused combustion noise to be seen as
knocking by the computer which then pulled timing. The solution became
thin liners which can only be honed approx. .010" for LS1s and .020" for LS2
engines. Obviously going .125" requires someone like ERL to remachine the
block and press fitting larger diameter sleeves for the big pistons.......
propriatary casting procedure with the cylinder liners (sleeves) in place as
opposed to the old way of casting the aluminum block...machining it....then
pressing in the liners. They then began experiencing knock sensor issues
because the liners were thick...which caused combustion noise to be seen as
knocking by the computer which then pulled timing. The solution became
thin liners which can only be honed approx. .010" for LS1s and .020" for LS2
engines. Obviously going .125" requires someone like ERL to remachine the
block and press fitting larger diameter sleeves for the big pistons.......

#3
TECH Enthusiast
Join Date: Nov 2004
Location: Tampa FL
Posts: 714
Likes: 0
Received 0 Likes
on
0 Posts

The sleeves are the correct bore size and thicker than the stock liners. A stock cylinder liner can only be bored and honed so much before the walls get too thin.
#4
TECH Resident
iTrader: (4)

cylinder wall thickness.
going that big on the stock cylinder sleeves leaves little support - the casting in the areas immediately surrounding the cylinders isn't robust enough to be excessively loaded leaving the sleeves themselves prone to failure. With sleeves, you buy yourself back the cylinder wall thickness making it much more reliable when dealing with higher horsepower situations.
going that big on the stock cylinder sleeves leaves little support - the casting in the areas immediately surrounding the cylinders isn't robust enough to be excessively loaded leaving the sleeves themselves prone to failure. With sleeves, you buy yourself back the cylinder wall thickness making it much more reliable when dealing with higher horsepower situations.
Last edited by ckpitt55; 06-28-2013 at 10:00 AM.
#5

Sorry guys...still don't get it. Let me explain what i don't understand in another way. Lets say going 0.70 will leave the cylinder walls at a thickness of 150. Put a sleeve in there and bore it to 0.70 over, wouldn't the thickness of the cylinder bore still be 150. So if you are left with a 150-thick cylinder wall regardless of whether it is sleeved or not...why would it be safer when sleeving??
UNLESS...sleeving is only recommended on aluminum blocks because the original sleeves will be too thin when you go big on boreing. So with resleeving, you bore more than you would if you are not resleeving just so you can fit the sleeves and once you fit them in you bore to your desired bore size...that way you get a thicker cylinder wall with the new sleeve than you would if you just bored on the original sleeves..... is that it??
UNLESS...sleeving is only recommended on aluminum blocks because the original sleeves will be too thin when you go big on boreing. So with resleeving, you bore more than you would if you are not resleeving just so you can fit the sleeves and once you fit them in you bore to your desired bore size...that way you get a thicker cylinder wall with the new sleeve than you would if you just bored on the original sleeves..... is that it??
Last edited by Freefallin; 06-28-2013 at 06:28 AM.
#6
TECH Veteran
iTrader: (14)

Lets try this another way then... If you look at an ls aluminum block you will see they have steel sleeves inbedded into the aluminum block. Now these liners can only be bored .010 before they become too thin. It has nothing to do with block thickness it has everything to do with the stock cylinder steel liners now becoming too thin and prone to cracking.
An iron block doesnt use steel liners because the block itself acts as the liners which is why it can be bored much bigger without a sleeve.
Stock iron block. no liners like a stock ls motor
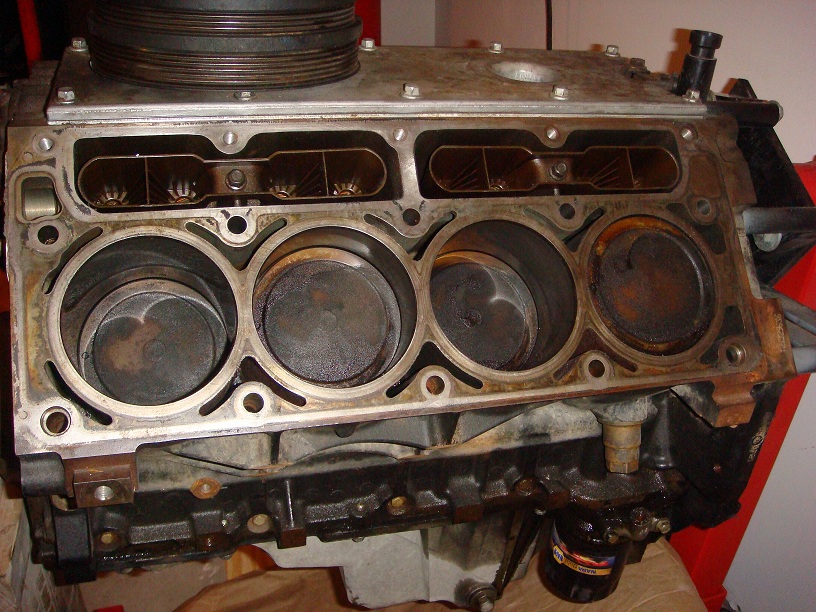
Stock Ls block notice the different color liners in the bores

By sleeving it you basically bore the old sleeve out of the block and continue to bore out the block for whatever type of sleeve you will be using. In a dry sleeve the sleeves fit into the area where the stock liners were and never comes into contact with the coolant as the stock cylinder walls in the block are still retained just bored out bigger to make room for the sleeve. a dry sleeve uses the stock coolant passages in the block never comes into contact with coolant thus the name dry sleeve....

A wet sleeve application is much stronger and can be bored larger. A wet sleeve completely cuts out the side of the block and the sleeves themselves act as the cylinder walls alone. wet sleeves as seen here make their own coolant passages
An iron block doesnt use steel liners because the block itself acts as the liners which is why it can be bored much bigger without a sleeve.
Stock iron block. no liners like a stock ls motor
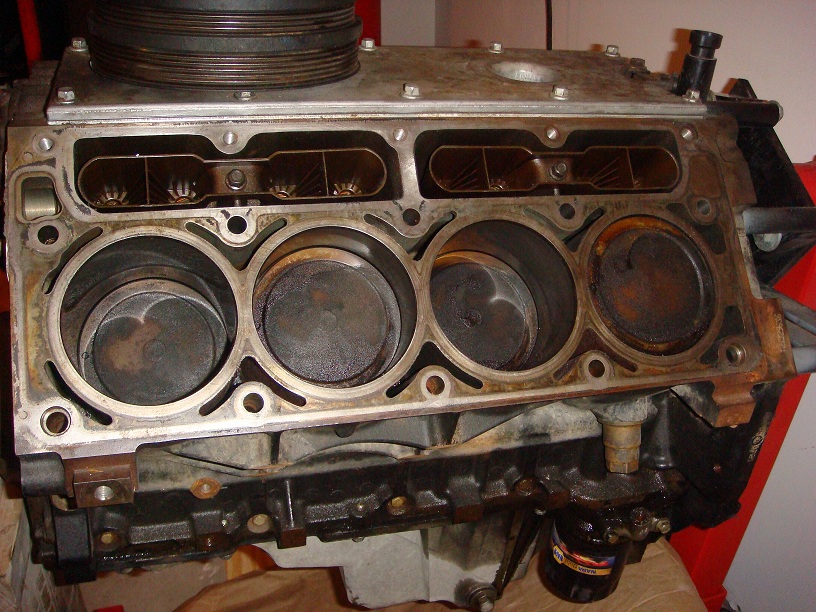
Stock Ls block notice the different color liners in the bores

By sleeving it you basically bore the old sleeve out of the block and continue to bore out the block for whatever type of sleeve you will be using. In a dry sleeve the sleeves fit into the area where the stock liners were and never comes into contact with the coolant as the stock cylinder walls in the block are still retained just bored out bigger to make room for the sleeve. a dry sleeve uses the stock coolant passages in the block never comes into contact with coolant thus the name dry sleeve....

A wet sleeve application is much stronger and can be bored larger. A wet sleeve completely cuts out the side of the block and the sleeves themselves act as the cylinder walls alone. wet sleeves as seen here make their own coolant passages

Trending Topics
#9

Redbird555 gave a very good explanation. I just want to add a couple of things that also make it safer and more reliable.
The difference comes in the difference between sleeve material. Factory LS blocks come with cast iron sleeves where ERL Performance uses our ductile iron sleeve. The ductile iron material is much stronger than cast iron.
One of the ways they can test the strength and maximum strength to different metals is by testing the "Tensile Strength" of the metal. Tensile strength is defined as a stress, which is measured as force per unit area.
A traditional cast iron sleeve will test at about 30,000 tensile strength where our ERL Performance ductile iron sleeve measures 100,000 + tensile strength. This enables us to apply greater cylinder pressures to our sleeves without cracking our sleeves like you see in so many LS cast iron sleeves causing major failures and it also enables us to be able to go with much thinner sleeves in N/A applications without worrying that "the sleeves are too thin" because our material is so much stronger.
One last huge benefit to our sleeving is that our sleeves are much longer than the factory cylinder liners and therefore helps with oil control and helps keep more of the piston up inside the cylinder when using a 4.000 stroke crank or larger.
The difference comes in the difference between sleeve material. Factory LS blocks come with cast iron sleeves where ERL Performance uses our ductile iron sleeve. The ductile iron material is much stronger than cast iron.
One of the ways they can test the strength and maximum strength to different metals is by testing the "Tensile Strength" of the metal. Tensile strength is defined as a stress, which is measured as force per unit area.
A traditional cast iron sleeve will test at about 30,000 tensile strength where our ERL Performance ductile iron sleeve measures 100,000 + tensile strength. This enables us to apply greater cylinder pressures to our sleeves without cracking our sleeves like you see in so many LS cast iron sleeves causing major failures and it also enables us to be able to go with much thinner sleeves in N/A applications without worrying that "the sleeves are too thin" because our material is so much stronger.
One last huge benefit to our sleeving is that our sleeves are much longer than the factory cylinder liners and therefore helps with oil control and helps keep more of the piston up inside the cylinder when using a 4.000 stroke crank or larger.